Unit 2
Production Management
According to Bates and Parkinson:
“Production is the organised activity of remoulding resources into finished products in the form of goods and services; the aim of production is to satisfy the demand for such transformed resources”.
According to J. R. Hicks:
“Production is any activity directed to the satisfaction of other peoples’ wants through exchange”. This definition makes it clear that, in economics, we don't treat the mere making of things as production. What’s made must be designed to satisfy wants.
Meaning of Production Management:
Production Management refers to the appliance of management principles to the production function in a factory. In other words, production management involves application of planning, organizing, directing and controlling the assembly process.
The application of management to the sector of production has been the results of at least three developments:
(i) First is the development of factory system of production. Until the emergence of the concept of producing, there was no such thing as management as we all know it. It's true that people operated business of 1 type or another, but for the most part, these people were owners of business and didn't regard themselves as managers as well,
(ii) Essentially stems from the first, namely, the development of the large corporation with many owners and therefore the necessity to hire people to operate the business,
(iii) Stems from the work of the many of the pioneers of scientific management who were able to demonstrate the worth, from a performance and profit point of view, of a number of the techniques they were developing.
It is observed that one cannot demarcate the start and end points of Production Management in an establishment. The reason is that it's interrelated with many other functional areas of business, viz., marketing, finance, industrial relation policies etc.
Alternately, Production Management isn't independent of marketing, financial and personnel management because of which it's very difficult to formulate some single appropriate definition of Production Management.
Scope of Production Management:
The objectives of production management are aimed toward satisfying the needs of the customers through offering organisations products/services. The scopes of production management are often considered from the point of view of both strategic decisions influencing the production system and at the operation level. The strategic level decisions are mainly concerned with the planning of product and production system. These decisions involve decisions, which have long terms implications.
The strategic level decisions are:
1. New Product Identification and Design:
The success of an organisation depends upon the product mix that it offers to the customer. There exist demands for the products if the product has good market acceptability. The products should be designed in such way on meet the expectations of consumers. The tools like value analysis should be applied at the design stage to avoid unnecessary cost build up in to the product.
2. Process Design and Planning:
This involves the appropriate technology for conversion of materials in to products. The selection of technology depends upon several factors like demand, investment capability, labour availably and degree of automation required. This is often followed by selection of the process of conversion and determining the workstations and therefore the flow of work. At this stage, macro level process planning is completed.
3. Facilities Location and Layout Planning:
The facilities location is a strategic decision and facilities once located won't be altered in near feature. So due considerations should be implied to all the factors that affect the location
4. Design of material Handling System:
As per the principle of material handling, the handling should be kept at minimum though it's impractical to avoid handling. The selection of particular flow patterns and material handling equipment depends on the distance between the workstations, intensity of flow or traffic and size, shape and nature of materials to be handled.
5. Capacity Planning:
This decision is concerned with the procurement of fixed assets like plants and machineries. The choice regarding the scale of the plant, output etc. are decided at this stage. The capacity planning activity is again a function of volume of demand. The operational level decisions are short-term decisions. These are mainly concerned with planning and control of production activities.
The operational level decisions are:
1. Production planning:
It is concerned with determining the future course of action regarding production to realize the organisation objectives.
2. Production control:
It is a management technique, which aims to see that the activities are administered as per the plan. Production control activity cares about comparing actual output with standard output and to require corrective action if there exists a deviation between actual and standard.
3. The other activities include:
Inventory control, maintenance and replacement, cost reduction and cost control and work system design
Production planning and control is a predetermined process that plans, manages and controls the allocation of human resource, raw material, and machinery to attain maximum efficiency.
Production planning is a sequence of steps that empower manufacturers to figure smarter and optimize their production process within the absolute best manner. This helps manufacturer’s work smarter by efficiently managing internal resources to satisfy customer demand.
Objectives of Production Planning and Control (PPC)
Having a reliable Production Planning and Control software in your company makes it easy to:
• Ensure cost-efficient production process
• Promote timely delivery of products
• Minimize production time
• Improve customer satisfaction
• Coordinate with departments about production, to make sure things are on the same page
• Ensure the proper man is assigned the proper work
Production planning is the core of any manufacturing unit. It includes material forecasting, master production scheduling, future planning, demand management and more. The PPC process kicks off with demand forecasting of a product, and thereafter designing the production plan according to the demand to move it forward.
Production planning is a strategy to plan a chain of operations that supports manufacturers to be at the proper place, at the proper time so that they can achieve the maximum efficiency from their resources.
Now, let’s straightway discuss the steps involved in Production Planning and Control. As per British Standards Institute, there are four stages or essential elements within the process of production planning and control. These are as follows:
1. Routing
Routing determines the trail / path from which the raw materials flow within the factory. Once, the sequence is followed, raw materials are transformed into finished goods.
Setting up time for every step is vital to measure the overall duration of the production process. Simply saying, routing in manufacturing states the sequence of work and operations. Routing throws light on the quantity and quality of materials to be used, resources involved (men, machine, and material), the series of operations and place of production.
Routing manages “How”, “What”, “How much”, & “Where” to produce in a very manufacturing company. It systematizes the process and nurtures optimum utilization of resources to urge the best results.
2. Scheduling
Scheduling is the second step that emphasizes on “When” the operations are going to be completed. It aims to make the most of the time given for completion of the operation.
As per Kimball and Kimball, scheduling is defined as –
“The determination of the time that ought to be required to perform the whole series as routed, making allowance for all factors concerned.”
Organizations use different kinds of schedules to manage the time element. These include Master Schedule, Operation Schedule, Daily Schedule and more.
3. Dispatching
The third step ensures that operations are done successfully and everything is loaded on the software. Dispatching includes the discharge of orders, in accordance with the scheduled charts.
Here are the points that encapsulate “Dispatching”
• Issue of materials or fixtures that are important for the production
• Issue of orders or drawings for initiating the work
• Maintain the records from start to finish
• Initiate the control procedure
• Cascade the work from one process to another
4. Follow-up
Also referred to as expediting, follow-up is the final step that finds faults or defects, bottlenecks and loopholes within the entire production process. In this step, the team measures the real performance from start till the end then compares it with the expected one.
Expediters or stock chasers are accountable for performing follow-up processes. It’s quite obvious that any of the processes may undergo break-downs or machine failure. Follow-up promotes smooth production by eliminating these defects.
Productivity refers to the physical relationship between the quantity produced (output) and therefore the quantity of resources utilized in the course of production (input).
