Unit - 5
Sandwich structures
Q1) Define sandwich structures.
A1)
Due to its excellent strength-to-weight ratio, sandwich architecture has found widespread use in aircraft, missiles, and spacecraft constructions. As seen in Figure 13, this form of construction is made up of thin, rigid, and strong sheets of metallic or fibre composite material separated by a thick layer of low density material. The core material is a thick layer of low-density material that can be light foam (e.g., Nomex core or Rohacell as shown in Figure 14a), metallic honeycomb (as shown in Figure 14b), or corrugated core (as shown in Figure 14c). The face sheets are usually adhered to the core material with glue.
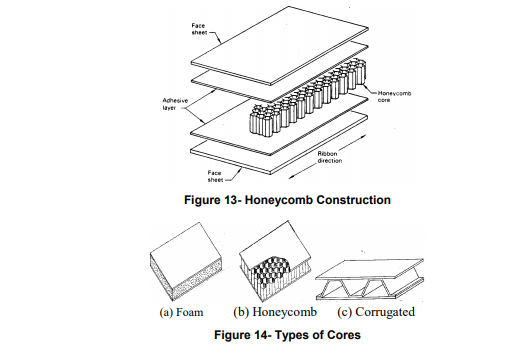
The core of various sandwich structures is constructed of metallic or composite material corrugations (Figure 14c). If the face sheets are made of metallic material, the corrugated core can be glued, riveted, or weld bonded. The core of a sandwich made using composite face sheets can be bonded or co-cured with the face sheets.
Q2) What are the advantages of sandwich construction
A2)
The advantages of a sandwich construction are as follows:
• When compared to monolithic construction, there is a high ratio of bending stiffness to weight.
• Excellent mechanical and acoustical fatigue resistance, as well as a good damping characteristic.
• Thermal insulation has been improved.
• Because there are no mechanical fasteners, there are no crack start locations. The following are the main drawbacks of honeycomb construction:
• In-service training Corrosion is caused by trapped moisture in the core material. As a result, the structural integrity of the pieces deteriorates.
• During the fabrication process, good quality control is required to ensure that the adhesive layer does not disbond.
• During service, disbonds may form and proliferate in the adhesive layer, reducing the weight carrying capability of structures.
Q3) Define Core type arrangements.
A3)
Corrugated, honeycomb, balsa wood, and foams are the four basic types of cores used in load-bearing sandwich constructions. First and foremost, the core should be low density in order to reduce the overall weight of the sandwich design. The core is primarily susceptible to shear, which results in global deformations and core shear stresses. As a result, a core must be selected that will not fail under the imposed transverse load and has a high enough shear modulus to provide the needed shear stiffness. The critical wrinkling load is determined by the core's Young's modulus and shear modulus. Other sandwich functions, such as thermal and acoustic insulation, are largely determined by the core material and thickness. Density, shear modulus, shear strength, stiffness perpendicular to the faces, and thermal and acoustic insulation are the major features of interest for the core.
Aluminum, impregnated glass, and aramid fibre mats, such as Nomex, are the most often used honeycombs. Because of the diverse manufacturing methods used, most honeycombs have not only varied out-of-plane properties, but also different in-plane properties. This is obvious since the corrugation and expansion processes both produce double cell walls in one direction and single cell walls in the other. Anisotropy is also created by over-expanded cells. The width (W), length (L), and transverse (T) dimensions are the three primary dimensions to which material parameters of most honeycombs are related. Honeycombs offer excellent qualities, including the highest shear stiffness and strength-to-weight ratios of all available coe materials, as well as very high stiffness perpendicular to the faces. The main disadvantages are the high cost and difficult handling during sandwich element layup, as well as the fact that they cannot be employed in wet lay-up manufacturing.
Q4) Define Honey comb structures
A4)
The honeycomb structure is a natural or man-made structure with the geometry of a honeycomb to allow the minimization of the amount of used material to achieve minimal material cost and weight.
The honeycomb structure is characterised by an array of hollow cells produced between thin vertical walls, and the cells are frequently columnar and hexagonal in shape. These structures result in a material with a low density and good out-of-plane compression capabilities.
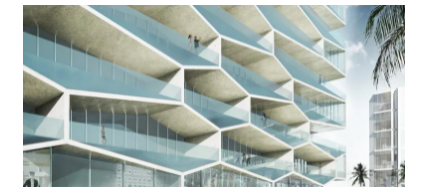
Man-made honeycomb structural materials are frequently manufactured by layering a honeycomb material between two thin layers that offer strength under tension, and honeycomb materials are widely employed in situations where flat or slightly curved surfaces are required.
Q5) What is Micromechanics models for stiffness? Explain longitudinal stiffness.
A5)
To forecast the effective elastic characteristics of composite materials, numerous micromechanics models are available (Chamis, 1984). The micromechanics model for composites with periodic microstructure is recommended for computing the ply stiffnesses for the roving and SF layers because of its precision (Luciano and Barbero, 1994). The original publication includes detailed equations for computing the elastic constants E1E2, G12, and v12, as well as experimental correlations. The SF and roving layers are commonly described as two orthogonal unidirectional composites. However, the CSM layer is considered to be isotropic in the plane, and the characteristics can be calculated as follows: (Harris and Barbero, 1998)

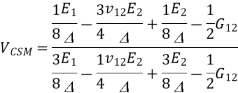

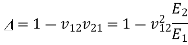
Longitudinal stiffness
The longitudinal stiffness of multispan suspension bridges plays an essential role in load-resisting systems. In this research, a model identified as the kinematic multispring (KMS) model is proposed for predicting the longitudinal deformation behaviour of multispan suspension bridges. Tower springs and cable springs constitute a series-parallel system in the KMS model. The stiffness formulas for cable springs were derived on the basis of the energy concept. The elastic elongation of the cable was evaluated and proven to be nonnegligible, especially for long-span bridges. The influence of the inclined angle of the cables was first incorporated in the formulas for the cable elastic stiffness. The elastic stiffness and the geometric stiffness of the cables were found to be relevant. Compared with numerical models, the KMS model suggested in this paper was demonstrated to be accurate and applicable.
