UNIT 4
Overheads 1
All indirect costs are collectively termed as overheads. It is total of all indirect material, indirect labour and indirect expenses. They constitute an important component of total cost of a product, a job or a process. Overhead costs have to be incurred for production although they are not directly measurable, observed related to specific activity or unit of production. For example: depreciation of factory building and machinery, rent, taxes, insurance, maintenance etc
Classification of overheads
The process of grouping the overheads according to their common characteristics is known as classification of overheads. It provides the manager with information that enablesthem to manage the business effectively. The overheads can be classified according to:
a) a.Element: Indirect materials, Labour Expenses;
b) b.Functions: Production, Administration, Selling and Distribution overheads;
c) c.Behaviour: Fixed,Variable, and Semi-variable overheads.
- Fixed overheads remain fixed and are unaffected by the changes in the level of production. For example, rent, rates, salaries, legal expenses etc.
2. Variable overheads vary in direct proportion to changes in the volume of production, such as indirect materials, fuel, power, stationery, salesmen’s commission etc.
3. Semi-variable overheads are the expenses which are partly fixed and partly variable.
They remain fixed upto a volume of production and vary when the production is made beyond the particular volume. For example, telephone charges depreciation of machinery, repairs and maintenance, cost of supervision etc.
Allocation of overheads
Allocation of overheads is the Reallotment’ of all items of cost of cost centers or cost to units. It refers to charging overheads to the cost centers. It means that overheads have been incurred because of the existence of that cost centre. When the company provides more than one product, factory overheads are allocated to various production departments or cost centers. Proper overheads allocation is of great importance as wrong allocation can distort income determination, asset valuation and performance evaluation. The overhead allocation process is as follows:-
- Accumulating overheads on the basis of departments or products.
- Identifying the cost objectives of the allocated costs
- Selecting the method of relating costs so accumulated to the cost objectives.
Apportionment of overheads
Apportionment of Overheads refers to the distribution of common items of cost to two or more cost centers on some appropriate basis. When overheads are incurred for the factory as a whole and benefit two or more cost centers, it is necessary to apportion them to different departments that receive benefits from such overhead costs. For example, factory rent benefits all the departments; hence it should be apportioned to all the departments on the basis of the floor arean occupied by each department in factory. Thus, common factory overheads have to be apportioned to various production and service departments in the factory on some appropriate basis.
A production department is one that engages in the actual manufacture of product. On the other hand, service department is one that renders a service which contributes indirectly in the manufacture of the product. It renders services to the production as well as other service departments.
The common factory overheads are to be apportioned to various production and service departments on some equitable basis which are called principles of apportionment. Accordingly, overheads are distributed over various departments on the basis of actual benefit received or potential benefits to be received by the respective departments Overheads can also be apportioned on the specific criteria or given ratio which may be determined after careful survey for different service functions. Apportionment of overheads can also be made on the basis of ability to pay (Revenue) of the departments.
The usual basis of apportionment of commonitems of factory overheads can be stated a follows:-
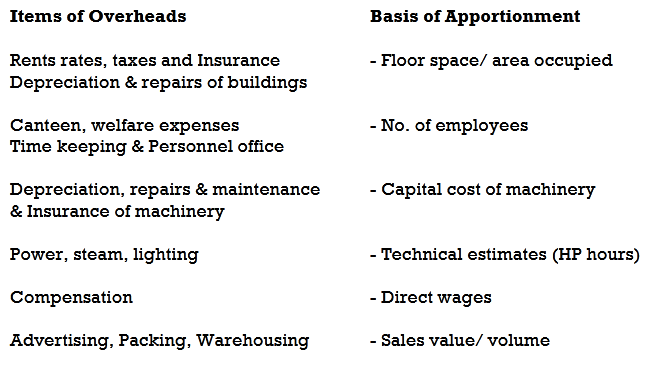
CIMA defines Absorption of Overheads as “the process of absorb, overhead costs allocated or apportioned over a particular cost centre or production department by the units produced”.
The overhead absorption rate is calculated as follows:
Methods of Overhead Absorption:
- Production Unit Method: Under this method, overhead absorption rate is calculated by dividing the overhead cost by number of units produced or expected to be produced as shown below:
2. Percentage of Direct Material Cost Method: Under this method overhead is absorbed based on the actual or predetermined absorption rate calculated by expressing the overhead cost as percentage of direct materials for the same period.
3. Percentage of Direct Labour Cost Method: Under this method, overhead absorption rate is calculated by expressing the overhead expense to be absorbed as a percentage of cost of direct labour for the same period, as shown below:
4. Percentage of Prime Cost Method: This method is a combination of both direct material cost and direct labour cost method. The overhead absorption is calculated as follows:

5. Direct Labour Hour Rate Method: Under this method, overhead absorption rate is calculated by dividing the overhead with the number of direct labour hours.

