UNIT 1
Engineering Materials
1. Explain the Cement and their uses? Also describe the properties of cement?
CEMENT
Cement is a binder, a substance that sets and hardens and can bind other materials together. Cements used in construction can be characterized as being either hydraulic or non-hydraulic, depending upon the ability of the cement to be used in the presence of water. Non-hydraulic cement will not set in wet conditions or underwater, rather it sets as it dries and reacts with carbon dioxide in the air. It can be attacked by some aggressive chemicals after setting. Hydraulic cement is made by replacing some of the cement in a mix with activated aluminium silicates, pozzolanas, such as fly ash. The chemical reaction results in hydrates that are not very water-soluble and so are quite durable in water and safe from chemical attack. This allows setting in wet condition or underwater and further protects the hardened material from chemical attack (e.g., Portland cement).
- USE OF CEMENT
- Cement mortar for Masonry work, plaster and pointing etc.
- Concrete for laying floors, roofs and constructing lintels, beams, weather shed, stairs, pillars etc.
- Construction for important engineering structures such as bridge, culverts, dams, tunnels, light house, clocks, etc.
- Construction of water ,wells, tennis courts, septic tanks, lamp posts, telephone cabins etc.
- Making joint for joints, pipes , etc.
- Manufacturing of precast pipes, garden seats, artistically designed wens, flower posts, etc.
- Preparation of foundation, water tight floors, footpaths, etc.
- ENGINEERING PROPERTIES OF CEMENT
Fineness
- This test is carried out to check proper grinding of cement. The fineness of cement particles may be determined either by sieve test or permeability apparatus test.
- In sieve test, the cement weighing 100 gm is taken and it is continuously passed for 15 minutes through standard BIS sieve no. 9.The residue is then weighed and this weight should not be more than 10% of original weight.
- In permeability apparatus test, specific area of cement particles is calculated. This test is better than sieve test. The specific surface acts as a measure of the frequency of particles of average size.
Compressive strength
- This test is carried out to determine the compressive strength of cement.
- The mortar of cement and sand is prepared in ratio 1:3.
- Water is added to mortar in water cement ratio 0.4.
- The mortar is placed in moulds. The test specimens are in the form of cubes and the moulds are of metals. For 70.6 mm and 76 mm cubes ,the cement required is 185gm and 235 gm respectively.
- Then the mortar is compacted in vibrating machine for 2 minutes and the moulds are placed in a damp cabin for 24 hours.
- The specimens are removed from the moulds and they are submerged in clean water for curing.
- The cubes are then tested in compression testing machine at the end of 3days and 7 days. Thus compressive strength was found out.
Consistency
- The purpose of this test is to determine the percentage of water required for preparing cement pastes for other tests.
- Take 300 gm of cement and add 30 percent by weight or 90 gm of water to it.
- Mix water and cement thoroughly.
- Fill the mould of Vicat apparatus and the gauging time should be 3.75 to 4.25 minutes.
- Vicat apparatus consists of a needle is attached a movable rod with an indicator attached to it.
- There are three attachments: square needle, plunger and needle with annular collar.
- The plunger is attached to the movable rod.the plunger is gently lowered on the paste in the mould.
- The settlement of plunger is noted. If the penetration is between 5 mm to 7 mm from the bottom of mould, the water added is correct. If not process is repeated with different percentages of water till the desired penetration is obtained.
Setting time
- This test is used to detect the deterioration of cement due to storage. The test is performed to find out initial setting time and final setting time.
- Cement mixed with water and cement paste is filled in the Vicat mould.
- Square needle is attached to moving rod of vicat apparatus.
- The needle is quickly released and it is allowed to penetrate the cement paste. In the beginning the needle penetrates completely. The procedure is repeated at regular intervals till the needle does not penetrate completely. (up to 5mm from bottom)
- Initial setting time equal to or less than 30min for ordinary Portland cement and 60 min for low heat cement.
- The cement paste is prepared as above and it is filled in the Vicat mould.
- The needle with annular collar is attached to the moving rod of the Vicat apparatus.
- The needle is gently released. The time at which the needle makes an impression on test block and the collar fails to do so is noted.
- Final setting time is the difference between the time at which water was added to cement and time as recorded in previous step ,and it is equal to or less than 10hours.
Soundness
- The purpose of this test is to detect the presence of un combined lime in the cement.
- The cement paste is prepared.
- The mould is placed and it is filled by cement paste.
- It is covered at top by another glass plate.A small weight is placed at top and the whole assembly is submerged in water for 24 hours.
- The distance between the points of indicator is noted. The mould is again placed in water and heat is applied in such a way that boiling point of water is reached in about 30 minutes. The boiling of water is continued for one hour.
- The mould is removed from water and it is allowed to cool down.
- The distance between the points of indicator is again measured. The difference between the two readings indicates the expansion of cement and it should not exceed 10 mm.
Tensile strength
- This test was formerly used to have an indirect indication of compressive strength of cement.
- The mortar of sand and cement is prepared.
- The water is added to the mortar.
- The mortar is placed in briquette moulds. The mould is filled with mortar and then a small heap of mortar is formed at its top . It is beaten down by a standard spatula till water appears on the surface. Same procedure is repeated for the other face of briquette.
- The briquettes are kept in a damp for 24 hours and carefully removed from the moulds.
- The briquettes are tested in a testing machine at the end of 3 and 7 days and average is found out
2. Explain the mortar and their uses? Also describe the properties of mortar?
MORTAR
Mortar is a bonding agent which is generally produced by mixing cementing or binding material (lime or cement) and fine aggregate (sand, surki, sawdust, etc.) with water. Mortar is used to bind different building blocks like bricks, stones, etc. It can also add a decorative pattern in brick or stone masonry.
Mortar, a bonding agent between building materials, is mainly a mixture of water, fine aggregate (sand, surki, etc) and binding material like cement, lime etc. The applications of mortar in various construction phase have made it a very important civil engineering material.
- USES OF MORTAR
- Mortar is used to bind together the bricks or stones in brick or stone masonry.
- It is used to give a soft even bed between different layers of brick or stone masonry for equal distribution of pressure over the bed.
- It is used to fill up the spaces between bricks or stones for making walls tight.
- It is used in concrete as a matrix.
- It is used in plastering works to hide the joints and to improve appearance.
- It is used for molding and ornamental purpose.
ENGINEERING PROPERTIES OF MORTAR
Cement: It should be fresh and free from adulteration. To know more about the properties of good cement read >> Properties of Good Cement
Lime: Lime must be well slaked.
Sand: Sand should be sharp, angular and porous. It should be free from salts and other impurities. Read>> Function of Sand in Mortar
Surki: Surki should be perfectly pure and free from foreign matter. It should be sufficiently fine to pass through the desired sieve
Mud: Mud should be free from adulteration.
Water: Water should be clean and free from salts and other impurities.
3. What are the uses of STEEL?
USES OF STEELS
Some vital utilization of steels is given below:
- Steel is environment-friendly & sustainable. It posses great durability.
- Compared to other materials, steel requires a low amount of energy to produce lightweight steel construction.
- Steel is the world’s most recycled material which can be recycled very easily. Its unique magnetic properties make it an easy material to recover from stream to be recycled.
- Steel can be designed into various forms. It gives better shape and edge than iron which is used to make weapons.
- Engineering steels are used for general engineering and manufacturing sectors.
- Steel is highly used in the automobile industry. Different types of steels are used in a car body, doors, engine, suspension, and interior. The average 50% of a car is made of steel.
- Steel reduces CO2 emissions.
- All types of energy sectors demand steel for infrastructure and resource extraction.
- Stainless steels are used to produce offshore platforms and pipelines.
- Steels are used for packaging and protecting goods from water, air and light exposure.
- Most of the household appliances like fridge, TV, oven, sinks, etc are made of steel.
- Steels are used for producing industrial goodies like farm vehicles and machines.
- Stainless steel is used as a cutlery material.
- Because of its easily welding capability and attractive finishing, steel has become a prominent feature in modern architecture.
- Stainless steel gives a hygienic environment. That’s why it is used for surgical implants.
- Steel has a wider range of temperature which is used to make large sheets.
- Renewable energy resources like solar, hydro and wind power use the stainless steel components.
- Mild steel is used for building construction. It is also a highly favored building frame material.
4. Explain the properties of steel?
- ENGINEERING PROPERTIES OF STEEL
- Tensile strength
The stress-strain curve for the steel is generally obtained by conducting tensile test on any standard steel specimen. Tensile strength of the steel can be defined in terms of yield strength and ultimate strength.
b. Hardness
Hardness is regarded as the resistance of any material to identification and scratching. This is generally determined by forcing an indenter on to the surface. The resultant deformation steel is both elastic and plastic. The different methods to find out the hardness of metal which includes Brinell hardness test, Vicker’s hardness test, and Rockwell hardness test.
c. Toughness
There is the possibility of microscopic cracks in a material or the material may develop such cracks as a result of several cycles of loading. These cracks may result in sudden collapse of the structure and it is very dangerous. Therefore to ensure that this should not happen, materials in which the cracks grow slowly are preferred. These types of steel are known as notch-tough steels and the amount of energy it absorb is measure by impacting the notch specimen.
d. Fatigue strength
A component of structure, which is designed to carry a single monotonically static load, may fail if the same load is applied cyclically a large number of times. If the example of a thin rod is considered, it bent back and forth beyond yielding fails after few cycles of such repeated bending. This type of failure is termed as fatigue failure. Examples: bridges, cranes, offshore structure, slender tower, etc.
e. Corrosion resistance
Corrosion is the procedure in which oxidation of a metal in a normal atmospheric condition owing to the excessive presence of moisture and oxygen in the air. Corrosion of the metal is a very natural and rapid phenomenon in the areas of high humidity and places closer to saline water. Therefore the efforts to be made to control the corrosion by using galvanize and epoxy coated reinforcement bars but failed in practical usage due to the risk of disbanding, causing accelerated corrosion. Corrosion resistance elements such as copper, phosphorus and chromium are added in appropriate measure to the metal which results in corrosion resistance steel
5. Explain the Brick varieties and strength and also tests on bricks?
BRICKS
Constituents of good brick earth: Bricks are the most commonly used construction material. Bricks are prepared by moulding clay in rectangular blocks of uniform size and then drying and burning these blocks. In order to get a good quality brick, the brick earth should contain the following constituents.