Q6) Explain Briefly Transverse stiffness.
A6)
Quantification of both regional contractile state and its interaction with global function would be possible if regional ventricular wall stress could be determined. Mathematical modelling and strain gauge measurements are now used to quantify regional stress. Validation of these methods is tough. We expected that transverse stiffness (the ratio of indentation stress to strain as the ventricular wall is indented perpendicular to the wall) would be proportional to stresses in the plane of the wall and might be used to estimate the latter. Six arterially perfused canine ventricular septa were put in an instrument that could impose biaxial load in the plane of the wall to test this idea. During active contractions, a servo mechanism kept the central third of the septa isometric while the septa were paced at 30-60 pulses per minute. A probe with a diameter of 7 mm depressed the septa in the centre of the isometric zone, and the transverse indentation stress and strain were measured. The transverse stiffness varied from 1.2 to 11.7 g/mm2 and was linearly related to the in-plane wall stress in each septum for values of peak systolic in-plane stress ranging from 0.56 to 2.6 g/mm2 (p less than 0.001, ANOVA). The transverse stiffness of each dog after cardioplegia was also related to passively applied wall stress (p less than 0.001). Individual relationships between transverse stiffness and wall stress from active contractions had slopes that were similar to passively applied stress (mean +/- SEM; 1.82 +/- 0.36 versus 1.45 +/- 0.31, NS). (THE ABSTRACT HAS BEEN TRUNCATED TO 250 WORDS)
Fibre reinforced polymer (FRP) composites are a type of material that has piqued the interest of engineers in a variety of industries. The reinforcing fibres are the material's backbone, determining its strength and stiffness in the direction of the fibres, while some "lateral contributions" cannot be ruled out. A laminated FRP composite material's primary building component is the unidirectional lamina (Figure 1). Experimental measurements can be used to identify composite properties, but this method is both costly and time consuming (Agarwal et al., 2006, Daniel et al., 2006). As a result, any theoretical tool that allows evaluation of composite characteristics is appreciated. As a result, experimental approaches are mostly used to confirm theoretical results.
In the material axes directions, the unidirectional composite has various properties. In the design of composite structures, the stiffness properties of unidirectional fibre reinforced composites, E1 (longitudinal modulus) and E2 (transverse modulus), are required. Unlike the longitudinal modulus E1, which is dominated by fibres, the transverse modulus E2 is dominated by matrices.
Q7) Definition of Poisson's ratio
A7)
In the direction of stretching force, Poisson's ratio is the ratio of transverse contraction strain to longitudinal extension strain. Compressive deformation is regarded as negative, while tensile deformation is regarded as positive. Poisson's ratio has a minus sign in its definition, indicating that normal materials have a positive ratio. Poisson's ratio, also known as Poisson ratio, Poisson coefficient, or coefficient de Poisson, is generally written as nu in lower case.
If your browser does not recognize the Symbol typeface, Greek nu may appear as a bold face Latin n.
= -
trans /
longitudinal
In its most basic form, strain is defined as the difference in length divided by the original length.
=
L/L.
Q8) What is longitudinal compressive strength?
A8)
In modern aeroplanes, composite materials, particularly carbon pre reinforced plastics (CFRP), are commonly used. At the moment, most laminated composite structure design approaches rely on linear elastic structural analysis mixed with failure criteria denied at the scale of the elementary unidirectional (UD) ply.
As a result, finding the design allowable, i.e., the ply strengths while accounting for material scattering as indicated in the aviation standards [4], is a major problem for the designers. Because a significant number of tests are required, determining the design allowable is a time-consuming and costly operation. Fast and simple identification tests and analysis procedures are required to save cost and product lead-time.
Furthermore, presenting identification tests with low coefficients of variation (CV) will raise the A- and B-basis allowable, resulting in greater performance designs. The MIL-HDBK [4] specifies statistical figures for the A and B-basis design allowable. With a 95% level of confidence, the A (resp. B-basis) value indicates that 99 percent (resp. 90 percent) of the population values are predicted to be equal to or greater than this number.
The determination of the ply longitudinal compressive strength, one of the in-plane strengths of a unidirectional ply, is now a technological and scientific problem. Bre kinking, which has been widely researched experimentally and numerically in the literature [510], is the failure mechanism seen for specimens subjected to longitudinal compressive pressure.
Because various aspects including as alignment, specimen shape, load introduction scheme, stress concentration, buckling stability, and specimen end-crushing are extremely sensitive to this failure mechanism, compressive testing should be given considerable consideration. Some standards, like as the EN2850 AECMA standard, which is based on a uniaxial compressive test on unidirectional 0° laminates, are used to determine the longitudinal compressive strength associated with the onset of severe kinking.
This type of test, however, is difficult to conduct in order to achieve reliable and repeatable results. Indeed, while designing compressive testing on 0° laminates, two main issues must be carefully considered:
I the application of the imposed loading; and (ii) the specimen geometry. Many standards for testing procedures and xtures can be available in the literature. The compressive force can be conveyed into the specimen through shear at wedge grip contacts, as proposed by and later refined in the ASTM D3410/D3410M-16 standard.
