Unit - 3
Metallic Materials
Q1) What is steel?
A1)
Steels are iron–carbon alloys that may contain significant amounts of additional alloying elements; there are thousands of distinct alloys with various compositions and heat treatments. The mechanical properties are affected by the carbon content, which is typically less than 1.0 wt%. Some of the more prevalent steels are divided into low-, medium-, and high-carbon categories based on carbon content. Within each group, subclasses exist based on the concentration of various alloying elements. Other than carbon and a small amount of manganese, plain carbon steels contain only residual impurities. More alloying elements are purposely introduced in specified concentrations to alloy steels.
Q2) Explain Low carbon steel.
A2)
Low-carbon steels account for the majority of the numerous types of steel manufactured. These typically contain less than 0.25 wt% C and are insensitive to heat treatments designed to create martensite; cold work is used to reinforce them. The elements of microstructures are ferrite and pearlite. As a result, these alloys are relatively soft and weak but have exceptional ductility and toughness; they are also machinable, weldable, and the least expensive to create of all steels.
Automobile body components, structural shapes (I-beams, channel and angle iron), and sheets used in pipelines, buildings, bridges, and tin cans are only a few examples. They have a yield strength of 275 MPa (40,000 psi), tensile strengths of 415 to 550 MPa (60,000 to 80,000 psi), and 25 percent EL ductility. The high-strength, low-alloy (HSLA) steels are another type of low-carbon alloy. They have higher strengths than ordinary low-carbon steels because they incorporate various alloying elements such as copper, vanadium, nickel, and molybdenum in combined concentrations as high as 10% by weight.
Heat treatment can increase tensile strength to above 480 MPa (70,000 psi); they are also ductile, formable, and machinable. In normal environments, HSLA steels are more corrosion resistant than ordinary carbon steels, which they have largely supplanted in many applications where structural strength is required (for example, bridges, towers, high-rise building support columns, and pressure vessels).
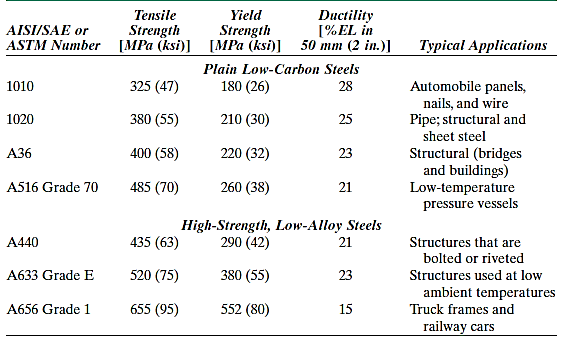
Q3) Explain Medium Carbon steel.
A3)
Carbon contents in medium-carbon steels range from 0.25 to 0.60 wt percent. To improve their mechanical properties, these alloys can be heat-treated by austenitizing, quenching, and tempering. They are most used in tempered form, with tempered martensite microstructures. Plain medium-carbon steels have low hardenability and can only be heat-treated satisfactorily in very thin sections and at extremely high quenching rates.
Additions of chromium, nickel, and molybdenum improve the alloys' heat-treatability, resulting in a wide range of strength–ductility combinations. These heat-treated alloys are stronger than low-carbon steels, but ductility and toughness are sacrificed. Railway wheels and tracks, gears, crankshafts, and other machine elements, as well as high-strength structural components, all require a blend of strength, wear resistance, and toughness.
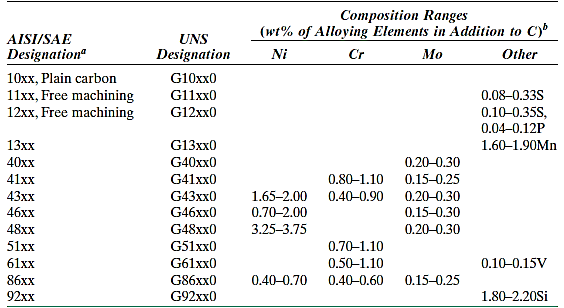
Q4) Explain High-Carbon Steels.
A4)
High-carbon steels, with carbon levels typically ranging from 0.60 to 1.4 wt%, are the hardest, strongest, and least ductile of the carbon steels. They are virtually always hardened and tempered, which makes them particularly wear resistant and capable of keeping a sharp cutting edge. High-carbon alloys with chromium, vanadium, tungsten, and molybdenum are used in tool and die steels. These alloying elements mix with carbon to generate carbide compounds that are extremely hard and wear resistant.