- Silica
- Alumina
- Lime
- Iron oxide
- Magnesia
Brick plays very important role in the field of civil engineering construction. Bricks are used as an alternative of stones in construction purpose.
USES OF BRICKS
- Construction of walls of any size
- Construction of floors
- Construction of arches and cornices
- Construction of brick retaining wall
- Making Khoa (Broken bricks of required size) to use as an aggregate in concrete
- Manufacture of surki (powdered bricks) to be used in lime plaster and lime concrete
CLASSIFICATION OF BRICKS AS PER CONSTITUENT MATERIALS
There are various types of bricks used in masonry
- Common Burnt Clay Bricks
- Sand Lime Bricks (Calcium Silicate Bricks)
- Engineering Bricks
- Concrete Bricks
- Fly ash Clay Bricks
Common Burnt Clay Bricks
Common burnt clay bricks are formed by pressing in moulds. Then these bricks are dried and fired in a kiln. Common burnt clay bricks are used in general work with no special attractive appearances. When these bricks are used in walls, they require plastering or rendering.
Sand Lime Bricks
Sand lime bricks are made by mixing sand, fly ash and lime followed by a chemical process during wet mixing. The mix is then moulded under pressure forming the brick. These bricks can offer advantages over clay bricks such as: their colour appearance is grey instead of the regular reddish colour. Their shape is uniform and presents a smoother finish that doesn’t require plastering. These bricks offer excellent strength as a load-bearing member.
Engineering Bricks
Engineering bricks are bricks manufactured at extremely high temperatures, forming a dense and strong brick, allowing the brick to limit strength and water absorption. Engineering bricks offer excellent load bearing capacity damp-proof characteristics and chemical resisting properties. Concrete Bricks Concrete bricks are made from solid concrete. Concrete bricks are usually placed in facades, fences, and provide an excellent aesthetic presence. These bricks can be manufactured to provide different colours as pigmented during its production.
Fly Ash Clay Bricks
Fly ash clay bricks are manufactured with clay and fly ash, at about 1,000 degrees C. Some studies have shown that these bricks tend to fail poor produce pop-outs, when bricks come into contact with moisture and water, causing the bricks to expand.
6. Explain the ENGINEERING PROPERTIES OF BRICKS?
To know the quality of bricks following 7 tests can be performed. In these tests some are performed in laboratory and the rest are on field.
- Compressive strength test
- Water Absorption test
- Efflorescence test
- Hardness test
- Size, Shape and Colour test
- Soundness test
TESTS ON BRICKS
Structure test Compressive strength test
This test is done to know the compressive strength of brick. It is also called crushing strength of brick. Generally 5 specimens of bricks are taken to laboratory for testing and tested one by one. In this test a brick specimen is put on crushing machine and applied pressure till it breaks. The ultimate pressure at which brick is crushed is taken into account. All five brick specimens are tested one by one and average result is taken as brick’s compressive/crushing strength.
Water Absorption test In this test bricks are weighed in dry condition and let them immersed in fresh water for 24 hours. After 24 hours of immersion those are taken out from water and wipe out with cloth. Then brick is weighed in wet condition. The difference between weights is the water absorbed by brick. The percentage of water absorption is then calculated. The less water absorbed by brick the greater its quality. Good quality brick doesn’t absorb more than 20% water of its own weight.
Efflorescence test The presence of alkalies in bricks is harmful and they form a grey or white layer on brick surface by absorbing moisture. To find out the presence of alkalis in bricks this test is performed. In this test a brick is immersed in fresh water for 24 hours and then it’s taken out from water and allowed to dry in shade. If the whitish layer is not visible on surface it proofs that absence of alkalis in brick. If the whitish layer visible about 10% of brick surface then the presence of alkalis is inacceptable range. If that is about 50% of surface then it is moderate. If the alkalies’ presence is over 50% then the brick is severely affected by alkalies.
Hardness test
In this test a scratch is made on brick surface with a hard thing. If that doesn’t left any impression on brick then that is good quality brick.
Size, shape and colour test
In this test randomly collected 20 bricks are staked along lengthwise, width wise and height wise and then those are measured to know the variation of sizes as per standard. Bricks are closely viewed to check if its edges are sharp and straight and uniform in shape. A good quality brick should have bright and uniform colour throughout.
Soundness test
In this test two bricks are held by both hands and struck with one another. If the bricks give clear metallic ringing sound and don’t break then those are good quality bricks.
Structure test In this test a brick is broken or a broken brick is collected and closely observed. If there are any flows, cracks or holes present on that broken face then that isn’t good quality brick.
7. What are Aggregates? Also explain types & requirements?
AGGREGATES
Aggregate is an aggregation of non-metallic minerals obtained in particulate form and can be processed and used for civil and highway engineering construction.
Aggregates are mainly classified into two categories:
- Fine Aggregate
- Coarse Aggregate
ENGINEERING PROPERTIES OF AGGREGATES
Aggregates are used in concrete to provide economy in the cost of concrete. Aggregates act as filler only. These do not react with cement and water. But there are properties or characteristics of aggregate which influence the properties of resulting concrete mix. These are as follow.
- Composition
- Size & Shape
- Surface Texture
- Specific Gravity
- Bulk Density
- Voids
- Porosity & Absorption
- Bulking of Sand
- Fineness Modulus of Aggregate
- Surface Index of Aggregate
- Deleterious Material
- Crushing Value of Aggregate
- Impact Value of Aggregate
- Abrasion Value of Aggregate
1. COMPOSITION
Aggregates consisting of materials that can react with alkalies in cement and cause excessive expansion, cracking and deterioration of concrete mix should never be used. Therefore it is required to test aggregates to know whether there is presence of any such constituents in aggregate or not.
2. SIZE & SHAPE
The size and shape of the aggregate particles greatly influence the quantity of cement required in concrete mix and hence ultimately economy of concrete. For the preparation of economical concrete mix on should use largest coarse aggregates feasible for the structure. IS-456 suggests following recommendation to decide the maximum size of coarse aggregate to be used in P.C.C & R.C.C mix.
Maximum size of aggregate should be less than
- One-fourth of the minimum dimension of the concrete member.
- One-fifth of the minimum dimension of the reinforced concrete member.
- The minimum clear spacing between reinforced bars or 5 mm less than the minimum cover between the reinforced bars and form, whichever is smaller for heavily reinforced concrete members such as the ribs of the main bars.
3. SURFACE TEXTURE
The development of hard bond strength between aggregate particles and cement paste depends upon the surface texture, surface roughness and surface porosity of the aggregate particles.If the surface is rough but porous, maximum bond strength develops. In porous surface aggregates, the bond strength increases due to setting of cement paste in the pores.
4. SPECIFIC GRAVITY
The ratio of weight of oven dried aggregates maintained for 24 hours at a temperature of 100 to 1100C, to the weight of equal volume of water displaced by saturated dry surface aggregate is known as specific gravity of aggregates.
5. BULK DENSITY
It is defined as the weight of the aggregate required to fill a container of unit volume. It is generally expressed in kg/litre.
Bulk density of aggregates depends upon the following 3 factors.
- Degree of compaction
- Grading of aggregates
- Shape of aggregate particles
6. VOIDS
The empty spaces between the aggregate particles are known as voids. The volume of void equals the difference between the gross volume of the aggregate mass and the volume occupied by the particles alone.
7. POROSITY & ABSORPTION
The minute holes formed in rocks during solidification of the molten magma, due to air bubbles, are known as pores. Rocks containing pores are called porous rocks. Water absorption may be defined as the difference between the weight of very dry aggregates and the weight of the saturated aggregates with surface dry conditions.
Depending upon the amount of moisture content in aggregates, it can exist in any of the 4 conditions.
- Very dry aggregate ( having no moisture)
- Dry aggregate (contain some moisture in its pores)
- Saturated surface dry aggregate (pores completely filled with moisture but no moisture on surface)
- Moist or wet aggregates (pores are filled with moisture and also having moisture on surface)
8. BULKING OF SAND
It can be defined as in increase in the bulk volume of the quantity of sand (i.e. fine aggregate) in a moist condition over the volume of the same quantity of dry or completely saturated sand. The ratio of the volume of moist sand due to the volume of sand when dry, is called bulking factor.
9. FINENESS MODULUS
Fineness modulus is an empirical factor obtained by adding the cumulative percentages of aggregate retained on each of the standard sieves ranging from 80 mm to 150 micron and dividing this sum by 100.
Fineness modulus is generally used to get an idea of how coarse or fine the aggregate is. More fineness modulus value indicates that the aggregate is coarser and small value of fineness modulus indicates that the aggregate is finer.
10. SPECIFIC SURFACE OF AGGREGATE
The surface area per unit weight of the material is termed as specific surface. This is an indirect measure of the aggregate grading. Specific surface increases with the reduction in the size of aggregate particle. The specific surface area of the fine aggregate is very much more than that of coarse aggregate.
