UNIT 2
MATERIAL
The main techniques of material control are as follows
- ABC Analysis
- Determination of stock levels
- Economic Order Quantity (EOQ) Analysis
- Perpetual Inventory System
- Periodic Annual Inventory Control System
- VED Analysis.
- ABC analysis - In the nineteenth century, the concept of ABC Analysis was coined by Pareto, an Indian philosopher. It is a value-based system of material control. In this technique materials are analyzed according to their value which means greater attention and care are given costly and more valuable materials.
All items of materials are classified according to their value—high, medium and low values, which are known as A, B and C items respectively. ABC technique is some time called as “Always better control” method.
“A” item - These are high value items which may consist of only a small percentage of the total items handled. These materials are kept under the tightest control and the responsibility of the most experienced personnel.
‘B’ Items: These are medium value materials which should be under the normal control procedures.
‘C’ Items: These are low value materials which may represent a very large number of items. These materials are kept under the simple and economic methods of control.
Thus classifying the material in A,B,C category ensures that the management focuses on ‘A’ item where tightest control should be installed. B items may be given less attention and C items least attention.
For example
2. Determination of stock levels - After the material classification and codification is done for all the materials, for each material code we have to fix the Minimum Level, Maximum Level, Re-order Level and Re-order Quantity. It is the storekeeper’s responsibility to ensure inventory of any material is maintained between the Minimum Level and Maximum Level.
Maximum Level:
The Maximum Level indicates the maximum quantity of an item of material that can be held in stock at any time. The stock in hand is regulated in such a manner that normally it does not exceed this level. While fixing the level, the following factors are to be taken into consideration:
- Rate of consumption of material
- Risk of obsolescence and deterioration
- Storage space available
- Cost of storage and insurance
- Availability of funds needed
- Seasonal considerations, e.g. Bulk purchases during seasons at low prices
- Reorder Quantity
Maximum Level = Re-Order Level + Re-Order Qty – (Minimum Rate of Consumption X Minimum Re- Order Period)
Minimum Level:
The Minimum Level indicates the lowest quantitative balance of an item of material which must be maintained at all times so that there is no stoppage of production due to the material being not available.
Minimum Level = Re-Order level – (Normal Rate of Consumption X Normal Re
Order Period)
Re-Order Level:
When the stock in hand reach the ordering or re-ordering level, store keeper has to initiate the action for replenish the material. This level is fixed somewhere between the maximum and minimum levels in such a manner that the difference of quantity of the material between the Re-ordering Level and Minimum Level will be sufficient to meet the requirements of production up to the time the fresh supply of material is received.
Re-Ordering level= Minimum Level + Consumption during lead time
= Minimum Level + (Normal Rate of Consumption × Normal Re-order Period)
Danger Level:
It is the level at which normal issue of raw materials is stopped and only emergency issues are only made. This is a level fixed usually below the Minimum Level. When the stock reaches this level very urgent action for purchases is indicated. This presupposed that the minimum level contains a cushion to cover such contingencies. The normal lead time cannot be afforded at this stage
Danger Level = Normal Rate of Consumption × Maximum Reorder Period for emergency purchases
3. Economic order quantity analysis - Economic order Quantity is also termed as Re-order Quantity. Economic Order Quantity is that size of the order which gives maximum economy in purchasing any material and ultimately contributes towards maintaining the material at the optimum level and at minimum cost.
Two types of cost are taken into consideration while fixing economic order quantity
- Ordering cost – ordering cost refers to the cost of placing on order with the supplier. It includes Cost of staff posted in the purchasing department, inspection section and payment department. Cost of stationery, postage and telephone charges, etc.
- Carrying cost – carrying cost refers to the cost of holding the materials in the store. It includes Cost of storage space which could have been used for some other purpose, Transportation cost in relation to stock, insurance cost, clerical cost, etc
Formula
Where,
- EOQ = Economic Order Quantity
- 2 = It is a constant figure
- A = Annual consumption of materials in units or rupees
- S = Cost of placing an order
- I = Annual carrying cost of storing one unit.
4. Perpetual inventory system - This is a system of stock control in which continuous record of receipt and issue of materials is maintained by the stores department. It shows the physical movement of stocks and their current balance. It means the system of stock records that will show the receipts, issue and balance of all items in stock at all times.
