Unit 02
Question Bank
Q-1What are monomers?
Monomers are atoms that bond together to form more complex structures such as polymers. There are four main types of monomer i.e.; sugars, amino acids, fatty acids, and nucleotides. Each of these monomer types play important roles in the existence and development of life and each one can be synthesized abiotically. Monomers are commonly found in the interstellar medium, nebulae, and chondritic meteorites. The number of repeating units (n) in the chain so formed is called the Degree of polymerization (DP=n). Polymers with a high degree of polymerization are called High polymers and those with low degree of polymerization are called Oligo polymers.
Q-2Explain chain polymerization.
The addition polymerization is the process in which the linking together of monomer molecules by a chain reaction is observed. Polymer synthesized by addition polymerization has the same empirical formula as that of monomer. No molecule is evolved during polymerization and the polymer is an exact multiple of the original monomeric molecule.
Q-3Explain co-polymerization.
Addition polymerization involving a mixture of two or more suitable or compatible monomers gives a copolymer and the process is known as copolymerization. A reaction in which a mixture of two or more monomers is allowed to undergo polymerization is known as copolymerization. The polymer is known as copolymer.
E.g.: Copolymerization of styrene and methyl methacrylate
Q-4Explain mechanism of free radical polymerization.
The formation of polymer from the successive addition of free-radical building blocks through the polymerization is called as the free radical polymerization. In order to obtain the wide variety of different polymers and material composites the free radical polymerization plays a major role in it. The relatively non-specific nature of free-radical chemical interaction make it one of the most versatile forms of polymerization which allows a facile reactions of polymeric free radical chain ends and other chemical or substrates. The monomers from which addition polymers are made are alkenes. The most common and thermodynamically favored chemical transformations of alkenes are addition reactions. Many of these addition reactions are known to proceed in a stepwise fashion by way of reactive intermediates, and this is the mechanism followed by most polymerization. The monomers are initiated by traces of oxygen, the pure compounds are stabilized by radical inhibitors.
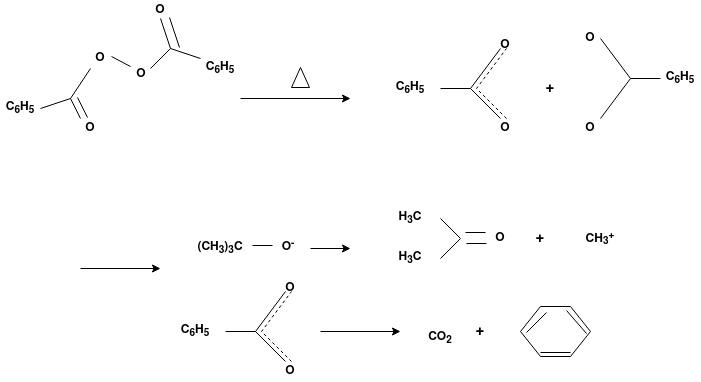
Radical Initiators
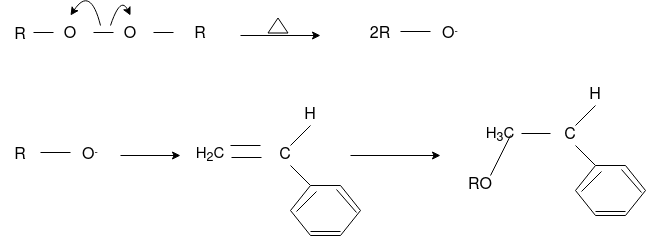
Chain Initiation
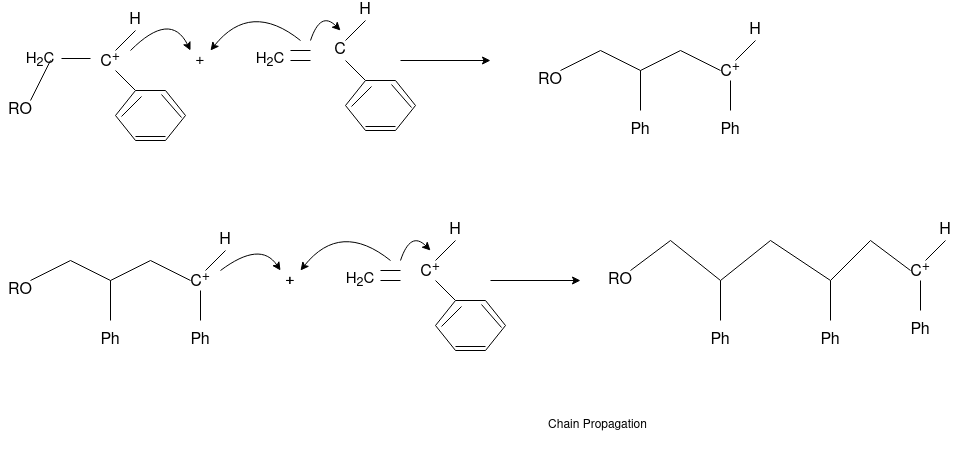
Chain Propagation
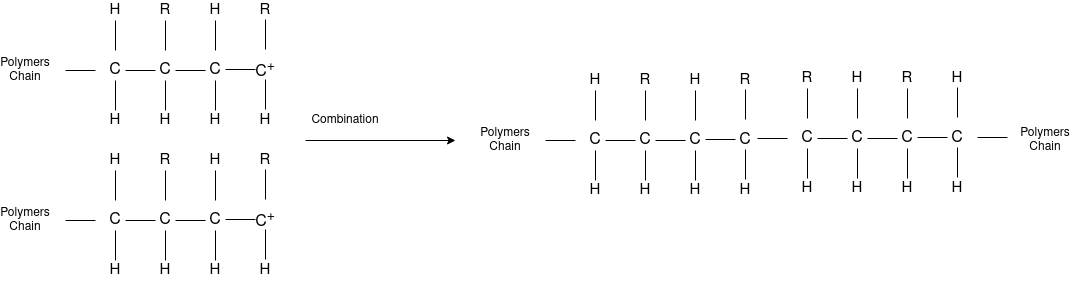
Chain Termination
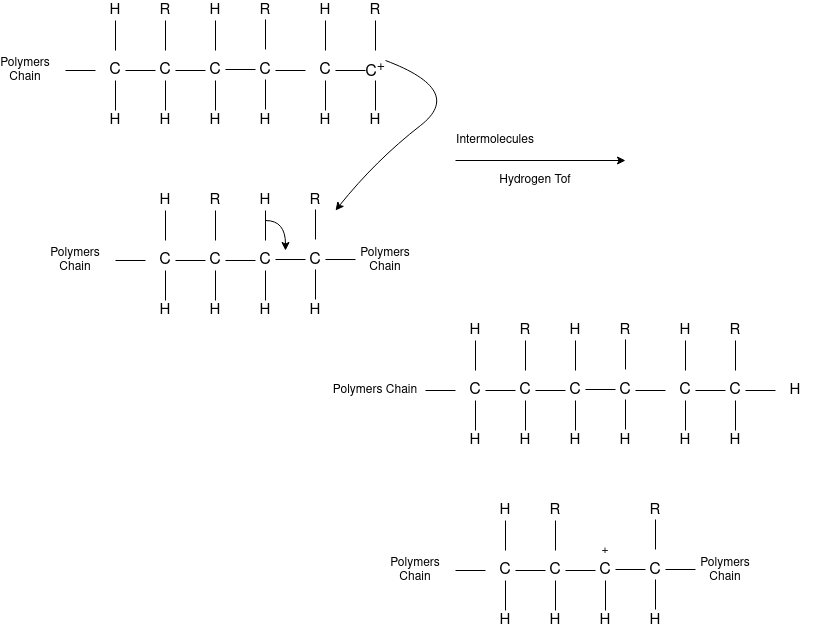
Chain Transfer Reaction
Q-5Explain the mechanism of cationic polymerization.