The use of tabbed specimens as well as intricate and hefty xtures is required for this experimental equipment. Alternatively, the EN2850 AECMA standard suggests end loading to pass the compressive force into the specimen, obviating the need for extra tabs. This approach, which conforms to the ASTM D695-15 standard, is currently the most widely employed in the aerospace industry.
Finally, the ASTM D6641/D6641M standard transmits the compressive force by combining shear loading and end-loading. Despite the fact that this approach produces higher compressive strength, it is rarely employed because it is difficult to manage the relative contributions of shear loading and end-loading. In terms of specimen shape and design, specimens are typically thin to replicate the production process of most common aircraft panels while also reducing the amount of material required and hence the cost.
To avoid premature failure owing to specimen buckling, the gauge length is kept short (10 mm, as specified by the EN2850 AECMA standard). Due of local stress concentrations, failure usually occurs at the machine jaws with this specimen geometry. The dispersion on the observed longitudinal compressive strength can be as high as ten percent.
As a result, the corresponding design allowed is significantly lower than the average measured strength, penalizing composite solutions in comparison to their metallic counterparts.
Lee and Soutis investigated the effect of specimen size on the measured axial compressive strength of CFRP materials loadings to overcome this constraint. The longitudinal tensile strength is substantially lower.
Q9) Explain Transverse tensile strength.
A9)
Reinforcing fibers are usually much stronger than the bulk material because they have fewer defects. However, the fibers are only effective uniaxially and not in transverse directions. The strength and stiffness of a composite depends on the orientation of the reinforcing fibers. Both the longitudinal and transverse modulus of elasticity influences the total stiffness of a composite.
The transverse modulus of elasticity is
I/Et = (1-vf)/Em+ vf/Ef
This equation indicates that the fibers do not greatly contribute to the stiffness in transverse directions unless their volume fraction is high. Both the longitudinal and transverse modulus of elasticity assumes that the stresses are equal in the fibers and matrix. While thermal and moisture expansion are also factors that affect stiffness, they do not contribute greatly in this application.
The strength of the composite takes into account the longitudinal and transverse tensile and compressive strengths. The longitudinal tensile strength is the only property controlled predominantly by the fiber strength. The longitudinal compressive strength is usually lower than the tensile strength by a factor of one-half or greater. The transverse tensile strength is mostly controlled by the matrix strength, defect concentration within the matrix, and the adhesion between the matrix and the fibers.
Failure caused by buckling is governed by the shear properties of the composite as well as fiber misalignment. The misalignment is especially due to the curing process; the fibers become misoriented when the polymer component shrinks between 3 to 9% of its volume. Depending on the processing, there may be fewer defects present in the matrix of a composite than in the bulk matrix material. However, the fibers may add stress concentrations. The same factors are considered in predicting the transverse compressive strength, and because of the complex nature of these factors, the strengths cannot be calculated to a great degree of accuracy.
A composite laminate can be made up of several prepreg layers with varying fiber orientation. The main advantage of these laminates is the ability to compensate for weakness in the transverse directions.
The ‘indirect’ transverse tensile strengths, σA, of several 52% Vf uniaxially aligned glass fibre/polyester pultrusions were measured using the diametral compression of disc-shaped samples between concave loading anvils. In the vicinity of the disc centre there is an axial compressive stress, −3σA; thus, the test, when performed at atmospheric pressure, is biaxial. In an attempt to identify the failure criterion, triaxial test was carried out by superimposing hydrostatic pressure, −H, which yielded the principal stresses σ1 = σA + H σ2 = H σ3 = −3σA + H For the cases where there was no interaction between the pressurizing medium and the composite, the linear pressure dependence of σA was c. −0·1 H, i.e., for −H > 30 MPa, extensile failure from the fibre/resin interfaces took place when all the principal stresses, though unequal, were compressive. This rules out maximum tensile stress as a transverse tensile (interfacial) failure criterion; the results, however, were consistent with that of a critical tensile strain. Using this criterion, the (simple) transverse tensile strengths were estimated to lie in the range 59–101 MPa. For the cases of environmental attack by the pressurizing medium (a synthetic diester), the relevant criterion appeared to be that of maximum deviatoric stress, and on this hypothesis the (atmospheric) strengths of the glass fibre/polyester interfaces were estimated to lie in the range 47–57 MPa.
Q10) Explain Transverse compressive strength.
A10)
The transverse compressive stress, , is given as follows:

It depicts the hybrid rods' typical transverse compressive stress-displacement (TC-U) curves.
The transverse compressive strength, TCi, is defined as the transverse compressive stress at which these tangent lines intersect. Table 1 shows a summary of the findings. The hybrid rods' transverse compressive strengths, TCi, were 15.26 (24K1P), 8.79 (24K2P), and 8.05 MPa (24K3P), respectively. Figure 4 depicts the link between transverse compressive strength and volume percent of carbon fibre, VCF, as determined by earlier research [11, 12]. By raising VCF, the tensile strength improved but the TCi decreased.
For the cutting operation, the hybrid rods were first wrapped in sticky tape. A rotary cutting machine set to 2500 rpm was used to cut the hybrid rods into 6.0 mm lengths. The non-ferrous metal abrasive cutting wheel (GC150NB, Heiwa Technica Co., Ltd.) was utilized. To explore the deformation behaviour and strain fluctuations of micro-scale on hybrid rods, a high-precision polishing surface is required. Although the embedding moulding method for polishing metal materials has been carried out using a resin as a conventional polishing technique, the pre-existing polishing method cannot be applied to the hybrid rods due to their sensitivity to damages caused by heat and solution conditions. To study the transverse compression behaviours under the rod's original settings, a new polishing tool was designed that can be directly polished without causing fabrication damage. A novel polishing tool [14] for the auto-rotary polishing machine was used to polish the cross section of the hybrid rods. Under steady pressure and the same polishing circumstances, the tool can polish a large number of rods at the same time with a well-right angle.