“It is the ratio between the output of products and services and the input of resources consumed within the process of production.”
Productivity is the ratio between output of wealth and input of resources utilized in production processes.
Output means the quantity of products produced and therefore the inputs are the varied resources utilized in the production. The resources used could also be land, building, equipment, machinery, materials, labour etc.
Productivity means an economic measure of output per unit of input. Output refers to the entire production in terms of units or in terms of revenues while input refers to all the factors of production used like capital, labour, equipment, etc.
Productivity: Meaning, Concept, Factors, Importance, Formulas, Techniques, Measurement and Other Details
Productivity – Meaning
Productivity refers to the physical relationship between the quantity produced (output) and the quantity of resources utilized in the course of production (input). “It is that the ratio between the output of products and services and the input of resources consumed in the process of production.”
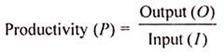
Output implies total production while input means land, labour, capital, management, etc. Productivity measures the efficiency of the production system. The efficiency with which resources are utilized is termed productive efficiency. Higher productivity means producing more from a given amount of inputs or producing a given amount with lesser inputs.
At the level of a plant or an industry productivity is an output-input ratio. But at the macro level, productivity may be a measure of performance of an economy or country. From a nation’s viewpoint productivity is the ratio of available goods and services to the potential resources of the country.
Productivity means an economic measure of output per unit of input. Output refers to the entire production in terms of units or in terms of revenues while input refers to all or any the factors of production used like capital, labour, equipment, etc. Productivity could be a good indicator of the efficiency with which a factory is working . If a firm has higher productivity, i.e. it produces more with a given amount of inputs, it means it's utilising the resources properly.
Similarly, a lower productivity indicates wastage of resources and time. It's vital to possess a high productivity rate because resources like capital and time are scarce and will be exploited within the absolute best way. Productivity is often calculated because the ratio of the quantity of output to the quantity of inputs.
Productivity = Output/Input
Productivity can thus be measured as:

“Productivity is the relation between; what a firm produces and what a firm uses as a resource to produce output, i.e. arithmetic ratio of amount produced (output) to the amount of resources (input)”.
“Productivity is an aggregate measure of the efficiency of production; it's the ratio of output to inputs i.e. capital, labor, land, energy and materials”.
“Productivity refers to the efficiency of the assembly system and an indicator to; how well the factors of production (land, capital, labor and energy) are utilized”.
Productivity is the ratio between output of wealth and input of resources utilized in production processes. Output means the quantity of products produced and therefore the inputs are the varied resources utilized in the production. The resources used is also land, building, equipment, machinery, materials, labour etc.
Productivity is increased by the subsequent ways:
1. Increasing the output using a similar input.
2. Reducing the input by maintaining the output as constant.
3. Increasing the output to a maximum extent with a smaller increase in input.
Labour productivity measures the efficiency of workers in an organisation.
It refers to the quantity of output obtained for a given quantity of input. The output is measured in units like kgs., tonnes, gallons, litres, etc. While input is expressed in terms of time, wages paid or number of workers.
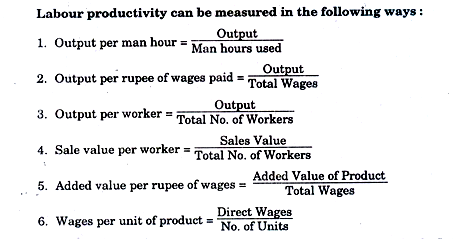
Labour productivity so calculated has to be compared with standards. It's also compared with previous period’s figures and with the productivity of similar units in the industry.
Material Productivity:
Some of the ways of measuring material productivity are given as follows:
Material Productivity

Machine Productivity:
Where most of the work is done by machinery, measure of machine productivity is important to understand the capacity utilisation and efficiency of machinery.
Machine productivity is measured by the subsequent ways:
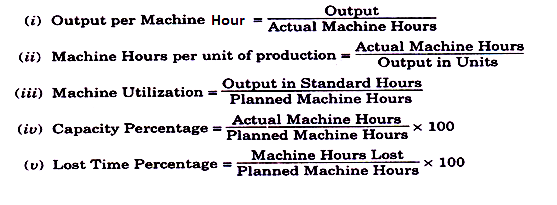
In appraising an organization’s potential for improving productivity, its current operations and management practices should be examined to decide how they ought to function in the future. a large number of techniques are developed for improving productivity.
Some of these techniques are described below:
1. Work Study:
Scientific analysis and improvement of work altogether its aspects is a very useful technique of increasing productivity. Work study leads to improvements in plant layout, material handling system, process design and standardization, working conditions, etc. These in turn help to reduce defective works and waste.
2. Research and Development:
Continuing research and development (R & D) results in the discovery of better techniques of production and enhancements in existing machinery, equipment, etc. the rate of technological progress is a direct determinant of productivity. That's why companies and countries spend huge sums of cash on research and development activities.
3. Incentive Schemes:
Wage incentive schemes seek to motivate employees by paying extra remuneration. Profit sharing or bonus, labour welfare measures and good working conditions also help in this objective. These schemes foster a sense of belonging and closer human relationships. As a result, there's reduction in idle time caused by absenteeism, labour turnover, accidents and disputes.
4. Production Planning and Control:
Scientific task planning ensures timely supply of inputs, proper maintenance of plants, efficient work scheduling and regulation of day-to-day ‘ activities within the plant. It facilitates full utilization of plant capacity and achievement of production targets.
5. Workers’ Participation in Management:
Labour participation in management is considered an efficient tool for improving productivity. It helps in developing mutual understanding and cooperation between management and labour. Joint consultation, suggestion schemes, two-way communication, grievance procedure are the main sorts of workers’ participation in management.
6. Automation:
Mechanization, automation and rationalization are major breakthroughs for increasing productivity. These schemes are effective provided the productivity gains are equitably shared with workers. Such measures increase the speed and accuracy of labor .
7. Management by Objectives (MBO):
MBO is a process whereby the superior and subordinates jointly identify the precise measurable goals, define results expected of each individual and jointly assess the contribution of every individual. It's an approach for integrating the individuals with the organization. The main target of MBO is on participative goal setting, joint evaluation of performance and results to be achieved.
It is also referred to as Management by Results. A link is formed between the organizational goals and individual’s targets so that an employee can see how his work contributes to the goals of the organization. Subordinate’s participation in setting goals and action plans and in reviewing performance provides a decent measure of self-control. As a result there's improvement within the understanding, motivation and morale of the individual. However, MBO requires education and training of subordinates and a democratic leadership style on the part of managers.
