UNIT 4
HIGH POLYMERS
Polymer chemists study large, complex molecules that are built up from many smaller units. They study about the smaller building blocks combine, and create useful materials with specific characteristics by manipulating the molecular structure of the monomers/polymers used, the composition of the monomer/polymer combinations, and applying chemical and processing techniques that can to a large extent, affect the properties of the final product. Polymer chemists are unique within the chemistry community because their understanding of the relationship between structure and property spans from the molecular scale to the macroscopic scale.
It is a long molecule formed by joining together of thousands of small molecular units by chemical bonds. Polymers are giant molecules also called macromolecules that are essential to our existence. They are important chemicals in our bodies in plants (starch, cellulose) and in our everyday lives (fibers, plastics, elastomers). Polymers are made by transforming small molecules into molecules with very large molecular weights. Although the chemical properties of polymers are similar to those of analogous small molecules, their physical properties are quite different. Every polymer has its own characteristics, but most polymers have the following general properties:
Polymers can be very resistant to chemicals.
Polymers can be both thermal and electrical insulators.
Generally, polymers are light in weight with varying degrees of strength.
Polymers can be processed in various ways to produce thin fibers or intricate parts.
Polymer is a molecule formed by joining of thousands of smaller molecular units together by chemical bonds. A chemical process that leads to the formation of polymer is known as polymerization. Degree of polymerization: The number of repeat units monomeric units available in the polymer is known as degree of polymerization.
Functionality: The number of bonding sites or reactive sites or functional groups present in the molecule. Ex: The double bond in vinyl monomers (CH2 = CHX) can be considered as a site for two free valencies. When the double bond is broken, two single bonds become available for combination.
H2C=CHX → CH2 – CHX
1. When the functionality of monomer is two bifunctional linear (or) straight chain polymer is formed. Ex: (a)vinyl monomers (b)adipic acid (c)hexamethylene diamine (d)terephthalic acid(e)ethylene glycol (f )amino acid Example for polymer: HDPE (high density polythene)
2. When the functionality of monomer is three (tri-functional), threedimensional net work polymer is formed. Ex: phenol, glycerol Examples for polymers : Urea formaldehyde, phenol formaldehyde.
The process in which the simpler molecules combine together to form very large molecule having high molecular weight is known as polymerization. The molecule is known as polymer. The different ways of doing polymerization are –
By opening a double bond
Ex:
NCH2 = CH2 (CH2 – CH2)n
Ethane polythene
NCH2=CH (CH2 – CH)n
Cl Cl
Vinyl chloride polyvinyl chloride
Types of polymerization:
Polymers can be synthesized by the following polymerization processes:
- Addition polymerization or chain polymerization
- Condensation or step or step growth polymerization
III. Copolymerisation
Addition polymerization:
The addition polymerization is the process in which the liniking together of monomer molecules by a chain reaction is observed. Polymer synthesized by addition polymerization has the same empirical formula as that of monomer. No molecule is evolved during polymerisation and the polymer is an exact multiple of the original monomeric molecule.
Condensation polymerization:
An intermolecular reaction involving two different bifunctional reactants with affinity for each other and taking place through repeated condensation reaction is known as condensation polymerization.
Copolymerisation:
Addition polymerisation involving a mixture of two or more suitable or compatible monomers gives a copolymer and the process is known as copolymerization. A reaction in which a mixture of two or more monomers is allowed to undergo polymerisation is known as copolymerization. The polymer is known as copolymer.
E.g.: Copolymerization of styrene and methyl methacrylate
Synthetic or semi-synthetic polymers are plastics. Plastics used for industrial work come from petrochemicals. Plastic refers to its ability to deform without breaking. The polymer used in making plastics is usually a combination of additives, colorants, plasticizers, stabilizers, fillers, and reinforcements. These additives affect the chemical composition, properties, and mechanical properties of plastics and affect its cost.
Thermoplastic polymer: A thermoplastic is a resin that is solid at room temperature but becomes plastic and soft upon heating, flowing due to crystal melting or by virtue of crossing the glass transition temperature (Tg). Upon processing, usually via injection-molding or blow-molding-like processes, thermoplastics take the shape of the mould within which they are poured as melt, and cool to solidify into the desired shape. The significant aspect of thermoplastics is their reversibility, the ability to undergo reheating, melt again, and change shape. This allows for additional processing of the same material, even after being prepared as a solid. Processes such as extrusion, thermoforming, and injection molding rely on such resin behavior. Some common thermoplastic materials include polyethylene (PE), polycarbonate (PC), and polyvinyl chloride (PVC).