Q11) What do you understand by Inplane shear failure.
A11)
This mechanism can cause the reinforced wall to fail by rupturing the FRP under tension or crushing the brickwork. Compressive crushing is most common in masonry walls reinforced with high reinforcement ratios. Because masonry crushing is a more ductile failure mode, FRP rupture is less desirable (Triantafillou, 1998).
Sliding shear failure and diagonal cracking are two types of in-plane shear failure. Due to their brittle nature, these failure modes occur for minimal levels of FRP reinforcement and should be avoided with careful design.
Q12) What Thermal effects are faced by wind turbines?
A12)
Wind turbine blade composites may be exposed to low temperatures (-20C or below) or high temperatures (50C or above) over the course of their 5-to-30-year operational life. Some tough polymers may become more brittle and their modulus may increase when exposed to low temperatures.
Many tests have been carried out in recent years to examine the behaviour of composite materials to higher temperatures. The effect of temperature on the fiber-matrix interface has been observed to be as powerful as the effects of fibre treatment and resin characteristics. At high temperatures, other mechanical parameters like as compression strength, ultimate tensile strength, and [45] tensile strength (which is matrix dominated) have been reported to decline.
Maro studied the influence of temperature on the fracture characteristics of composites extensively. Interlaminar fracture energy fell 25-30% when the temperature increased from – 50 to 100C, according to the study. With increasing temperature, noticeable changes in the quantities of fiber/matrix separation and resin-matrix fracture were detected in the interlaminar fracture surface features of graphite/epoxy.
The temperature effect on the mechanical properties of composites derives partly from the internal stresses introduced by the differential thermal coefficients of composite components. Internal stresses alter in amplitude as temperature changes, causing matrix cracking in some situations at very low temperatures. Each polymer has its unique working temperature range in practical applications. A polymer's maximum use temperature is usually just below its glass transition temperature (Tg), at which point it transitions from hard to rubbery and loses a lot of mechanical properties. Elevated temperatures combined with humid environments have been found to exacerbate the problem by further reducing Tg, among other factors.
Q13) How Moisture affects the mechanical properties of composites?
A13)
The mechanical properties of composites can be influenced by water molecules diffusing into the network. Water increases the mode I fracture toughness in the short term, but the toughness deteriorates in the long run, according to Marom. Shen and Springer found that the ultimate tensile strength and elastic moduli of 90-degree laminates declined as moisture content increased. The reduction might be as much as 50-90 percent. Moisture impairs the fiber-matrix interfacial bonding, lowers the glass transition temperature, swells, plasticizes, hydrolyzes, and sometimes microcracks the matrix when it diffuses into composites [3,13]. To forecast long-term behaviour, it is required to be able to forecast water diffusion and its effects on resin properties.
The method of water diffusion is described by Fick's law, and the intake of moisture is commonly quantified by weight gain. Shen and Springer examined water absorption and desorption in composite materials in 1975, based on Fick's law, and gave formulas for moisture distribution and moisture content as a function of time for one-dimensional composite materials. The analytical solution is backed up by a slew of experimental evidence, and this expression is commonly used to characterize water diffusion behaviour in composites.
However, the water absorption behaviour of some composites deviates significantly from the Fickian model. Because of the complexities of absorption behaviour and the variability of experimental data, such a non-Fickian process has remained a mystery. To analyze the diffusivity and moisture profiles over the thickness of laminates, some methodologies and computational algorithms are described that attempt to eliminate non-Fickian moisture content data.
Q14) How Stress and strain distribution at fibres occur.
A14)
Composite material stress-strain analysis the longitudinal modulus E11 of a unidirectional continuous-fiber laminate loaded in a direction parallel to its fibres can be determined from its constituent properties using the well-known rule of mixtures:
E11 = E1V1+EmVm
Where Ef is the fiber modulus, Vf is the fiber volume percentage, Em is the matrix modulus and Vm is the matrix volume percentage [17]. We treat the composite material as acting in a purely elastic manner and neglect the viscoelastic effects of the matrix; Hooke’s Law then can be applied:
σ1= E1 ε1
σm =Em ε m
Therefore, the longitudinal tensile strength σ11 also can be estimated by:
σ11 = σ1V1 + σmVm
The ultimate fibre and matrix strengths are f and m, respectively. Because fibre qualities dominate for all practical volume percentages, the matrix values can be discarded, and Eq. (6) is simplified:
σ11 ≈ σ1V1
Fiber-reinforced composites (FRC) are a form of composite material that can be classed as continuous or discontinuous, with continuous reinforcement providing the best strength. As shown in Eq. (7), the efficiency of FRC when utilized with continuous and aligned fibres oriented parallel to the load is 98 percent, but when fibres are randomly oriented throughout the 3-D area, the efficiency drops to 1/5 of its value.
Q15) Define Critical fibre length and average fibre stress.
A15)
Critical fibre length:
Since agrofibres have a specific strength and E-modulus similar to glass fibres, agrofibre composites have gotten a lot of attention in the recent decade. Thermoplastic polypropylene composites, in particular, are gaining popularity. When compared to the intrinsic fibre modulus, the specific stiffness of agrofibres can be employed successfully; however, an efficient use of the fibre strength in either melt-impregnated or injection moulded agrofibre composites is not expressed 2,3,4. Subcritical fibre lengths, especially in injection moulded agrofibre composites, could be to blame ", as well as a lack of fiber-matrix interaction. Despite the fact that various writers have investigated the impact of better fibre-matrix adhesion, nothing is known about the level of effective utilization of fibre strength “. However, because high fibre lengths limit the processability of such composites, proper use of fibre strength is a key criterion for good mechanical performance. As a result, the critical fibre length is a valuable metric for balancing mechanical characteristics and processability. Using single-fibre-fragmentation tests, the critical fibre length of both technical and elementary flax fibres in a polypropylene matrix is estimated in this work. A single flax plant cell is an elementary flax fibre (see figure 1). Furthermore, the apparent interfacial shear strength is calculated using these essential fibre lengths. Maleic anhydride modified polypropylene, which has been proven to improve the shear strength of interfaces of several agrofibre composites, is used to investigate the impact of increased fibre-matrix adhesion.
