Unit-1
High Polymers
1. Define Polymers and explain its type and Mechanism?
A polymer is a large molecule with high molecular weight, this high molecular weight is obtained when smaller molecules having low molecular weight of one or more types undergo the chemical interaction. The process of manufacture of a polymer is known as polymerization.
Polymer, either they are natural or synthetic substances consists of very large molecules called macromolecules, these macromolecules are units or multiples of simpler chemical units called monomers. Polymers find their space in many of the materials in living organisms, including, for example, proteins, cellulose and also nucleic acids. They are also present in manmade materials such as concrete, glass, plastics and rubbers, polymers also constitute the basis of such minerals like diamond, quartz and feldspar.
The word polymer designates an unspecified number of monomer units. When the number of monomers is very large, the compound is sometimes called a high polymer
Types of Polymerisation and Mechanism.
The repeated units of monomers form the basis for the formation of, these are linked together by covalent bonds. The reaction leading to the formation of with their respective monomers is called polymerization.
Addition polymerization:
In Addition, polymerization, molecules of the same or different monomers add up together to form a polymer on a large scale. When monomers are being added to form a large chain such a process is known as chain growth polymerization. The monomers that are used in this type of polymerization are unsaturated compounds (the compounds of carbon are connected by double or triple covalent bonds).
- For example, alkenes, alkynes and alkadienes.
The chain length is increased either by the formation of ion species or free radicals, in this case however the reaction takes place in the presence of free radicals, the mechanism is discussed below
Free radical mechanism:
Free generating initiator are the catalysts that polymerize the reaction of the compound of alkenes and their derivatives.
- For example, benzoyl peroxides.
When ethene is polymerised to polythene, the mixture of ethene is first heated with a small amount of the initiator benzoyl peroxide. A new and large free radicle is formed, when there is an additional free radicle formed by peroxide to the double bond of ethane. This step is known as the chain initiating step, this means that the chain formation is initiated in this very step. As the process proceeds, a bigger sized radical is formed as the free radical obtained from the first step reacts with another molecule of ethane. A chain propagating step is formed as the reaction continuous with the sequence being repeated leading to the formation of bigger and new radicals. The last stage being the chain termination step, where the radical formed and the product radical react with another radical to form the final polymerized product, and hence this is called the chain terminating step.
2. Condensation polymerization:
This type of polymerization involves a repeated condensation process between bi-functional monomers. Simple molecules such as water and alcohol are lost due to the condensation process. The Mechanism of Condensation mechanism refers to combining of smaller molecules to get larger molecules. The product that is formed in this polymerization is a bi-functional species, these species will further undergo a sequence of processes, however at each step a very unique and distinct functional species and each species that is forms is independent when compared to the other species. Hence this process is called as step growth polymerization.
- Examples, include ethylene glycol and terephthalic acid.
2. Explain two properties of polymers?
Properties of Polymers
Physical Properties
- The tensile strength of the polymer increases with the increase in chain length and tensile strength.
- Polymers do not melt; they change their state from crystalline to semi-crystalline.
- Many small molecules called monomers form polymers through a process called polymerization, polymers can either be natural or synthetic. Their consequently large molecular mass relative to small molecules, produce unique physical properties that include toughness, high elasticity viscoelasticity, and a tendency to semicrystalline and amorphous forms rather than crystalline form.
Mechanical Properties
With some basic mechanical properties of the material before its application in any field, such as how much it can be stretched, how much it can be bent, how hard or soft it is, how it behaves on the application of repeated load and so on. a. Strength: In simple words, the strength is the stress required to break the sample. There are several types of the strength, namely tensile (stretching of the polymer), compressional (compressing the polymer), flexural (bending of the polymer), torsional (twisting of the polymer), impact (hammering) and so on. The polymers follow the following order of increasing strength: linear < branched < cross-linked < network. Factors Affecting the Strength of Polymers
1. Molecular Weight: with the increase in molecular weight the tensile strength of the polymer increases, and reaches the saturation level is reached at some value of the molecular weight. When the molecular weight of the polymer is low, the polymer chains are loosely bound by the weak van der Waals forces and therefore the chains can move easily, and are also responsible for low strength, although crystallinity is present. When the molecular weight is large, the chains get entangled and become large and thereby give strength to the polymer.
2. Cross-linking: The strength of the polymer increases as the cross-linking controls the motion of the chains.
3. Crystallinity: The crystallinity of the polymer increases strength, because in the crystalline phase, the intermolecular bonding is more significant. Hence, the polymer deformation can result in the higher strength leading to oriented chains.
3. What are Plastics?
Plastics are compounds that have a wide range of synthetic or semi-synthetic organic compounds that are easily malleable and can be moulded into any solid form. Plastics are typically polymers that have molecular mass and are organic in nature, and often contain other substances also. They are usually synthetic in nature, most commonly derived from petrochemicals. However, an array of variants is made from renewable materials such as polylactic acid from corn or cellulosic from cotton linters.