Thermosetting Polymer: A thermosetting resin, or thermosetting polymer, is generally a liquid material at room temperature which hardens irreversibly upon heating or chemical addition. When it is placed in a mould and heated, the most solidifies into the specified shape, but this solidification process includes the formation of certain bonds, called cross links, that hold the molecules in place and change the basic nature of the material, preventing it from melting. As a result, a there most, as opposed to a thermoplastic, cannot return to its initial phase, rendering the process irreversible. There most, upon heating, become set, fixed in a specific form. During overheating, there most tend to degrade without entering a fluid phase. Processes such as compression molding, resin transfer molding, pultrusion, hand lay-up, and filament winding depend on thermosetting polymer behavior. Some common there most include epoxy, polyimide, and phenolic, many of which are significant in composites.
Properties:
Property | Thermoplastics Polymer | Thermosetting Polymer |
Molecular Structure | Linear polymer: weak molecular bonds in a straight-chain formation | Network polymers: high level of crosslinking with strong chemical molecular bonds |
Melting point | Melting point lower than the degradation temperature | Melting point higher than the degradation temperature |
Mechanical | Flexible and elastic. High resistance to impact (10x more than thermosets). Strength comes from crystallinity | Inelastic and brittle. Strong and rigid. Strength comes from crosslinking. |
Polymerization | Addition polymerisation: repolymerised during manufacture (before processing) | Polycondensation polymerisation: polymerised during processing |
Microstructure | Comprised of hard crystalline and elastic amorphous regions in its solid state | Comprised of thermosetting resin and reinforcing fibre in its solid state |
Size | Size is expressed by molecular weight | Size is expressed by crosslink density |
Solubility | Can dissolve in organic solvents | Do not dissolve in organic solvents |
Service temperature | Lower continuous use temperature (CUT) than thermosets | Higher CUT than thermoplastics |
(1) Pigments
(2) Solvents
(3) Hardeners
(4) Lubricants
(5) Catalysts
(6) Plasticizers
(7) Fillers
Pigments: The pigments addition helps in two ways, namely, they act as fillers and they impart desired color to the plastics. They should be durable and adequately fast to light. The commonly used pigments are zinc oxides, etc. The selection of pigments should be done in such a way that their addition does not alter or affect the other properties of plastics.
Solvents: Solvents are used to dissolve the plasticizer. E.g.: addition of alcohol took place in cellulose nitrate plastics to dissolve camphor.
Hardeners: Hardeners are the compound used to increase the resins hardness. E.g.: hexamethylene tetramine acts as hardener for phenol formaldehyde.
Lubricants: Lubricants are the fluid, solid or plastic substance that is helpful in the control of friction by the introduction of friction-reducing film between moving surfaces in contact. There are many different forms of the substance which is helpful in lubrications. The most common substances that are used are oil and grease.
Catalysts: Catalysts are the compound that alters the reaction rate. The compounds that increases or decreases the reaction are called as the catalysts.
Plasticizer: The plasticizers are the organic compounds which are oily in nature and of low molecular weight. They are used to separate the polymer chain by a greater distance to make the crystallization difficult. A non-crystalline solid is thereby produced from a polymer that normally crystallizes.
Nylon-6:
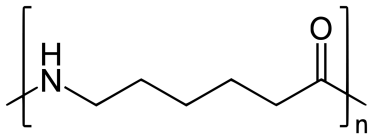
Nylon 6 is also called as the Polycaprolactam which is developed by Paul Schlack. They are semicrystalline polyamide.They have smooth surface and are featureless as a glass rods. Nylon 6 can be modified using comonomers or stabilizers during polymerization to introduce new chain end or functional groups, which changes the reactivity and chemical properties. It's often done to change its dyeability or flame retardance. Nylon 6 is synthesized by ring-opening polymerization of caprolactam. When caprolactam is heated at about 533 K in an inert atmosphere of nitrogen for about 4–5 hours, the ring breaks and undergoes polymerization. Then the molten mass is passed through spinnerets to form fibres of nylon 6.
