UNIT 1
INTRODUCTION TO COST ACCOUNTING
Modern business needs information about activities to be planned for the future. A major function of management is decision- making. It requires selection of an optimal course of action from among a set of alternatives. Costing techniques play an important role in gathering and analyzing revenue and cost data. It also helps to control business results and to make a proper appraisal of the performance of persons working in an organisation. Cost accounting also helps in acquiring Plant and Machinery, adding or dropping product, make or buy decision, special pricing of products and replacement of assets.
The widespread interest in the subject of cost accounting could be said to have developed with Industrial Revolution, which started in 1760. As mechanization, simplification, standardization and mass production followed in the wake of factory system, costing had to keep pace with these developments. Until the 18th century, cost accounting was in the domain of the engineer. Its integration with financial accounting began when accountants started to audit the cost records. Under the influence of financial accountant, cost accounting came to be viewed almost exclusively as a means of inventory valuation and profit measurement. It has grown only in the 20th century as an independent discipline.
Cost accounting has found to be of assistance to management, in compiling and providing requisite statistical data. It has developed rapidly and assisted management in providing valuable information to take appropriate decision in time. Cost Accounting throws light on the excessive waste of materials, inefficient labour operations, idle machinery and many other similar factors, which are responsible for reduction in the profit of the business activities. Managements found that cost accounting could render valuable assistance in planning, controlling and coordinating the activities.
Costing:
The institute of Cost & Management Accountants (ICMA) London has defined costing as the ascertainment of costs, costing includes techniques and processes of ascertaining costs.
Cost Accountancy:
The Institute of Cost and Management Accountants (ICMA) London has defined Cost Accountancy as the “application of costing and cost accounting principles, methods and techniques to the science, art and practice of cost control and ascertainment of profitability as well as presentation of information for the purpose of management decision making”. Accordingly, Cost Accountancy includes costing, cost accounting, budgetary control, cost control and cost audit. Cost accounting refers to the process of determining and accounting the cost of some particular product or activity. It also includes classification, analysis and infers production of costs.
Cost Accounting:
The I.C.M.A. London defines Cost Accounting as “the process of accounting for cost from the point at which expenditure is incurred or committed to the establishment of its ultimate relationship with cost centers and cost units”.
In practice, costing, cost accounting and cost accountancy are often used interchangeably. Costing refers to ascertainment of costs, accumulation and measurement of cost of activities, processes, products or services. Cost data are used to prepare the statement of cost or cost sheet. Cost Accounting is a specialized branch of accounting which assists management to control costs and to create an awareness of the importance of cost to wells- being of the business organization. Systematic and useful cost data and reports are required to manage the business to achieve its objectives.
Cost Centre:
Cost Centre is a location, person or an asset for which costs can be ascertained and used for the purpose of cost control. It is an organizational segment or area of activity used to accumulate costs. Different types of cost centers used in a manufacturing organization are personal cost canters, impersonal cost centers, operation cost centers and process centers.
Cost Units:
A cost unit is a unit of quantity of product or service in relation to which cost may be as certained. There should be a unit of activity for proper ascertainment of cost. Every organization has a unit of its own for measurement of raw materials, and finished products. Once the unit of activity is decided, it becomes a cost unit for the cost accountant. The cost units should be suitable to the organization. The following are the examples of cost units in different industries are: -
Nature of Industry Cost Unit
Cement Tonne
Cable Metre
Power Kilowatt/ hour
Hospital Per bed
The cost accounting objectives are normally used to denote activities for which costs are required to be determined separately. The activities may be function, organizational sub-division, contract or other work unit for which data are required. There is direct relationship among information needs of management, cost accounting objectives and techniques and tools used for analysis in cost accounting. Thus, cost accounting has the following objectives-
- To determine product costs.
- To facilitate planning and controlling of regular business activities.
- To supply information for short and long run decisions.