These steels are used in knives, razors, hacksaw blades, springs, and high-strength wire, as well as cutting tools and dies for moulding and shaping materials.
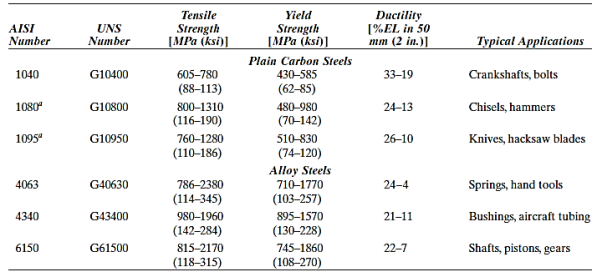
Q5) Write about Stainless Steels.
A5)
In a range of conditions, including the ambient atmosphere, stainless steels are highly resistant to corrosion (rusting). The most common alloying element is chromium, which must have a concentration of at least 11 weight percent Cr. Nickel and molybdenum additives can also improve corrosion resistance. On the basis of the major phase composition of the microstructure, stainless steels are classified as martensitic, ferritic, or austenitic. Stainless steels are extremely adaptable in their use due to their wide range of mechanical qualities and good corrosion resistance. Heat-treating martensitic stainless steels to make martensite the predominant microconstituent is possible. The iron–iron carbide phase diagram changes dramatically when alloying metals are added in considerable amounts.
The austenite (or ) phase field in austenitic stainless steels is extended to ambient temperature. The α-ferrite (BCC) phase is found in ferritic stainless steels. Because austenitic and ferritic stainless steels cannot be heat-treated, cold work is used to harden and strengthen them. Because of the high chromium content and nickel additions, austenitic stainless steels are the most corrosion resistant, and they are manufactured in the greatest amounts. Stainless steels that are martensitic or ferritic are magnetic; stainless steels that are austenitic are not.
Because they resist oxidation and maintain mechanical integrity at high temperatures and in harsh environments, several stainless steels are extensively utilised; the top temperature limit in oxidising atmospheres is around 1000C (1800F). Gas turbines, high-temperature steam boilers, heat-treating furnaces, aircraft, missiles, and nuclear power-generating equipment all use these steels.
Q6) What is Cast iron?
A6)
Cast irons are a type of ferrous alloy with a carbon concentration greater than 2.14 weight percent; however, most cast irons possess between 3.0 and 4.5 weight percent C, as well as other alloying elements. A closer look at the iron–iron carbide phase diagram reveals that alloys in this composition range become entirely liquid at temperatures between 1150 and 1300C (2100 and 2350F), which is significantly lower than steel temperatures. As a result, they are easily melted and castable. Furthermore, some cast irons are extremely fragile, and casting is the most practical method of manufacturing
Q7) Draw The iron–iron carbide phase diagram.
A7)
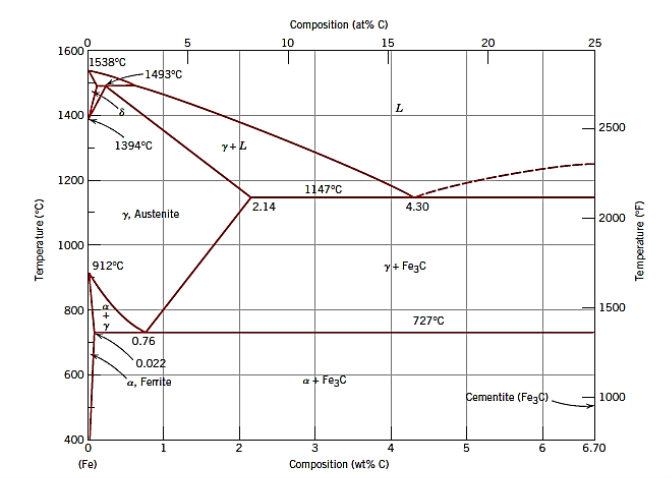
Q8) What is Gray iron?
A8)
Gray cast irons have carbon and silicon concentrations of 2.5 to 4.0 wt percent and 1.0 to 3.0 wt percent, respectively. The graphite in most of these cast irons is in the form of flakes (like corn flakes), which are usually surrounded by an x-ferrite or pearlite matrix; this is the microstructure of a typical grey iron. A shattered surface takes on a grey look as a result of the graphite flakes, hence the name.