11. DELETERIOUS MATERIALS
Aggregates should not contain any harmful material in such a quantity so as to affect the strength and durability of the concrete. Such harmful materials are called deleterious materials. Deleterious materials may cause one of the following effects
- To interfere hydration of cement
- To prevent development of proper bond
- To reduce strength and durability
- To modify setting times
12. CRUSHING VALUE
The aggregates crushing value gives a relative measure of resistance of an aggregate to crushing under gradually applied compressive load. The aggregate crushing strength value is a useful factor to know the behavior of aggregates when subjected to compressive loads.
13. IMPACT VALUE
The aggregate impact value gives a relative measure of the resistance of an aggregate to sudden shock or impact. The impact value of an aggregate is sometime used as an alternative to its crushing value.
14. ABRASION VALUE OF AGGREGATES
The abrasion value gives a relative measure of resistance of an aggregate to wear when it is rotated in a cylinder along with some abrasive charge.
8. Explain Workability, Strength properties of Concrete?
•Concrete is an artificial conglomerate stone made essentially of Portland cement, water, and aggregates.
•Portland cement is produced by mixing ground limestone, clay or shale, sand and iron ore.
•This mixture is heated in a rotary kiln to temperatures as high as 1 600 degrees Celsius high as 1,600 degrees Celsius. The heating process causes the materials to break down and recombine into new compounds that can react with water in a crystallization process called hydration.
•The raw ingredients of Portland cement are iron ore, lime, alumina and silica. These are ground up and fired in a kiln to produce a clinker. After cooling, the clinker is very finery ground.
•When first mixed the water and cement constitute a paste which surrounds all the individual pieces of aggregate to make a plastic mixture.
•A chemical reaction called hydration takes place between the water and cement, and concrete normally changes from a plastic to a solid state in about 2 hours.
•Concrete continues to gain strength as it cures. Heat of hydration - is the heat given off during the chemical reaction as the cement hydrates.
Workability that property of freshly mixed concrete that determines its working characteristics, i.e. the ease with which it can be mixed, placed, compacted and finished.
Factors effecting workability:
•Method and duration of transportation
•Quantity and characteristics of cementing materials
•Concrete consistency (slump)
•Aggregate grading, shape & surface texture
•% entrained air
•Water content
•Concrete & ambient air temperature Admixtures
9. Explain Nominal Proportion Of Concrete Preparation Of Concrete, Compaction and Curing?
Nominal Proportion of Concrete Preparation Of Concrete
Concrete is a commonly used construction material, which is the mixture of cement, sand, aggregate, and admixtures blended with water. Concrete gets hardened with time and gains the strength, and for the best results in a construction of your dream home, mixing of concrete is said to be the most important process. All the ingredients are to be mixed in proper proportion because the properties of concrete like workability, strength, surface finish, and durability of concrete etc. are ensured by the right and proportionate blending.
In the nominal mix concrete, all the ingredients and their proportions are prescribed in the standard specifications. These proportions are specified in the ratio of cement to aggregates for certain strength achievement.
The mix proportions like 1:1.5:3, 1:2:4, 1:3:6 etc. are adopted in nominal mix of concrete without any scientific base, only on the basis on past empirical studies. Thus, it is adopted for ordinary concrete or you can say, the nominal mix is preferred for simpler, relatively unimportant and small concrete works.
As per the ‘Indian Standard- IS 456:2000’, nominal mix concrete may be used for concrete of M20 grade or lower grade such as M5, M7.5, M10, M15.
M 20 is identified as the concrete grade in which, M denotes the Mix and 20 denotes the compressive strength of concrete cube after 28 days of curing in N/mm2. There are various grades of concrete that can be used like M10, M15, M20, M25, M30, etc.
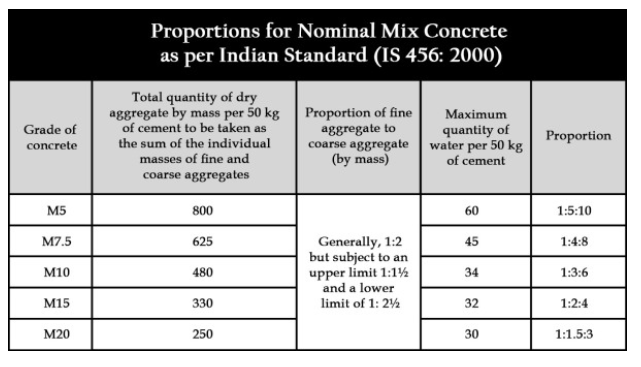
10. Explain Compaction and Curing ?
Compaction of concrete and curing process of concrete
1) Compaction of concrete
•Concrete should be thoroughly compacted and fully work around the reinforcement and into the corners of the formworks
•Concrete shall be compacted using mechanical vibrators
•Whenever vibration has been applied externally the design of formwork and the deposition of vibrators should receive special consideration to ensure efficient compaction and to avoid sir face blemishes
2) Curing process of concrete
•Curing of concrete is defined as the process of maintaining the moisture and temperature condition of concrete for hydration reaction to the normally so that the concrete develops hardened and properties over time
•The main components which need to be taken care of your heat and time during curing process
•Curing is the process of preventing the loss of moisture from the concrete which maintaining a satisfactory temperature effect
•If the cement has high rate of strain development and if the concrete contains granulated blast furnace and flue Ash then,
•The curing should also prevent the development of high temperature gradients within the concrete
a) Moist curing
•Surface of the concrete shall be kept continuously in Dam or wet condition by covering with the layers of materials like checking Canvas etc.
•it should be kept continuously wet for at least 7 days from the date of placing concrete.
•In case of ordinary Portland cement at least 10 days. Where mineral admixture or blended cement are used.
•The period of curing shall not be less than 10 days for concrete exposed to the dry and hot weather condition.
•In case of concrete where mineral admixture or blended cement are used it is recommended that above minimum period may be extended 14 days.
b) Membrane curing
•Approved curing compounds may be used in place of moist curing with the permission of engineer in charge.
•Search compound shall be applied to all exposed surfaces of the concrete as soon as possible after the concrete has set.
•Impermeable membrane such as polyethylene sheeting covering closely the concrete surface may also be used to provide effective barriers against evaporation.
•For the concrete containing Portland pozzolana cement, Portland slag cement or mineral admixture period of curing may be increased
UNIT 1
Engineering Materials
1. Explain the Cement and their uses? Also describe the properties of cement?
CEMENT
Cement is a binder, a substance that sets and hardens and can bind other materials together. Cements used in construction can be characterized as being either hydraulic or non-hydraulic, depending upon the ability of the cement to be used in the presence of water. Non-hydraulic cement will not set in wet conditions or underwater, rather it sets as it dries and reacts with carbon dioxide in the air. It can be attacked by some aggressive chemicals after setting. Hydraulic cement is made by replacing some of the cement in a mix with activated aluminium silicates, pozzolanas, such as fly ash. The chemical reaction results in hydrates that are not very water-soluble and so are quite durable in water and safe from chemical attack. This allows setting in wet condition or underwater and further protects the hardened material from chemical attack (e.g., Portland cement).
- USE OF CEMENT
- Cement mortar for Masonry work, plaster and pointing etc.
- Concrete for laying floors, roofs and constructing lintels, beams, weather shed, stairs, pillars etc.
- Construction for important engineering structures such as bridge, culverts, dams, tunnels, light house, clocks, etc.
- Construction of water ,wells, tennis courts, septic tanks, lamp posts, telephone cabins etc.
- Making joint for joints, pipes , etc.
- Manufacturing of precast pipes, garden seats, artistically designed wens, flower posts, etc.
- Preparation of foundation, water tight floors, footpaths, etc.
- ENGINEERING PROPERTIES OF CEMENT
Fineness
- This test is carried out to check proper grinding of cement. The fineness of cement particles may be determined either by sieve test or permeability apparatus test.
- In sieve test, the cement weighing 100 gm is taken and it is continuously passed for 15 minutes through standard BIS sieve no. 9.The residue is then weighed and this weight should not be more than 10% of original weight.
- In permeability apparatus test, specific area of cement particles is calculated. This test is better than sieve test. The specific surface acts as a measure of the frequency of particles of average size.
Compressive strength
- This test is carried out to determine the compressive strength of cement.
- The mortar of cement and sand is prepared in ratio 1:3.
- Water is added to mortar in water cement ratio 0.4.
- The mortar is placed in moulds. The test specimens are in the form of cubes and the moulds are of metals. For 70.6 mm and 76 mm cubes ,the cement required is 185gm and 235 gm respectively.
- Then the mortar is compacted in vibrating machine for 2 minutes and the moulds are placed in a damp cabin for 24 hours.
- The specimens are removed from the moulds and they are submerged in clean water for curing.
- The cubes are then tested in compression testing machine at the end of 3days and 7 days. Thus compressive strength was found out.
Consistency
- The purpose of this test is to determine the percentage of water required for preparing cement pastes for other tests.
- Take 300 gm of cement and add 30 percent by weight or 90 gm of water to it.
- Mix water and cement thoroughly.
- Fill the mould of Vicat apparatus and the gauging time should be 3.75 to 4.25 minutes.
- Vicat apparatus consists of a needle is attached a movable rod with an indicator attached to it.
- There are three attachments: square needle, plunger and needle with annular collar.
- The plunger is attached to the movable rod.the plunger is gently lowered on the paste in the mould.