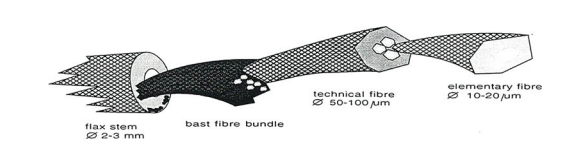
Average fibre stress
The stress transfer in single flax fibre polypropylene composites, both elementary and technical, is investigated by finding the critical fibre length and apparent interfacial shear strength. The impact of better fibre-matrix interaction is discussed, and the findings are compared to literature data. The crucial fibre length for elementary flax fibres, according to the study, is equal to or even higher than the flax fibre lengths found after extrusion and injection moulding methods. Furthermore, adding maleic anhydridy modified polypropylene to the matrix results in an apparent interfacial shear strength for elementary flax fibres that is close to the matrix's shear yield strength, but slightly lower for technical fibres.
Q16) Define Stiffness and strength of aligned systems.
A16)
Stiffness
Joint stiffness refers to pain and/or a reduction of range of motion in a joint. See stiff equation for the concept referring to the stability of a differential equation.
"Flexibility" is a misnomer. See also Flexibility (disambiguation) (disambiguation).
Extension of a coil spring, δ, caused by an axial force, F
The degree to which an object resists deformation in reaction to an applied force is known as stiffness.
Flexibility, or pliability, is a complimentary concept: the more flexible a thing is, the less stiff it is.
Strength
You can personalize the formulation to fulfil unique strength needs of every application by combining certain resins and reinforcements – and there are a lot of them. You can, for example, change the resin-to-reinforcement ratio or position the fibres in one or more orientations.
Composites are anisotropic, which means that the material properties fluctuate depending on how many layers of reinforcement materials – fibres – are used. This provides engineering freedom, allowing designers to customize the final product's attributes. There are four types of strength that influence structural design: specific, tensile, shear, and compressive strength.
Q17) Define Non-aligned systems and variable fibre orientation.
A17)
Variable fibre orientation
Injection-moulded short-glass fibre-reinforced polypropylene and polyamide, as well as long-glass fibre-reinforced polyamide, had inter-related process factors, fibre orientation distribution, and mechanical properties. The reinforced grades' attributes were also compared to those of the base polymer. A rectangular mould with triple pin-edge gates on the same side was used to allow a single melt flow-front or two flow-fronts to advance adjacently. Fiber orientation distribution, as well as tensile, dynamic mechanical, and fracture properties, were assessed in mouldings. The melt and mould temperatures, as well as the injection ram speed, influenced the respective magnitudes of the shell and core fibre-orientation persuasions. With fibre reinforcement, G c, K c, ultimate tensile strength (UTS), and elastic moduli values increased, but tan values decreased. Because of the accompanying differences in fibre orientation, the characteristics were highly sensitive to the position of the specimens in the moulding. The Halpin-Tsai equations for elastic moduli and a rule of mixture relationship for strength had limited success in predicting UTS. The accuracy of the predictions was increased by using measured data from high-fiber-orientation locations, such as the knit-line. In material systems with considerable production-induced voids, the estimation was weakened. The fracture toughness measurements suggested that the composites had flows of the order of 0.2 mm in diameter, which might have occurred either as voids or as defects introduced during specimen milling.
Non-aligned systems
Short-fiber (2–6 mm) mats and veils are routinely aligned using fluid or hydrodynamic alignment techniques in a range of industries. Fibers are usually suspended in a viscous liquid (such as glycerol), and alignment is achieved by forcing the fibres to follow the fluid streamlines by accelerating the carrier medium through a converging nozzle. Fiber alignment in injection moulded objects is frequently caused by flow induced alignment. High levels of alignment are possible, with the ability to align more than 90% of fibres in the 158 range. The degree of fibre alignment is a function of fibre length, with shorter fibres being easier to align in the fluid's shear flow. The tensile strength utilization of the fibres in moulded composites is claimed to be in the region of 70–80%, which compares favourably to the 80–90% efficiency cited for continuous fibre composites. In the late 1990s, aligned, discontinuous carbon fibre prepregs were successfully manufactured using a two-stage technique for 3 mm fibres. Carbon and thermoplastic fibres floating in a supporting liquid were forced through nozzles onto a slanted rail to begin alignment. Following that, the slurry was poured onto a revolving cylindrical mandrel where the final alignment took place. The claimed alignment is far superior than that of other traditional hydrodynamic approaches, with all fibres in the 48 percent Vf range.
Tensile stiffness and strength retentions are reported to be 94 and 80 percent, respectively, when compared to continuous fibres. Fibers must be thoroughly disseminated in the suspension and the fibre concentration must be very low (50.8 vol percent) to avoid obstructions in hydrodynamic processes. As a result, long cycle times are unavoidable, especially since the fibres must be dried before forming. As a result, the output of hydrodynamic processes is limited to roughly 4 kg/h [22].