Because of its microstructure, grey iron is comparatively weak and brittle in tension; the tips of the graphite flakes are sharp and pointed and may act as stress concentration locations when an external tensile load is applied. Under compressive loads, strength and ductility are substantially higher.
Gray irons have several useful properties and are widely used. When comparing the respective damping capacities of steel and grey iron, they are quite effective in damping vibrational energy. This material is widely used to build the base constructions of machinery and heavy equipment that are subjected to vibrations. In addition, grey irons have a good wear resistance. Furthermore, they have a high fluidity at casting temperature in the molten state, allowing for the casting of intricately shaped objects, as well as reduced casting shrinkage. Finally, and perhaps most importantly, grey cast iron is one of the most affordable metals available.
Q9) What is Ductile iron?
A9)
Before casting, a small quantity of magnesium and/or cerium is added to the grey iron, resulting in a specific microstructure and set of mechanical properties. Graphite still exists, albeit in the shape of nodules or spherelike particles rather than flakes. The resulting alloy has a characteristic microstructure and is known as ductile or nodular iron. Depending on the heat treatment, the matrix phase enclosing these particles is either pearlite or ferrite; for an as cast piece, the matrix phase is usually pearlite. However, a heat treatment at around 700C (1300F) for several hours will result in a ferrite matrix, as seen in this photomicrograph. Castings are substantially more ductile and stronger than grey iron
Q10) What is white iron?
A10)
Most of the carbon in low silicon cast irons (less than 1.0 wt percent Si) and quick cooling rates resides as cementite rather than graphite. Because the fracture surface of this alloy is white, it is known as white cast iron. Thick portions may only have a thin layer of white iron on the top that was "chilled" during the casting process; grey iron forms in the inside, which cools more slowly. White iron is highly hard but also extremely brittle, to the point of being essentially unmachinable, due to large concentrations of the cementite phase. Its applications are limited to those that require a highly hard and wear-resistant surface without a significant degree of ductility, such as rollers in rolling mills. White iron is typically utilised as a step between the manufacture of malleable iron and another type of cast iron.
Heating white iron for a long time at temperatures between 800 and 900 degrees Celsius (1470- and 1650-degrees Fahrenheit) in a neutral atmosphere (to prevent oxidation) causes the cementite to decompose, forming graphite in the form of clusters or rosettes surrounded by a ferrite or pearlite matrix, depending on the cooling rate.
Q11) Write about Iron carbon Diagram.
A11)
In the Fe–Fe3C phase diagram, the components are Fe and Fe3C (iron carbide). It is also feasible to have a phase diagram with the components Fe and C (graphite). Graphite has a higher stability than Fe3C. As a result, the Fe–Fe3C phase diagram might be called metastable. The majority of steels do not include graphite and instead contain just iron carbide.
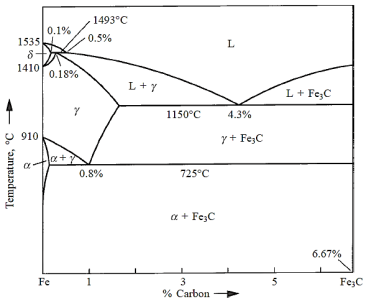
Pure iron melts at 1535°C. A peritectic invariant reaction occurs at 1493°C with the peritectic composition at 0.18% carbon.
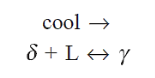
Austenite is the name for the product phase . At 1150°C, a eutectic reaction occurs, with the following eutectic composition.
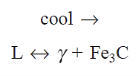
At 725°C, a eutectoid reaction occurs, with the following eutectoid composition.

Austenite () breaks down into two phases: ferrite (x) and cementite (α) (Fe3C).
Steels are Fe–C alloys having 0–1.4 percent carbon. Mild steels have a carbon percentage of 0–0.3 percent, medium carbon steels have a carbon content of 0.3–0.6 percent, and high carbon steels have a carbon content of 0.8–1.4 percent. We'll look at the microstructures of slowly cooled steels with various carbon contents. Steel's structure is fundamentally polycrystalline (ferrite), which is the interstitial solid solution of carbon in BCC iron, when the carbon percentage is minimal.
