UNIT 2
Basic requirements of a building
The planning and construction of a building should be aimed at fulfilling the following requirements:
- Strength and stability
- Dimensional stability
- Comforts and convenience
- Resistance to dampness
- Resistance to fire
- Heat insulation
- Lighting and ventilation
- Sound insulation
- Protection against termite attack
- Strength and Stability:
The building should be capable of transferring the expected loads in its life period safely to the ground. The design of various structural components like slabs, beams, walls, columns, and footing should ensure safety. None of the structural components should buckle, overturn, and collapse.
2. Dimensional Stability:
Excessive deformation of structural components give a sense of instability and result in a crack in walls, flooring, etc. All structural components should be so designed that deflections do not exceed the permissible values specified in the codes.
3. Comforts and Conveniences:
Various units in the building should be properly grouped and integrated keeping in mind the comfort and convenience of the user.
4. Resistance to Dampness:
Dampness in a building is a great nuisance and it may reduce the life of the building. Great care should be taken in planning and in the construction of the building to avoid dampness.
5. Resistance to Fire:
Regarding achieving resistance to fire, the basic requirements laid down in the codes are:
(a) the structure should not ignite easily.
(b) building orientation should be such that the spread of fire is slow.
(c) In case of fire, there should be a means of easy access to vacate buildings quickly.
6. Heat Insulation:
A building should be so oriented and designed that it insulates interior from heat.
7. Lighting and Ventilation:
For healthy and happy living natural light and ventilation are required. Diffused light and good cross ventilation should be available inside the building.
8. Sound Insulation:
Buildings should be planned against outdoor and indoor noises.
9. Protection from Termite:
Buildings should be protected from termites.
The basic components of a building structure are the foundation, floors, walls, beams, columns, roof, stairs, etc. These elements serve the purpose of supporting, enclosing, and protecting the building structure.
- Roof
- Parapet
- Lintels
- Beams
- Columns
- Damp-proof course (DPC)
- Walls
- Floor
- Stairs
- Plinth Beam
- Foundation
- Plinth
- Roof
The roof forms the topmost component of a building structure. It covers the top face of the building. Roofs can be either flat or sloped based on the location and weather conditions of the area.
2. Parapet
Parapets are short walls extended above the roof slab. Parapets are installed for flat roofs. It acts as a safety wall for people using the roof.
3. Lintels
Lintels are constructed above the wall openings like doors, windows, etc. These structures support the weight of the wall coming over the opening. Normally, lintels are constructed by reinforced cement concrete. In residential buildings, lintels can be either constructed from concrete or bricks.
4. Beams and slabs
Beams and slabs form the horizontal members in a building. For a single-story building, the top slab forms the roof. In the case of a multi-story building, the beam transfers the load coming from the floor above the slab which is in turn transferred to the columns. Beams and slabs are constructed by reinforced cement concrete (R.C.C).
5. Columns
Columns are vertical members constructed above the ground level. Columns can be of two types: Architectural columns and structural columns. Architectural columns are constructed to improve the building’s aesthetics while a structural column takes the load coming from the slab above and transfers safely to the foundation.
6. Damp Proof Course (DPC)
DPC is a layer of waterproofing material applied on the basement level to prevent the rise of surface water into the walls. The walls are constructed over the DPC.
7. Walls
Walls are vertical elements which support the roof. It can be made from stones, bricks, concrete blocks, etc. Walls provide an enclosure and protect against wind, sunshine, rain, etc. Openings are provided in the walls for ventilation and access to the building.
8. Floors
The floor is the surface laid on the plinth level. Flooring can be done by a variety of materials like tiles, granites, marbles, concrete, etc. Before flooring, the ground has to be properly compacted and leveled.
9. Stairs
A stair is a sequence of steps that connects different floors in a building structure. The space occupied by a stair is called as the stairway. There are different types of stairs like a wooden stair, R.C.C stair, etc.
10. Plinth Beam
The plinth beam is a beam structure constructed either at or above the ground level to take up the load of the wall coming over it.
11. Plinth
The plinth is constructed above the ground level. It is a cement-mortar layer lying between the substructure and the superstructure.
12. Foundation
The Foundation is a structural unit that uniformly distributes the load from the superstructure to the underlying soil. This is the first structural unit to be constructed for any building construction. A good foundation prevents settlement of the building.
