Unit 9
Question Bank
Question 1) Why Cylinder Diameter reduces as Pressure Increases?
Answer 1)
Have you ever noticed in a multi-stage compressor; the diameter of cylinder liners of each stage is different? To be more elaborate, the first stage cylinder diameter is biggest and the intermediate stage is the second biggest and the third or final stage is the smallest of all. Do you know the reason for this?
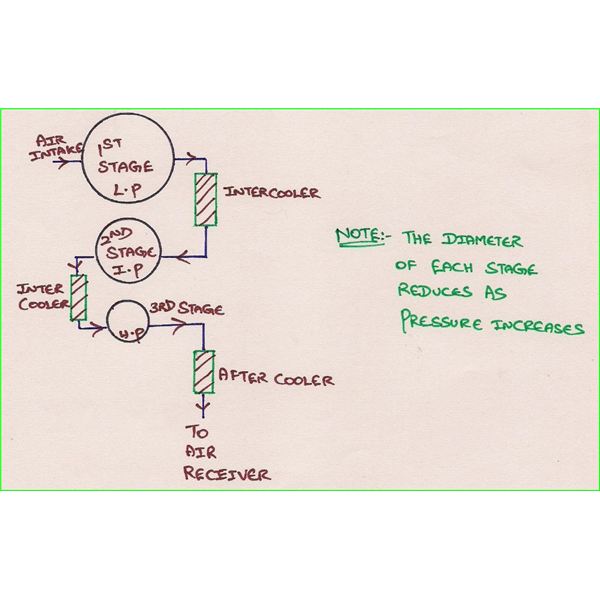
As the pressure of compression increases, the cylinder diameter decreases. The mass flow rate or the amount of air passing through each stage is same. Thus, as the pressure increases with the same mass flow rate, the volume occupied by air must reduce. This is accomplished by reducing the diameter and thus the volume of the cylinder.
Question 2) Advantages of Multi-stage compression?
Answer 2)
- The work done in compressing the air is reduced, thus power can be saved
- Prevents mechanical problems as the air temperature is controlled
- The suction and delivery valves remain in cleaner condition as the temperature and vaporization of lubricating oil is less
- The machine is smaller and better balanced
- Effects from moisture can be handled better, by draining at each stage
- Compression approaches near isothermal
- Compression ratio at each stage is lower when compared to a single-stage machine
- Light moving parts usually made of aluminum, thus less cost and better maintenance
Question 3) Lobe Type Air Compressor
Answer 3) this is one of the simpler compressor type. In this there is no complicated moving part. There are two lobes attached to the driving shaft by the prime mover. These lobes are displaced with 90 degrees to one another. Thus, if one of the lobe is in horizontal direction the other lobes will be exactly positioned at 90 degree i.e. in vertical direction.
The air gets trapped from one end and as the lobes rotate the air gets compressed as shown in image. The compressed air is then delivered to delivery line.
Question 4) Vane Type Rotary Compressor?
Answer 4)
This is another type of rotary compressor. There is a fixed casing in Vane type compressor in which a rotary rotor disc is placed which has slots that are used for holding the sliding plates.
Whenever rotor rotates the disc also rotates thus allowing the sliding plates to slide as the inner surface of casing is eccentric. Whenever the plate’s moves away from the centre a huge amount of air get trapped inside it and with the rotation the sliding plates converge due to its shape and the trapped air get compressed. This results in compression of air.
Question 5) Explain Rotary scroll compressor
Answer 5) they are one of the best compressor type in rotary compressors. The air is compressed using two spiral elements. One element is stationary and the other one moves in small eccentric circles inside the spiral. Air gets trapped inside the spiral way of that element and gets transported in small air-pockets to the centre of the spiral.
Simply air gets trapped at the outer edge and get compressed due to reduction of are as it travels from outer edge to inner edge . It takes about 2 to 3 turns for the air to reach the pressure output in the centre.
Question 6) Explain advantage and disadvantage of rotary scroll compressor?
Answer 6)
Advantages
- Very quiet.
- This is very compact in size.
- Simple design with not so many parts.
- Oil-free design and low maintenance.
Disadvantages
- Output capacity is low.
- Relatively expensive
- You have to buy a new scroll element with the failure of older one even if there is not any big problem.
- The temperature of compressed air is too much high.
Question 7) Explain Rotary compressors
Answer 7) Rotary compressors are another type of famous compressors. It uses two Asymmetrical rotors that are also called helical screws to compress the air.
The rotors have a very special shape and they turn in opposite directions with very little clearance between them. The rotors are covered by cooling jackets. Two shafts on the rotors are placed that transfer their motion with the help of timing gears that are attached at the starting point of the shafts/compressor (as shown in the image).
Working principle-Air sucked in at one end and gets trapped between the rotors and get pushed to other side of the rotors .The air is pushed by the rotors that are rotating in opposite direction and compression is done when it gets trapped in clearance between the two rotors. Then it pushed towards pressure side.
Rotary screw compressors are of two types oil-injected and oil-free.
Oil-injected is cheaper and most common than oil-free rotary screw compressors.
Question 8) Explain advantage and disadvantage rotary compressor?
Answer 8)
Advantages
- Less noisy.
- These are called the work-horses as they supply large amount of compress air.
- More energy efficient as compared to piston type compressors.
- The air supply is continuous as compared to reciprocating compressors.
- Relatively low end temperature of compressed air.
Disadvantages
- Expensive then piston-type compressors.
- More complex design.
- The maintenance is very important
- Minimum one day use is important in a weak to avoid rusting.
Question 9) Explain Applications of Vane Compressor?
Answer 9) Vane Compressor has many applications. They serve a wide range of industries. Some of the applications of the vane compressor are:-
1) They are used in agriculture for operating farm equipment, material conveying, etc.
2) Used in the auto body paint shop for paint pump operation.
3) Used in tire and wheel shop for tire inflation.
4) Used in Dry Cleaning.
5) Used in the operation of air knives for cutting and peeling.
6) It is used in welding operations and air-operated metal and woodworking tools.
Question 10) Explain Advantages and disadvantages of reciprocating compressor
Answer 10)
Advantages:
1. High thermal efficiency and low power consumption per unit
2. Convenient processing, low material requirements and low cost
3. Simple device system
4. Early design and production, mature manufacturing technology
5. Wide range of application
Disadvantages:
1. There are many moving parts, complex structure, heavy maintenance work and high maintenance cost
2. Speed Limited
3. The wear of piston ring, the wear of cylinder and the transmission mode of belt make the efficiency drop rapidly
4. Loud noise
5. The backward control system does not meet the needs of chain control and unattended, so although the price of piston machine is very low, it is often not accepted by users.