The Chartered Institute of Management Accountants London defines the perpetual inventory system as, “a system of records maintained by the controlling department, which reflects the physical movements of stocks and their current balance.”
5. Periodic/annual inventory control system–the stock-taking is undertaken at the end of the accounting year, under this system. The stock taking involves verifying the physical quantities of stores in hand. The annual stock- taking should be organized well in advance to minimize production holds up.
The following points are considered while conducting periodic stock verification:
- To control the whole operation a person should be appointed.
- While stock verification is going on, store room should not be opened for issues and receipts.
- All damaged, deteriorated or used items must be recorded separately.
- The stock-taking sheets must be under the control of one individual.
- Materials received should be listed separately but still under inspection.
- Make each person responsible for a particular section.
- Show the method of check i.e. count, weight, measurement on the stock sheet for each item.
6. VED analysis - VED-vital, essential, desirable, analysis. It is used primarily for control of spare parts. Keeping in view the criticality to production, the spare parts can be divided into three categories-vital, essential and desirable.
The spares, the absence of which even for a short time will stop production for quite some time and where the cost of stock out is very high, are known as vital spares.
The spares, the absence of which cannot be tolerated for more than a few hours or a day and the cost of lost production is high and which are essential for the production to continue, are known as essential spares.
The desirable spares are those spares which are needed but their absence for even a week or so will not lead to stoppage of production.
Accounting for purchase
The purchase is the result of exchanging values for material and work by means of money or its equivalent for the satisfaction of need and for generating profit in business by the process of purchasing and selling.
Purchasing involves procurement of materials of requisite quantity and quality at economic price. It is of extreme importance particularly to a manufacturing concern because it has bearing on all vital factors of manufacture such as quantity, quality, cost, efficiency, economy, prompt delivery, volume of production and so on. Purchase department in a business concern can be organized into two types i.e. Centralized Purchasing System and De-centralized Purchasing System. Purchasing process in most of the organisation is a centralised function because the advantages of a centralised purchasing out weight its disadvantages.
Types of purchase
All purchase revolves around cash purchase and credit purchase and any purchase can be made in cash or on credit.
Cash purchase – the cash purchase is the purchase which is made on payment against getting anything on the spot or exchange of value on the spot.
The following double entry is made when a cash purchase is made;
Purchase (debit/ income statement)
Cash (credit/ asset)
The purchase is debited to purchase account which belongs to the cost of goods sold and cash is credited to cash account decreases assets of an entity.
Credit purchase – credit purchase is the purchase made later under an agreement or mutual understanding of seller and purchaser. Like this purchase, goods are obtained without paying cash and cash is paid later.
The following double entry is made when credit purchase is the liability of purchaser and assets of seller when it is made
Purchase (debit)/ income statement
Account payable (credit) liability
When the liability is paid, the balance in payable account will be reduced and to zero as ;
Account payable (debit)/ liability
Cash (credit)/assets
Purchase Requisition
Purchases Requisition is a request made to the Purchase Department to procure materials of given description and of the required quality and quantity within a specified period. It is a formal request and it authorizes the Purchase Department to issue a Purchase Order to secure materials intended for periodic requirements of a given material or materials to provide guidance to the Purchase Department to estimate the future requirements in order to secure maximum purchase benefits in the form of higher discount and better credit terms. The extent and range of materials requirements provide a basis for preparation of a purchase budget. The actual requirements of a given period can be summarized from the purchases requisition and compared with the purchase budget in order to determine the variances and the reasons thereof. This form is prepared by storekeeper for regular items and by the departmental head for special materials not stocked as regular items.
The Purchase Requisition is prepared in three copies. Original will be sent to Purchase department, Duplicate copy will be retained by the indenting (request initiating) department and the triplicate will be sent to approver for approving the purchase requisition.
Purchase Requisition provides the three basic things:-
- What type of material is to be purchased?
- When to be purchased?
- How much is to be purchased?