Formwork is temporary or permanent molds into which concrete or similar materials are poured. In the context of concrete construction, the falsework supports the shuttering molds.
Types of Formwork (Shuttering)
1. Timber Formwork
Timber for formwork should satisfy the following requirement:
It should be:
- Well-seasoned
- Light in weight
- Easily workable with nails without splitting
- Free from loose knots
The timber used for shuttering for exposed concrete work should have smooth and even surface on all faces which come in contact with concrete.
Table 1: Normal sizes of members for timber formwork
Sheeting for slabs, beam, column side, and beam bottom | 25 mm to 40 mm thick |
Joints, ledges | 50 x 70 mm to 50 x 150 mm |
Posts | 75 x 100mm to 100 x 100 mm |
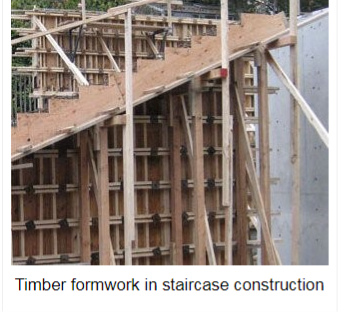
2. Plywood Formwork
Resin-bonded plywood sheets are attached to timber frames to make up panels of the required sizes. The cost of plywood formwork compares favorably with that of timber shuttering, and it may even prove cheaper in some instances given the following considerations:
- It is possible to have a smooth finish in which case on cost in surface finishing is there.
- By the use of large-size panels, it is possible to affect saving in the labor cost of fixing and dismantling.
- The number of reuses is more as compared with timber shuttering. For estimation purposes, the number of reuses can be taken as 20 to 25.
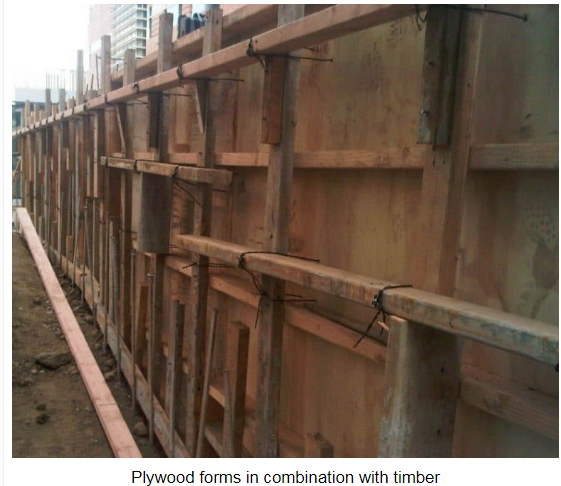
3. Steel Formwork
This consists of panels fabricated out of thin steel plates stiffened along the edges by small steel angles. The panel units can be held together through the use of suitable clamps or bolts and nuts.
The panels can be fabricated in large numbers in any desired modular shape or size. Steel forms are largely used in large projects or in a situation where large number reuses of the shuttering is possible. This type of shutter is considered most suitable for circular or curved structures.
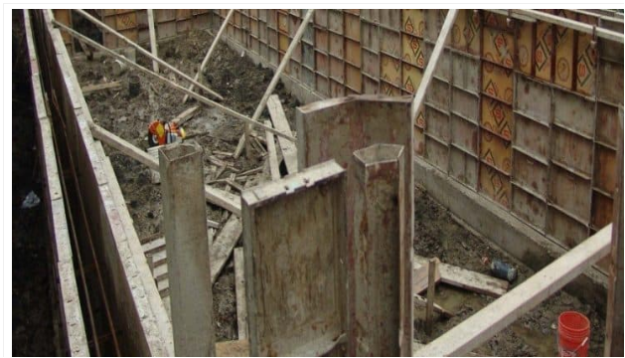
4. Aluminum Formwork
Aluminum formwork is similar in many respects similar to those made of steel. Aluminum forms are lighter than steel forms due to low density and this is their primary advantage when compared to steel. The shuttering is economical if large numbers of repeating usage are made in construction. The disadvantage is that no alteration is possible once the formwork is constructed.