Cost Accounting is very important for a commercial organization. It is also useful for any other organization. It helps management in different fields one of such fields is presentation of information in the most useful manner. Cost Accounting is used to measure, analyze or estimate the costs. Profitability and Performance of individual products, departments and other segments of an organization, for either internal or external or both and to report to the interested parties. Cost Accounting concerns itself with the synthesis and analysis of costs. Its purpose in the modern days is to help management in the twin functions of decision- making and control. Thus, Cost Accounting is not simply cost finding but it is advising management, planning and control of organization and business operations. The Companies Act also provides that certain companies have to maintain cost accounting records and accounts and conduct the audit of cost accounts.
A cost accounting system when installed will result in the following: -
- Cost Accounting reveals areas where materials were used excessively, labour operated inefficiently and expenses incurred exorbitantly.
- It suggests cost reduction programme. A continuous cost jointly with technical personnel seeking areas for effecting cost reduction brings beneficial results.
- Cost account locates the specific causes for the variations in profit. It points out the losing product or operations. It indicates reasons for loss and suggests remedial measures in time.
- It provides suitable data to management to select best alternatives. It may be to decide whether to buy or make a part, to operate Machine X or Y, to accept or reject an order below cost.
- Cost accounts give actual cost for price fixation. True demand and supply play vital role in fixing price. But cost is an essential guide here.
- It provides vital data to till in tenders. Tenders filled in with the help of marginal costing technique are successful.
- Standard costing and budgetary control aid maximum efficiency.
- Cost comparison helps cost control. Such comparison may be between different periods of the same department or comparable operations of different units.
- Cost data are useful to outside agencies like Government, Tribunals, etc., for taking decisions on tariff regulations, settlement of disputes, variations in wage levels etc.
- It provides idle capacity cost to assist overcoming capacity utilization crises.
- Marginal costing technique helps to take suitable short-term decisions in times of trade depression.
- Cost Accounting lays down cost centres and responsibility centres which ensure proper organizational structure.
- Cost accounting provides for perpetual inventory system. This enables inventory control and preparation of short-term profit and loss accounts.
- Cost of closing stock of raw materials, work in progress and finished products are readily available in cost records.
All organizations will not get all the advantages listed above. However, an efficiently operated costing system with full support from management can reap most of them.
Financial Accounting is concerned with providing information to external users such as shareholders, creditors, labour unions, government authorities etc., It is oriented towards the preparation of financial statements i.e. Profit and Loss account and Balance Sheet which summarises the results of operations for selected periods of time and show the financial position at particular dates. It follows Generally Accepted Accounting Principle. Financial accounting accounts for money. Since, financial statements are general purpose in nature and only one set of accounts are prepared and sent to all, financial accounting suffers from the following limitations.
Limitations of Financial Accounting -
- Financial accounting is mostly historical in nature.
- It does not provide detailed cost information for different jobs. Processes or departments.
- It is difficult to know the behaviour of cost as expenses are not classified into fixed and variable.
- It does not possess an adequate system of standards to evaluate the performance of departments and employees.
- It does not provide necessary information to management in taking important decisions like pricing, special orders, alternative etc.
- Annual reporting is a rule in financial accounting.
Several methods or types of costing have been designed to suit the needs of individual business conditions.
There are two main methods of costing;
These are Job Costing and Process Costing.
All other costing methods are either variants of these two methods or techniques designed for particular purposes, for specific occasions and for specific conditions.
Job Costing: This method is suitable for ascertaining cost of a job, a specific order or a batch of finished products.
Here the cost unit is a job comprising a specific quantity manufactured as per an order. A job may be small or big. It may be as per a customer’s order of for stock for eventual sale. Other variations of job costing are given below: -
- Contract Costing: This method is used by contractors for construction of building bridges etc. Here the unit of cost is a contract. The period of this contract normally extends beyond the current financial years.
- Batch Costing: This method is applicable to manufacturers producing economic batches of components for subsequent assembling. Large engineering firms use this method. Here the costing is done for a batch of the components instead of a single component.
- Multiple Costing: This is used in large industries such as automobile, aeroplane industries etc., Here the cost of components is calculated separately. Each component has a job sheet. Later, these are assembled to complete the cost of airplane or other finished product.