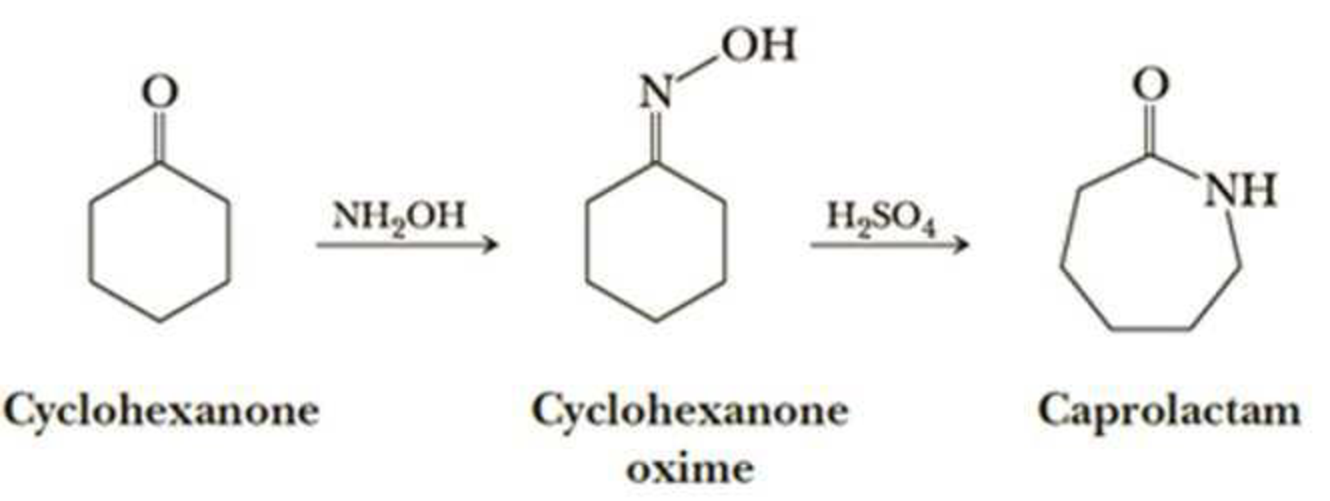
On further heating of Caprolactam at 533K with inert atmosphere of nitrogen for about 4-5 hours it gives
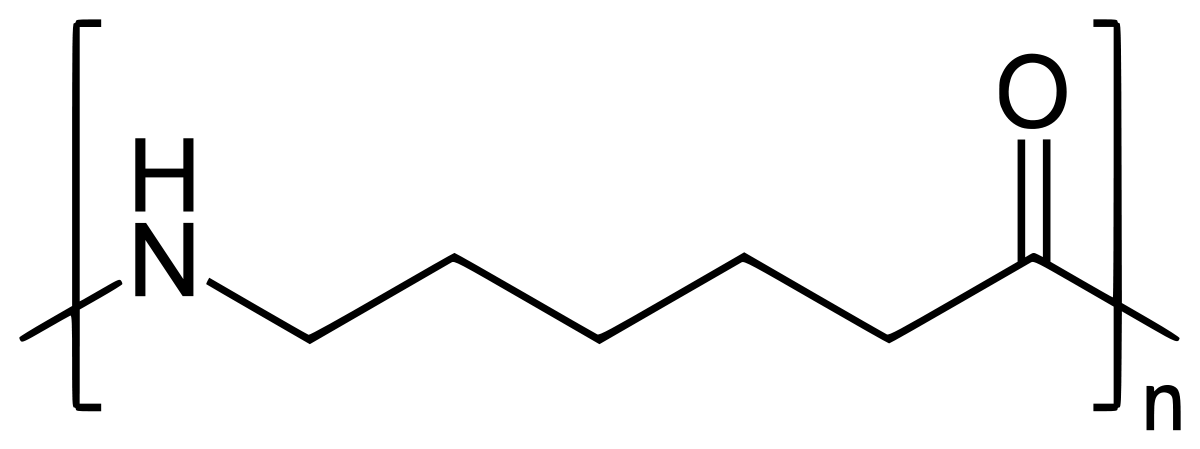
(Nylon-6)
Application:
(i) Nylon 6 is widely used for gears, fittings, bearings and automotive industry for various parts and as a material for power tools and housings.
(ii) It is used as threads in bristles for toothbrushes, surgical sutures and strings for acoustic and classical instruments.
(iii) It is used in production of large variety of ropes, filaments, nets as well as knitted garments.