- The settlement of plunger is noted. If the penetration is between 5 mm to 7 mm from the bottom of mould, the water added is correct. If not process is repeated with different percentages of water till the desired penetration is obtained.
Setting time
- This test is used to detect the deterioration of cement due to storage. The test is performed to find out initial setting time and final setting time.
- Cement mixed with water and cement paste is filled in the Vicat mould.
- Square needle is attached to moving rod of vicat apparatus.
- The needle is quickly released and it is allowed to penetrate the cement paste. In the beginning the needle penetrates completely. The procedure is repeated at regular intervals till the needle does not penetrate completely. (up to 5mm from bottom)
- Initial setting time equal to or less than 30min for ordinary Portland cement and 60 min for low heat cement.
- The cement paste is prepared as above and it is filled in the Vicat mould.
- The needle with annular collar is attached to the moving rod of the Vicat apparatus.
- The needle is gently released. The time at which the needle makes an impression on test block and the collar fails to do so is noted.
- Final setting time is the difference between the time at which water was added to cement and time as recorded in previous step ,and it is equal to or less than 10hours.
Soundness
- The purpose of this test is to detect the presence of un combined lime in the cement.
- The cement paste is prepared.
- The mould is placed and it is filled by cement paste.
- It is covered at top by another glass plate.A small weight is placed at top and the whole assembly is submerged in water for 24 hours.
- The distance between the points of indicator is noted. The mould is again placed in water and heat is applied in such a way that boiling point of water is reached in about 30 minutes. The boiling of water is continued for one hour.
- The mould is removed from water and it is allowed to cool down.
- The distance between the points of indicator is again measured. The difference between the two readings indicates the expansion of cement and it should not exceed 10 mm.
Tensile strength
- This test was formerly used to have an indirect indication of compressive strength of cement.
- The mortar of sand and cement is prepared.
- The water is added to the mortar.
- The mortar is placed in briquette moulds. The mould is filled with mortar and then a small heap of mortar is formed at its top . It is beaten down by a standard spatula till water appears on the surface. Same procedure is repeated for the other face of briquette.
- The briquettes are kept in a damp for 24 hours and carefully removed from the moulds.
- The briquettes are tested in a testing machine at the end of 3 and 7 days and average is found out
2. Explain the mortar and their uses? Also describe the properties of mortar?
MORTAR
Mortar is a bonding agent which is generally produced by mixing cementing or binding material (lime or cement) and fine aggregate (sand, surki, sawdust, etc.) with water. Mortar is used to bind different building blocks like bricks, stones, etc. It can also add a decorative pattern in brick or stone masonry.
Mortar, a bonding agent between building materials, is mainly a mixture of water, fine aggregate (sand, surki, etc) and binding material like cement, lime etc. The applications of mortar in various construction phase have made it a very important civil engineering material.
- USES OF MORTAR
- Mortar is used to bind together the bricks or stones in brick or stone masonry.
- It is used to give a soft even bed between different layers of brick or stone masonry for equal distribution of pressure over the bed.
- It is used to fill up the spaces between bricks or stones for making walls tight.
- It is used in concrete as a matrix.
- It is used in plastering works to hide the joints and to improve appearance.
- It is used for molding and ornamental purpose.
ENGINEERING PROPERTIES OF MORTAR
Cement: It should be fresh and free from adulteration. To know more about the properties of good cement read >> Properties of Good Cement
Lime: Lime must be well slaked.
Sand: Sand should be sharp, angular and porous. It should be free from salts and other impurities. Read>> Function of Sand in Mortar
Surki: Surki should be perfectly pure and free from foreign matter. It should be sufficiently fine to pass through the desired sieve
Mud: Mud should be free from adulteration.
Water: Water should be clean and free from salts and other impurities.
3. What are the uses of STEEL?
USES OF STEELS
Some vital utilization of steels is given below:
- Steel is environment-friendly & sustainable. It posses great durability.
- Compared to other materials, steel requires a low amount of energy to produce lightweight steel construction.
- Steel is the world’s most recycled material which can be recycled very easily. Its unique magnetic properties make it an easy material to recover from stream to be recycled.
- Steel can be designed into various forms. It gives better shape and edge than iron which is used to make weapons.
- Engineering steels are used for general engineering and manufacturing sectors.
- Steel is highly used in the automobile industry. Different types of steels are used in a car body, doors, engine, suspension, and interior. The average 50% of a car is made of steel.
- Steel reduces CO2 emissions.
- All types of energy sectors demand steel for infrastructure and resource extraction.
- Stainless steels are used to produce offshore platforms and pipelines.
- Steels are used for packaging and protecting goods from water, air and light exposure.
- Most of the household appliances like fridge, TV, oven, sinks, etc are made of steel.
- Steels are used for producing industrial goodies like farm vehicles and machines.
- Stainless steel is used as a cutlery material.
- Because of its easily welding capability and attractive finishing, steel has become a prominent feature in modern architecture.
- Stainless steel gives a hygienic environment. That’s why it is used for surgical implants.
- Steel has a wider range of temperature which is used to make large sheets.
- Renewable energy resources like solar, hydro and wind power use the stainless steel components.
- Mild steel is used for building construction. It is also a highly favored building frame material.
4. Explain the properties of steel?
- ENGINEERING PROPERTIES OF STEEL
- Tensile strength
The stress-strain curve for the steel is generally obtained by conducting tensile test on any standard steel specimen. Tensile strength of the steel can be defined in terms of yield strength and ultimate strength.
b. Hardness
Hardness is regarded as the resistance of any material to identification and scratching. This is generally determined by forcing an indenter on to the surface. The resultant deformation steel is both elastic and plastic. The different methods to find out the hardness of metal which includes Brinell hardness test, Vicker’s hardness test, and Rockwell hardness test.
c. Toughness
There is the possibility of microscopic cracks in a material or the material may develop such cracks as a result of several cycles of loading. These cracks may result in sudden collapse of the structure and it is very dangerous. Therefore to ensure that this should not happen, materials in which the cracks grow slowly are preferred. These types of steel are known as notch-tough steels and the amount of energy it absorb is measure by impacting the notch specimen.
d. Fatigue strength
A component of structure, which is designed to carry a single monotonically static load, may fail if the same load is applied cyclically a large number of times. If the example of a thin rod is considered, it bent back and forth beyond yielding fails after few cycles of such repeated bending. This type of failure is termed as fatigue failure. Examples: bridges, cranes, offshore structure, slender tower, etc.
e. Corrosion resistance
Corrosion is the procedure in which oxidation of a metal in a normal atmospheric condition owing to the excessive presence of moisture and oxygen in the air. Corrosion of the metal is a very natural and rapid phenomenon in the areas of high humidity and places closer to saline water. Therefore the efforts to be made to control the corrosion by using galvanize and epoxy coated reinforcement bars but failed in practical usage due to the risk of disbanding, causing accelerated corrosion. Corrosion resistance elements such as copper, phosphorus and chromium are added in appropriate measure to the metal which results in corrosion resistance steel
5. Explain the Brick varieties and strength and also tests on bricks?
BRICKS
Constituents of good brick earth: Bricks are the most commonly used construction material. Bricks are prepared by moulding clay in rectangular blocks of uniform size and then drying and burning these blocks. In order to get a good quality brick, the brick earth should contain the following constituents.
- Silica
- Alumina
- Lime
- Iron oxide
- Magnesia
Brick plays very important role in the field of civil engineering construction. Bricks are used as an alternative of stones in construction purpose.
USES OF BRICKS
- Construction of walls of any size
- Construction of floors
- Construction of arches and cornices
- Construction of brick retaining wall
- Making Khoa (Broken bricks of required size) to use as an aggregate in concrete
- Manufacture of surki (powdered bricks) to be used in lime plaster and lime concrete
CLASSIFICATION OF BRICKS AS PER CONSTITUENT MATERIALS
There are various types of bricks used in masonry
- Common Burnt Clay Bricks
- Sand Lime Bricks (Calcium Silicate Bricks)
- Engineering Bricks
- Concrete Bricks
- Fly ash Clay Bricks
Common Burnt Clay Bricks
Common burnt clay bricks are formed by pressing in moulds. Then these bricks are dried and fired in a kiln. Common burnt clay bricks are used in general work with no special attractive appearances. When these bricks are used in walls, they require plastering or rendering.
Sand Lime Bricks
Sand lime bricks are made by mixing sand, fly ash and lime followed by a chemical process during wet mixing. The mix is then moulded under pressure forming the brick. These bricks can offer advantages over clay bricks such as: their colour appearance is grey instead of the regular reddish colour. Their shape is uniform and presents a smoother finish that doesn’t require plastering. These bricks offer excellent strength as a load-bearing member.
Engineering Bricks
Engineering bricks are bricks manufactured at extremely high temperatures, forming a dense and strong brick, allowing the brick to limit strength and water absorption. Engineering bricks offer excellent load bearing capacity damp-proof characteristics and chemical resisting properties. Concrete Bricks Concrete bricks are made from solid concrete. Concrete bricks are usually placed in facades, fences, and provide an excellent aesthetic presence. These bricks can be manufactured to provide different colours as pigmented during its production.
Fly Ash Clay Bricks
Fly ash clay bricks are manufactured with clay and fly ash, at about 1,000 degrees C. Some studies have shown that these bricks tend to fail poor produce pop-outs, when bricks come into contact with moisture and water, causing the bricks to expand.
6. Explain the ENGINEERING PROPERTIES OF BRICKS?
To know the quality of bricks following 7 tests can be performed. In these tests some are performed in laboratory and the rest are on field.