8. Job Enrichment:
Job enrichment is the process of redesigning a job in order to enlarge its scope and to offer the worker more to do. Its purpose is to improve job satisfaction, motivation and morale of workers. When the job is engineered to workers the dehumanization element is reduced so as to improve productivity and to reduce cost. It provides a chance for the satisfaction of higher level needs.
9. Flexitime—an Alternative Work Pattern:
Flexitime is a relatively new work pattern which may be a major departure from tradition. It allows the workers to line their own work hours subject to a minimum number of hours per week. During a particular period all workers are required to be present. Such a period is named ‘core hours.’ Subject to those limitations workers are given the liberty to decide when they will work.
Flexitime helps to scale back worker alienation and to boost productivity. It reduces the tyranny of supervisors and provides job opportunities to working mothers, aged persons and students. It's a greater motivational value than five days’ work-week. By permitting workers the right of self-determination, flexitime reduces tardiness, overtime and short-term absenteeism.
10. Quality of work Life (QWL):
QWL may be a new technique for improving productivity and quality of work.
11. Quality Circles (QC):
A quality circle is a small group of workers which regularly meets to discuss problems, investigate causes, recommend solutions and if authorized, to require corrective action. It always consists of 5 to fifteen members who collectively identify, analyze and resolve work-related problems and should even implement solutions.
A leader is appointed to direct and guide the circle. A Facilitator makes integration of programmes easier at all levels. The Coordinator supervises the facilitators and directs administration of the programme. There's a steering committee which oversees and directs the efforts of all quality circles in the organization.
The purpose of a quality circle programme is to enhance motivation, productivity and product quality. It’s designed to optimize the manpower by capturing the creative and innovative power of the workforce. It provides workers an opportunity to participate in decisions about their work. As a result, they take greater interest in their jobs. It develops a sense of participation and contribution among workers.
A quality circle programme relies on the philosophy that quality and output are often improved through the participation of employees in solving work problems.
The Japanese concept of quality circle has taken firm roots in India. Introduced in India by BHEL in 1981, the movement has now spread to about 250 to 350 establishments. Nearly 7,000 quality circles involving 70,000 workers are in operation. Companies like BHEL, HMT, Modi Rubber, J.K. Synthetics, etc., have successfully implemented this idea.
However, a number of top managers treat this idea as bad and in such cases the quality circle programme fails to click. It cannot thrive without positive commitment and support of top management and without grass-root support.
Ways to improve Productivity and Quality of Products
It is vital to develop a high rate of productivity because it's the foundation of the business’s future growth.
There are some ways by which productivity are often increased:
i. Adoption of up so far technology in machines and equipment.
Ii. Implementing a proper system of managerial planning and control.
Iii. Effective time management.
Iv. Maintenance of labor facilities in factories.
v. Standardisation and automation for mass production.
Vi. Empower employees by providing training and an environment conducive for private as well as organisational growth.
Vii. Let workers participate in management.
Viii. Provide a flexible work schedule rather than rigid working hours.
Ix. Clear communication should be there between management and workers.
The following are the ways for improving productivity and quality of products:
1. Combining the Resources for Production:
Managers attempt to utilize the resources just described in a manner that achieves production at a low cost. They combine the varied resources with the use of work stations and assembly lines. a workstation is an area within which one or more employees are assigned a specific task. A workstation may require machinery and equipment also as employees.
An assembly line consists of a sequence of workstations in which each workstation is designed to cover specific phases of the production process. The production of a single product may require several workstations, with each station using employees, machinery, and materials.
Since the cost of all these resources along with the building are often substantial, efficient management of the production process can reduce expenses, which may convert into higher profits.
Employees use buildings, machinery, and equipment to convert materials into a product or service. For example, employees of printing firms use machines for typesetting, printing, and binding to produce books. Employees of General Nutrition Centers (GNC) use its manufacturing plant (which is the size of 4 football fields) to produce quite 150,000 bottles of vitamins per day.
2. Selecting a Site:
A critical decision in production management is the selection of a site (location) for the factory or office. Location can significantly affect the cost of production and thus the firm’s ability to compete against other firms. This is very true for industrial firms like Bethlehem Steel and DaimlerChrysler, which require a large investment in plant and equipment.
3. Selecting the design and Layout:
Once a site for a manufacturing plant or office is chosen, the design and layout must be determined. The design indicates the size and structure of the plant or office. The layout is the arrangement of the machinery and equipment within the factory or office.
The design and layout decisions directly affect operating expenses because they determine the costs of rent, machinery, and equipment. They'll even affect the firm’s interest expenses because they influence the amount of cash that must be borrowed to get property or machinery.
4. Production Control:
Once the plant and design are selected, the firm can engage in production control, which involves the following:
(i) Purchasing materials
(ii) Inventory control
(iii) Routing
(iv) Scheduling
(i) Purchasing Materials:
Managers perform the subsequent tasks when purchasing supplies. First, they must select a supplier. Second, they attempt to obtain volume discounts. Third, they determine whether to delegate some production tasks to suppliers.
(ii) Inventory Control:
Inventory control is the process of managing inventory at A level that minimizes costs. It requires the management of materials inventories, work-in-process inventories, and finished goods inventories.
(iii) Routing:
Routing is that the sequence (or route) of tasks necessary to complete the production of a product. Raw materials are commonly sent to varied work stations in order that they will be used as specified in the production process. A specific part of the production process is completed at each workstation.
For example, the production of a bicycle may require (1) using materials to produce a bike frame at one workstation, (2) assembling wheels at a second workstation, and (3) packaging the frames and wheels that are assembled at a 3rd workstation.
The routing process is periodically evaluated to see whether it can be improved to allow a faster or less costly production process. General Motors, DaimlerChrysler, and United Parcel Service have streamlined their routing process to enhance production efficiency.
(iv) Scheduling
Scheduling is the act of setting time periods for every task in the production process. A production schedule is a plan for the timing and volume of production tasks. For instance , the production schedule for a bicycle may set a time of two hours for one frame to be assembled and one hour for one wheel to be assembled.
Scheduling is helpful because it establishes the expected amount of production that should be achieved at each workstation over a given day or week. Therefore, each employee understands what's expected.
Furthermore, scheduling allows managers to forecast what proportion will be produced by the end of the day, week, or month. If a firm doesn't meet its production schedule, it'll not be able to accommodate customer orders in a timely fashion and can lose few of its customers.