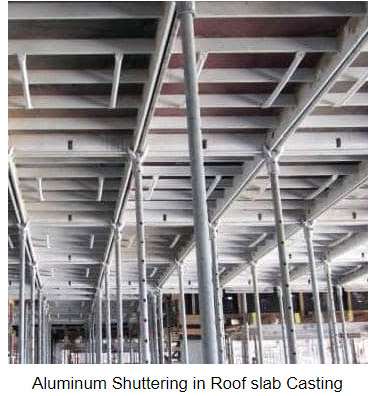
Foundations are classified as shallow and deep foundations. Types of foundations under shallow and deep foundations for building construction and their uses are discussed.
Types of Foundation and their Uses
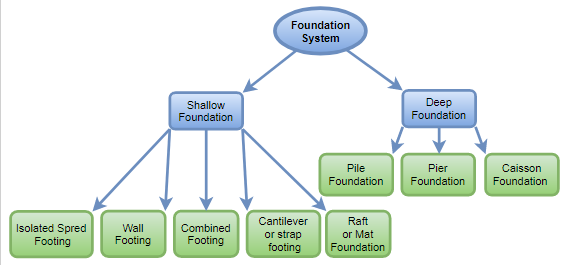
TYPES OF SHALLOW FOUNDATION-
1. Isolated Spread Footing
This is the most widely recognized and most straightforward shallow foundation type, as this is the most economical type. They are typically utilized for shallow establishments to convey and spread concentrated burdens caused, for instance, by pillars or columns. They are generally used for ordinary buildings (Typically up to five stories).
Isolated footing comprises a foundation directly at the base of the segment. Generally, every section has its footing. They straightforwardly transfer the loads from the column to the soil. It might be rectangular, square, or roundabout. It can comprise both reinforced or non-reinforced material. For the non-reinforced footing, however, the stature of the footing has to be more prominent to give the vital spreading of the load. They should possibly be utilized when it is sure beyond a shadow of a doubt that no differing settlements will happen under the whole structure. Spread footings are inadmissible for the orientation of large loads. It is given to lessen the twisting minutes and shearing powers in their primary areas.
The size of the footing can be roughly calculated by dividing the total load at the column base by the allowable bearing capacity of the soil.
The followings are the types of spread footing.
- Single pad footing.
- Stepped footing for a column.
- Sloped footing for a column.
- Wall footing without step.
- Stepped footing for walls.
- Grillage foundation.
To decide when to use shallow foundations, it is necessary to know when it is economical. It is economical when:
- The load of the structure is relatively low.
- Columns are not closely placed.
- The bearing capacity of the soil is high at a shallow depth.
2. Wall Footing or Strip footing
Wall footing is also known as continuous footing. This type is used to distribute loads of structural or non- structural load-bearing walls to the ground in such a way that the load-bearing limit of the soil isn't outperformed. It runs along the direction of the wall. The width of the wall foundation is usually 2-3 times the width of the wall.
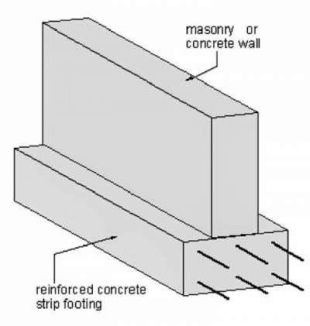
The wall footing is a continuous slab strip along the length of the wall. Stone, brick, reinforced concrete, etc. are used for the construction of wall foundations.
- On account of block walls, the footing comprises a few courses of bricks, the least course being generally double the expansiveness of the wall above.
- On account of stone masonry walls, the counterbalances could be 15 cm, with the statues of the course as 30 cm. Along these lines, the size of footings is marginally more than that of the block divider footings.
- If the heap on the wall is substantial or the soil is of low bearing limit, this reinforced concrete foundation type can be given.
Wall footing is economical when:
- Loads to be transmitted are of small magnitude.
- It is placed on dense sand and gravel.
3. Combined Footing
The combined footing is very similar to the isolated footing. When the columns of the structure are carefully placed, or the bearing capacity of the soil is low and their footing overlap each other, combined footing is provided. It is fundamentally a blend of different footings, which uses the properties of various balances in a single footing dependent on the necessity of the structure.
The foundations which are made common to more than one column are called combined footings. There are different types of combined footing, including slab type, slab and beam type, rectangular, raft, and strap beam type. They may be square, tee-shaped, or trapezoidal. The main objective is the uniform distribution of loads under the entire area of footing, for this is necessary to coincide with the center of gravity of the footing area with the center of gravity of the total loads.