The specimen form of Purchase Requisition is as shown below:
X Ltd | |||||
Purchase Requisition or Indent | |||||
Purchase Req Type: Special / Regular :
Purchase Req No : Purchase Requisition Date : Department: | |||||
S.No | Material Code | Description Of the Goods | Quantity Required | Material Required by date | Remarks |
|
|
|
|
|
|
Requestedby Approved by
For use in Purchase Dept. Quotations from
(1) PO Placed : Yes /No (2) PO No: (3) |
Purchase order
Purchase Order (PO) is a request made in writing to selected supplier to deliver goods of requisite quality, quantity, (as per the purchase requisition) at the prices, terms and conditions agreed upon. It is a commitment on the part of the purchaser to accept the delivery of goods contained in the Purchase Order if the terms included therein, are fulfilled. Purchase Order contains the following details :-
(a) Purchase Order No; (b) PO Date; (c) Supplier Name and Address; (d) Material Code; (e) Material description; (f) Grade & Other particulars of the material; (g) Quantity to be supplied; h) Price; i) Place of delivery; j) Taxes; k) Terms of Payment (Credit period) etc
Usually a purchase order is made in five copies, one each for suppliers, Receiving/Stores Department, Originating Department, Accounts Department and filing. Thus we see that all the departments concerned with the materials are informed fully about all the details of every purchases and it becomes easier for everyone to follow up on any relevant matter.
X Ltd | |||||||
Purchase Order | |||||||
To |
|
|
|
|
| PO No: |
|
Supplier XXXXXX |
|
|
|
| PO date: |
| |
Address |
|
|
|
|
| Quotation Reference: PR No: |
|
Please supply the following items in accordance with the instructions mentioned there in On the following terms and conditions. | |||||||
S.No | Material Code | Material Description | Quantity | Rate per Unit | Amount | Delivery Date | Remarks |
|
|
|
|
|
|
|
|
|
|
|
|
|
|
|
|
|
|
|
|
|
|
|
|
|
|
|
|
|
|
|
|
|
|
| Packing & Freight |
|
|
| |
|
|
| Taxes |
|
| ||
|
|
| Total Amount |
|
| ||
Delivery: Goods to be delivered at | |||||||
Delivery date: | |||||||
Payment Terms: | |||||||
Authorized signatory |
Material storage and control
Once the material is received, it is the responsibility of the stores-in-charge, to ensure that material movements in and out of stores are done only against the authorized documents. Stores-in-charge is responsible for proper utilization of storage space & exercise better control over the material in the stores to ensure that the material is well protected against all losses such as theft, pilferage, fire, misappropriation etc.
Duties of store keeper:
The duties of store-keeper are as follows:-
- To exercise general control over all activities in stores department.
- To ensure safe storage of the materials.
- To maintain proper records.
- To initiate purchase requisitions for the replacement of stock of all regular materials, whenever the stock level of any item in the store reaches the Minimum Level.
- To initiate the action for stoppage of further purchasing when the stock level approaches the Maximum Level.
- To issue materials only in required quantities against authorized requisition documents.
- To check and receive purchased materials forwarded by the receiving department and to arrange for storage in appropriate places.
Different classes of stores:-
Broadly speaking, there are three classes of stores
- Central Stores
- Decentralized stores
- Sub-Store (Imprest Store)
Centralized stores:
The usual practice in most of the concerns is to have a central store. Separate store to meet the requirements of each production department are not popular because of the heavy expenditure involved. In case of centralized stores materials are received by and issued from one stores department. All materials are kept at one central store. The advantages and disadvantages of this type of store are set out as follows:
Advantages of centralized stores:
- Better control can be exercised over stores because all stores are housed in one department. The risk of obsolescence of stores can be minimized.
- The economy of staff-experts, or clerical, floor space, records and stationery are available.
- Better supervision is certainly possible.
- Obsolescence of the stores items can be kept under strict vigil and control.
- Centralized material handling system can be put into operation thus further economizing on space, personnel and equipments.
- Investment in stocks can be minimized.
Disadvantages of centralized stores:
- The transportation costs of the materials may increase because the movements of the stores may be for a greater distance since the storing is centralized.
- If the user departments are far away from the stores there may be delay in receipt of the stores by those departments.
- Breakdown of inter-departmental transport system may hold up the entire process, and similarly labour problem in the centralized stores may bring the entire concern to standstill.
- There is greater chance of losses through fire, burglary or some other unhappy incidents.