Dry alignment of discontinuous fibres (2–6 mm) can be accomplished using an electric field [25–27] or pneumatic techniques [28]. Electric field methods require conductive fibres, which can be obtained with conductivity-enhancing coatings such acidic salts. The fibres are aligned in the direction of the electric filed lines using electrodes positioned beneath a moving belt. Previously, bindered glass strands were fired onto orientated plates at the end of fibre supply tubes using pneumatic means to align glass-mat reinforced thermoplastics (GMT). In general, electric field and pneumatic procedures allow for the faster fabrication of aligned preforms than wet methods, but the degree of alignment is poor when compared to hydrodynamic or long fibre alignment techniques. Fiber length has no effect on electri field alignment [26], but only around 70% of fibres are oriented between 208 and 308, and only 80–90% between 308 and 308. The possibility for alignment Short-fiber (2–6 mm) mats and veils are routinely aligned using fluid or hydrodynamic alignment techniques in a range of industries. Fibers are usually suspended in a viscous liquid (such as glycerol), and alignment is achieved by forcing the fibres to follow the fluid streamlines by accelerating the carrier medium through a converging nozzle. Fiber alignment in injection moulded objects is frequently caused by flow induced alignment. High levels of alignment are possible, with the ability to align more than 90% of fibres in the 158 range. The level of alignment is determined by fibre length, with shorter fibres being easier to align in the fluid's shear flow.
The tensile strength utilization of the fibres in moulded composites is claimed to be in the region of 70–80%, which compares favourably to the 80–90% efficiency cited for continuous fibre composites.
In the late 1990s, aligned, discontinuous carbon fibre prepregs were successfully manufactured using a two-stage technique for 3 mm fibres. Carbon and thermoplastic fibres were forced through nozzles onto a sloping rail to begin alignment. The slurry was then poured onto a revolving cylindrical mandrel, where it was finalized. With all fibres in the range of 48 at 50% Vf, the reported alignment is substantially better than other conventional hydrodynamic approaches.
Tensile stiffness and strength retentions are reported to be 94 and 80 percent, respectively, when compared to continuous fibres.
Fibers must be thoroughly disseminated in the suspension and the fibre concentration must be very low (50.8 vol percent) to avoid obstructions in hydrodynamic processes. As a result, long cycle times are unavoidable, especially since the fibres must be dried before forming. As a result, the output of hydrodynamic processes is limited to roughly 4 kg/h.
Dry alignment of discontinuous fibres (2–6 mm) can be accomplished by passing the fibres through an electric field or utilizing pneumatics. Electric field methods require conductive fibres, which can be obtained with conductivity-enhancing coatings such acidic salts. The fibres are aligned in the direction of the electric filed lines using electrodes positioned beneath a moving belt. Previously, bindered glass strands were fired onto orientated plates at the end of fibre supply tubes using pneumatic means to align glass-mat reinforced thermoplastics (GMT). In general, electric field and pneumatic procedures allow for the faster fabrication of aligned preforms than wet methods, but the degree of alignment is poor when compared to hydrodynamic or long fibre alignment techniques. Although fibre length has no effect on electric field alignment [26], only 70 percent of fibres are oriented between and only 80–90 percent between. The possibility for alignment Short-fiber (2–6 mm) mats and veils are routinely aligned using fluid or hydrodynamic alignment techniques in a range of industries. Fibers are usually suspended in a viscous liquid (such as glycerol), and alignment is achieved by forcing the fibres to follow the fluid streamlines by accelerating the carrier medium through a converging nozzle. Fiber alignment in injection moulded objects is frequently caused by flow induced alignment. High levels of alignment are possible, with the ability to align more than 90% of fibres in the 158 range. The level of alignment is determined by fibre length, with shorter fibres being easier to align in the fluid's shear flow.
The tensile strength utilization of the fibres in moulded composites is claimed to be in the region of 70–80%, which compares favourably to the 80–90% efficiency cited for continuous fibre composites.
In the late 1990s, aligned, discontinuous carbon fibre prepregs were successfully manufactured using a two-stage technique for 3 mm fibres. Carbon and thermoplastic fibres floating in a supporting liquid were forced through nozzles onto a slanted rail to begin alignment. The slurry was then poured onto a revolving cylindrical mandrel, where it was finalized. With all fibres in the range of 48 at 50% Vf, the reported alignment is substantially better than other conventional hydrodynamic approaches. Tensile stiffness and strength retentions are reported to be 94 and 80 percent, respectively, when compared to continuous fibres. Fibers must be thoroughly disseminated in the suspension and the fibre concentration must be very low (50.8 vol percent) to avoid obstructions in hydrodynamic processes. As a result, long cycle times are unavoidable, especially since the fibres must be dried before forming. As a result, the output of hydrodynamic processes is limited to roughly 4 kg/h.
Dry alignment of discontinuous fibres (2–6 mm) can be accomplished using an electric field [25–27] or pneumatic techniques. The use of electric field methods requires that the fibre be conductive, which can be achieved by coating it with conductivity-enhancing coatings such acidic salts. The fibres are aligned in the direction of the electric filed lines using electrodes positioned beneath a moving belt. Previously, bindered glass strands were fired onto orientated plates at the end of fibre supply tubes using pneumatic means to align glass-mat reinforced thermoplastics (GMT). Both electric field and pneumatic methods may produce aligned preforms at a faster rate than wet methods, but the degree of alignment is poor for these procedures.
When compared to hydrodynamic or long fibre alignment approaches, this method is more efficient. Electric field alignment is mainly unaffected by fibre length, although only around 70% of fibres are oriented between 208 and 308, and only 80–90% between 308. The possibility for alignment
The use of an ultrasonic device to align short fibres has also been reported in the literature [ 17]. Short fibres in different matrix media are aligned in the ultrasonic alignment (UA) technique in response to standing waves produced by two piezoelectric transducers placed on either side of the UA device. The fibres are aligned in their nodal point by standing waves. Low fibre volume percentage is one of the key disadvantages. Injection moulding is one of the most common methods for producing SFRPCs. Fibre alignment is usually caused by interactions between different layers of the mould.