Process Costing: This method is used by industries manufacturing products by continuous processes. Cost is ascertained for a period by process or department. As distinct from job costing, time is given more importance here. Hence, this is also called period costing. Examples of the industries using process costing are chemical industries, papermaking and refineries. Other variants of process costing are:
- Operation Costing: Operation Costing is applied where the production passes through several operations successively before the final product is made. Wastages may occur in each operation. Operation costing is used in industries such as box making, shoe making, toy making industries. Here cost unit is an operation around which costs are accumulated.
- Single or Output or Unit Costing: This method is applied where the production is of continuous nature and the final product is only one or the different grades of same product. Examples of the industries applying this method are mining industry, quarries and steel production.
- Operation Costing: This method is applied for ascertaining cost of service rendered. Examples of industries using this method are transport services, electricity and boiler house. In transport services, the unit of cost is a passenger Kilometer, or a Kilogram kilometer.
- The costing system should fit in the general organisation of the business. Normally no alternations in the organisation should be made to facilitate costing system. However, unavoidable changes could be made in the set up to ensure effective costing system.
- All relevant technical aspects (such as nature and method of production, varieties of product) should be adequately studied for employing suitable cost control devises.
- The size lay out and organisation of the factory should be adequately described for the benefit of those operating costing system.
- The procedure required to be followed for purchase; receipt, storage and issue of materials should be clearly laid down.
- The methods of wage payment and system of labour control should be specified.
- The norms for appointment and allocation of overhead should be specified.
- Forms and records of original entry should be suitably designed to ensure economy.
- The forms should be got printed. It should contain full instructions. Persons who use them should be adequately trained to ensure accuracy and relevance of the data written on the forms.
- An examiner should check and sign every entry in the forms.
- Responsibility for preparing and sending the cost reports to various levels of management at periodical intervals should be fixed and necessary instructions in this regard issued.
- Full co-operation from all concerned in the management should be enlisted. The resistance from the employees should be minimum.
- Cost of administering the costing system should be commensurate with the benefit available there from.
- Design the system suitably to enable exercising cost control effectively.
- The cost accounts and the financial accounts should be interlocked. Alternatively, result of the two sets of accounts should be reconciled.
- Frequency, regularity and promptness in the presentation of cost reports should be ensured.
Cost Accounting is a close follower of financial accounting. It is not independent of financial accounting. Though there are common grounds between the two, the important differences are given below:-
- Reporting: The major objective of financial accounting is external reporting whereas the focus of cost accounting has been essentially internal i.e. management.
- Flexibility: Financial accounting is mostly historical or after the event while cost accounting is much more flexible and open minded and includes in both retrospective and anticipatory calculations.
- Nature: Financial accounting classifies records, presents and interprets in terms of money transactions whereas cost accounting classifies, records, presents and interprets in a significant manner the material, labour and overhead costs involved in manufacturing and selling each product.
- Financial accounting uses Generally Accepted Accounting Principles while recording, classifying summarizing and reputing business transactions whereas cost accounting is not bound to use GAAP and it can use any technique or practice which generates useful information.
- Time Span: Financial accounting data are developed for a definite period, usually a year, half year or a quarter, but cost accounting reports and statements can be prepared whenever needed.
- Accounting Method: Financial Accounting follows the double – entry system for recording, classifying and summarizing business transactions. The data under Cost Accounting can be gathered for small or large segments or activities of an organisation and monetary as well as other measures can be used for different activities in the organisation.
Composition of Elements of Costs:
A manufacturing organisation converts raw materials into finished products. For that it employs labour and provides other facilities. While compiling production cost, amount spent on all these are to be ascertained. For this purpose, costs are primarily classified into various elements. This classification is required for accounting and control.
The elements of cost are
(i) Direct material
(ii) Direct labour
(iii) Direct expenses and
(iv) Overhead expenses.
The following chart depicts the broad headings of costs and this acts as the basis for preparing a Cost sheet.