- It may not be safe to have some hazardous elements bunched together in the centralized stores.
Decentralized stores:
Under this type of stores, independent stores are situated in various departments. Handling of stores is undertaken by the store keeper in each department. The departments requiring stores can draw them from their respective stores situated in their departments. The disadvantages of centralized stores can be eliminated, if there are decentralized stores. But these types of stores are uncommon because of heavy expenditure involved.
Central stores with sub-stores:
In large organizations, factories / workshops may be located at different places which are far from the central stores. So in order to keep the transportation costs and handling charges to the minimum level, sub-stores should be situated near to the factory. For each item of materials a quantity is determined and this should be kept in the stock at the beginning of any period. At the end of a period, the store keepers of each sub-store will requisition from the central stores the quantity of the materials consumed to bring the stock up to the predetermined quantity. In short this type of stores operates in a similar way to a petty cash system, so this system of stores is also known as the imprest system of stores control.
Advantages:
- It ensures the prompt issue of stores.
- It confines the advantages of centralized stores with sub-stores and at the same time it does not sacrifice the centralized control.
- It reduces handling cost of materials.
- It avoids the maintenance of elaborate inventory records.
Issue of materials
Materials are kept in the stores so that store keeper may issue them whenever the production department requires these. A storekeeper can issue materials when authorized material requisition is presented to him.
A material requisition is the most important document of an authority to the storekeeper to issue materials. This request is written in a paper from production department to store department. An authorized person signs the document so as to prevent wrong drawl of materials.
Three copies are prepared and two copies are sent to the store and one copy is sent to the costing department. It includes date, requisition number, description of materials, quantity, unit price, total value, etc
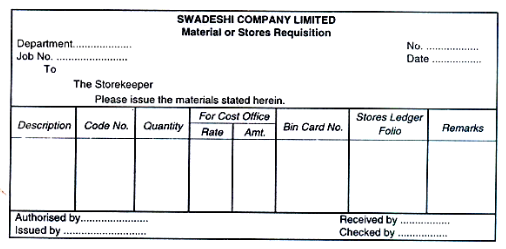
The important methods followed in pricing of issue of materials are as follows
- First in – First Out Method:
It is a method of pricing the issue of materials in the order in which they are purchased. In other words the materials are issued in the order in which they arrive in the store. This method is considered suitable in times of falling price because the material cost charged to production will be high while the replacement cost of materials will be low. In case of rising prices this method is not suitable.
Advantages of FIFO:
- It is simple and easy to operate.
- In case of falling prices, this method gives better results.
- Closing stocks represents the market prices.
Disadvantages:
- If the prices fluctuate frequently, this method may lead to clerical errors.
- In case of rising prices this method is not advisable.
- The material costs charged to same job are likely to show different rates.
2. Weighted Average Price Method:
This method removes the limitation of Simple Average Method in that it also takes into account the quantities which are used as weights in order to find the issue price. This method uses total cost of material available for issue divided by the quantity available for issue.
Issue Price = Total Cost of Materials in stock / Total Quantity of Materials in stock
3. LIFO (Last in first out method):
Under this method most recent purchase will be the first to be issued. It means the most recently items produced are sold first. The issues are priced out at the most recent batch received and continue to be charged until a new batch received is arrived into stock. It is a method of pricing the issue of material using the purchase price of the latest unit in the stock.
Advantages:
- Based on the replacement cost Stocks issued at more recent price represent the current market value
- It is simple to understand and easy to apply.
- Since material cost is charged at more recent price, product cost will tend to be more realistic
- It minimizes unrealized inventory gains and tends to show the conservative profit.
Disadvantages:
- Valuation of inventory under this method is not acceptable in preparation of financial accounts.
- It renders cost comparison between jobs difficult.
- It involves more clerical work and sometimes valuation may go wrong.
4. Simple average cost method- The simple average price is calculated by adding the different prices paid during the period for the batches purchased by dividing the number of batches.
For example, three batches of materials received at Rs. 10, Rs. 12 and Rs. 14 per unit respectively.
The simple average price is calculated as follows:
Rs. 10 + Rs. 12 + Rs. 14/3 batches = Rs. 36/3 batches = Rs 12 per unit
The main disadvantages of this method are it only takes into consideration the prices of different batches but not the quantities purchased in different batches.