(v) Quality control:
Quality is often defined as the degree to which a product or service satisfies a customer’s requirements or expectations. Quality relates to customer satisfaction, which can have an impact on future sales and thus on the future performance of the firm. Customers are more likely to get additional products from the same firm if they're satisfied with the quality.
Firms now realize that it's easier to retain existing customers than it has to get new customers who are unfamiliar with their products or services. Thus, firms are increasingly recognizing the impact that the quality of their products or services can have on their overall performance.
Quality control is a process of determining whether the quality of a product or a service meets the required quality level and identifying improvements (if any) that require to be made in the production process. Quality is often measured by assessing the varied characteristics (such as how long the product lasts) that enhance customer satisfaction.
Productivity – Advantages of higher Productivity
Higher productivity provides several benefits to management, employees as well as customers and other stakeholders associated with a firm. At the macroeconomic level, productivity improves a country’s living standards because more goods and services are produced at better prices, inflation and interest rates tend to be stable, and gross domestic product (GDP) tends to be high and at the microeconomic level, high productivity can increase people’s real income and improve their ability to get goods and services, enjoy leisure activities, access better housing and education, and contribute to social and environmental programs.
At a firm or industry level, the advantages of productivity growth are distributed in a number of various ways:
i. To the workforce through better wages and conditions.
Ii. To shareholders and superannuation funds through increased profits and dividend distributions.
Iii. To customers through lower prices.
Iv. To the environment through more stringent environmental protection.
v. To governments through increases in tax payments (which are often used to fund social and environmental programs).
Vi. GDP is determined in 3 ways, all of which should, in principle, give the same result. They’re the product (or output) approach, the income approach, and therefore the expenditure approach.
1. Management:
Highly productive companies can better meet their obligations to suppliers, workers, shareholders, and governments (payment of taxes and compliance with regulations), while maintaining competitiveness or improving their competitiveness in the marketplace. When the productivity of a corporation improves, the business will gain many benefits.
These can include:
i. Increase in income/profitability.
Ii. Lowering running costs/operational costs.
Iii. Maximizing the utilization of all of the company’s resources like land, equipment’s/machineries, factory, workers, and etc.
Iv. Gaining a greater share of the market.
v. Additional cash flows mean more opportunity for the corporate to expand and grow.
Vi. To clear the debt or loans acquired from different sources.
Vii. To face better in the market.
Viii. Contributes to the competitive advantages of the firm.
2. Customers:
Most of the highly productive companies all over the world have used it to achieve the loyalty of consumers and meet their needs. Satisfaction of consumers will result in their loyalty towards the company.
Higher productivity provides customers the subsequent benefits:
i. Productivity helpful in reducing the price of the article.
Ii. Higher productivity leads to better customer satisfaction.
Iii. Customers are supplied with good quality products at low prices.
3. Employee/Workers:
When a firm is very productive it becomes successful eventually, and since of this, incentives are bound to be made available to the workers . These include pay raises, bonuses, and medical insurance then on. This can also motivate employees and provide them more job opportunities because the company grows. The worker gets many benefits.
These can include:
i. Companies pay higher salary and wages.
Ii. Better Working Conditions.
Iii. Higher standard of living.
Iv. Job Security and Satisfaction.
So, Productivity in the workplace is a vital aspect of each company and when top Management understands this idea, success is just round the corner.
Some Other Advantages
Advantages of higher Level of Productivity:
i. Belter wages and working conditions for workers.
Ii. Increased profitability as high productivity leads reduces cost of production.
Iii. Reduce wastage of precious resources.
Iv. More retained earnings as results of increase in profits which results in shareholders’ wealth maximisation.
v. Improved quality goods at nominal prices are available to customers.
Vi. Greater chances of growth for the corporate.
Increase in Productivity Movement in India: Reasons and Objectives!
The productivity movement has been on in India for a long time. With a view to increasing productivity of various segments of the economy, the government of India has been making systematic efforts especially since independence. There's no denying the very fact that various developed countries of the globe viz., U.S.A, U.S.S.R. And Japan etc., owe their present status to increased productivity.
Ours is a developing economy. So as to attain the desired targets of production and to ensure proper allocation and utilisation of obtainable resources, productivity plays an important role. There are many other reasons emphasizing the requirement of increased productivity in India.
These reasons are:
(a) To make sure higher living standards for people.
(b) To increase per capita income.
(c) To decrease production costs.
(d) To increase exports.
(e) To ensure overall development and prosperity of the economy.
(f) To assist in increasing labour efficiency.
National Productivity Council (NPC) was established in 1958 with the object of making productivity consciousness in the country providing specialised services to industries to extend their operational and managerial efficiency and to disseminate productivity information.
It is a non-profit autonomous body registered under the Societies Registration Act, 1860. The constitution of the NPC provides that its membership should be limited to 60 and therefore the number of representatives should be 11 each from employers, employees and therefore the Government.
The remaining member needs to be co-opted from amongst other interests like researchers, technicians, consumers and local productivity councils. The NCP was entrusted with the task of facilitating the formation of local productivity councils. There's a nation-wide network of local productivity councils.
The NPC has its Headquarters in New Delhi and it also has nine Regional Directorates at Ahmedabad, Bangalore, Bombay, Calcutta, Chandigarh, Guwahati, Kanpur, Madras and New Delhi.
The objectives of NPC are as follows:
1. To create and develop productivity consciousness in the country.
2. To form arrangements for the training of managers at every level of management.
3. To form arrangements for the services of experts on the requisitions of local productivity councils.
4. To undertake research with reference to various production processes.
5. To send delegations to developed countries to gather and study information with reference to increased productivity.
6. To make arrangements for training of personnel with reference to productivity methods and techniques in other countries.
7. To invite experts on productivity from foreign countries and to make use of their knowledge and services.
8. To import various productivity services with a view to having maximum utilisation of obtainable resources, viz; men, money, materials and machines.
9. To make sure higher and better living standards for the people of the country.
10. To conduct various seminars on different subjects to enhance productivity.
11. To create a positive productivity atmosphere within the country by developing harmonious employer-employee relations.
Quality management is the act of overseeing all activities and tasks that has to be accomplished to keep up a desired level of excellence. This includes the determination of a quality policy, creating and implementing quality planning and assurance, and quality control and quality improvement.
Quality control management ensures that what your company delivers and therefore the delivery processes it uses are cohesive which every business phase of the organization focuses on a similar goal.