Combined foundations are economic when:
- The columns are placed close to each other.
- When the column is close to the property line and the isolated footing would cross the property line or become eccentric.
- Dimensions of one side of the footing are restricted to some lower value.
4. Cantilever or Strap Footing
Strap footings are similar to combined footings. Reasons for considering or choosing strap footing are identical to the combined one.
In strap footing, the foundation under the columns is built individually and connected by a strap beam. Generally, when the edge of the footing cannot be extended beyond the property line, the exterior footing is connected by a strap beam with interior footing.
5. Raft or Mat Foundation
Raft or Mat foundations are used where other shallow or pile foundations are not suitable. It is also recommended in situations where the bearing capacity of the soil is inadequate, the load of the structure is to be distributed over a large area or structure is subjected continuously to shocks or jerks.
Raft foundation consists of a reinforced concrete slab or T-beam slab placed over the entire area of the structure. In this type, the whole basement floor slab acts as the foundation. The total load of the structure is spread evenly over the entire area of the structure. This is called raft because, in this case, the building seems like a vessel that floats on a sea of soil.
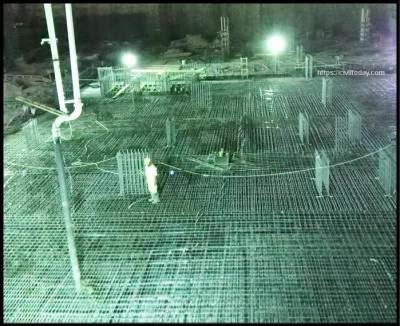
Raft foundations are economic when:
- The soil is weak and the load has to be spread over a large area.
- The structure includes a basement.
- Columns are closely placed.
- Other kinds of foundations are not feasible.
- Differential settlement is to be prevented.
Deep Foundations
Several Types of Deep Foundations Are Discussed Below.
Types of Deep Foundation.
The followings are the types of deep foundation.
1. Pile Foundation
Pile is a common type of deep foundation. They are used to reduce cost, and when as per soil condition considerations, it is desirable to transmit loads to soil strata which are beyond the reach of shallow foundations.
The followings are the types of pile foundations.
- Based on Function or Use
- Sheet Piles
- Load Bearing Piles
- End Bearing Piles
- Friction Piles
- Soil Compactor Piles
- Based on Materials and Construction Method
- Timber Piles
- Concrete Piles
- Steel Piles
- Composite Piles
Pile is a slender member with a small cross-sectional area compared to its length. It is used to transmit foundation loads to a deeper soil or rock strata when the bearing capacity of soil near the surface is relatively low. Pile transmits load either by skin friction or bearing. Piles are also used to resist structures against uplift and provide structures stability against lateral and overturning forces.
Pile is a slender member with a small cross-sectional area compared to its length. It is used to transmit foundation loads to a deeper soil or rock strata when the bearing capacity of soil near the surface is relatively low. Pile spreads load either by skin friction or bearing. Piles are also used to resist structures against uplift and provide structures stability against lateral and overturning forces.
Pile foundations are economic when
- Soil with great bearing capacity is at a greater depth.
- When there are chances of construction of irrigation canals in the nearby area.
- When it is very expensive to provide raft or grillage.
- When the foundation is subjected to a heavily concentrated load.
- In marshy places.
- When the topsoil layer is compressible.
- In the case of bridges, when the scouring is more in the river bed.
It can again be classified based on its material and its mechanism of load transfer or function. Several types of pile foundations are shown in the following chart.
2. Pier Foundation
Pier is an underground structure that transmits a more massive load, which cannot be carried by shallow foundations. It is usually shallower than piles. The pier foundation is generally utilized in multi-story structures. Since the base region is determined by the plan strategy for the regular establishment, the single pier load test is wiped out. Along these lines, it is increasingly well known under tight conditions.
Pier foundation is a cylindrical structural member that transfers heavy load from superstructure to the soil by end bearing. Unlike piles, it can only transfer load by bearing and by not skin friction.
Pier Foundation is economic when:
- Sound rock strata lie under a decomposed rock layer at the top.
- The topsoil is stiff clay which resists driving the bearing pile.
- When a heavy load is to be transferred to the soil.