Elements of cost
Materials Labour Other Expenses
Direct Indirect Direct Indirect Direct Indirect
Overheads

Factory Administrative Selling & Distribution
Break up of cost sheet
Classification of Cost
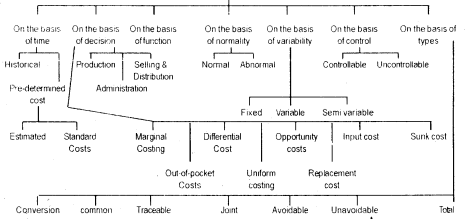
Prime Cost:
The aggregate of Direct material cost, Direct labour and Direct expenses is termed as Prime Cost. Direct costs are traceable to products or jobs.
Direct materials:
It includes cost of materials consumed in the production process which can be directly allocated to the cost center. Direct material can be identified and charged to the finished product.
Examples:
- Material specially purchased for a specific job or process.
- Materials passing from one process to another.
- Consumption of materials or components manufactured in the same factory.
- Primary packing materials.
- Freight, insurance and other transport costs, import duty, octroi duty, carriage inward, cost of storage and handling are treated as direct costs of the materials consumed.
In certain cases, direct materials are used in small quantities and it will not be feasible to ascertain their costs and allocate them directly. For instance, nails used in the manufacture of chairs and tables, glue used in the manufacture of toys. In such cases cost of the total quantity consumed for the period will be treated as Indirect costs.
Direct Labour:
This includes the amount of wages which can be easily identified and directly charged to the product. These are the costs for converting raw material into finished products. Wages paid to workers for operating lathe machines, drilling machines etc. in a tool room are direct wages.
Direct Expenses:
This includes expenses other than materials and labour which can be easily identified with a particular product or process. For example: Excise duty expenses. Indirect costs cannot be easily identified with a particular products or process.
Indirect materials:
Materials which cannot be traced as part of the finished products are known as Indirect materials.
Examples:
- Consumable stores such as lubricants, cotton wastes, tools etc.
- Materials of insignificant value not worthwhile to ascertain the cost separately, for charging directly such as nails (for making chair) glues (for making toys). These materials can be apportioned to or absorbed by cost centres or cost units arbitrarily.
Indirect labour:
Indirect labour is the cost which cannot be directly charged or identified to the finished product. Indirect labour is apportioned to or absorbed by cost centres or cost units suitably.
Examples:
- Salary to Store- keeper
- Wages to Time – keeper
Indirect Expenses:
These are general expenses not incurred for any particular product or service and not chargeable to the products directly.
Examples:
- Rent, Rates and Insurance of Factory
- Power, lighting, heating, repairs, telephone expense, printing and
Stationery.
Overheads can be sub-divided into following main groups.
1.Factory or Works Overheads: Also known as manufacturing or production overheads it consists of all costs of indirect materials, indirect labour and other indirect expenses which are incurred in the factory.
Examples: Factory rent and insurance. Depreciation of Factory building and machinery.
2. Office or Administration overheads: All indirect costs incurred by the office for administration and management of an enterprise.
Examples: Rent, rates, taxes and insurance of office buildings, audit fees, director’s fees.
3. Selling and Distribution overheads: These are indirect costs in relation to marketing and sale.
Examples: Advertising, salary and commission of sales agents, travelling expenses of salesmen.
A manufacturing organisation converts raw materials into finished products. For the purpose, it employs labour and provides other facilities. While compiling production cost, amounts spent on all these facilities are required to be ascertained. Thus, cost ascertainment involves:
(a) Collection and classification of costs according to cost elements
(b) Its allocation or apportionment to cost centers or units
(c) Choice of an appropriate method of costing and
(d) Selection of an appropriate costing technique.
Costs are primarily classified into various elements for accounting and control.
Cost represents a sacrifice, a foregoing or a release of something of value. It is reckoned in money and usually appears as payment of money. It is money outlay for productive factors.
Costs are expenditure incurred in doing something. Costing is the process of determining the cost of doing something i.e. cost of manufacturing an article, rendering service or performing a function.
Cost is composed of three elements- material, labour and expenses or overheads. Each of these costs can be further classified as (a) Direct and (b) Indirect.