When broken down, quality control management is often segmented into four key components to be effective: quality planning, quality control, quality assurance, and quality improvement.
Quality Control Planning
The first step of quality management is planning. You need to require the time to identify your goals and what you want your baseline to be. You should determine what your quality standards are, the requirements necessary to satisfy these standards, and what procedures will be used to make sure these criteria are being met. During this planning stage, you'll want to consider:
• What your stakeholder’s expectations and priorities are, if applicable
• What your company’s definition of success is
• What legal standards or requirements are in place that has to be abided by
• Who will handle each role within the quality management process (supervision, testing, etc.)
• How often processes are evaluated for improvement
Quality Control
Once you have a plan in place, quality control comes into play. This is the method of physically inspecting and testing what you laid out in the planning stage to make sure it's obtainable. You need to confirm that each one the standards you have put into place is met and you need to identify any mishaps or errors that require to be corrected. The sooner you'll catch these errors, the better. As such, you should be paying attention to all aspects of the goods, including both the materials used and therefore the process of putting them together.
Once the inspection data has been collected, it should be displayed in a way that creates it easy to investigate. You'll create histograms, run charts, or cause and effect displays, then easily share them through your document management software to form sure everyone has access to them.
Quality Assurance
While quality control involves inspecting the actual products or services in the field, quality assurance is reviewing the delivery process of services or the quality management manufacturing of products. By inspecting your goods or services at the source, you'll catch mistakes before they reach the customer. You’ll also fine tune your processes to stop errors in the future. When reviewing your product or service during this stage of quality control management, you'll want to follow these steps:
• Confirm that everything is working as it was agreed upon during the quality planning stage
• Measure how effective your pre-determined processes are and ensure that all compliance needs are being met
• Take note of any lessons learned
• Identify areas where there's an opportunity for a smoother process
To be effective, quality assurance must be completed regularly through independent audits. For the simplest results, have the audit completed by a third-party that's not financially or emotionally invested in the outcome.
Quality Improvement
Finally, after completing the quality control process, you need to thoroughly review your findings and come up with a way to enhance your methods going forward. Quality control management is fruitless if you're not willing to form changes once they are necessary. The desire for continual improvement is the goal for every successful company. So, gather all your data, re-evaluate both the processes and therefore the product—always keeping compliance in mind—and then begin the quality control management process again. With each cycle, you'll end up with a better product, happier customers, and more profit in your pocket
Introductory Observations of Total Quality Management (TQM):
A total approach to quality is the current thinking of today; which is popularly called total quality management (TQM).
The idea behind TQM is to create a quality culture throughout the organisation.
The credit for pioneering the concept of TQM should be bestowed upon W.Edward Deming of Japan; who introduced this philosophy in Japan over four decades ago. Gradually, the concept of TQM caught the attention of industrialists, all over the world, including India.
TQM could simply be defined as follows:
TQM is a philosophy that believes during a company-wide responsibility toward quality via fostering a quality culture throughout the organisation; involving continuous improvement in the quality of labor of all employees with a view to best meeting the requirements of consumers.
TQM is an integrated organizational effort designed to improve quality at every level.
OR
TQM is a process and philosophy of achieving best possible outcomes from the inputs, by using them effectively and efficiently so as to deliver best value for the customer, while achieving long term objectives of the organization.
OR
Total Quality Management is a structured system for managing the quality of products, processes, and resources of a corporation in order to satisfy its internal and external customers, also as its suppliers.
OR
TQM is a philosophy that's designed to make an organization faster, flexible, focused and friendly. It leads to a structured system that focuses each employee on the customer. It creates an environment that allows organization-wide participation in planning and implementing a continual improvement process to satisfy customer needs.
In brief, TQM is a comprehensive management system which:
a. Focuses on meeting owners’/customers’ needs, by providing quality services at a reasonable cost.
b. Focuses on continuous improvement.
c. Recognizes the role of everyone in the organization.
d. Views organization as an internal system with a standard aim.
e. Focuses on the way tasks are accomplished.
f. Emphasizes teamwork.
Elements of TQM:
The following are the essential elements of TQM:
(i) Meeting Customers’ Requirements:
Customer satisfaction is the key to the survival and growth of an organisation. TQM aims at the best satisfying the requirements of consumers which never remain constant; but keep changing with changes in environment and wishes , preferences etc. of consumers .
(ii) Continuous Improvement:
TQM is a total concept. It involves the combination of all functions and processes within an organisation, in order to realize continuous improvement in the quality of products/services. Moreover, quality may be a dynamic concept.
With advancement in technology, an organisation must adopt new processes and redesign products to yield continuous improvement in quality to offer the best advantage of technology to customers.
(iii) Involvement of all Employees:
TQM is termed people’s success. According to TQM philosophy, quality isn't the responsibility only of production personnel. Rather it's a company-wide responsibility. TQM is successful only when the entire organisation is quality-conscious.
Hence the nomenclature of this philosophy as TQM i.e. totals quality management. TQM involves improvement in the quality of work of all employees through popularizing the concept of quality culture. In fact, TQM should be the priority of all managers and workers, in the organisation.
Features of TQM
1. Customer Focused
Quality begins and ends with the customer.
The customer dictates what the focus will be as well because the approach to achieving those results.
But most importantly the customer determines if the efforts were successful.
For instance, organizations solicit feedback from customers about products and services. Use what's learned from that feedback to enhance the product or service.
2. Involved Employees
Organizations that manage with TQM understand the importance of employee involvement.
These front-line members of the team often hold the answers to solving problems and improving how work gets done.
For instance, in the service industry, employees are the ones who interact with customers and listen to real-time feedback.
Use employees to help identify areas to enhance for the customer.
3. Process Oriented
Everything contains a process. Whether the process to hire employees or a process to form a cake – there are steps that lead the way
TQM organizations study steps in a process, fine-tune those steps, and work to eliminate unnecessary steps which will save time and money.
For instance, use quality tools to make a visual for internal processes. Check out the steps in the process and work to reduce or eliminate unnecessary steps.
4. Mutually Dependent Systems
Most organizations have several departments or areas of expertise but all have systems that support the final delivery of the goods.
Organizations that manage with TQM integrate these internal systems to create a seamless process.
This is done by creating a culture that understands and values how quality is determined and how it's achieved.
For instance, create training for all employees that teaches quality concepts and reinforces why they're there – the vision and mission of the organization.