The microstructure of steel with a eutectoid carbon content of 0.8 percent consists of alternate layers of thin, parallel plates of α (ferrite) and Fe3C. (cementite). Pearlite is the name for this eutectoidal combination. Pearlite is not a single phase, but rather a microconstituent. It gets its name from its iridescent appearance under the microscope, which resembles mother of pearl.
About 75% of proeutectoid ferrite, which occurs above the eutectoid temperature, and 25% of pearlite make up mild steel with 0.2 percent carbon. The amount of pearlite grows as the carbon percentage of the steel increases, until we reach the totally pearlitic structure at 0.8 percent carbon. In addition to pearlite, high carbon steels contain proeutectoid cementite above 0.8 percent.
The relative proportions of the soft, ductile ferrite and the hard, brittle cementite govern the overall hardness and ductility of slowly cooled carbon steels. As we progress from low carbon to high carbon steels, the cementite content increases, resulting in an increase in hardness and a decrease in ductility.
Cast irons are Fe–C alloys containing more than 2% carbon. Consider the cooling of a 3 percent carbon cast iron, for example. Proeutectic (austenite) crystallises first upon crossing the liquidus into the (L +
) zone.
When a liquid with eutectic composition passes through the eutectic temperature, it decomposes into a mixture of austenite and cementite.
The austenite decomposes to pearlite when it cools to the eutectoid temperature, providing white cast iron. White cast iron is highly hard and brittle due to the presence of a large amount of cementite.
The carbon in cast iron may be present as graphite or cementite, depending on the cooling rate and any alloying components present. Graphite flakes can be found in grey cast iron. The creation of graphite is aided by slow cooling rates and the presence of silicon. Gray cast iron has a microstructure of graphite flakes in a ferrite matrix. The sharp tips of the graphite flakes work as stress relievers. Gray cast iron is fragile under tensile pressures as a result of this, despite the fact that graphite is softer than the exceedingly strong cementite found in white cast iron.
Brittleness can be prevented by manufacturing graphite in the shape of spherical nodules (without stress-inducing sharp ends), as in malleable cast iron and SG (spheroidal graphite) iron.
Malleable cast iron is made by heating white cast iron to around 900°C for a long time and then cooling it gently. To ensure that cementite rather than flaky graphite forms during solidification, the alloy's silicon concentration must be less than 1%. During the subsequent heat treatment, the cementite decomposes into the more stable graphite
In the heat-treated microstructure, graphite appears as roughly spherical temper carbon particles. SG iron (also known as nodular iron) is made by adding specific alloys to molten iron, such as Mg or Ce. To encourage graphitization, the silicon content must be around 2.5 percent. The alloy additives change the development rate of graphite from the melt to be more or less equal in all directions, resulting in nodules (rather than flakes) of graphite. SG iron does not require any additional heat treatment.
Q12) Explain Annealing.
A12)
The term annealing refers to a thermal treatment in which a material is heated to a high temperature for a long time and then cooled gently. Annealing is typically used to (1) relieve stresses, (2) enhance softness, ductility, and toughness, and/or (3) create a specified microstructure. There are many different types of annealing heat treatments; they are distinguished by the changes that are generated, which are often microstructural and are responsible for the change in mechanical properties.
Any annealing process has three stages: heating to the required temperature, holding or "soaking" at that temperature, and cooling to room temperature. In these operations, time is a crucial factor. Temperature gradients exist between the outer and interior components of the piece during heating and cooling; their magnitudes are dependent on the item's size and form.
Temperature gradients and internal tensions may be created if the rate of temperature change is too fast, resulting in warping or breaking. In addition, the actual annealing period must be sufficient to allow for any required transformation reactions. The annealing temperature is also crucial to consider; because diffusional processes are generally involved, annealing can be hastened by increasing the temperature.
Q13) Explain Process Annealing.
A13)
Process annealing is a heat treatment that softens and increases the ductility of a previously strain-hardened metal, thereby negating the effects of cold work. It's widely used in fabrication techniques that demand a lot of plastic deformation to keep the deformation going without fracturing or wasting a lot of energy. Processes of recovery and recrystallization are permitted to take place. Typically, a fine-grained microstructure is desired, so the heat treatment is stopped before significant grain growth occurs. By annealing at a low temperature (but above the recrystallization point) or in a nonoxidizing environment, surface oxidation or scaling can be avoided or minimised.