Teflon: Teflon is also known as Fluon. It is obtained by the polymerization of water emulsion tetra fluoro ethylene under pressure in presence of benzoyl peroxide as catalyst
n F2C = CF2
( F2c– CF2 )n
Properties:- Due to the presence of highly electronegative fluorine atoms there are strong attractive force is responsible for high toughness & high chemical resistance towards all chemicals except hot alkali metal & hot fluorine.
Uses:-
- It is used in making seals & gaskets, which have to withstand high temperature.
- It is also used for insulation of electrical items and for making non-sticky surface coating, particularly for cooking utensils.
- Teflon used as insulating material for motors, transformers, cables, wires, fitting etc.
Bakelite:
Preparation of Bakelite

Properties: It is very smooth to mold the Bakelite. Molding is very smooth and retains any shape. They are resistant proof, scratch proof.
Applications and uses of Bakelite:
- This element has a low electrical conductivity and high heat resistance
- It can be used in manufacturing electrical switches and machine parts of electrical systems.
- It is a thermosetting polymer and Bakelite has high strength meaning
- It basically retains its form even after extensive molding.
- Phenolic resins are also extensively used as adhesives and binding agents. They are further used for protective purposes as well as in the coating industry.
Natural Rubber:- Natural Rubber is a high molecular weight hydrocarbon polymer represented by the formula (C5H8)x. It is obtained from a milk emulsion called latex by tapping the bark of the tree. “Heve a brasiliensis”. It is a polymer of isoprene units.
n H2C = C – CH = CH2 ( H2C – C = C – CH2 )n
CH3 CH3
The polymer chain of natural rubber is made of 2000 to 3000 monomer units.
Processing of Natural Rubber:- By cutting the bark of rubber tree the milky colloidal rubber milk is obtained. The main constituent of rubber latex is 25-45% of rubber and the remaining are water, protein & resinous materials. The rubber latex is coagulated by using 5% acetic acid and made in to sheets. The rubber sheets are cured under mild heat and then subjected to further processing.
Crepe rubber:- To the rubber latex a small amount of sodium bisulphate is added to bleach the colour and feed in to roller which produce 1mm or more thickness sheets which are dried in air at about 40- 500C. The dried thin sheet of rubber are known as “smoked crepe rubber”.
Mastication:- Rubber becomes soft and gummy mass when subjected to severe mechanical agitation. This process is known as mastication. Mastication followed by the addition of certain chemical (compounding) which is carried out on roll mills or internal mixers. After mastication is complete, the rubber mix is prepared for vulcanization.
Applications:
(i) The major application of natural rubber is in the manufacture of tyres.
(ii) In heavy duty tyres, the major portion of the rubber used is natural rubber.
(iii) The tank linings in chemical plants where corrosive chemicals are stored are prepared from rubber.
(iv) To reduce machine vibrations, rubber is used for sandwiching between two metal surfaces.
(v) Foam rubber is used for making cushions’, matrices, padding etc. toys and sports items are manufactured from natural rubber.
Vulcanization is a chemical process that converts natural rubber and other polydiene elastomers into cross-linked polymers. The most common vulcanization agent is sulfur. It forms bridges between individual polymer molecules when heated with rubber. Often a catalyst and initiator is added to accelerate the vulcanization process. The cross-linked elastomers have much improved mechanical properties. In fact, unvulcanized rubber has poor mechanical properties and is not very durable.
- Mixing of crude rubber with about 5-30% of sulfur (cross-linking agent) and other additives such as:
- Activator (commonly zinc oxide or stearic acid),
- Accelerator (guanidines, thiazoles, dithiocarbamates, xanthates, thiurams) ,
- Coagulants (acetic acid, calcium chloride),
- Anti-oxidants (amines, phenolics, phosphites),
- Color pigments,
- Surfacants,
- Softeners,
- Ant-foaming agents,
- Anti-tack agents (Rosin derivates, coumarone-indene resins, aliphatic petroleum resins, alkyl-modified phenol-formaldehyde resins).
Slow cross-linking starts at this stage. It is neccessary to avoid active vulcanization during mixing, which may cause cracks formation at the molding stage.
- Molding (shaping) the rubber mixture. The rubber must be shaped prior to heating stage since cross-linking makes shaping impossible.
- Heating the mixture to 250-400ºF (120-200ºC). Increased temperature speeds up the vulcanization process resulting in fast and complete cross-linking. C-S bonds replace C-H bonds linking chain polyisoprene molecules. Each link is formed by one to seven sulfur atoms.