5. Strategic Approach
Businesses that operate under a TQM model, use strategy to assist achieve mission and vision.
They develop a strategic plan and use that as the cornerstone for its quality efforts and all decision making.
Invest the time to make a mission and vision statement and use that to guide the development of a strategic plan.
6. Continuous Improvement
Continuous improvement is how organizations get better at what they are doing by working to enhance processes that create products and services.
These constant efforts help to ensure the organization remains competitive and meets the expectations of key stakeholders.
Make it a part of daily practice to pay attention to how work gets done and continuously search for ways to enhance even the most insignificant tasks.
7. Data-Driven Decisions
Data drives decisions in TQM organizations. Data is collected, analyzed, and used to improve internal operations.
All decisions are supported by the continual collection of business data.
Business Data is set by the identification of key success measures. It's those measures that drive decisions.
Spend a while identifying the critical success factors for your organization and create a process to collect and report data on those factors.
8. Effective Communications
Communicating is a priority in organizations that strive to enhance.
Employees and customers are given on-going communication and interaction with the organization.
There are strategies that drive communication and employees are provided information about internal changes as they become available.
Create a communication strategy and constantly seek for ways to communicate with all key stakeholders.
a. TQM is a complete customer-focused approach.
b. Aims at satisfying the customer or delighting them.
c. Provides highest quality product at lowest possible price.
d. It's companywide strategy.
e. Involves everyone in the organization.
f. Prevention of defects is the way and therefore the target is zero defects.
g. Total quality management is methodical.
h. It makes moves based on information.
i. It's an endless process.
The concept of quality control originated in the U.S. And was taken to Japan by W. Edwards Deming who marked the start of revolution in quality control. As quality control awareness increased in Japan, the japanese companies used statistical quality control to motivate their workers to produce high-quality products.
One of the mechanisms used by these companies to enhance the quality not only of their products but also the personnel was quality circles which are in practice even today.
Quality circle is a group of labour and management who belong to one department, do same or similar work, meet periodically to discuss and analyse manufacturing problems (for about an hour per week in paid time) and find solutions to quality problems.
Rather than developing technical staff that works with management and workers, quality circles train the workers who identify and solve the issues they face during the production process. Quality circle is “an approach to improving quality and reducing the cost of manufacturing a product or service by the voluntary efforts of small groups of workers, who are generally led by a first-line supervisor”.
However, the supervisor doesn't issue orders. The circle members analyse their problems, gather relevant information, find solutions and implement them. The QC members don't receive monetary rewards for presenting solutions to management but receive recognition for their services to the organisation.
QCs improve the quality of products and the work atmosphere as members feel they're a vital part of the organisation who can positively contribute to product quality. Though initially started in the manufacturing area, the concept of QCs widely applies in the service sector also (banking, insurance etc.).
Quality circles are regular short meetings that help to resolve work-related problems.
(a) 5-10 people attend the meeting at work-time.
(b) Supervisor is nominated and he runs the meeting.
(c) Flip charts, audio-visual equipment, notice boards etc. are utilized.
(d) Problem areas are recommended by the group.
(e) Problems are prioritized.
(f) Information is collected; ideas are generated via brainstorming and force-field analysis.
(g) Effectiveness, costs, savings, consequences to other departments etc. are considered.
(h) Final solution is recommended to manager and implemented by the quality circle group.
Objectives of Quality Circles:
Following are the objectives of Quality Circles:
(a) To enhance the quality of products.
(b) To enhance productivity of the firm.
(c) To develop a sense of confidence in the workers that they will solve their own problems.
(d) To enhance employees’ morale.
(e) To enhance employees’ job satisfaction.
(f) To develop the personality of employees by making them aware of their importance within the work related areas and work atmosphere.
(g) To enhance interpersonal relationships between management and workers.
Quality Circle-Problem Solving Steps
In Quality circle problem solving is employed as a main process to attain its objectives. Member’s creativity is tapped to resolve their day-to-day work related problems. It’s through this process they become a cohesive team and their organizational ownership gets developed. Hence it's necessary that the group member should understand this process very clearly.
The step process for solution
1) Identification of work related problem
Method:
a) Generate a list of problem using Brainstorming
b) Prioritise problems employing a , B, C analysis
2) Selection of problem (from A list)
Method:
a) Pareto Analysis or Rating supported on past data
b) Register the chosen problem with coordinator
3) Defining the issue
Method:
Flow Diagram
4) Analyse the issue
Method:
Data Collection of problem on all possible aspects
5) Identification of causes
Method:
Brainstorming and Cause and Effect diagram
6) Finding the base of causes
Method:
Identifying the most relevant causes in Cause and Effect diagram by data collection and discussion
7) Data Analysis
Method:
a) Using techniques like bar, pie, areal graph, histogram, stratification, scatters diagram etc.
b) Why-Why analysis
8) Developing solution
Method:
Brainstorming
9) Foreseeing the probable resistance
Method:
Brainstorming
a) Identifying the probable constraints and finding ways to solve them.
b) Make a presentation to all or any involved employees to clarify the solution selected
i.e. Departmental head, facilitator, other officials and non-members involved implementation.
c) Discuss and evolve a system of implementation.
10) Trial implementation and checking performance.
Method:
a) Data collection after implementation
b) Comparison of old and new data with Pareto, Histogram, and Control charts
c) Watch process trend
d) Analyse the results.
e) Discuss and incorporate the changes needed
11) Regular implementation
Method:
Once validity is checked and improvement observed with data regular implementation are often done
12) Follow-up and review
Method:
a) Implement evaluation procedure, use control charts have six monthly reports for evaluation
b) Make modification if required
ISO 9000 is an international standard for a quality system. a quality system is concerned with the essential principles of good quality management which apply to any activity regardless of product or process. A quality system like ISO 9000 specifies what basic activities must happen, what responsibilities need to be assigned and how the people specific responsibilities should be organized.
ISO 9000 is defined as a set of international standards on quality management and quality assurance developed to assist companies effectively document the quality system elements needed to maintain an efficient quality system. They're not specific to any one industry and can be applied to organizations of any size
Steps to follow
These eight steps--along with their sub-steps--are based totally on what many principal groups have observed to realize their own ISO 9000 registration. These steps are beneficial for businesses simply in search of to adapt to the ISO 900 standards, however not formally find you certified.
These steps are a desirable guide for fixing a timeline, schedule, and conceivable charges for the procedure of becoming ISO 9000 certified.