Cationic polymerizations are typically initiated by carbocations, generated by protonation of an alkene with a strong acid such as sulfuric or tri-fluoro methane sulfonic acid.
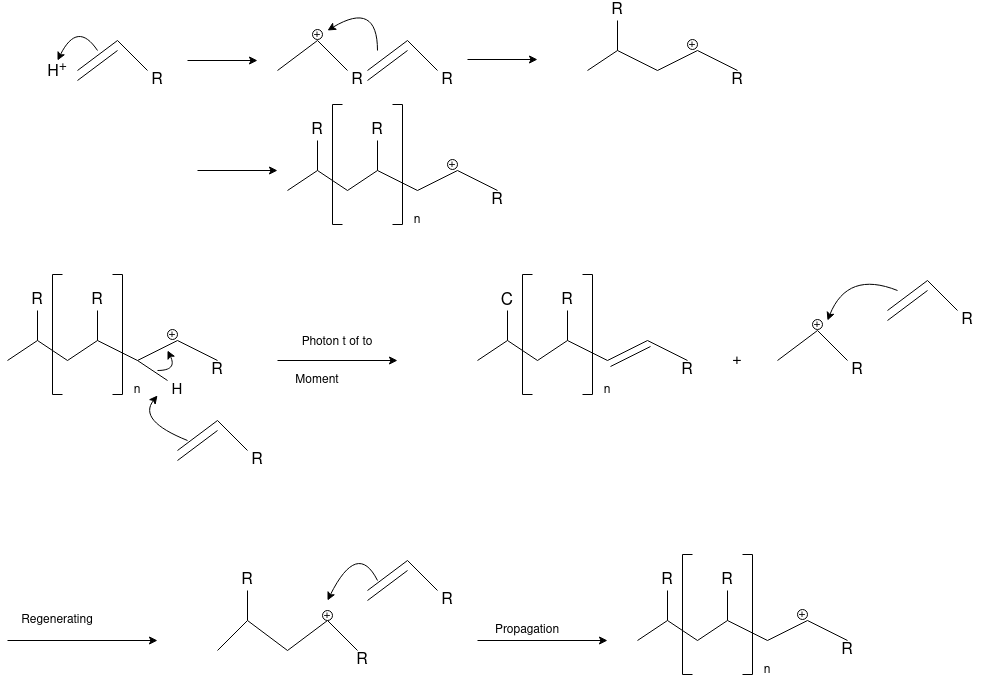
Q-6What are thermoplastic polymer?
A thermoplastic is a resin that is solid at room temperature but becomes plastic and soft upon heating, flowing due to crystal melting or by virtue of crossing the glass transition temperature (Tg). Upon processing, usually via injection-molding or blow-molding-like processes, thermoplastics take the shape of the mould within which they are poured as melt, and cool to solidify into the desired shape. The significant aspect of thermoplastics is their reversibility, the ability to undergo reheating, melt again, and change shape. This allows for additional processing of the same material, even after being prepared as a solid. Processes such as extrusion, thermoforming, and injection molding rely on such resin behavior. Some common thermoplastic materials include polyethylene (PE), polycarbonate (PC), and polyvinyl chloride (PVC).
Q-7What are thermosetting polymer?
A thermosetting resin, or thermosetting polymer, is generally a liquid material at room temperature which hardens irreversibly upon heating or chemical addition. When it is placed in a mould and heated, the most solidifies into the specified shape, but this solidification process includes the formation of certain bonds, called cross links, that hold the molecules in place and change the basic nature of the material, preventing it from melting. As a result, a there most, as opposed to a thermoplastic, cannot return to its initial phase, rendering the process irreversible. There most, upon heating, become set, fixed in a specific form. During overheating, there most tend to degrade without entering a fluid phase. Processes such as compression molding, resin transfer molding, pultrusion, hand lay-up, and filament winding depend on thermosetting polymer behavior. Some common there most include epoxy, polyimide, and phenolic, many of which are significant in composites.