Pier foundation has many advantages:
- It has a broad scope of assortment with regards to structure. There are different materials we can here to build a stylish view, and it stays in our spending limit.
- It sets aside cash and time as it doesn't require broad removal of a ton of cement.
- Bearing limits can increment by under-reaming the base.
Along with the advantages, it has a few disadvantages as well:
- If one post or dock is harmed, it can prompt critical harm to the general establishment.
- It can be vitality wasteful if not protected appropriately.
- Floors must be intensely, vigorously protected, and shielded from critters.
Water-proofing techniques-
- Waterproofing is the formation of an impervious barrier over surfaces of foundations, roofs, walls, and other structural members. The function of the impermeable barrier is to prevent water penetrations. The building surfaces are made water-resistant and sometimes waterproof.
- Waterproofing is necessary for the basement, walls, bathrooms, kitchen, balconies, decks, terrace or roofs, green roofs, water tanks, and swimming pools, etc.
Waterproofing Methods
- Cementitious Waterproofing
- Liquid Waterproofing Membrane
- Bituminous Membrane
- Bituminous Coating
- Polyurethane Liquid Membrane
1. Cementitious Waterproofing
- Cementitious waterproofing is the easiest method of waterproofing in construction. The materials for cementitious waterproofing are readily available from suppliers of masonry products. And they are easy to mix and apply.
- The applications of the cementitious waterproofing technique are in the internal wet areas, such as toilets. That is why it does not go through the contract and expansion process.
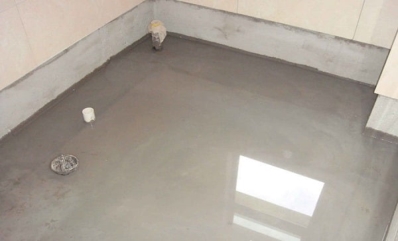
Fig.: Cementitious Waterproofing
2. Liquid Waterproofing Membrane
- The liquid membrane consists of a primer coat and two topcoats. The application of the coatings is by spray, roller, or trowel. The liquid layer is thin and offers more flexibility than the cementitious types of waterproofing.
- Liquid waterproofing membrane can be of a spray-applied liquid layer composed of polymer-modified asphalt. Polyurethane liquid membranes in separate grades for trowel, roller, or spray are also available from various manufacturers.
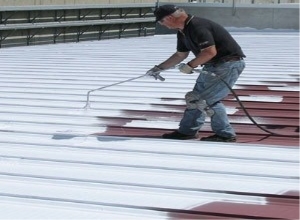
Fig.: Liquid Waterproofing Membrane
3. Bituminous Coating Waterproofing
- Bituminous coating (asphalt coating) is made of bitumen based materials. It is a flexible protective coat based on its formulation and polymerization grade. The flexibility and protection against water can be influenced by the polymer grade and reinforcement of fiber.
- The most common applications of bituminous coatings include areas that are beneath screed wet. It is an excellent protective coating and waterproofing agent, especially on surfaces such as concrete foundations.
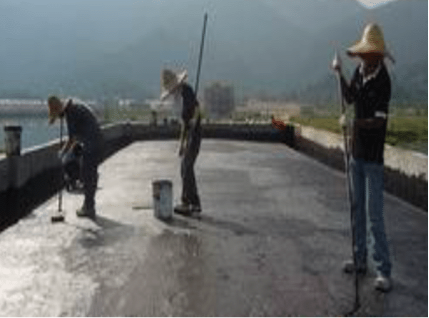
Fig.: Bituminous Waterproof Coating
4. Bituminous Membrane Waterproofing
Bituminous membrane waterproofing is a popular method used for low-sloped roofs due to their proven performance. The bituminous waterproofing membrane has a torch on the layer and self-adhesive membrane.
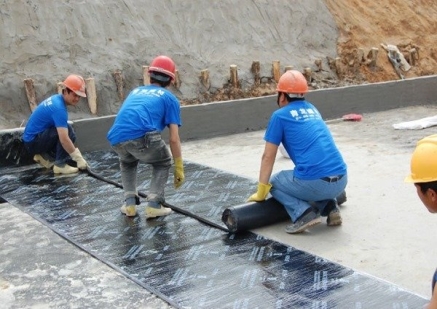
Fig.: Bituminous Membrane Waterproofing
5. Polyurethane Liquid Membrane Waterproofing
Polyurethane liquid membrane method of waterproofing is used for the flat roof area and exposed to weathering. This waterproofing method is expensive.