Synthetic rubbers (Buna-S):
Buna-S is also known as the styrene-butadiene. It is a copolymer of butadiene (75%) and styrene (24%). Buna is derived from the Bu-Butadiene while Na is Sodium or Natrium and S is Styrine. Buna-S is the replacement of natural rubber while styrene, 2 monomers and butadiene play a major role in its derivation where as these 2 monomers is polymerized by two basically different process i.e., from solution (S-SBR) or as an emulsion (E-SBR). It is prepared by the copolymerization of butadiene & styrene.
It is a random co-polymer formed by the emulsion polymerization of a mixture of 1:3 butadiene and styrene in the presence of peroxide as a catalyst at 5o C and this is the reason why the product is called as cold rubber. The obtained rubber is called as the Styrene Butadiene Rubber (SBR).
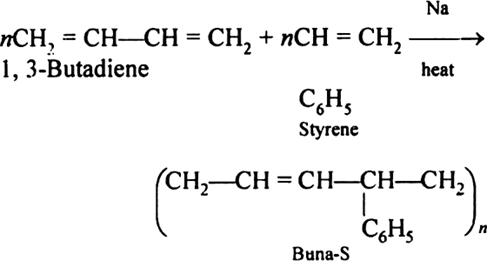
Applications:
(i) Buna-S is used as the natural rubber i.e., they are widely used in pneumatic tyres.
(ii) SBR is extensively used in coated papers.
(iii) They are highly used in building materials as a binding material.
SBR is also used as binder in lithium-ion battery electrodes.
Buna-N:
Buna-N are commonly used as elastomers. They are unsaturated synthetic co-polymer. They are obtained by the co-polymerisation of 1,3-butadiene and acrylonitrile in the presence of a peroxide catalyst. Nitrile rubber, NBR or Perbunan are another terms used for the Buna-N. They are synthetic rubber copolymer of acrylonitrile (ACN) and butadiene. Elastomers is natural or synthetic material which does not break when stretched and when released it return to its original length. The most important monomer used in preparing Buna-N is Acrylonitrile rubber which gives hardness, tensile strength, fuel and oil resistance. It usually contain 34% ACN. Grinding wheels can be made with nitrile rubber. When they are used for grinding smokes or fumes are emitted, which are known as acrid. The objectionable odor can be prevented if certain classes of diketones, which contain a conjugated system of two double bonds or unsaturated groups are added. Dibenzoylethylene, chloranil and anthraquinone help to prevent odor formation.

Buna-N are resistive to oil, fuel and other chemicals which means more Buna-N higher the resistance to oil but flexibility of the material is less. They are resistant to aliphatic hydrocarbons. They are non resistant to solvents but they may be attacked by ozone, ketones, esters and aldehydes.
Applications:
(i) They are used in the disposable non-latex rubbers, belts, gaskets.
They are used in preparation of adhesive and as a pigment binder.
Thiocol:
Thiocol is prepared by the condensation polymerization of sodium poly sulphide (Na2Sx) and ethylene dichloride (Cl CH2 CH2 Cl). In these elastomers, sulphur forms a part of the polymer chain.
Cl – CH2 – CH2 – Cl + Na – S – S – Na + Cl – CH2 – CH2 – Cl
(CH2 – CH2 – S – S – CH2 – CH2 )n + NaCl Thikol
Properties:-
(1) These rubbers possess strength and impermeability to gases.
(2) This rubber cannot be vulcanized because its structure is not similar to natural rubber and it cannot form hard rubber.
(3) It possesses extremely good resistance to mineral oils, fuels, oxygen, solvents ozone & sunlight.
Applications:-
(1) Fabrics coated with Thiokol are used for barrage balloons
(2) It is mainly used as solid propellant fuel for rocket
(3) It is also used for making gaskets, hoses, cable linings, tank linings etc.
(4) It is also used for printing rolls
(5) Containers for transporting solvents
(6) Diaphragms and seats in contact with solvents.
Lubricants are the fluid, solid or plastic substance that is helpful in the control of friction by the introduction of friction-reducing film between moving surfaces in contact. There are many different forms of the substance which is helpful in lubrications. The most common substances that are used is oil and grease. Grease is composed of oil and a thickening agent to obtain its consistency, while the oil helpful in lubrication. Oil can be a synthetic vegetable or mineral as well as a combination of these.