6. Machine Hour Rate Method: CIMA defines Machine Hour Rate as an “actual or predetermined rate of cost apportionment or overhead absorption, which is calculated by dividing the cost to be apportioned or absorbed by a number of hours for which a machine or machines are operated or expected to be operated.”

Application of overhead absorption rate
For the application of pre-determined absorption rates, the actual (i.e., the actual number of units or other actual base data e.g., direct labour hours, machine hours etc.,) is multiplied by the predetermined rate. The resultant amount will give the amount of overhead to be applied (or charged) to production for the period.
It is seldom applied overheads agree with the actual overheads. There will always be a difference between the actual overheads and applied overheads. If the absorbed amount exceeds actual overhead, the difference would be called as “over applied overhead”. If however, it falls short of actual overhead, the difference would be called ‘Under applied overhead”.
On the basis of predetermined overhead absorption rate the overhead are absorbed according to the actual production of goods throughout the accounting period or specific period. To determine overhead rate budgeted overheads and budgeted output are used. If budgeted overhead and budgeted outputs differ from actual overhead and actual output, three is a difference between predetermined overhead rate and actual overhead rate.
Over absorption refers to the overheads absorbed are higher than the actual overheads incurred. Under absorption refers to the overhead absorbed is lower than the actual overheads incurred during the accounting period.
Reasons for Over or Under absorption of overhead
- The actual hours worked is more or less than budgeted hours
- The actual overhead costs are different from budgeted overheads
- The method of overhead absorption may be wrong
- Unexpected expenses may be incurred during the accounting period.
- Seasonal fluctuations in the overhead expenses from period to period
- Both actual overhead costs and actual activity level are different from the budgeted costs and level.
Treatment of over or under absorbed overheads
- Application of supplementary rates - The supplementary rate is calculated by dividing the under or over absorbed amount by the actual base. The over recovered amount will be adjusted by applying the supplementary rate and vice versa, in case of over absorption.
2. Adjustment to cost of sales - The over or under absorbed overheads is closed and transferred to the cost of sale account. This is done at the end of every month or at the end of accounting period by the Cost Accountant. If the transfer is made at the end of the accounting period, the over/under-absorbed overhead is carried forward from month to month treating it as deferred income if over applied and as deferred charges, if under applied.
3. Write off to Costing Profit and Loss Account - If the over or under absorbed overhead is small, and then it will be written off by transferring it to the costing profit and loss account.
4. Adjusted to gross profit - The under or over absorbed overhead balances are closed by entering the adjustment in gross profit.
5. Carry forward to subsequent years - The under or over absorbed overhead may be carried forward to the subsequent accounting year and are transferred to Overhead Suspense Account or Overhead Reserve Account. This Overhead Suspense Account or Overhead Reserve Account will be shown in the Balance Sheet. The under or overhead absorption debit and credit balances are shown in the asset and liabilities side of the balance sheet.
Capacity means the ability of a company to produce a product or provide a service within a given period of time. It is defined by constraints such as space, labor, materials, equipment and access to capital.
- Normal capacity - normal capacity is based on the theory of operational efficiency. Normal capacity is driven by business demand not by maximum capacity. It is estimated over a two- to three-year period taking into consideration the seasonal and cyclical demand cycle. A rule of thumb is to take normal activity to represent 75% to 90% of practical capacity.
2. Expected capacity – expected capacity is based on actual inputs and is updated version of normal capacity. The capacity is expected to prevail over the next year. This method is more appropriate than normal capacity when environmental conditions prevent reliable forecasts being made for periods in excess of one year.
3. Practical capacity – practical capacity is also known as human error or "Murphy's law.". It involves the level of capacity a business can operate at that allows for a certain amount of inefficiency. It is based on theory not on actual demand like ideal capacity. It takes into consideration loss due to weather, holidays, repairs and breakdowns. Depending on nature of business practical capacity may be lower or higher than normal or expected capacity. Practical capacity is always lower than maximum or ideal capacity.
4. Ideal capacity - when the volume of activity is at its peak performance, with no allowance for operational inefficiency refers to ideal capacity. This is also referred to as theoretical capacity or maximum capacity and is often used as the upper limit for determining capacity limitations. Normal capacity and expected capacity will always be lower than ideal capacity.
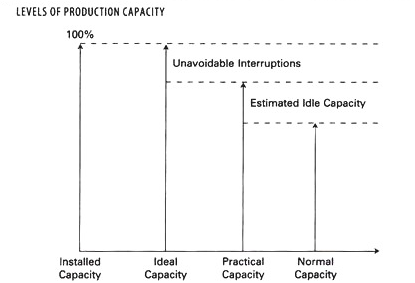
There is a gap between the 100% maximum of ideal capacity and the more realistic practical capacity due to inevitable but acceptable interruptions. Between practical capacity and normal capacity there is a gap which allows for the contingencies of uncertainty and environmental fluctuations.