Plastic, polymeric material that has the capability of being moulded or shaped, usually by the application of heat and pressure. This property of plasticity, often found in combination with other special properties such as low density, low electrical conductivity, transparency, and toughness, allows plastics to be made into a great variety of products.
4. Explain the compounding and fabrication of Plastics?
Compounding is a procedure that provides formulations for the formation of plastics. The formulations consist of mixing or blending polymers that are in a melted state to attain the needed characteristics. Through hoppers the blends doses are automatically fixed at set points the blends usually are ABS, SMA, SAN. Strengthening agents like glass fibres are added if characteristics. Through-stabilizers and anti-oxidants are the additives that are added.
Compounding is usually done by extrusion the process begins with a hopper where the resins are added to the dye gradually. There are different zones in the barrel that can be modified according to the properties of resin.
The most common compounders used in the plastic industry are the Co-kneaders and twin screws (co- and counter rotating) as well internal mixers.
The process proceeds to form extrudates, which are land plastic threads or strands, these are then cooled in a water bath or sprayed on a conveyor belt, which then moves into a granulator, in the granulator the strands are broken down to obtain the desired pellet sizes.
The manufacture design and assembly of plastic is done by one of the methods
Plastic Fabrication Methods
The property of plastic, that include cost efficiency and its malleability, can make it a durable product for a wide range of products.
Plastic Welding
Plastic welding includes heating the substance to melt two or more pieces together. The thermoplastics which are known to be unsuitable for adhesive binding is effective for this process.in this process the individual pieces are fused or joined together with a filler material between them, this is done when the pieces differ extremely in the boiling point. Welding is accomplished by different methods like high frequency vibration, spinning or hot gas.
Compounding (or Blending) Plastic Fabrication Techniques
This process involves combining two or more plastics to form an amalgam, which later is formed into a single part. In this process, the plastic that is in molten form is mixed with exact specifications which eventually forms them into a mould, dye or any other tool.
Compounding is often used to improve the ease of processing a given material or to enhance product performance. By combining the advantages and disadvantages of several types of plastic, the process can result in a unique material complementary to a specific application. Some common types of plastic compounds include:
- Polymer fillers
- Base resins
- Pigment master batches
- Blowing agents
- Flame-retardants
- Purge compounds
Plastic Lamination
Lamination in plastics creates a barrier on another material along its surface. Lamination is done to improve certain features in the product such as styling, durability or the products aesthetic quality. Lamination also helps in reducing the cost of the material, in cases the material is sensitive or is prone to destruction, lamination helps in shielding the defects and reduces its need for maintenance.
Two most common types of lamination are the film and resin. In both processes, for a moving substrate, heat and pressure are applied for adhesion to a fabricated film the most effective method for forming a plastic barrier on the exterior of the product is the film lamination method., while resin lamination is more frequently used to create an adhesive layer between two substrates. Paper, fabrics, metal sheeting, and flexible foam are common lamination base materials.
Moulding Processes
In plastic moulding, plastic is formed into a specified shape by allowing the heated, pliable work piece to cool and harden around or within a mould. There are various methods for plastic moulding methods. They are blow moulding, injection melding and rotational moulding. Rotational melding is utilised in hollow products that are plastic in nature, they include toys, buoys and automotive parts, products such as fuel tanks or bottles are done by Blow moulding is often used to create containers, while injection melding is used in large scale production like dishware that need a higher melt index, like dishware production.
Plastic Extrusion
Plastic Extrusion is a process that can be used to prepare tubing, piping, or components used for sheeting. The Extrusion process is utilised to further enhance the processing stages. For example, plastic extrusion is often a precursor to adhesion or lamination procedures.
Profile extrusion and sheet extrusion are the most common forms of the process. profile extrusion is a process where the plastics pellets are melted using a single screw extruder, the melted plastic is moves through a pressurized screw mechanism and forms an annual dye by pressure. Very thin plastic sheets are obtained through this method, the plastic formed solidifies around a calibration sleeve to create a pipe or tube component of a specific diameter. The Sheet extrusion method, also uses a similar technique to create thin plastic sheeting.
Plastic Foaming
A variety of different shapes are formed from Foam products. Configurations of Common foaming configurations include sheet, round, film, solid plank, rod and bun stock. To achieve the desired characteristics, polymer composites are typically shaped through a process of physical or chemical blowing.