1. Get top administration commitment
1. Top administration considers ISO 9000 registration
2. Quality steerage committee meets to think about process
3. Committee informs pinnacle administration of ISO 9000 costs, schedule, etc.
4. Top management commits to pursue ISO 9000 registration
2. Train personnel
1. Hold simple excellent and ISO 9000training for all employees
2. Select and educate personnel to be interior auditors
3. Prepare Quality Policy Manual
1. Study and recognize ISO 9000 necessities as they apply to your company
2. Write (or re-write) company Vision and Mission statements
3. Write simple Quality Policy Manual outline
4. Complete first draft of Quality Policy Manual
5. Send replica of guide to customer desiring ISO 9000 compliance (if necessary)
4. Prepare Operating Procedures
1. Define responsibilities, using Quality Manual as a guide
2. Have these liable for functions define their procedures
3. Interview managers and fine-tune procedures
4. Compare Operating Procedures with Quality Manual for consistency
5. Hold interior audit
1. Hold interior audit of ISO 9000 guide vs. ISO 9000 compliance
2. Implement corrective motion objects from audit
6. Select registrar
1. Research registrars and their cost
2. Qualify possible registrars
3. Select 0.33 birthday celebration registrar
7. Go via registration process
1. Apply for registration and audits
2. Comply with audit manner etc. with registrar
3. Hold pre-assessment audit
4. Take any needed corrective action
5. Have ISO 9000 registration audit
6. Take any wished corrective action
7. Re-audit as required
8. Take any needed corrective action
8. Obtain ISO 9000 registration
This verifies that you simply operate your business in compliance to the ISO 9000 requirements.
Summary
These simple steps can convince be a fine guide to acquiring ISO 9000 registration:
1. Get top management commitment
2. Train personnel
3. Prepare Quality Policy Manual
4. Prepare Operating Procedures
5. Hold inside audit
6. Select registrar
7. Go via registration process
8. Obtain ISO 9000 registration
Following are the ways to urge ISO 9000 certified:
• First, make a concise quality mission statement for your company. Then openly post it and familiarize all your employees with it. By employing a quality mission statement as a guideline, the management must develop an in depth set of quality goals for the organization.
• Establish a group of policies which will be the instructor for every work guiding on how to achieve the overall quality goals. You’ll also develop a related process to manage and monitor whether the work elements are following the policies and achieving the quality goals.
• Proper education to the workforce on the new quality management system. Besides, make sure that each work element is knowledgeable about their work instructions and understand how they will be evaluated in terms of achieving quality goals.
• Implement processes of quality and instructions throughout the company. When the changes to the quality management system are required then only allow the authorized senior management personnel to form such changes. Side by side, a careful control over all policy of documents and work instructions is additionally necessary so you can later demonstrate to certification personnel that nobody other than authorized personnel has accessed or amended the documents.
• In any recognized ISO 9000 Certifying body, you'll contact to request a certification audit. These certification organizations are present throughout the US and in dozens of countries overseas.
• Now, you want to publish the date of the pending audit to all employees and ensure they're fully familiar with their specific instructions, policies, and quality goals, also as the overall corporate quality mission statement.
• To conduct the ISO 9000 Audit of your company also as for processes, permit the certifying organization. Afterward, demonstrate that your documentation as employees knows their work elements processes in reference to meeting company quality goals and that you've got effective quality management systems in place.
• At last, obtain certification documents from the certifying organization after successfully completing the audit.
ISO 14000 series is a voluntary set of standards intended to encourage organisations to systematically address the environmental impacts of their activities. The goal is to establish a standard approach to the environmental management system that's internationally recognised resulting in improved environmental protection.
ISO 14000 is a management system standard. It’s intended to be applicable to firms and organisations. It includes an organizational evaluation standard and therefore the standard for product services and processes.
Further, it provides a general framework for organizing the tasks necessary for effective environmental management. The series of documents that encompass ISO 14000 includes components, like environmental management systems, environmental auditing, and environmental labelling and merchandise life cycle assessment.
Environmental Auditing:
Environmental auditing is a management tool comprising a scientific documented, periodic and objective evaluation of how well environmental organisation, management and equipment are performing with the aim of helping to safeguard the environment by facilitating management control of environmental practices and assessing compliance with company policies which might include meeting regulatory requirements.
Objectives of Environmental Audit:
The following are the objectives of environmental audit:
1. To supply management with information in order to help them make informed decisions related to improved environmental action.
2. To determine the extent to which environmental management systems in a company are performing consistent with their documented procedure and aims.
3. To spot potential waste management costs.
4. To cut back exposure to litigation and regulatory risk.
5. To extend employee awareness of corporate environmental policy and responsibility.
6. To enhance the public image of the corporation.
7. To spot new markets and commercial opportunities.
Benefits of Environmental Audit Report:
The environmental audit report is a useful weapon in applying the principle of polluter pays principle and user pays principle for the protection of the environment. The government can impose taxes on the polluting industries by verifying the environmental audit report. Therefore, environmental audit is an excellent management tool to assess the activities of an industry from a pollution angle and measures the efficiency of control measures.
Moreover, the communication gap between the public and the industries are often minimised by publishing environmental audit reports. The wrong notion of the public generally that industries are the major pollutants can be minimised if industries are transparent in this regard. Last but not the least, efficiency or inefficiency of the varied production units is assessed by environmental audit reports.
The advantages of getting ISO 14000 Certified
Following are the advantages of getting the ISO 14000 certification:
1. It identifies and controls the environmental impact of its activities, product or services.
2. Continuously improve its environmental performance
3. Helps in implementing a scientific approach to setting environmental objectives to achieving these and to demonstrating that they need been achieved.
4. Ensuring legal compliance.
Apart from this, there are several other benefits also which is categorized under Internal benefits and External benefits:
Internal Benefits:
• Assurance to the management: it's in the control of the organizational procedures and activities having an impression on the environment.
• Assure employees: It assures the workers that they're working for an environmentally responsible organization.
External Benefits:
• It provides assurance on environmental issues to the external stakeholders like customers, community and regulatory agencies.
• Comply with the regulations of the environment.
• Claims and communication: It supports the organization’s claims and communication about its own environmental policies, plans, and actions by gaining its EMS certificate.
• Demonstrate conformity: It provides a framework for the demonstration conformity via suppliers’ declarations of conformity, assessment of conformity by an external stakeholder like a business client and for certification of conformity by an independent certification body.