- Compressive strength test
- Water Absorption test
- Efflorescence test
- Hardness test
- Size, Shape and Colour test
- Soundness test
TESTS ON BRICKS
Structure test Compressive strength test
This test is done to know the compressive strength of brick. It is also called crushing strength of brick. Generally 5 specimens of bricks are taken to laboratory for testing and tested one by one. In this test a brick specimen is put on crushing machine and applied pressure till it breaks. The ultimate pressure at which brick is crushed is taken into account. All five brick specimens are tested one by one and average result is taken as brick’s compressive/crushing strength.
Water Absorption test In this test bricks are weighed in dry condition and let them immersed in fresh water for 24 hours. After 24 hours of immersion those are taken out from water and wipe out with cloth. Then brick is weighed in wet condition. The difference between weights is the water absorbed by brick. The percentage of water absorption is then calculated. The less water absorbed by brick the greater its quality. Good quality brick doesn’t absorb more than 20% water of its own weight.
Efflorescence test The presence of alkalies in bricks is harmful and they form a grey or white layer on brick surface by absorbing moisture. To find out the presence of alkalis in bricks this test is performed. In this test a brick is immersed in fresh water for 24 hours and then it’s taken out from water and allowed to dry in shade. If the whitish layer is not visible on surface it proofs that absence of alkalis in brick. If the whitish layer visible about 10% of brick surface then the presence of alkalis is inacceptable range. If that is about 50% of surface then it is moderate. If the alkalies’ presence is over 50% then the brick is severely affected by alkalies.
Hardness test
In this test a scratch is made on brick surface with a hard thing. If that doesn’t left any impression on brick then that is good quality brick.
Size, shape and colour test
In this test randomly collected 20 bricks are staked along lengthwise, width wise and height wise and then those are measured to know the variation of sizes as per standard. Bricks are closely viewed to check if its edges are sharp and straight and uniform in shape. A good quality brick should have bright and uniform colour throughout.
Soundness test
In this test two bricks are held by both hands and struck with one another. If the bricks give clear metallic ringing sound and don’t break then those are good quality bricks.
Structure test In this test a brick is broken or a broken brick is collected and closely observed. If there are any flows, cracks or holes present on that broken face then that isn’t good quality brick.
7. What are Aggregates? Also explain types & requirements?
AGGREGATES
Aggregate is an aggregation of non-metallic minerals obtained in particulate form and can be processed and used for civil and highway engineering construction.
Aggregates are mainly classified into two categories:
- Fine Aggregate
- Coarse Aggregate
ENGINEERING PROPERTIES OF AGGREGATES
Aggregates are used in concrete to provide economy in the cost of concrete. Aggregates act as filler only. These do not react with cement and water. But there are properties or characteristics of aggregate which influence the properties of resulting concrete mix. These are as follow.
- Composition
- Size & Shape
- Surface Texture
- Specific Gravity
- Bulk Density
- Voids
- Porosity & Absorption
- Bulking of Sand
- Fineness Modulus of Aggregate
- Surface Index of Aggregate
- Deleterious Material
- Crushing Value of Aggregate
- Impact Value of Aggregate
- Abrasion Value of Aggregate
1. COMPOSITION
Aggregates consisting of materials that can react with alkalies in cement and cause excessive expansion, cracking and deterioration of concrete mix should never be used. Therefore it is required to test aggregates to know whether there is presence of any such constituents in aggregate or not.
2. SIZE & SHAPE
The size and shape of the aggregate particles greatly influence the quantity of cement required in concrete mix and hence ultimately economy of concrete. For the preparation of economical concrete mix on should use largest coarse aggregates feasible for the structure. IS-456 suggests following recommendation to decide the maximum size of coarse aggregate to be used in P.C.C & R.C.C mix.
Maximum size of aggregate should be less than
- One-fourth of the minimum dimension of the concrete member.
- One-fifth of the minimum dimension of the reinforced concrete member.
- The minimum clear spacing between reinforced bars or 5 mm less than the minimum cover between the reinforced bars and form, whichever is smaller for heavily reinforced concrete members such as the ribs of the main bars.
3. SURFACE TEXTURE
The development of hard bond strength between aggregate particles and cement paste depends upon the surface texture, surface roughness and surface porosity of the aggregate particles.If the surface is rough but porous, maximum bond strength develops. In porous surface aggregates, the bond strength increases due to setting of cement paste in the pores.
4. SPECIFIC GRAVITY
The ratio of weight of oven dried aggregates maintained for 24 hours at a temperature of 100 to 1100C, to the weight of equal volume of water displaced by saturated dry surface aggregate is known as specific gravity of aggregates.
5. BULK DENSITY
It is defined as the weight of the aggregate required to fill a container of unit volume. It is generally expressed in kg/litre.
Bulk density of aggregates depends upon the following 3 factors.
- Degree of compaction
- Grading of aggregates
- Shape of aggregate particles
6. VOIDS
The empty spaces between the aggregate particles are known as voids. The volume of void equals the difference between the gross volume of the aggregate mass and the volume occupied by the particles alone.
7. POROSITY & ABSORPTION
The minute holes formed in rocks during solidification of the molten magma, due to air bubbles, are known as pores. Rocks containing pores are called porous rocks. Water absorption may be defined as the difference between the weight of very dry aggregates and the weight of the saturated aggregates with surface dry conditions.
Depending upon the amount of moisture content in aggregates, it can exist in any of the 4 conditions.
- Very dry aggregate ( having no moisture)
- Dry aggregate (contain some moisture in its pores)
- Saturated surface dry aggregate (pores completely filled with moisture but no moisture on surface)
- Moist or wet aggregates (pores are filled with moisture and also having moisture on surface)
8. BULKING OF SAND
It can be defined as in increase in the bulk volume of the quantity of sand (i.e. fine aggregate) in a moist condition over the volume of the same quantity of dry or completely saturated sand. The ratio of the volume of moist sand due to the volume of sand when dry, is called bulking factor.
9. FINENESS MODULUS
Fineness modulus is an empirical factor obtained by adding the cumulative percentages of aggregate retained on each of the standard sieves ranging from 80 mm to 150 micron and dividing this sum by 100.
Fineness modulus is generally used to get an idea of how coarse or fine the aggregate is. More fineness modulus value indicates that the aggregate is coarser and small value of fineness modulus indicates that the aggregate is finer.
10. SPECIFIC SURFACE OF AGGREGATE
The surface area per unit weight of the material is termed as specific surface. This is an indirect measure of the aggregate grading. Specific surface increases with the reduction in the size of aggregate particle. The specific surface area of the fine aggregate is very much more than that of coarse aggregate.
11. DELETERIOUS MATERIALS
Aggregates should not contain any harmful material in such a quantity so as to affect the strength and durability of the concrete. Such harmful materials are called deleterious materials. Deleterious materials may cause one of the following effects
- To interfere hydration of cement
- To prevent development of proper bond
- To reduce strength and durability
- To modify setting times
12. CRUSHING VALUE
The aggregates crushing value gives a relative measure of resistance of an aggregate to crushing under gradually applied compressive load. The aggregate crushing strength value is a useful factor to know the behavior of aggregates when subjected to compressive loads.
13. IMPACT VALUE
The aggregate impact value gives a relative measure of the resistance of an aggregate to sudden shock or impact. The impact value of an aggregate is sometime used as an alternative to its crushing value.
14. ABRASION VALUE OF AGGREGATES
The abrasion value gives a relative measure of resistance of an aggregate to wear when it is rotated in a cylinder along with some abrasive charge.
8. Explain Workability, Strength properties of Concrete?
•Concrete is an artificial conglomerate stone made essentially of Portland cement, water, and aggregates.
•Portland cement is produced by mixing ground limestone, clay or shale, sand and iron ore.
•This mixture is heated in a rotary kiln to temperatures as high as 1 600 degrees Celsius high as 1,600 degrees Celsius. The heating process causes the materials to break down and recombine into new compounds that can react with water in a crystallization process called hydration.
•The raw ingredients of Portland cement are iron ore, lime, alumina and silica. These are ground up and fired in a kiln to produce a clinker. After cooling, the clinker is very finery ground.
•When first mixed the water and cement constitute a paste which surrounds all the individual pieces of aggregate to make a plastic mixture.
•A chemical reaction called hydration takes place between the water and cement, and concrete normally changes from a plastic to a solid state in about 2 hours.
•Concrete continues to gain strength as it cures. Heat of hydration - is the heat given off during the chemical reaction as the cement hydrates.
Workability that property of freshly mixed concrete that determines its working characteristics, i.e. the ease with which it can be mixed, placed, compacted and finished.
Factors effecting workability:
•Method and duration of transportation
•Quantity and characteristics of cementing materials
•Concrete consistency (slump)
•Aggregate grading, shape & surface texture
•% entrained air
•Water content
•Concrete & ambient air temperature Admixtures
9. Explain Nominal Proportion Of Concrete Preparation Of Concrete, Compaction and Curing?
Nominal Proportion of Concrete Preparation Of Concrete
Concrete is a commonly used construction material, which is the mixture of cement, sand, aggregate, and admixtures blended with water. Concrete gets hardened with time and gains the strength, and for the best results in a construction of your dream home, mixing of concrete is said to be the most important process. All the ingredients are to be mixed in proper proportion because the properties of concrete like workability, strength, surface finish, and durability of concrete etc. are ensured by the right and proportionate blending.
In the nominal mix concrete, all the ingredients and their proportions are prescribed in the standard specifications. These proportions are specified in the ratio of cement to aggregates for certain strength achievement.