Q14) Explain Stress relieving.
A14)
Internal residual tensions in metal parts may emerge as a result of the following: (1) plastic deformation processes such as machining and grinding; (2) nonuniform cooling of a piece that has been processed or fabricated at a high temperature, such as a weld or a casting; and (3) a phase transformation induced by cooling in which the parent and product phases have different densities. If these residual pressures are not eliminated, distortion and warpage may occur. A stress relief annealing heat treatment, in which the piece is heated to the recommended temperature, kept there long enough to achieve a consistent temperature, and then cooled to room temperature in air, may be used to eradicate them. The annealing temperature is usually kept low enough to preserve the effects of cold working and other heat treatments.
Q15) Explain Tempering
A15)
The tempering process provides a method for transforming martensite into ferrite and cementite. How much of the martensite is transformed depends on the temperature and time of the tempering process.
Tempering occurs in four stages:
Stage 1:
Heating hardened steel up to a temperature of 200^0 C causes the martensite to reject some of the interstitial carbon.
In doing this, the tetragonal martensite structure comes closer to the equilibrium B.C.C. Structure of ferrite.
This rejected carbon combines with some martensite to form a carbide whose composition ranges from 〖Fe〗_(2 ) C to 〖Fe〗_3 C. This precipitation is called epsilon carbide or hexagonal closed packed carbide.
Its presence distorts the martensite matrix and results in a slight hardening of the steel.
Stage 2:
Further heating to about 300^0 C, causes any austenite that was retained by the steel after quenching to decompose into ferrite and cementite. Some softening accompanies this transformation.
Stage 3:
Further heating to about 400^0 C, causes the epsilon carbide to transform to cementite and ferrite.
Most of it forms to cementite because the composition of epsilon carbide is close to that of cementite. This portion of the tempering cause significant softening. If the transformation is allowed to progress long enough, the final structure will consist of cementite and ferrite.
Often the tempering process is stopped at a point where steel contains cementite, ferrite and martensite.
Stage 4:
If tempering is done at a temperature just below the lower critical point or the eutectic point, the cementite forms spheres or spheroidized steel.
In steel containing one alloying addition, cementite forms first and the alloy diffuse to it.
Q16) Explain Normalizing.
A16)
Steels that have been plastically deformed, such as by rolling, include irregularly shaped pearlite grains (and most likely a proeutectoid phase) that are quite large yet vary significantly in size. Normalizing is an annealing heat treatment that refines the grains (i.e., reduces the average grain size) and produces a more uniform and acceptable size distribution; fine-grained pearlitic steels are tougher than coarse-grained pearlitic steels. Heating to at least 55°C (100°F) over the upper critical temperature—that is, above A3 for compositions less than the eutectoid (0.76 wt percent C), and above Acm for compositions more than the eutectoid (0.76 wt percent C)—is required to normalise. After allowing enough time for the alloy to fully change to austenite (a process known as austenitizing), the treatment is completed by cooling in air.
Q17) What do you mean by Hardenability?
A17)
Hardenability is a measure that relates the effect of alloy composition on a steel alloy's ability to transition to martensite for a specific quenching procedure. There is a unique relationship between mechanical qualities and cooling rate for each distinct steel alloy. The ability of an alloy to be hardened by the development of martensite as a result of a specific heat treatment is referred to as hardenability.
Hardenability is a qualitative measure of the rate at which hardness drops down with distance into the interior of a specimen as a result of decreasing martensite content, rather than "hardness," which is the resistance to indentation. A steel alloy with a high hardenability hardens, or develops martensite, not only on the surface but also throughout the inside to a great extent.
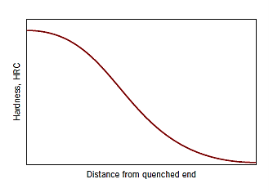
Q18) Write about Copper based alloys.
A18)
Since antiquity, copper and copper-based alloys have been used in a wide range of applications due to their ideal mix of physical qualities. Unalloyed copper is difficult to mill because it is so soft and malleable; nonetheless, it has an almost limitless capacity for cold working. It also has a strong corrosion resistance in a variety of conditions, including the ambient atmosphere, seawater, and several industrial chemicals.