The application determines which oil, commonly referred to as the base oil and should be used. In extreme conditions, synthetic oils can be beneficial. Where the environment is of concern, vegetable base oils may be utilized. Lubricants containing oil have additives that enhance, add or suppress properties within the base oil. The amount of additives depends on the type of oil and the application for which it will be used. For instance, engine oil might have a dispersant added. A dispersant keeps insoluble matter conglomerated together to be removed by the filter upon circulation. In environments that undergo extremes in temperature, from cold to hot, a viscosity index (VI) improver may be added. These additives are long organic molecules that stay bunched together in cold conditions and unravel in hotter environments. This process changes the oil’s viscosity and allows it to flow better in cold conditions while still maintaining its high-temperature properties. The only problem with additives is that they can be depleted, and in order to restore them back to sufficient levels, generally the oil volume must be replaced. The roles of lubricant are -
- Reduce friction
- Prevent wear
- Protect the equipment from corrosion
- Control temperature (dissipate heat)
- Control contamination (carry contaminants to a filter or sump)
- Transmit power (hydraulics)
- Provide a fluid seal
Mechanism of lubrication:
(i) Fluid Film or Hydrodynamic Lubrication:
The shaft rotating in a bearing is supported by a layer or wedge of oil so that the shaft is not in contact with the bearing material. It is carried out with the help of liquid lubricants. In this mechanism, two moving and sliding surfaces are separated by thick film of lubricant fluid of about 1000A°, applied to prevent direct surface to surface contact and consequently reduce wearing and tearing of metals. Therefore it is known as thick film or fluid film lubrication or hydrodynamic lubrication. In this case fluid is formed by mixing of hydrocarbon oils and anti-oxidants with long chain polymer so as to maintain viscosity. Fluid film lubrication is useful in delicate and light machines like watches, clocks, guns, scientific equipments.
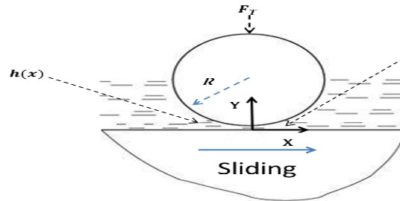
Lubrication film between the two contact surfaces is thick enough and two contact surfaces are separated completely by viscous oil film. At this time, frictional force of two contact surfaces are determined by viscous resistance of lubricant and it can take a very small value. Under this condition, when shaft also rotates due to the viscosity of the lubricant oil and generates oil pressure at the load area. This phenomenon is called wedge effect. The oil pressure P generated within lubricating oil film is affected by change of temperature and viscosity of lubricating oil, surface roughness, clearance and rotational speed of the shaft.
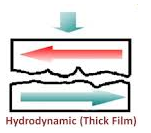
(ii) Thin Film or Boundary Lubrication:
It is carried out with grease and graphite & molybdenum disulphide lubricants. Boundary lubrication is a condition in which the lubricant film becomes too thin to provide total separation. In this type of lubrication a thin film of lubricant is adsorbed on the surface by weak Vander Waals forces. Thin film lubrication is operating at relatively low speed and high pressure. Lubricating oil film between the two contact surfaces is extremely thin and no viscous hydrodynamic oil film exists between the two contact areas, only film of absorbed oil molecules exists.
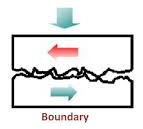
Absorptive oil film is arranged oil molecules that are adhered onto the solid surfaces and its shear resistance is greater than hydrodynamic oil film. Frictional force in this area is greater compare to hydrodynamic lubrication. In the frictional contact points, oil film is frequently broken. The lubrication condition that generates a frictional condition such as this is called boundary lubrication; in order to decrease the friction under this condition selection of self-lubricating bearing may be desirable.
Classification of lubricants:
Lubricants are classified on the basis of their physical state:
(i) Lubricating Oil
(ii) Semi-solid Lubricants (grease)
(iii) Solid lubricants
Lubricating Oil:
It plays the major role in reduction of friction between two moving metallic surfaces. The lubricating oil provides the fluid film in between the metallic surfaces those results in the friction reduction. Lubricants also act as the cooling medium, corrosion preventer.
Poroperties:
(i) They posses low pressure or high boiling point
(ii) Adequate viscosity for particular service condition
(iii) High oxidation resistance
(iv) They non-corrosive properties
They are further classified as-
Vegetable oils:
The petroleum industry existence took a several decades prior to its existence oil of the vegetable and animal origins were the most commonly used lubricants. They were very good for the use but due to their cost and the property of its to undergo oxidation easily tend to leave its presence. They were used as the blending agent with other lubricating oils to produce desired effects.