The mix proportions like 1:1.5:3, 1:2:4, 1:3:6 etc. are adopted in nominal mix of concrete without any scientific base, only on the basis on past empirical studies. Thus, it is adopted for ordinary concrete or you can say, the nominal mix is preferred for simpler, relatively unimportant and small concrete works.
As per the ‘Indian Standard- IS 456:2000’, nominal mix concrete may be used for concrete of M20 grade or lower grade such as M5, M7.5, M10, M15.
M 20 is identified as the concrete grade in which, M denotes the Mix and 20 denotes the compressive strength of concrete cube after 28 days of curing in N/mm2. There are various grades of concrete that can be used like M10, M15, M20, M25, M30, etc.
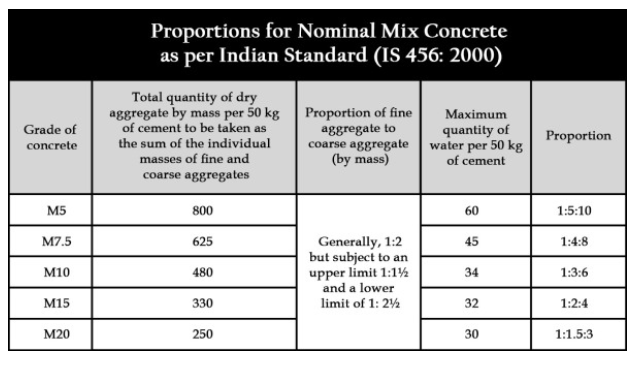
10. Explain Compaction and Curing ?
Compaction of concrete and curing process of concrete
1) Compaction of concrete
•Concrete should be thoroughly compacted and fully work around the reinforcement and into the corners of the formworks
•Concrete shall be compacted using mechanical vibrators
•Whenever vibration has been applied externally the design of formwork and the deposition of vibrators should receive special consideration to ensure efficient compaction and to avoid sir face blemishes
2) Curing process of concrete
•Curing of concrete is defined as the process of maintaining the moisture and temperature condition of concrete for hydration reaction to the normally so that the concrete develops hardened and properties over time
•The main components which need to be taken care of your heat and time during curing process
•Curing is the process of preventing the loss of moisture from the concrete which maintaining a satisfactory temperature effect
•If the cement has high rate of strain development and if the concrete contains granulated blast furnace and flue Ash then,
•The curing should also prevent the development of high temperature gradients within the concrete
a) Moist curing
•Surface of the concrete shall be kept continuously in Dam or wet condition by covering with the layers of materials like checking Canvas etc.
•it should be kept continuously wet for at least 7 days from the date of placing concrete.
•In case of ordinary Portland cement at least 10 days. Where mineral admixture or blended cement are used.
•The period of curing shall not be less than 10 days for concrete exposed to the dry and hot weather condition.
•In case of concrete where mineral admixture or blended cement are used it is recommended that above minimum period may be extended 14 days.
b) Membrane curing
•Approved curing compounds may be used in place of moist curing with the permission of engineer in charge.
•Search compound shall be applied to all exposed surfaces of the concrete as soon as possible after the concrete has set.
•Impermeable membrane such as polyethylene sheeting covering closely the concrete surface may also be used to provide effective barriers against evaporation.
•For the concrete containing Portland pozzolana cement, Portland slag cement or mineral admixture period of curing may be increased
UNIT 1
Engineering Materials
1. Explain the Cement and their uses? Also describe the properties of cement?
CEMENT
Cement is a binder, a substance that sets and hardens and can bind other materials together. Cements used in construction can be characterized as being either hydraulic or non-hydraulic, depending upon the ability of the cement to be used in the presence of water. Non-hydraulic cement will not set in wet conditions or underwater, rather it sets as it dries and reacts with carbon dioxide in the air. It can be attacked by some aggressive chemicals after setting. Hydraulic cement is made by replacing some of the cement in a mix with activated aluminium silicates, pozzolanas, such as fly ash. The chemical reaction results in hydrates that are not very water-soluble and so are quite durable in water and safe from chemical attack. This allows setting in wet condition or underwater and further protects the hardened material from chemical attack (e.g., Portland cement).
- USE OF CEMENT
- Cement mortar for Masonry work, plaster and pointing etc.
- Concrete for laying floors, roofs and constructing lintels, beams, weather shed, stairs, pillars etc.
- Construction for important engineering structures such as bridge, culverts, dams, tunnels, light house, clocks, etc.
- Construction of water ,wells, tennis courts, septic tanks, lamp posts, telephone cabins etc.
- Making joint for joints, pipes , etc.
- Manufacturing of precast pipes, garden seats, artistically designed wens, flower posts, etc.
- Preparation of foundation, water tight floors, footpaths, etc.
- ENGINEERING PROPERTIES OF CEMENT
Fineness
- This test is carried out to check proper grinding of cement. The fineness of cement particles may be determined either by sieve test or permeability apparatus test.
- In sieve test, the cement weighing 100 gm is taken and it is continuously passed for 15 minutes through standard BIS sieve no. 9.The residue is then weighed and this weight should not be more than 10% of original weight.
- In permeability apparatus test, specific area of cement particles is calculated. This test is better than sieve test. The specific surface acts as a measure of the frequency of particles of average size.
Compressive strength
- This test is carried out to determine the compressive strength of cement.
- The mortar of cement and sand is prepared in ratio 1:3.
- Water is added to mortar in water cement ratio 0.4.
- The mortar is placed in moulds. The test specimens are in the form of cubes and the moulds are of metals. For 70.6 mm and 76 mm cubes ,the cement required is 185gm and 235 gm respectively.
- Then the mortar is compacted in vibrating machine for 2 minutes and the moulds are placed in a damp cabin for 24 hours.
- The specimens are removed from the moulds and they are submerged in clean water for curing.
- The cubes are then tested in compression testing machine at the end of 3days and 7 days. Thus compressive strength was found out.
Consistency
- The purpose of this test is to determine the percentage of water required for preparing cement pastes for other tests.
- Take 300 gm of cement and add 30 percent by weight or 90 gm of water to it.
- Mix water and cement thoroughly.
- Fill the mould of Vicat apparatus and the gauging time should be 3.75 to 4.25 minutes.
- Vicat apparatus consists of a needle is attached a movable rod with an indicator attached to it.
- There are three attachments: square needle, plunger and needle with annular collar.
- The plunger is attached to the movable rod.the plunger is gently lowered on the paste in the mould.
- The settlement of plunger is noted. If the penetration is between 5 mm to 7 mm from the bottom of mould, the water added is correct. If not process is repeated with different percentages of water till the desired penetration is obtained.
Setting time
- This test is used to detect the deterioration of cement due to storage. The test is performed to find out initial setting time and final setting time.
- Cement mixed with water and cement paste is filled in the Vicat mould.
- Square needle is attached to moving rod of vicat apparatus.
- The needle is quickly released and it is allowed to penetrate the cement paste. In the beginning the needle penetrates completely. The procedure is repeated at regular intervals till the needle does not penetrate completely. (up to 5mm from bottom)
- Initial setting time equal to or less than 30min for ordinary Portland cement and 60 min for low heat cement.
- The cement paste is prepared as above and it is filled in the Vicat mould.
- The needle with annular collar is attached to the moving rod of the Vicat apparatus.
- The needle is gently released. The time at which the needle makes an impression on test block and the collar fails to do so is noted.
- Final setting time is the difference between the time at which water was added to cement and time as recorded in previous step ,and it is equal to or less than 10hours.
Soundness
- The purpose of this test is to detect the presence of un combined lime in the cement.
- The cement paste is prepared.
- The mould is placed and it is filled by cement paste.
- It is covered at top by another glass plate.A small weight is placed at top and the whole assembly is submerged in water for 24 hours.
- The distance between the points of indicator is noted. The mould is again placed in water and heat is applied in such a way that boiling point of water is reached in about 30 minutes. The boiling of water is continued for one hour.
- The mould is removed from water and it is allowed to cool down.
- The distance between the points of indicator is again measured. The difference between the two readings indicates the expansion of cement and it should not exceed 10 mm.
Tensile strength
- This test was formerly used to have an indirect indication of compressive strength of cement.
- The mortar of sand and cement is prepared.
- The water is added to the mortar.
- The mortar is placed in briquette moulds. The mould is filled with mortar and then a small heap of mortar is formed at its top . It is beaten down by a standard spatula till water appears on the surface. Same procedure is repeated for the other face of briquette.
- The briquettes are kept in a damp for 24 hours and carefully removed from the moulds.
- The briquettes are tested in a testing machine at the end of 3 and 7 days and average is found out
2. Explain the mortar and their uses? Also describe the properties of mortar?
MORTAR
Mortar is a bonding agent which is generally produced by mixing cementing or binding material (lime or cement) and fine aggregate (sand, surki, sawdust, etc.) with water. Mortar is used to bind different building blocks like bricks, stones, etc. It can also add a decorative pattern in brick or stone masonry.
Mortar, a bonding agent between building materials, is mainly a mixture of water, fine aggregate (sand, surki, etc) and binding material like cement, lime etc. The applications of mortar in various construction phase have made it a very important civil engineering material.
- USES OF MORTAR
- Mortar is used to bind together the bricks or stones in brick or stone masonry.
- It is used to give a soft even bed between different layers of brick or stone masonry for equal distribution of pressure over the bed.
- It is used to fill up the spaces between bricks or stones for making walls tight.
- It is used in concrete as a matrix.
- It is used in plastering works to hide the joints and to improve appearance.
- It is used for molding and ornamental purpose.
ENGINEERING PROPERTIES OF MORTAR
Cement: It should be fresh and free from adulteration. To know more about the properties of good cement read >> Properties of Good Cement
Lime: Lime must be well slaked.