Due to the friction exerted by the mould walls, the alignment of fibres follows the flow direction in the boundary areas of the mould. The friction diminishes as you get closer to the centre, when the fibre alignment is transverse to the flow direction. There's a probability that a shearing flow will form between the boundary and core regions, which will help to align the fibres in the core region [18].
Shear controlled orientation in injection moulding (SCORIM) is a modification that is mostly utilized in injection moulding to align small fibres along the flow direction [19]. A device installed between the mould chamber and nozzle of an injection moulding machine is used to create macroscopic shears in this experiment. This device consists of oscillating pistons that provide macroscopic shear to solidify melt inside the core portion of the mould, increasing fibre alignment in this area.
Researchers have employed a combination of injection moulding and compression moulding to create aligned SNPFPCs. Initially, injection moulding was utilized to create cylindrical rods of short fibres with polymer matrices. Finally, those rods were aligned in a leaking mould before being compressed to form aligned short fibre composites [20]. Printing or fused deposition modelling of aligned SFRPCs can be done via additive manufacturing or 3D printing of polymer composites [6, 21].
In this process, short fibre filaments with polymer matrices are extruded and fed into a 3D printer to manufacture (or print) aligned SFRPCs [22]. The maximum degree of fibre alignment recorded in the literature is +/- 3 ° (measured within the prepregs or composites produced) [2] using all of the aforementioned approaches. The HiPerDiF (67 percent of the fibres in this range) and rotating vacuum drum are the two methods that have shown this range of fibre alignment (60 percent of the fibres with in this range).
The alignment performance of the electric field and pneumatic methods is +/- 20 ° (70 percent of the fibres in this range) and +/- 52 ° (majority of the fibres in this range), respectively.
Q18) What if the components of a course are misaligned?
A18)
Assessments that aren't connected with learning objectives or instructional methodologies can have a negative impact on both student motivation and learning. Consider the following two possibilities:
Although your goal is for students to learn to use analytical skills, your exam solely assesses factual recollection. As a result, students sharpen their analytical skills and are disappointed that the exam does not assess what they have learnt.
Your test assesses students' abilities to compare and analyse the arguments of various authors, however your instructional tactics are solely focused on summarising the arguments of various authors. As a result, pupils do not learn or practise the comparison and evaluation abilities that will be evaluated.
Q19) What do well-aligned assessments look like?
A19)
This table presents examples of the kinds of activities that can be used to assess different types of learning objectives.
Type of learning objective | Examples of appropriate assessments |
Recall | Fill-in-the-blank, matching, labelling, and multiple-choice questions are examples of objective test items that require students to: Be able to recall or recognize phrases, facts, and ideas |
Interpret | Papers, exams, problem sets, class debates, and idea maps are examples of activities that require students to: o writes summaries of readings, movies, or speeches Two or more hypotheses, events, or processes are compared and contrasted o Use defined criteria to classify or categories cases, elements, or events o publications or remarks that have been paraphrased o seeks out or locate examples or instances of a subject or premise |
Apply | Activities that encourage students to: o employ techniques to solve or finish familiar or unfamiliar tasks, such as problem sets, performances, labs, prototyping, or simulations Determine which procedure(s) is/are best for a specific task |
Analyze | Case studies, critiques, labs, papers, projects, discussions, and idea maps are examples of activities that require students to: Distinguish or pick relevant and irrelevant portions to figure out how pieces interact Determine the material's prejudice, values, or underlying intent |
Evaluate | Journals, diaries, critiques, problem sets, product reviews, or studies in which students are required to: o test, monitor, judge, or critique readings, performances, or goods against predefined criteria or standards |
Create | Research projects, musical compositions, performances, essays, business plans, website designs, and set designs are all examples of activities that require students to: Create, construct, design, or create something new |
Q20) Give a brief Introduction of Polymer Composites.
A20)
Polymer composites are composite materials that are made up of more than two phases, and usually refer to polymer/polymer or filler (fibre, metal, etc.)-based polymer composites. Polymer composites were developed later than traditional materials such as ceramic and clay. Polymer composites have essential uses in a variety of disciplines, including electronics, food packaging, and medicine, among others. The demand for higher material performance is growing in tandem with the rapid advancement of science and technology. Traditional polymer materials based on a single component are unable to meet the growing demand for great overall performance. Polymers, for example, have a melting temperature range of 100–250°C, indicating that they are not appropriate for use at high temperatures. As a result, the notion of integrating additives into the polymer matrix was developed, which might significantly increase the polymer's performance. Wakabayashi et al. Found that adding graphite (2.5 wt percent, 1870 MPa) to the pristine PP matrix (910 MPa) improved Young's modulus significantly. Based on the advances gained in many application domains, this conceptual innovation of incorporating inorganic materials/metals into polymer matrix has sparked a lot of interest in the scientific community.