Mineral or petroleum oils: They are obtained by the petroleum distillation. The carbon chain varies from 12 to 50 carbon atom. They posses viscosity according to their chain length the shorter chain posses lower viscosity while vice versa for longer chain. This is one of the most widely used lubricants as because of its price and its availability. Crude liquid petroleum oils contain lot of impurities (like wax, asphalt, etc.) and consequently, they have to be thoroughly purified before being put to use.(i) The wax, if not removed, raises the pour-point and renders the lubricating oil unfit for use at low temperatures. (ii) Certain constituents get easily oxidized under working conditions and cause sludge formation. (iii) Some constituents mainly asphalt, undergo decomposition at higher temperatures, causing carbon deposition and sludge formation. A number of processes are used for removing these unwanted impurities by using Dew axing or acid refining or by solvent refining.
Semi-solid Lubricants (grease):
Lubricating grease is a semi - solid, consisting of a soap dispersed throughout liquid lubricating oil. The liquid lubricant may be petroleum oil or even synthetic oil and it may contain any of the additives for specific requirements. Greases are prepared by saponification of fat with alkali, followed by adding hot lubricating oil while under agitation. The total amount of mineral oil added determines the consistency of the finished grease. The structure of lubricating greases is that of a gel. Soaps are gelling agents, which give an interconnected structure containing the added oil. At high temperatures, the soap dissolves in the oil, whereupon the interconnected structures cease to exist and the grease liquefies. Consistency of greases may vary from a heavy viscous liquid to the of a stiff solid mass. To improve the heat-resistance of grease, inorganic solid thickening agents (like finely divided clay, bentonite, colloidal silica, carbon black, etc.) are added.
Greases have higher shear or frictional resistance than oils and, therefore, can support much heavier loads at lower speeds. They also do not require as much attention unlike the lubricating liquids. But greases have a tendency to separate into oils and soaps.
Grease is used:
(i) in situations where oil cannot remain in place, due to high load, low speed, intermittent operation, sudden jerks, etc. e.g. Rail axle boxes,
(ii) in bearing and gears that work at high temperatures
(iii) in situations where bearing needs to be sealed against entry of dust, dirt, grit or moisture, because greases are less liable to contamination by these
(iv) in situations where dripping or spurting of oil is undesirable, because unlike oils, greases if used do not splash or drip over articles being prepared by the machine. For example, in machines preparing paper, textiles, edible articles, etc.
Solid lubricants:
Solid lubricants are used at the place where liquid lubricant or grease cannot secured to be useful. The most usual solid lubricants used are graphite and molybdenum disulphide.
Graphite:
It is an allotropic form of the carbon atom (Allotropy form- When any element is formed in more than one form and in each form they posses different property). In graphite carbon are arranged in hexagonal ring form and each form is arranged upside down to form the layer and are attached together by weak Vander-wall’s forces. Graphite is the most stable form of the carbon. It is the good conductor of heat and electricity. The two major known form of graphite are alpha (Hexagonal) and Beta (Rhombohederal).
Structure:
The carbon atom is sp2 hybridized that means there is 4 valence electron in their outermost shell as in the diamond the all 4 valence electron are covalently bonded while in graphite the 3 electron makes a covalent bond while the remaining 1 electron are free. The interconnection of these carbon atoms forms the hexagonal structure. The C-C bond bond length is 1.42 Angstrom. This hexagonal layer attached toward each other by weak Vander Wall forces at a distance of 3.35 Angstrom. This is the reason why graphite is soft.
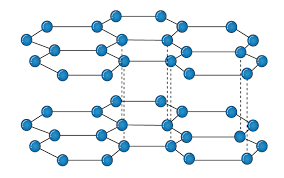
Properties:
Conducting Property: As the carbon of Graphite are sp2 hybridized that means the p orbital remain vacant of the carbon atom this tend to overlapping of the vacant P-orbital. This overlapping of the vacant orbital is responsible for the movement of electrons in parallel on their vacant orbital that is why Graphite shows the conducting property.
Lubricating Property: There is presence of weak Vander Wall forces between two layers due to these weak forces the two layers are flexible in nature which in result make the Graphite to be used for Lubricating purpose.
Applications:
1-Graphite can be used as the solid lubricant
2-Graphite can be used as conductor.
3-Graphite can be used as the electrodes.