Sand: Sand should be sharp, angular and porous. It should be free from salts and other impurities. Read>> Function of Sand in Mortar
Surki: Surki should be perfectly pure and free from foreign matter. It should be sufficiently fine to pass through the desired sieve
Mud: Mud should be free from adulteration.
Water: Water should be clean and free from salts and other impurities.
3. What are the uses of STEEL?
USES OF STEELS
Some vital utilization of steels is given below:
- Steel is environment-friendly & sustainable. It posses great durability.
- Compared to other materials, steel requires a low amount of energy to produce lightweight steel construction.
- Steel is the world’s most recycled material which can be recycled very easily. Its unique magnetic properties make it an easy material to recover from stream to be recycled.
- Steel can be designed into various forms. It gives better shape and edge than iron which is used to make weapons.
- Engineering steels are used for general engineering and manufacturing sectors.
- Steel is highly used in the automobile industry. Different types of steels are used in a car body, doors, engine, suspension, and interior. The average 50% of a car is made of steel.
- Steel reduces CO2 emissions.
- All types of energy sectors demand steel for infrastructure and resource extraction.
- Stainless steels are used to produce offshore platforms and pipelines.
- Steels are used for packaging and protecting goods from water, air and light exposure.
- Most of the household appliances like fridge, TV, oven, sinks, etc are made of steel.
- Steels are used for producing industrial goodies like farm vehicles and machines.
- Stainless steel is used as a cutlery material.
- Because of its easily welding capability and attractive finishing, steel has become a prominent feature in modern architecture.
- Stainless steel gives a hygienic environment. That’s why it is used for surgical implants.
- Steel has a wider range of temperature which is used to make large sheets.
- Renewable energy resources like solar, hydro and wind power use the stainless steel components.
- Mild steel is used for building construction. It is also a highly favored building frame material.
4. Explain the properties of steel?
- ENGINEERING PROPERTIES OF STEEL
- Tensile strength
The stress-strain curve for the steel is generally obtained by conducting tensile test on any standard steel specimen. Tensile strength of the steel can be defined in terms of yield strength and ultimate strength.
b. Hardness
Hardness is regarded as the resistance of any material to identification and scratching. This is generally determined by forcing an indenter on to the surface. The resultant deformation steel is both elastic and plastic. The different methods to find out the hardness of metal which includes Brinell hardness test, Vicker’s hardness test, and Rockwell hardness test.
c. Toughness
There is the possibility of microscopic cracks in a material or the material may develop such cracks as a result of several cycles of loading. These cracks may result in sudden collapse of the structure and it is very dangerous. Therefore to ensure that this should not happen, materials in which the cracks grow slowly are preferred. These types of steel are known as notch-tough steels and the amount of energy it absorb is measure by impacting the notch specimen.
d. Fatigue strength
A component of structure, which is designed to carry a single monotonically static load, may fail if the same load is applied cyclically a large number of times. If the example of a thin rod is considered, it bent back and forth beyond yielding fails after few cycles of such repeated bending. This type of failure is termed as fatigue failure. Examples: bridges, cranes, offshore structure, slender tower, etc.
e. Corrosion resistance
Corrosion is the procedure in which oxidation of a metal in a normal atmospheric condition owing to the excessive presence of moisture and oxygen in the air. Corrosion of the metal is a very natural and rapid phenomenon in the areas of high humidity and places closer to saline water. Therefore the efforts to be made to control the corrosion by using galvanize and epoxy coated reinforcement bars but failed in practical usage due to the risk of disbanding, causing accelerated corrosion. Corrosion resistance elements such as copper, phosphorus and chromium are added in appropriate measure to the metal which results in corrosion resistance steel
5. Explain the Brick varieties and strength and also tests on bricks?
BRICKS
Constituents of good brick earth: Bricks are the most commonly used construction material. Bricks are prepared by moulding clay in rectangular blocks of uniform size and then drying and burning these blocks. In order to get a good quality brick, the brick earth should contain the following constituents.
- Silica
- Alumina
- Lime
- Iron oxide
- Magnesia
Brick plays very important role in the field of civil engineering construction. Bricks are used as an alternative of stones in construction purpose.
USES OF BRICKS
- Construction of walls of any size
- Construction of floors
- Construction of arches and cornices
- Construction of brick retaining wall
- Making Khoa (Broken bricks of required size) to use as an aggregate in concrete
- Manufacture of surki (powdered bricks) to be used in lime plaster and lime concrete
CLASSIFICATION OF BRICKS AS PER CONSTITUENT MATERIALS
There are various types of bricks used in masonry
- Common Burnt Clay Bricks
- Sand Lime Bricks (Calcium Silicate Bricks)
- Engineering Bricks
- Concrete Bricks
- Fly ash Clay Bricks
Common Burnt Clay Bricks
Common burnt clay bricks are formed by pressing in moulds. Then these bricks are dried and fired in a kiln. Common burnt clay bricks are used in general work with no special attractive appearances. When these bricks are used in walls, they require plastering or rendering.
Sand Lime Bricks
Sand lime bricks are made by mixing sand, fly ash and lime followed by a chemical process during wet mixing. The mix is then moulded under pressure forming the brick. These bricks can offer advantages over clay bricks such as: their colour appearance is grey instead of the regular reddish colour. Their shape is uniform and presents a smoother finish that doesn’t require plastering. These bricks offer excellent strength as a load-bearing member.
Engineering Bricks
Engineering bricks are bricks manufactured at extremely high temperatures, forming a dense and strong brick, allowing the brick to limit strength and water absorption. Engineering bricks offer excellent load bearing capacity damp-proof characteristics and chemical resisting properties. Concrete Bricks Concrete bricks are made from solid concrete. Concrete bricks are usually placed in facades, fences, and provide an excellent aesthetic presence. These bricks can be manufactured to provide different colours as pigmented during its production.
Fly Ash Clay Bricks
Fly ash clay bricks are manufactured with clay and fly ash, at about 1,000 degrees C. Some studies have shown that these bricks tend to fail poor produce pop-outs, when bricks come into contact with moisture and water, causing the bricks to expand.
6. Explain the ENGINEERING PROPERTIES OF BRICKS?
To know the quality of bricks following 7 tests can be performed. In these tests some are performed in laboratory and the rest are on field.
- Compressive strength test
- Water Absorption test
- Efflorescence test
- Hardness test
- Size, Shape and Colour test
- Soundness test
TESTS ON BRICKS
Structure test Compressive strength test
This test is done to know the compressive strength of brick. It is also called crushing strength of brick. Generally 5 specimens of bricks are taken to laboratory for testing and tested one by one. In this test a brick specimen is put on crushing machine and applied pressure till it breaks. The ultimate pressure at which brick is crushed is taken into account. All five brick specimens are tested one by one and average result is taken as brick’s compressive/crushing strength.
Water Absorption test In this test bricks are weighed in dry condition and let them immersed in fresh water for 24 hours. After 24 hours of immersion those are taken out from water and wipe out with cloth. Then brick is weighed in wet condition. The difference between weights is the water absorbed by brick. The percentage of water absorption is then calculated. The less water absorbed by brick the greater its quality. Good quality brick doesn’t absorb more than 20% water of its own weight.
Efflorescence test The presence of alkalies in bricks is harmful and they form a grey or white layer on brick surface by absorbing moisture. To find out the presence of alkalis in bricks this test is performed. In this test a brick is immersed in fresh water for 24 hours and then it’s taken out from water and allowed to dry in shade. If the whitish layer is not visible on surface it proofs that absence of alkalis in brick. If the whitish layer visible about 10% of brick surface then the presence of alkalis is inacceptable range. If that is about 50% of surface then it is moderate. If the alkalies’ presence is over 50% then the brick is severely affected by alkalies.
Hardness test
In this test a scratch is made on brick surface with a hard thing. If that doesn’t left any impression on brick then that is good quality brick.
Size, shape and colour test
In this test randomly collected 20 bricks are staked along lengthwise, width wise and height wise and then those are measured to know the variation of sizes as per standard. Bricks are closely viewed to check if its edges are sharp and straight and uniform in shape. A good quality brick should have bright and uniform colour throughout.
Soundness test
In this test two bricks are held by both hands and struck with one another. If the bricks give clear metallic ringing sound and don’t break then those are good quality bricks.
Structure test In this test a brick is broken or a broken brick is collected and closely observed. If there are any flows, cracks or holes present on that broken face then that isn’t good quality brick.
7. What are Aggregates? Also explain types & requirements?
AGGREGATES
Aggregate is an aggregation of non-metallic minerals obtained in particulate form and can be processed and used for civil and highway engineering construction.
Aggregates are mainly classified into two categories:
- Fine Aggregate
- Coarse Aggregate
ENGINEERING PROPERTIES OF AGGREGATES
Aggregates are used in concrete to provide economy in the cost of concrete. Aggregates act as filler only. These do not react with cement and water. But there are properties or characteristics of aggregate which influence the properties of resulting concrete mix. These are as follow.
- Composition
- Size & Shape
- Surface Texture
- Specific Gravity
- Bulk Density
- Voids
- Porosity & Absorption
- Bulking of Sand
- Fineness Modulus of Aggregate
- Surface Index of Aggregate
- Deleterious Material
- Crushing Value of Aggregate
- Impact Value of Aggregate
- Abrasion Value of Aggregate
1. COMPOSITION
Aggregates consisting of materials that can react with alkalies in cement and cause excessive expansion, cracking and deterioration of concrete mix should never be used. Therefore it is required to test aggregates to know whether there is presence of any such constituents in aggregate or not.
