Fig 1 (a) Fig 1 (b)
|
Fig.2 |
Fig.3
|
= |
Fig.4
|







|
Fig.6 |
Helix angle X is very small. ϕ is the total angle through which one end of the spring is turned relative to the other , when couple M is applied. Work done on spring = (½) Mϕ .
Fig 6 shows a b AB of Length subjected to Bending moment M rϕ = L ϕ = L/r , Where r = Radius of Curvature. From Flexure Formula
∴ ϕ = L = 2nπR , I =
∴ ϕ =
∴ δ = |












Open coiled Helical Spring subjected to axial moment An open- coiled helical spring of mean coil radius R, Helix angle α & number of turns n is subjected to an axial moment m as shown in fig. Components of M are M' = M cos α = bending moment & T' = M sin α = Twisting moment δθ' = Angular Twist due to T' δθ' = δϕ = Angular rotation due to M' about y' y' axis = δθ = Angular Twist about xx-axis = δ ϕ ' sin α - δ ϕ ' cos α. Δθ = (
Total angular Twist . θ = ∫δθ = 0∫L M sin α cos α( L = 2 π n R sec α ∴ ϕ (Total Angular Rotation) = 2π n R sec α( |
1) The radial pressure ‘px’ (compressive) 2) The hoop stress fx (tensile) 3) The longitudinal tensile stress po(tensile)
Thin spherical shells
|
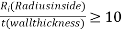
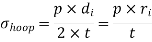
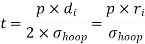