‘Inventory refers to the stockpile of the product a firm is offering for sale and the components that make up the merchandise.’ In short, inventory is such a sort of asset which can be disposed of in future in the ordinary course of the business.
The objectives of inventory management are as follows:
1. To ensure a continuous supply of materials and stock so that production shouldn't suffer at the time of consumer demand.
2. To avoid both overstocking and under-stocking of inventory.
3. To maintain the supply of materials whenever and wherever required in enough quantity.
4. To maintain minimum working capital as needed for operational and sales activities.
5. To optimize various costs indulged with inventories like purchase cost, carrying a cost, storage cost, etc.
6. To keep material cost in check as they contribute to reducing the cost of production.
7. To eliminate duplication in ordering stocks.
8. To attenuate loss through deterioration, pilferage, wastages, and damages.
9. To ensure everlasting inventory control in order that materials shown in stock ledgers should be physically lying within the warehouse.
10. To ensure the quality of products at reasonable prices.
11. To facilitate furnishing of data for short and long-term planning with a controlled inventory.
12. To provide the required material continuously.
13. To maintain a systematic record of inventory.
14. To create stability in price.
Meaning of Inventory Management
Inventory Management is a practice of tracking and controlling the inventory orders, its usage and storage alongside the management of finished goods that are ready for sale. Improper inventory management can result in a rise in storage cost, working capital crunch, wastage of resource, and increase in idle time, disruption of the availability chain, etc. All this results in a decrease in sales and unsatisfied customers Therefore, inventory management is a vital aspect of the business which the management cannot afford to ignore. Effective and efficient management of the same is a must.
Inventory Management Techniques are as follows:
There are various sorts of inventory management techniques which may help in efficient inventory management. They’re as follows:
ABC Analysis
ABC analysis stands for Always Better Control Analysis. It's an inventory management technique where inventory items are classified into three categories namely: A, B, and C. The things in a category of inventory are closely controlled because it consists of high-priced inventory which may be less in number but are very expensive. The things in B category are relatively less expensive inventory as compared to A category and the number of items in B category is moderate so control level is also moderate. The C category consists of a high number of inventory items which require lesser investments therefore the control level is low. Types of Inventory Management Techniques
Just In Time (JIT) Method
In the Just in Time method of inventory control, the company keeps only as much inventory as it needs during the production process. With no excess inventory in hand, the corporation saves the cost of storage and insurance. The corporate orders further inventory when the old stock of inventory is close to replenishment. This is often a little risky method of inventory management because a little delay in ordering new inventory can result in a stock out situation. Thus this method requires proper planning so new orders can be timely placed.
Material Requirements Planning (MRP) Method
Material Requirements Planning is an inventory control method in which the manufacturers order the inventory after considering the sales forecast. The MRP system integrates data from various areas of the business where inventory exists. Based on the information and demand within the market, the manager would carefully place the order for new inventory with the material suppliers.
Economic Order Quantity (EOQ) Model
Economic Order Quantity technique focuses on taking a decision regarding what proportion quantity of inventory should the corporate order at any point of time and when should they place the order. In this model, the shop manager will reorder the inventory when it reaches the minimum level. EOQ model helps to save the ordering cost and carrying costs incurred while placing the order. With the EOQ model, the organization is in a position to place the proper quantity of inventory.
Minimum Safety Stocks
The minimum safety stock is the level of inventory which an organization maintains to avoid the stock-out situation. It’s the level once we place the new order before the existing inventory is over. Like for instance, if the entire inventory in an organization is 18,000 units, they place a new order when the inventory reaches 15,000 units. Therefore, the 3,000 units of inventory shall form a part of the minimum safety stock level.
VED Analysis
VED stands for Vital Essential and Desirable. Organizations mainly use this system for controlling spare parts of inventory. Like, a higher level of inventory is required for vital parts that are very costly and essential for production. Others are essential spare parts, whose absence may slow down the production process, hence it's necessary to maintain such inventory. Similarly, a corporation can maintain a low level of inventory for desirable parts, which aren't often required for production.
Fast, Slow & Non-moving (FSN) Method
This method of inventory control is extremely useful for controlling obsolescence. All the items of inventory aren't utilized in the same order; some are required frequently, while some aren't required at all. So this method classifies inventory into three categories, fast-moving inventory, slow-moving inventory, and non-moving inventory. The order for new inventory is placed based on the use of inventory
Inventory Costs
Inventory procurement, storage and management is associated with huge costs related to each of these functions.
Inventory costs are basically categorized into three headings:
Ordering Cost
Carrying Cost
Shortage or stock out Cost & Cost of Replenishment
Cost of Loss, pilferage, shrinkage and obsolescence etc.
Cost of Logistics
Sales Discounts, Volume discounts and other related costs.
1. Ordering Cost
Cost of procurement and inbound logistics costs form a part of Ordering Cost. Ordering Cost is dependant and varies supported two factors - the cost of ordering excess and therefore the Cost of ordering too less.
Both these factors move in opposite directions to each other. Ordering excess quantity will result in carrying the cost of inventory. Whereas ordering less will result in increase of replenishment cost and ordering costs
These two above costs together are called Total Stocking Cost. If you plot the order quantity vs the TSC, you'll see the graph declining gradually until a certain point after which with every increase in quantity the TSC will proportionately show an increase.
This functional analysis and price implications form the idea of determining the Inventory Procurement decision by answering the 2 basic fundamental questions - how much to Order and When to Order.
How much to order is decided by arriving at the Economic Order Quantity or EOQ.
2. Carrying Cost
Inventory storage and maintenance involves various sorts of costs namely:
• Inventory Storage Cost
• Cost of Capital
Inventory carrying involves Inventory storage and management either using in house facilities or external warehouses owned and managed by third party vendors. In both cases, inventory management and process involves extensive use of Building, Material Handling Equipment, IT Software applications and Hardware Equipment coupled managed by Operations and Management Staff resources.
a) Inventory Storage Cost
Inventory storage costs typically include Cost of Building Rental and facility maintenance and related costs. Cost of material Handling Equipment, IT Hardware and applications, including cost of purchase, depreciation or rental or lease as the case could also be . Further costs include operational costs, consumables, communication costs and utilities, besides the cost of human resources employed in operations also as management.
b) Cost of Capital
Includes the costs of investments, interest on capital, taxes on inventory paid, insurance costs and other costs related to legal liabilities
The inventory storage costs as well as cost of capital is dependent upon and varies with the choice of the management to manage inventory in house or through outsourced vendors and third party service providers.