Copper can be alloyed to improve its mechanical and corrosion resistant qualities. Because heat-treating techniques cannot harden or strengthen most copper alloys, mechanical characteristics must be improved through cold working and/or solid solution alloying. Brasses are the most frequent copper alloys, with zinc being the most common alloying element as a substitutional impurity.
Yellow, naval, and cartridge brass; muntz metal; and gilding metal are some of the most prevalent brasses.
Bronzes are copper alloys with a variety of additional elements such as tin, aluminium, silicon, and nickel. These alloys are a little stronger than brasses, yet they still have excellent corrosion resistance. The beryllium coppers are the most prevalent heat-treatable copper alloys. They have tensile strengths of up to 1400 MPa (200,000 psi), excellent electrical and corrosion properties, and wear resistance when properly lubricated; they can be cast, hot worked, or cold worked. Precipitation-hardening heat treatments are used to achieve high strengths.
Because of the beryllium additions, which range between 1.0 and 2.5 weight percent, these alloys are expensive. Landing gear bearings and bushings for jet aircraft, springs, and surgical and dental tools are all examples of applications.
Q19) Write about Aluminium based alloys.
A19)
Aluminum and its alloys have a low density (2.7 g/cm3 compared to 7.9 g/cm3 for steel), good electrical and thermal conductivities, and corrosion resistance in a variety of conditions, including the ambient atmosphere. Because of their ductility, many of these alloys are simple to make, as illustrated by the thin aluminium foil sheet into which the relatively pure material can be rolled.
Aluminum's ductility is maintained even at very low temperatures due to its FCC crystal structure. Aluminum's main drawback is its low melting point of 660°C (1220°F), which limits the maximum temperature at which it may be employed.
Aluminum's mechanical strength can be increased through cold work and alloying, but both techniques reduce corrosion resistance. Copper, magnesium, silicon, manganese, and zinc are common alloying elements. Nonheat-treatable alloys are made up of a single phase, and solid-solution strengthening is used to boost their strength. As a result of alloying, some materials become heat treatable (i.e., they can be precipitation hardened). Precipitation hardening occurs in several of these alloys when two elements other than aluminium precipitate to produce an intermetallic complex such as MgZn2.
Aluminum alloys are generally classed as either cast or wrought. Both forms of composition are identified by a four-digit number that specifies the major contaminants and, in some situations, the purity level. A decimal point is placed between the last two numbers of cast alloys. After these numbers, there's a hyphen and the basic temper designation, which is a letter and perhaps a one- to three-digit number that specifies the alloy's mechanical and/or heat treatment. F, H, and O, for example, denote the as-fabricated, strain-hardened, and annealed states, respectively; T3 indicates that the alloy was solution heat-treated, cold worked, and naturally aged.
Aluminum alloys are used in a variety of applications, including aeroplane structural elements, beverage cans, bus bodywork, and automobile parts (engine blocks, pistons, and manifolds). Aluminum alloys and other low-density metals (e.g., Mg and Ti) have recently received attention as engineering materials for transportation, with the goal of reducing fuel consumption. Specific strength, as measured by the tensile strength–specific gravity ratio, is an important feature of these materials. Even if an alloy of one of these metals has a lower tensile strength than a denser substance (such as steel), it may support a greater load on a weight basis.
The aircraft and aerospace industries have lately produced a new generation of aluminum–lithium alloys. Low densities (between 2.5 and 2.6 g/cm3), high specific moduli (elastic modulus–specific gravity ratios), and outstanding fatigue and low-temperature toughness qualities characterise these materials. Furthermore, some of them may have hardened due to precipitation. However, due of lithium's chemical reactivity, unique processing processes are necessary, making these materials more expensive to produce than normal aluminium alloys
Q20) Explain the term super alloys.
A20)
Superalloys feature extraordinary combinations of characteristics. The majority are utilised in aircraft turbine components, which must endure prolonged exposure to highly oxidising conditions and high temperatures. Under these conditions, mechanical integrity is vital; density is a key issue in this regard because centrifugal stresses in rotating members are reduced when density is lowered.
These materials are divided into three groups based on the major metal(s) in the alloy: iron–nickel, nickel, and cobalt. Refractory metals (Nb, Mo, W, Ta), chromium, and titanium are some of the other alloying components. Additionally, these alloys are classified as wrought or cast.
Superalloys are used in nuclear reactors and petrochemical equipment, in addition to turbines.