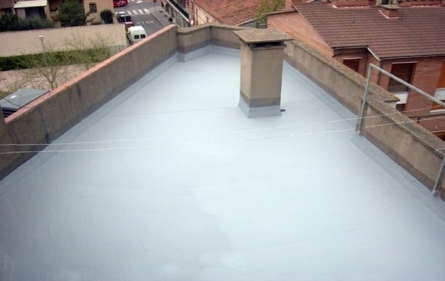
Fig.: Polyurethane Liquid Membrane Waterproofing
Anti termite treatment-
- Anti-termite treatment is a chemical procedure carried out for soil, masonry, wood, and electrical fixtures to provide the building with a chemical barrier against the subterranean or wood-nesting termites before and after construction.
How to do Anti-Termite Treatment in Masonry and RCC Foundation?
- The bottom surface and sides (up to about 30 cm) of the excavations carried out for foundation shall be treated with the chemical at the rate of 5 L/m2 of surface area.
- The backfill in immediate contact with the masonry foundation or retaining wall is treated with the chemical at the rate of 7.5 L/m2 of the vertical surface of the sub-structure for each side.
- The earth-fill is done in layers and, the chemical treatment shall be carried out for each layer.
- The voids in the joints of masonry are the possible entry points into the building for which the treatment is necessary.
- However, in RCC foundations, there are no such voids for the termites to penetrate.
- For the RCC foundation, the treatment may be started at 500 mm below ground level.
- The soil in the immediate contact with RCC shall be treated with 7.5 liters/m2 of the chemical, as shown in figure 2.
- For treatment in flooring, the chemical emulsion at the rate of 5litre/m2 shall be treated before laying sand bed or sub-grade.
- In the case where the surface is hard, and seeping of emulsion does not take place, holes up to 50 mm to 75 mm deep at 150 mm centers both ways may be made with a 12 mm steel rod to facilitate saturation of the soil with chemicals.
- After the completion of the building, holes of depth 300mm are dug at intervals of 150mm along the external perimeter of the building an,d the chemical emulsion is poured along the water at the rate of 7.5litre/m2 of the vertical surfaces in contact with the earth.
- In the event of the filling being more than 300 mm, the external perimeter treatment shall extend to the full depth of filling down to the ground level so as to ensure continuity of the chemical barrier.
- The treatment for the apron which is placed over the top surface of consolidated earth shall be treated with the chemical emulsion at the rate of 5 liters/m2 of the surface before the apron is laid.
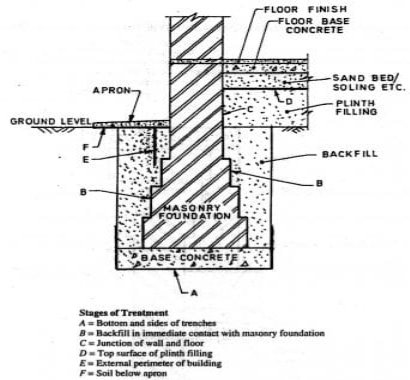
Fig : Anti Termite Treatment in Masonry Foundation
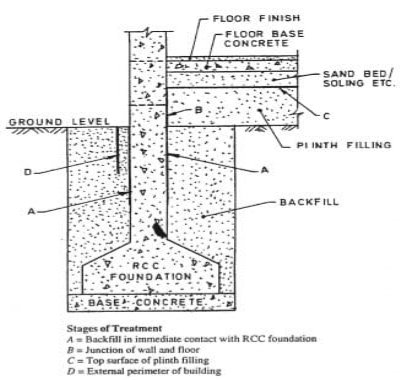
Fig 2: Anti Termite Treatment in RCC Foundation.
1. What is Anti-Termite Treatment in building?
Anti-termite treatment is a chemical procedure carried out for soil, masonry, wood, and electrical fixtures to provide the building with a chemical barrier against the subterranean or wood-nesting termites before and after construction.