Polymer composites have improved properties in a variety of applications as compared to neat polymers. By incorporating even a little amount of additives into the polymer matrix, a large number of studies have shown significant improvements in mechanical characteristics, electrical conductivity, thermal conductivity, corrosion resistance and wear resistance. These characteristics make them commercially viable in a variety of fields, including heat conduction and dissipation devices, resist-memory devices, energy storage, and so on. Traditional macroscale fillers, such as metals and minerals, have been widely used in a variety of applications. However, due to the restricted interfacial structure between them and the matrix, these additives are unable to significantly improve the characteristics. Because of their huge surface areas and good contact with the polymers, lowering the size of fillers to microscale and nanoscale should be one of the key methods for further improving the performance of composites. In 1984, Roy and Komarneni established the concept of polymer nanocomposite, which was defined as composite materials including at least one dispersed phase having a diameter of less than 100 nm, such as carbon nanotubes (CNTs), fullerenes, nanosized particles, and so on. These materials are ideal for blending with polymers to create polymer nanocomposites. Actually, the first report on polymer nanocomposites dates from the mid-nineteenth century, when carbon black was mixed with vulcanized rubber for use in vehicle tyres. Polymer nanocomposites, by combining different polymers or macro-scale materials into a single polymer, have improved mechanical, optical, and electrical properties. Meanwhile, as the size of traditional fillers shrank to the nanoscale, such as nano-SiO2 and nano-CaCO3, they demonstrated improved dispersion into polymer and a much higher property improvement effect than macro-scale particles. As a result, just a tiny amount of nanomaterials is required for the qualities, lowering the cost of fillers and avoiding many of the adverse effects associated with large filler content.
Two-dimensional (2D) materials are a novel form of sheet-like nanomaterial with lateral sizes ranging from hundreds of nanometers to a few micrometres and an average thickness of less than 5 nanometers. These materials have a big surface area and a high percentage of atoms exposed to the surface, which allows them to interact well with the matrix, and even a small amount of them can significantly improve polymer performance. Furthermore, their diverse species make them appropriate fillers for a variety of applications. It has been reported that adding a modest amount (1–5% wt%) of 2D materials to a polymer matrix, such as layered silicates or graphene, increased the mechanical properties of the resulting polymer composites by up to 200 percent compared to neat polymers. Grapheme, graphene oxide (GO), hexagonal boron nitride (h-BN), transitional metal dichalcogenides (TMDCs), metal organic frameworks (MOFs), and other 2D materials have been produced and employed in polymer composites thus far. The focus of this review will be on recent advancements in the manufacturing of 2D materials-based polymer composites. Their use in terms of energy storage will also be examined.
Preparation of exfoliated 2D materials and their dispersion into the polymer matrix is a typical procedure for making 2D materials-based polymer composites. The exfoliation technique is used to weaken or break the links between layers in order to prepare 2D materials. Intercalation expands interlayer space, causing slippage between layers when a shear force is applied. Intercalation-aided exfoliation, liquid phase exfoliation, etching assisted exfoliation, ball milling, electrochemical exfoliation, ion exchange-assisted exfoliation, and other methods have been used to exfoliate multilayer materials. After the 2D materials have been exfoliated, the next step is to ensure that they are evenly dispersed throughout the polymer matrix. Dissolving the polymer in solvents and then immersing the 2D materials in the dissolved polymer solution is a popular procedure. The difficult fabrication process, however, makes the final goods expensive, and the organic solvents are dangerous and toxic, which are two major barriers to the scale usage of 2D materials-based polymer composites. Further refining of the fabrication process is required to lower costs while also reducing pollutants. As a result, for the real-world use of 2D materials-based polymer composites, a study of the present status of the field and the most up-to-date strategies for overcoming the hurdles is critical. The preparation methods for various 2D materials-based polymer composites will be discussed in the next section. Then, different types of 2D materials-based polymer composites (graphene, h-BN, MoS2, and MOF) will be summarized in terms of property enhancement. The third section will summaries the uses of 2D materials/polymer composites for lithium ion batteries and supercapacitors. Finally, the difficulty of exfoliating and preparing polymer nanocomposites will be explored, as well as the future prospects for improving polymer composite performance.
Graphene-, GO-Based Polymer Composites
The history of graphene may be traced back to 2004, when Novoselov et al. Used a scotch tape transferring approach to generate few-layered graphene’s and evaluated their good electrical performance. This seminal breakthrough paved the way for basic graphene research and commercialization. Carbon atoms are tightly packed into a 2D honeycomb lattice structure in graphene thanks to sp2 hybridization. High carrier mobility at room temperature (10,000 cm2 V1 s1), high Young's modulus (1 TPa), large theoretical specific surface area (2630 m2 g1), low light absorption (2.3 percent), and high thermal conductivity (5000 Wm1 K1) are just a few of the physical and chemical properties of such a structure. Graphene is an essential derivative of graphene, which is made by oxidising graphite with powerful oxidants. Various oxygen-containing functional groups, including as carboxyl, hydroxyl, epoxy groups, and others, are introduced on the surface of grapheme during the oxidation process. Graphene and GO have completely different characteristics while having a similar 2D structure. Because the intense oxidation process transforms C–C bonds from sp2 to sp3 hybridization, GO has significantly lower electrical conductivity than graphene. Because of the enormous amount of hydrophilic oxygen-containing groups on the surface, graphene is insoluble in water and GO has good dispersity in water. As a result, graphene and GO serve different purposes in polymer composites. Prior to the development of graphene and GO, carbon nanotubes (CNTs) were widely used as fillers in polymer composites. The high cost of producing CNTs, as well as their aggregation, were hurdles in their use in polymer composites. Graphene and GO mass production are now well-understood, and their costs are also reasonable for commercial applications. As a result, they're thought to be good fillers for polymer composites in place of carbon nanotubes. It is critical to make the filler effectively disseminated in the polymer matrix and interact firmly with it in order to improve the properties of the polymer composites. Solution mixing, ball milling, in situ polymerization, and other procedures for the preparation of graphene and GO-based polymer nanocomposites have all been well established so far. The mechanism and principles of these procedures will be discussed in detail in the next subsections, as well as increased attributes derived from experimental data.