Advantages:
- This method is easy to operate.
- It gives reasonably accurate results if prices are stable.
Disadvantage:
- Materials are not priced at actual costs.
- It does not take into account the quantity of materials purchased.
- Verification of closing stock becomes difficult.
- When price and quantity of different lots are widely fluctuates, this method gives incorrect result.
5. Standard cost - Under this method, material issues are priced at a predetermined standard issue price. Any variance between the actual purchase price and standard issue price is written off to the Profit and Loss Account. Standard cost refers to predetermined cost set by the management before the actual material costs being known and the standard issue price is used for valuation of closing stock and all issues to production.
Advantages
- If initially the standard price is set carefully then it reduces all the clerical work and errors tremendously
- The stock recording procedure is simplified.
- By eliminating fluctuations in cost due to material price variance, the realistic production cost comparisons can be made easier.
6. Replacement cost–This method also refers to market price method. The replacement cost is a cost at which identical material can be replaced by purchasing at the date of pricing material issues; as distinct from the actual cost price at the date of purchase. The replacement price is the price of replacing the material at the time of issue of materials or on the date of valuation of closing stock.
The term replacement price has been defined by the Institute of cost and management accountants of England as
“the price at which there could be purchase of an asset identical to that which is being replaced or revalued.
Treatment of material surplus
The requisition received by the storekeeper is serially numbered and the details relating to the quantity issued and number of the stores requisition are entered in the issue column of the bin card. Then the requisitions are sent to the cost office where rate and amount columns are filled and entries are made in the store ledger and job ledger
Sometimes excess material is issued for a particular work to facilitate convenient handling. In such case full quantity is charged to the job or work order and surplus materials of that job may either be returned to stores or transferred to other job.
Return of surplus material
A Material Returned Note or Stores Debit Note or Shop Credit Note is prepared in the department when excess materials are returned to the stores. Three copies are prepared and signed by the storekeeper as a token of receipt of the surplus material and keeps one copy of the same with him for making entries on the receipt side of the bin cards.
The second copy is sent to the cost office for making entries in the stores ledger and for giving credit to the particular job where the materials is in excess and returned.
The third copy is sent to the department which returns the surplus material.
The format is given below
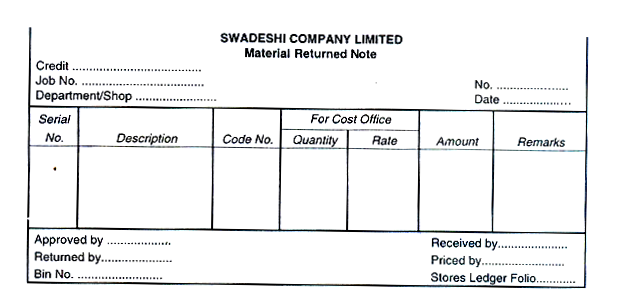
Transfer of surplus materials
As far as possible Transfer of excess materials from one job to another job should be avoided. The main reason is that record for the transfer may not be made and actual material cost for job may be inaccurate. An exception is given when return of surplus material to the stores may be costly due to the distance or excessive amount of handling charges. Thus materials are transferred to another job which is near the transferring job.
This will result in saving transport cost from the transferring job to the store. Transfer of materials from one job to the other job is to be allowed with the preparation of Material Transfer Note.
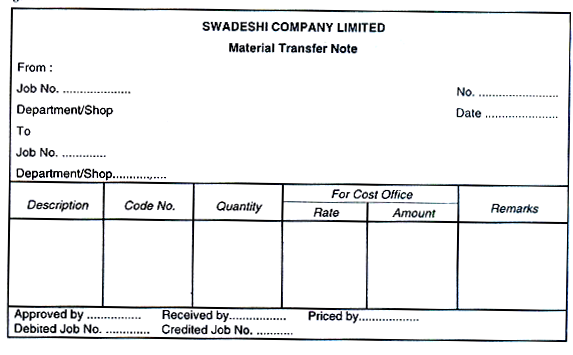
In the department Material Transfer Note is prepared where the material is in excess and one copy of the note is sent to the cost office for making necessary records. The job receiving the material is debited and the job transferring the material is credited.