Direct costs are costs which can be easily identified with a particular Product, Process or Department. Indirect costs refer to costs which cannot be conveniently identified with a particular product. Process or Department. Indirect costs are common costs like rent, repairs salaries, which are incurred for the benefit of a number of cost units or cost centres
Cost items are analysed or grouped according to their common characteristics which is some independent factor. There are many objectives of cost classifications depending on the requirements of management. The different cost classifications are as follows: -
Cost Classification by Elements:
The constituent elements of costs are broadly classified into three distinct elements i.e. materials, labour and expenses. These three elements of cost can be further grouped into direct and indirect categories. Direct materials refer to the cost of materials which are conveniently and economically traceable to specific units of output. For example: Raw cotton in textiles, crude oil in making diesel. The indirect materials refer to materials that are needed for the completion of the product but whose consumption with regard to the product is either so small or so complex that it would not be appropriate to treat it as a direct material. For example: stationery lubricants, cotton waste etc.
Cost Classification by Function:
A business organisation has to perform several functions such as Manufacturing, Administration, Selling and Distributing and Research and Development. Functional classification of cost implies that the business performs many functions for which costs are incurred. Expenses or Costs are usually classified by function and grouped under the headings of Manufacturing, Selling and Administrative costs in measuring net income.
Manufacturing costs are all check costs incurred to manufacture the products and to bring them to a saleable condition. This includes direct material, direct labour and indirect manufacturing costs or overheads. Administration costs are incurred for formulation of policy, directing the organisation and controlling the activities excluding the cost of research, development, production, selling and distribution. These costs include salary of executives, office, staff, office rent, stationery, postage etc. Selling costs include the cost of creating and stimulating demand and getting customers. For example: advertisement, salary and commission to salesmen, packing. Distribution costs include the cost of warehouse, freight, cartage etc.
Research and Development costs are incurred in the process of finding out new ideas, new processes by experiments or other means of putting the results of such experiments on a commercial basis. Functional classification of cost is important because it provides an opportunity to the management to evaluate the efficiency of departments performing different functions in an organisation.
Cost Classification by variability:
Cost can be classified as (i) fixed (ii) variable and (iii) semi - fixed or semi variable in terms of their variability or changes in cost behaviour in relation to changes in output or activity or volume of production. Activity may be indicated in any form such as units of output, hours worked, sales, etc. The separation of costs into variable and fixed categories is the most difficult part of the costing operation. Certain costs are easily identifiable as variable or fixed while other costs can be segregated only after careful consideration of their nature and an examination of their behaviour.
Fixed costs:
Fixed cost is a cost which does not change in total for a given time period despite wide fluctuations in output or volume of activity. These costs must be met by the organisation irrespective of the volume level. These costs are also known as capacity costs, period costs or stand - by costs; for example, rent, property taxes, supervisor’s salary, advertising, insurance etc.
Variable costs:
Variable costs are those costs which vary directly and proportionately with the output. There is a constant ratio between the change in the cost and the change in the level of output. Direct materials and labour are the examples of variable costs. Thus, all these costs which tend to vary directly with variations in volume of output are variable costs. However, it must be remembered that variable costs remain the same or approximately the same in amount per unit of production regardless of increase or decrease in volume.
Semi variable or semi fixed costs:
There is another group of costs in between the fixed and variable costs. It is semi variable or semi fixed costs. These costs vary in some degree with volume but not in direct proportion. Such costs are fixed only in relation to specified constant conditions. Semi fixed costs are those costs which remain constant upto a certain level of output after which they become variable. For example: maintenance of building, depreciation of plant, supervisor’s salary, telephone expenses etc.
CIMA defines a coding “a system of symbols designed to be applied to a classified set of items, to give a brief accurate reference facilitating entry, collation and analysis”.
Codification of costs is a system of assigning code numbers to each head, subhead and category of expense to facilitate the systematic and easy recording, accounting, summarization of cost data for ascertainment of cost, profitability and managerial decision-making.
The importance of coding is vital with the mechanized and computerised systems of costing. A good coding system should consist of clear, unambiguous and distinctive codes in order to systematize the analysis of costs for accurate cost ascertainment expeditiously and with least cost.