Choosing a Plastic Fabrication Process
Product functionality and ease of manufacturing are important things to consider when choosing a plastic fabrication process. Some methods are inefficient for fabricating certain types of plastic, and therefore may not be helpful for your particular project. Some other issues to keep in mind include:
- The need for single plastics versus plastic compounds
- The intended proportion of plastic to non-plastic material in the product
- The role of plastic in your fabrication process (as adhesion, lamination or base product)
- The dimensions and use of the final product,
5. Explain the Preparation and properties of Bakelite?
Bakelite is the commercial name for the polymer obtained by the polymerization of phenol and formaldehyde. These are one of the oldest polymers that were synthesized by man. Phenol is made to react with formaldehyde. The condensation reaction of the two reactants in a controlled acidic or basic medium result in the formation of ortho and para hydroxymethyl phenols and their derivatives.
Preparation and Properties of Bakelite
In a reaction when Phenol is present in excess, the reaction becomes acidic making the end product also acidic, however, when formaldehyde is added in more quantity than phenol the reaction becomes basic and the end product becomes basic in nature and is known as Resol.
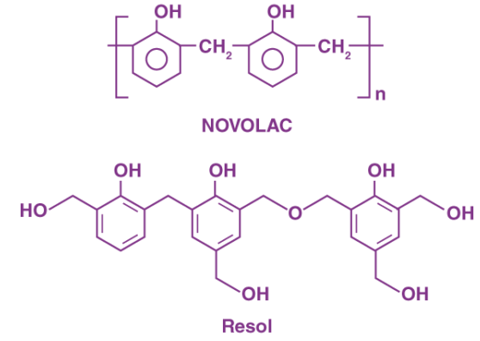
Fig 5: Structures of Resol and Novolac
There are intermediate products formed during the process of condensation and these are used as resins in the industries These intermediate condensation products are used as resins in different industries. When the compound Novolac undergoes cross linking with the help of phenol, which acts as a cross linking agent. Bakelite is produced.
The preparation of Bakelite involves several steps, as illustrated below.
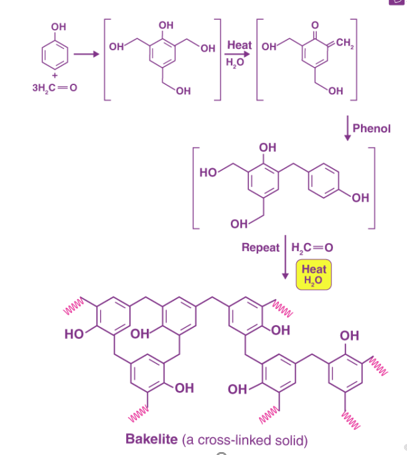
Fig 6: Preparation of Bakelite.
Initial methods of preparing Bakelite involved the heating of formaldehyde and phenol in the presence of one of the following catalysts -zinc chloride (ZnCl2), hydrochloric acid (HCl), or ammonia (NH3).
Bakelite Structure
The cross-linked product of phenol and formaldehyde has the following structure.
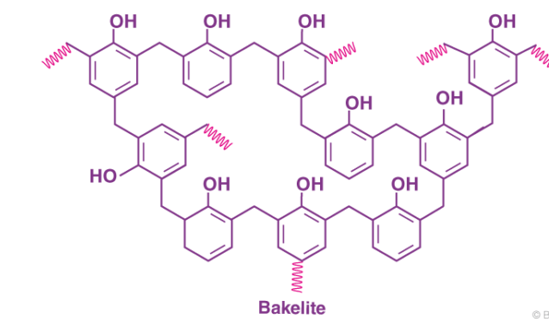
The chemical formula of Bakelite can be written as (C6H6O-CH2OH) n.
Properties of Bakelite
Some important properties of Bakelite are listed below.
- Bakelite can be quickly moulded.
- The smooth mouldings can be obtained with this polymer.
- Bakelite mouldings are heat-resistant and scratch-resistant.
- Bakelite is also resistant to several destructive solvents.
- Owing to its low electrical conductivity, Bakelite is resistant to electric current.
6. What is Thiokol Rubber?
Polysulfides, also called polythioethers or Thiokols (T), are compounds with thioether functions in the backbone. They are typically liquid polymers that can be crosslinked by oxidizing the polymer’s terminals thiol groups (-SH) to disulfide (-S-S-) links. Common curing agents are oxygen donating compounds such as manganese dioxide, cumene hydroperoxide, and p-quinone dioxime. Other organic hydro peroxides, aldehydes and metallic paint driers can also function as curatives.