2. SIZE & SHAPE
The size and shape of the aggregate particles greatly influence the quantity of cement required in concrete mix and hence ultimately economy of concrete. For the preparation of economical concrete mix on should use largest coarse aggregates feasible for the structure. IS-456 suggests following recommendation to decide the maximum size of coarse aggregate to be used in P.C.C & R.C.C mix.
Maximum size of aggregate should be less than
- One-fourth of the minimum dimension of the concrete member.
- One-fifth of the minimum dimension of the reinforced concrete member.
- The minimum clear spacing between reinforced bars or 5 mm less than the minimum cover between the reinforced bars and form, whichever is smaller for heavily reinforced concrete members such as the ribs of the main bars.
3. SURFACE TEXTURE
The development of hard bond strength between aggregate particles and cement paste depends upon the surface texture, surface roughness and surface porosity of the aggregate particles.If the surface is rough but porous, maximum bond strength develops. In porous surface aggregates, the bond strength increases due to setting of cement paste in the pores.
4. SPECIFIC GRAVITY
The ratio of weight of oven dried aggregates maintained for 24 hours at a temperature of 100 to 1100C, to the weight of equal volume of water displaced by saturated dry surface aggregate is known as specific gravity of aggregates.
5. BULK DENSITY
It is defined as the weight of the aggregate required to fill a container of unit volume. It is generally expressed in kg/litre.
Bulk density of aggregates depends upon the following 3 factors.
- Degree of compaction
- Grading of aggregates
- Shape of aggregate particles
6. VOIDS
The empty spaces between the aggregate particles are known as voids. The volume of void equals the difference between the gross volume of the aggregate mass and the volume occupied by the particles alone.
7. POROSITY & ABSORPTION
The minute holes formed in rocks during solidification of the molten magma, due to air bubbles, are known as pores. Rocks containing pores are called porous rocks. Water absorption may be defined as the difference between the weight of very dry aggregates and the weight of the saturated aggregates with surface dry conditions.
Depending upon the amount of moisture content in aggregates, it can exist in any of the 4 conditions.
- Very dry aggregate ( having no moisture)
- Dry aggregate (contain some moisture in its pores)
- Saturated surface dry aggregate (pores completely filled with moisture but no moisture on surface)
- Moist or wet aggregates (pores are filled with moisture and also having moisture on surface)
8. BULKING OF SAND
It can be defined as in increase in the bulk volume of the quantity of sand (i.e. fine aggregate) in a moist condition over the volume of the same quantity of dry or completely saturated sand. The ratio of the volume of moist sand due to the volume of sand when dry, is called bulking factor.
9. FINENESS MODULUS
Fineness modulus is an empirical factor obtained by adding the cumulative percentages of aggregate retained on each of the standard sieves ranging from 80 mm to 150 micron and dividing this sum by 100.
Fineness modulus is generally used to get an idea of how coarse or fine the aggregate is. More fineness modulus value indicates that the aggregate is coarser and small value of fineness modulus indicates that the aggregate is finer.
10. SPECIFIC SURFACE OF AGGREGATE
The surface area per unit weight of the material is termed as specific surface. This is an indirect measure of the aggregate grading. Specific surface increases with the reduction in the size of aggregate particle. The specific surface area of the fine aggregate is very much more than that of coarse aggregate.
11. DELETERIOUS MATERIALS
Aggregates should not contain any harmful material in such a quantity so as to affect the strength and durability of the concrete. Such harmful materials are called deleterious materials. Deleterious materials may cause one of the following effects
- To interfere hydration of cement
- To prevent development of proper bond
- To reduce strength and durability
- To modify setting times
12. CRUSHING VALUE
The aggregates crushing value gives a relative measure of resistance of an aggregate to crushing under gradually applied compressive load. The aggregate crushing strength value is a useful factor to know the behavior of aggregates when subjected to compressive loads.
13. IMPACT VALUE
The aggregate impact value gives a relative measure of the resistance of an aggregate to sudden shock or impact. The impact value of an aggregate is sometime used as an alternative to its crushing value.
14. ABRASION VALUE OF AGGREGATES
The abrasion value gives a relative measure of resistance of an aggregate to wear when it is rotated in a cylinder along with some abrasive charge.
8. Explain Workability, Strength properties of Concrete?
•Concrete is an artificial conglomerate stone made essentially of Portland cement, water, and aggregates.
•Portland cement is produced by mixing ground limestone, clay or shale, sand and iron ore.
•This mixture is heated in a rotary kiln to temperatures as high as 1 600 degrees Celsius high as 1,600 degrees Celsius. The heating process causes the materials to break down and recombine into new compounds that can react with water in a crystallization process called hydration.
•The raw ingredients of Portland cement are iron ore, lime, alumina and silica. These are ground up and fired in a kiln to produce a clinker. After cooling, the clinker is very finery ground.
•When first mixed the water and cement constitute a paste which surrounds all the individual pieces of aggregate to make a plastic mixture.
•A chemical reaction called hydration takes place between the water and cement, and concrete normally changes from a plastic to a solid state in about 2 hours.
•Concrete continues to gain strength as it cures. Heat of hydration - is the heat given off during the chemical reaction as the cement hydrates.
Workability that property of freshly mixed concrete that determines its working characteristics, i.e. the ease with which it can be mixed, placed, compacted and finished.
Factors effecting workability:
•Method and duration of transportation
•Quantity and characteristics of cementing materials
•Concrete consistency (slump)
•Aggregate grading, shape & surface texture
•% entrained air
•Water content
•Concrete & ambient air temperature Admixtures
9. Explain Nominal Proportion Of Concrete Preparation Of Concrete, Compaction and Curing?
Nominal Proportion of Concrete Preparation Of Concrete
Concrete is a commonly used construction material, which is the mixture of cement, sand, aggregate, and admixtures blended with water. Concrete gets hardened with time and gains the strength, and for the best results in a construction of your dream home, mixing of concrete is said to be the most important process. All the ingredients are to be mixed in proper proportion because the properties of concrete like workability, strength, surface finish, and durability of concrete etc. are ensured by the right and proportionate blending.
In the nominal mix concrete, all the ingredients and their proportions are prescribed in the standard specifications. These proportions are specified in the ratio of cement to aggregates for certain strength achievement.
The mix proportions like 1:1.5:3, 1:2:4, 1:3:6 etc. are adopted in nominal mix of concrete without any scientific base, only on the basis on past empirical studies. Thus, it is adopted for ordinary concrete or you can say, the nominal mix is preferred for simpler, relatively unimportant and small concrete works.
As per the ‘Indian Standard- IS 456:2000’, nominal mix concrete may be used for concrete of M20 grade or lower grade such as M5, M7.5, M10, M15.
M 20 is identified as the concrete grade in which, M denotes the Mix and 20 denotes the compressive strength of concrete cube after 28 days of curing in N/mm2. There are various grades of concrete that can be used like M10, M15, M20, M25, M30, etc.
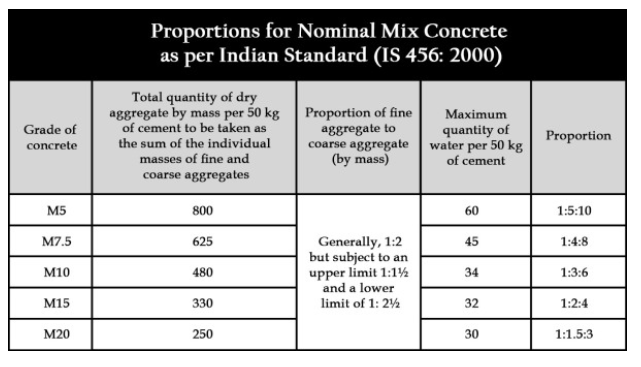
10. Explain Compaction and Curing ?
Compaction of concrete and curing process of concrete
1) Compaction of concrete
•Concrete should be thoroughly compacted and fully work around the reinforcement and into the corners of the formworks
•Concrete shall be compacted using mechanical vibrators
•Whenever vibration has been applied externally the design of formwork and the deposition of vibrators should receive special consideration to ensure efficient compaction and to avoid sir face blemishes
2) Curing process of concrete
•Curing of concrete is defined as the process of maintaining the moisture and temperature condition of concrete for hydration reaction to the normally so that the concrete develops hardened and properties over time
•The main components which need to be taken care of your heat and time during curing process
•Curing is the process of preventing the loss of moisture from the concrete which maintaining a satisfactory temperature effect
•If the cement has high rate of strain development and if the concrete contains granulated blast furnace and flue Ash then,
•The curing should also prevent the development of high temperature gradients within the concrete
a) Moist curing
•Surface of the concrete shall be kept continuously in Dam or wet condition by covering with the layers of materials like checking Canvas etc.
•it should be kept continuously wet for at least 7 days from the date of placing concrete.
•In case of ordinary Portland cement at least 10 days. Where mineral admixture or blended cement are used.
•The period of curing shall not be less than 10 days for concrete exposed to the dry and hot weather condition.
•In case of concrete where mineral admixture or blended cement are used it is recommended that above minimum period may be extended 14 days.
b) Membrane curing
•Approved curing compounds may be used in place of moist curing with the permission of engineer in charge.
•Search compound shall be applied to all exposed surfaces of the concrete as soon as possible after the concrete has set.
•Impermeable membrane such as polyethylene sheeting covering closely the concrete surface may also be used to provide effective barriers against evaporation.
•For the concrete containing Portland pozzolana cement, Portland slag cement or mineral admixture period of curing may be increased