Objectives of Cost Codification:
The important objectives of codification are given below:
- For apportionment of similar items of expenses on one suitable basis of apportionment.
- It systematizes the recording and accounting of cost data and control of expenses.
- The computerised Cost Accounting is made easier with codification of accounts.
- It will reduce the clerical work in the organization with huge number of accounts.
- It facilitates automatic allocation, apportionment and absorption of costs to different cost units or cost centres.
Requirements of Efficient Coding System:
The requirements for an efficient coding system are as follows:
- The codes should be as brief as possible, taking into account the necessity of details of item.
- As far as possible, all codes should be of same length. This helps in computerization of costs and location of errors.
- The code should comprehensive and elastic and should be capable of accommodating new items.
- To minimize errors, the code should incorporate check digits so that computerised system can detect coding errors.
- There is centralized authority in maintenance of coding system. Every individual should not be allowed to allocate code numbers.
- The code should be unique and certain. Each item should have only one possible code number and should be able to be identified from the structure of code.
Methods of Codification of Costs:
The following methods are used for codification of costs:
1. Straight Numbering Method:
Under this system, each item of expenditure is allotted a fixed number. This method is also called ‘numerical coding system’.
For example:
Factory rent – 21
Office rent – 22
Sales office rent – 23 etc.
2. Number Blocks:
Under this method, each head of expenditure is given one block of numbers. The block of numbers allotted will depend on the subheads to be accommodated. This method is a slight variation of straight numbering system.
For example:
Depreciation – 1 to 100
Insurance – 101 to 200
Repairs and maintenance – 201 to 300
3. Memoric Method:
Under this method, alphabets are used as codes to help the memory.
For example:
Depreciation – Office Buildings – DOB
Depreciation – Factory Buildings – DFB
Depreciation – Godown – DGD
4. Decimal Method:
Under this method, numerical codes are allotted to various expenses and cost centres classifying into major, minor and detail account heads:
A. Production Overhead
a. Indirect Materials:
i. Consumable store
Ii. Cotton waste
Iii. Lubricants
Iv. Loose tools
b. Indirect Labour:
i. Time office
Ii. Security
Iii. Clerical staff
c. Indirect Expenses:
i. Factory rent
Ii. Depreciation of Plant and machinery
Iii. Insurance of Factory building
B. Administration Overhead:
a. Indirect materials
2.1.1 ………………….
b. Indirect labour
1.13.1 ………………….
c. Indirect expenses
2.3.1 …………………. Etc.
5. Field Method with Numerical Codes:
Under this system, each code number consists of nine digits. The first two digits represent the variable or fixed nature of expense; the next three digits indicate head of expense, the next two digits stand for the analysis of expense and the last two digits indicate the cost centre, where expenses have been incurred.
For example Code 10/100/03/05/ represents for:
Fixed/Production Labour/Monthly Salary/Machine Shop
6. Combination of Symbol and Numbers:
Under this method, a combination of symbol, alphabet and a number is used to represent a code.
For example:
D1 – Depreciation Factory Building
D2 – Depreciation Administrative Building
D3 – Depreciation Plant and Machinery
D4 – Depreciation Vehicles, etc.
Here alphabet represents the main head of the expense and number represents the analysis of expense.
Cost sheet is a statement prepared to present the detailed costs of total output during a period. It provides information relating to cost per unit at different stages of total cost of production. The preparation of cost sheet is one of the important and primary function of cost accounting. Cost sheet is not an account. There is a prescribed form for preparation of cost sheet. A cost sheet is a statement of cost prepared for a given period of time in such a manner that it indicates various elements of cost as clearly as possible. A cost sheet is useful in ascertaining the total cost of production per unit, formulation of production plan, fixing up the selling price and minimizes the production cost. Sometimes standard cost data are provided to facilitate comparison with the actual cost increased. The preparation of the cost sheet requires understanding of the treatment of the following items: -
Stock of raw materials: The opening and closing stock of raw materials are to be adjusted with purchase of Raw materials in order to determine the value of raw materials consumed for the output produced. Carriage/Freight inward and Octroi on purchase etc. also to be added to purchases. This is a part of Prime Cost.