2. Which are the effective chemicals used for anti-termite treatment?
1. Heptachlor emulsifiable concentrate 0.5 percent by weight
2. Chlordane emulsifiable concentrate 1.0 percent by weight
3. Chlorpyrifosemulsifiable concentrate, 1.0 percent by weight
3. Which is the best time to carry out the anti-termite treatment?
Anti termite treatment should start when foundation trenches and pits are ready to take mass concrete in foundations. The treatment should not be carried out when it is raining or when the soil is wet.
Doors and windows- (Utility fixtures)
Fixtures are provided for doors and windows to provide operating facilities, security for rooms and ease of opening and closing etc. Different types of fixtures and fastenings such as, hinges, bolts, handles, locks are available.
Types of Fixtures and Fastenings for Doors and Windows
Hinges
Hinge is fixture which helps the door to rotate freely along its axis. There are so many types of hinges are there which are as follows.
1. Butt Hinge
This is the most common type of hinge used for doors and windows. It has two flanges made of cast iron or steel. One flange is screwed to the door or window and other one screwed to frame.
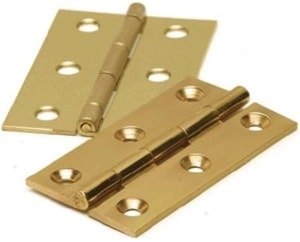
2. Back Flap Hinge
This are similar to butt hinges and used for thin doors. Back flap hinges have wide flanges than butt hinges. They are fixed to the back side of door and frame.
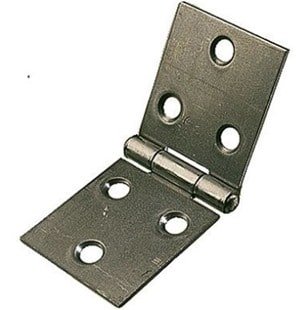
3. Counter Flap Hinge
This hinge has two centers, and these can be folded back to back.
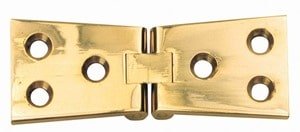
4. Parliamentary Hinge
When the opening is very small or narrow, then it is better to provide parliamentary hinges to provide more space of opening as well as to avoid obstruction while moving furniture etc.
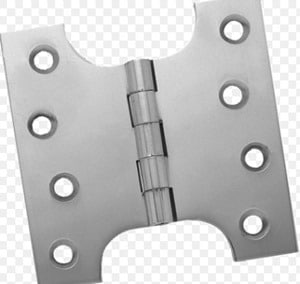
5. Spring Hinge
Spring hinges are used for swinging doors. The door is closed automatically due to spring action in this case. Spring hinges are available as single acting and double acting spring hinges.
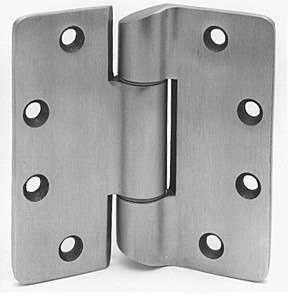
6. Rising Butt Hinge
It is similar to normal butt joint, but it has helical nickel joint in between flanges which helps the door to raise vertically upwards when opened. This is useful for the rooms having carpets etc. the raise may be about 10mm.
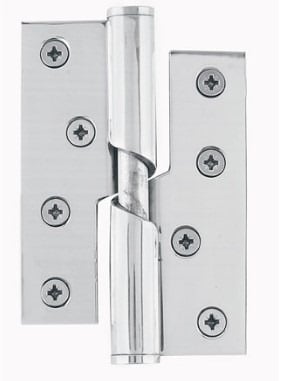
7. Garnet Hinge
It has Tw different shaped hinges. One is of long arm shaped which is fixed to the door and another is of plate shaped which is fixed to the frame. This type of hinge is used for battened or ledged doors.
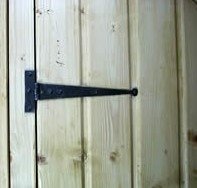
8. Strap Hinge
It is also used for battened and ledged doors and windows. It has two long arm shaped flanges.
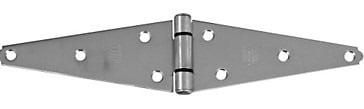
9. Pin Hinge
This type of hinge consist two flanges which are joined by pin. If the pin is removed then we can separate the flanges. This is generally used for heavy doors. Two flanges are separately fixed to the door and frame.