Q-8Explain the synthesis of Bakelite.
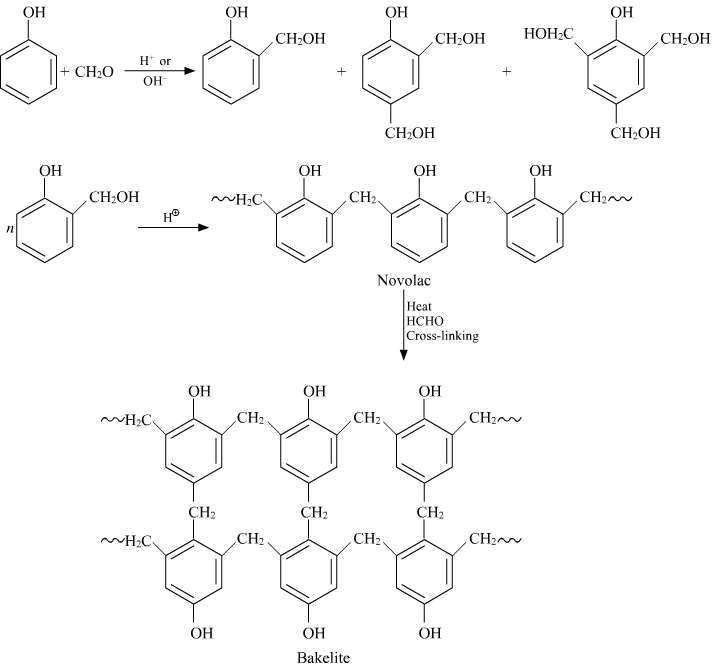
Q-9Explain the applications of Bakelite.
- This element has a low electrical conductivity and high heat resistance
- It can be used in manufacturing electrical switches and machine parts of electrical systems.
- It is a thermosetting polymer and Bakelite has high strength meaning
- It basically retains its form even after extensive molding.
Phenolic resins are also extensively used as adhesives and binding agents. They are further used for protective purposes as well as in the coating industry.
Q-10What are natural rubbers?
Natural Rubber is a high molecular weight hydrocarbon polymer represented by the formula (C5H8)x. It is obtained from a milk emulsion called latex by tapping the bark of the tree. “Heve a brasiliensis”. It is a polymer of isoprene units.
n H2C = C – CH = CH2 ( H2C – C = C – CH2 )n
CH3 CH3
The polymer chain of natural rubber is made of 2000 to 3000 monomer units.
Q-11Explain Buna-S with its applications.
Buna-S is also known as the styrene-butadiene. It is a copolymer of butadiene (75%) and styrene (24%). Buna is derived from the Bu-Butadiene while Na is Sodium or Natrium and S is Styrine. Buna-S is the replacement of natural rubber while styrene, 2 monomers and butadiene play a major role in its derivation where as these 2 monomers is polymerized by two basically different process i.e., from solution (S-SBR) or as an emulsion (E-SBR). It is prepared by the copolymerization of butadiene & styrene.
It is a random co-polymer formed by the emulsion polymerization of a mixture of 1:3 butadiene and styrene in the presence of peroxide as a catalyst at 5o C and this is the reason why the product is called as cold rubber. The obtained rubber is called as the Styrene Butadiene Rubber (SBR).
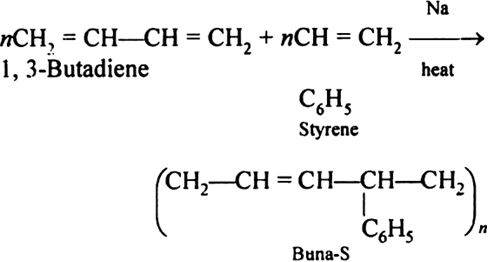
Applications:
(i) Buna-S is used as the natural rubber i.e., they are widely used in pneumatic tires.
(ii) SBR is extensively used in coated papers.
(iii) They are highly used in building materials as a binding material.
SBR is also used as binder in lithium-ion battery electrodes.