Stock of Work in Process: The value of stock of work in process is a part of Factory cost and therefore, it should be adjusted with factory overheads. Sale of scrap should be deducted from the factory overheads in order to determine the total factory cost.
Stock of Finished goods: Finished goods cover the products on which factory work has been completed. It is the cost of completed production. The opening and closing values of finished goods are to be adjusted with the total cost of production in order to arrive at cost of sales.
Expenses excluded from cost sheet:
There are certain expenses /costs which do not form a part of cost sheet. Some of these expenses are an apportionment of profit. Examples of these expenses are -
- Dividend to shareholders
- Income Tax
- Interest on loan
- Donations paid
- Capital expenditure
- Capital loss on sale of assets.
- Commission to Partners / Managing Director
- Discount on issue of shares/ debentures
- Underwriting commission.
- Writing of goodwill/ bad debts
- Provision for Taxation, Bad Debts or any kind of Fund or reserves.
Specimen of Cost Sheet
Cost Sheet for the period
(Production ------ Units)
Particulars | Total Cost Rs. | Cost Per Unit Rs. |
Direct Materials Raw Materials Opening stock Materials: Add: Purchases Add: Carriage / Freight Inwards Less: Closing stock Cost of materials consumed Direct Labour Direct Expenses
Prime cost Factory overheads Add: Work in Progress (Opening) Less: Work in Progress (Closing)
Works /Factory cost Add: Office and administrative expenses
Cost of Production (of goods produced)
Add: Op. Stock of finished goods Less closing of finished goods
Cost of production (of goods sold) Add: Selling & Distribution expenses
Cost of Sales Add: Profit (Loss) Sales |
|
|
Elements of Total Cost:
Costs are classified under different heads, which represent the successive stages through which the cost flow.
Prime Cost:
Prime cost is the basic cost of any product. It comprises of those expenses which could be traced directly to it. The prime cost consists of cost of direct materials, direct labour and direct expenses. Direct expenses include special expenses which can be identified with product or job and are charged directly to the product as part of the prime cost. For example: cost of hiring special plant or machinery, cost of special moulds, design or patterns, Architect’s fees, Royalties, License fees etc.
Works cost:
Works cost of a Product consists of prime cost plus the portion of works or factory expenses chargeable against the Production. Works or factory expenses include indirect materials indirect labour and indirect expenses. Indirect materials refer to those materials that are needed for the completion of the product but the consumption of these materials is either so small or complex that it would not be appropriate to treat it as direct materials. These are supplies that cannot be conveniently and economically charged to a specific unit of output. For example, lubricants, cotton waste, works stationery etc.
Indirect labour is that labour which does not affect the construction or the composition of the finished product. This is the labour cost of production related activities that cannot be associated with or conveniently traced to specific product through physical observation. For example, Foremen’s salary and salary of employees engaged in maintenance or service work. Indirect expenses cover all expenditure incurred by the manufacturer from the time of production to its completion as delivery to customer by way of rate of product. Any expense that cannot be allocated but which can be apportioned to or absorbed by the cost centres/ cost units are known as indirect expenses. These expenses are incurred for the benefit of more than one product, job or activity and therefore, must be apportioned by appropriate bases to the various functions or products. For example, lighting and heating, maintenance factory manager’s salary, watch and ward department’s salary etc.
Cost of Production:
Cost of Production consists of works cost plus an additional amount of office and administrative expenses. It includes all expenses connected with the managerial functions such as planning, organizing, directing, coordinating and controlling the operations of the manufacturing business. For example, office rent, salary, lighting, stationery, repairs and maintenance and depreciation of office building, audit fees, legal expenses.
Cost of Sales:
Cost of sales consists of cost of production plus proportionate selling and distribution expenses of the product. Selling expenses include the expenses incurred for creating demand for the product such as advertisement, salaries of salesmen, selling expenses and show room expenses. Distribution expenses are those expenses incurred in connection with the delivery of goods to the customers such as packing, carriage outwards, warehouse expenses.