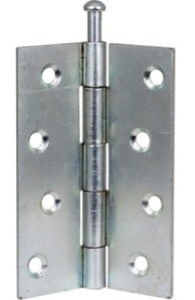
10. Nar-Madi Hinge
This is also used for heavy doors, but it consists only one flange which is fixed to the door. Pin is fixed to the frame to which flange is attached whenever is needed.
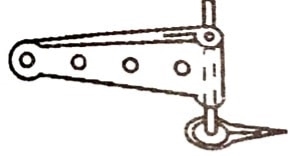
Bolts
Door or window bolts are used to provide security for the rooms. Different types of bolts are described below.
11. Hook and Eye Type Bolts
This type of bolt is used to keep the windows shutter in required position when it is opened. Hook is fixed to the shutter frame and eye is fixed to the window rail.
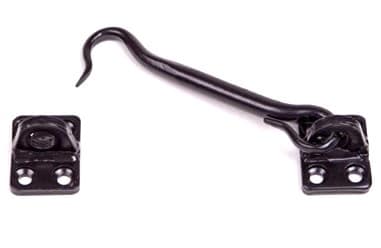
12. Flush Bolt
In case of flush bolt the bolt flush is desired to keep with the face of the door.
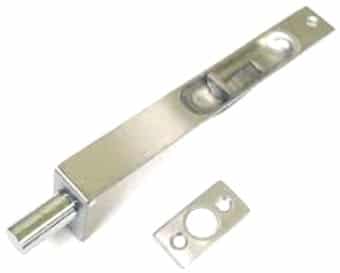
13. Aldrop Bolt
Aldrop bolt is olden type and most common type bolt. To lock this bolt pad locks are used.
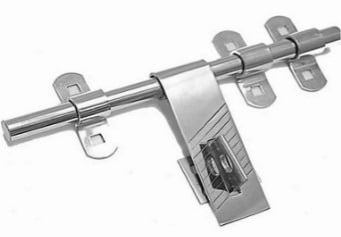
14. Barrel Bolt
To fix the back faces of doors barrel bolts are used. It contains socket and plate, socket is fixed to the frame and plate is fixed to the back face of door.
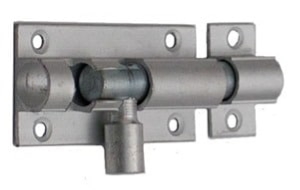
15. Espagnalette Bolt
This is used for highly secured doors and casement windows which cannot be reached easily.
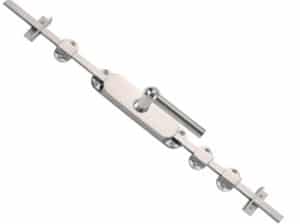
16. Hasp and Staple Bolt
This is also locked by using pad lock as aldrop bolt. Hasp is fixed to the door or window while staple is fixed to frame.
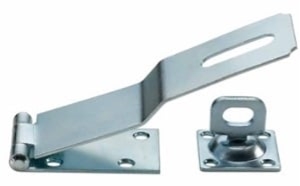
17. Handles
Handles are used to open or close the door or windows. There are many types of handles are available. Some of them are Bow type, Lever handle, Door handle, Wardrobe handle Etc.
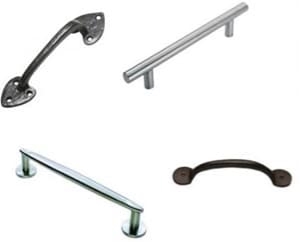
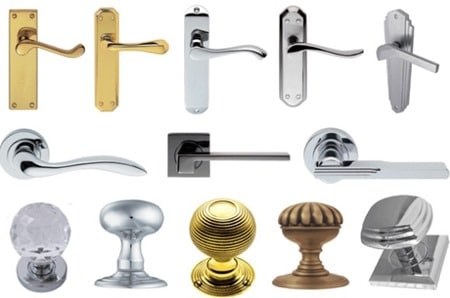
18. Locks
Locks used for doors and windows are many types and some of them are padlock, mortise lock, rim lock, cupboard lock and lever handle lock etc.
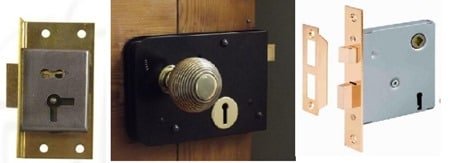