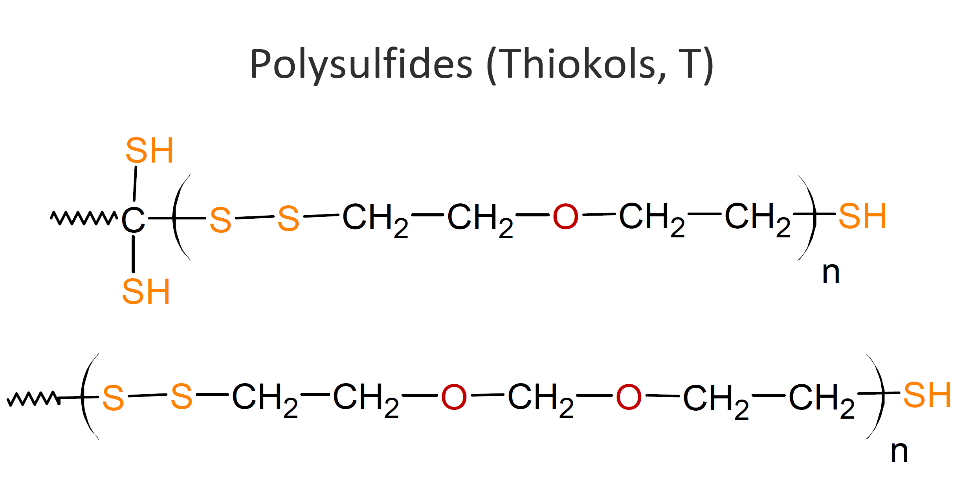
Thiokol elastomers show good resistance to oil, oxygen and ozone and other chemicals like aromatic hydrocarbons they exhibit gas permeability, and resistant to cracks. However, polythioethers have some major limitations. They do not stand out with respect to performance when compared to other elastomers, they show very poor resistance to heat, low tear. They are also not resistant to many polar solvents including (fatty) esters, mercaptans, amines, and chlorinated hydrocarbons.
APPLICATIONS
Polysulfides are widely used as the base polymer for sealants, caulks, and adhesives in various applications within the building & construction, aircraft, and automobile industry. Other industrial applications include highways sealants, molding / potting compounds, and concrete coatings.
The typical working temperature range is -45°C to +105°C. However, some grades can withstand temperatures up to 150/170°C (for a short time).
7. Define Elastomers?
Elastomers are polymers that are having a viscosity as well as elasticity and therefore are known as viscoelasticity. The molecules of elastomers inherit the property of regaining its original shape and size even after being stretched to a great extent. The molecules are held together by weak intermolecular forces; however, they show high strength yield or strain in failure.
8. Explain Vulcanization of Rubber?
Vulcanization, is a process natural rubber is treated with sulphur, the physical properties of both natural and synthetic polymers are improved. The rubber that has undergone vulcanization shows higher tensile strength and becomes resistant to abrasion or swelling,
Vulcanization is defined as a process of curing elastomers, in the process cross linking are formed between sections of polymer chains, thereby increasing their durability and rigidity. Changes are also brought about in the electrical and mechanical properties of the material. Vulcanization, in common with the curing of other thermosetting polymers, is generally irreversible.
The word vulcanization is derived from Vulcan, the Roman god of fire and forge.
9. What are Biodegradable Polymers?
Some examples are given as follows: -
Poly β-hydroxybutyrate – co-β-hydroxy valerate (PHBV): It is derived by combining 3-hydroxy butanoic acid and 3-hydroxy pentanoic acid, in which monomers are cross-linked by an ester linkage. It decomposes to form carbon dioxide and water. The compound is brittle and is utilised in drug production and bottle manufacture.
A polymer that can be decomposed by bacteria is called a biodegradable polymer.
The biodegradable polymer are the polymers which are degraded by the micro-organism within a suitable period so that biodegradable polymers & their degraded products do not cause any serious effects on the environment. They degrade by enzymatic hydrolysis & oxidation. The decomposition reactions involve hydrolysis (either enzymatically induced or by non –enzymatic mechanism) to non- toxic small molecules which can be metabolized by or excreted from the body.
The common examples of aliphatic biodegradable polymers are polyglycolic acid(PGA), Polyhydroxy butyrate (PHB), Polyhydroxy butyrate’s-co-beta hydroxyl valerate( PHBV), Polycaprolactone(pcl), Nylon-2-nylon-6.
These polymers are used mainly for medical goods such as surgical sutures, tissues in growth materials, for controlled drug release, plasma substitutes etc. They are also used in agriculture materials, such as films, seed coatings, fast food wrappers, personal hygiene products etc.
10.Define Thermo plastics and Thermosetting plastics?
One important classification of plastics is by the characteristic of permanence or impermanence of their form, or whether they are: thermoplastics or thermosetting polymer.
Thermoplastics these are plastics that do not show any changes in their chemical composition when subjected to heating, therefore they can be moulded again and again. Examples include: PVC, polystyrene and polypropylene.
Thermosets, or thermosetting polymers, when heated will melt and will take shape only once it cannot be moulded any further once they are solidified. If they are heated again, they do not melt but decompose. An irreversible chemical reaction occurs in the thermosetting process. A good example of thermosetting polymers is vulcanization of rubber is an example of a thermosetting process.