Unit - 5
Boiling and Condensation
Q1) Saturated steam at 54.5°C condenses on the outside surface of a 25.4 mm outer diameter 3.66 m long vertical tube maintained at a uniform temperature of 43.3°C. Because of the occurrence of ripples on the surface of the condensate film the actual heat transfer coefficient is about 20% higher than that obtained by Nusselt’s equation. Determine the average condensation heat transfer coefficient over the entire length of the tube and the rate of condensate flow at the bottom of the tube. Check that the flow is laminar. The properties of condensate at 48.9°C are hfg= 2372.4 kJ/kg, k = 0.642 W/mK, = 988.4 kg/m3 and
= 0.558 x10–3 kg/ms.
A1)
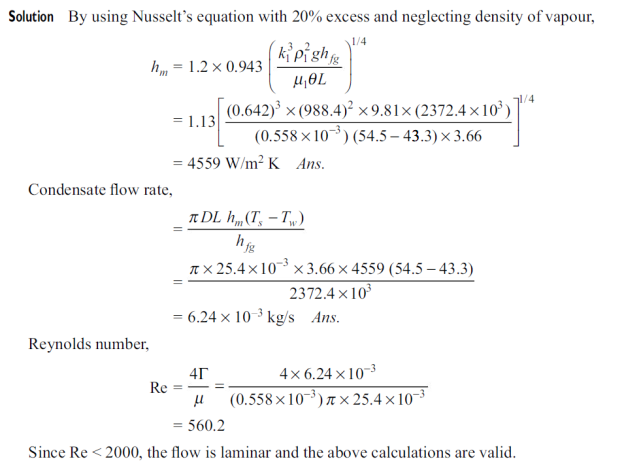
Q2) Steam flowing at a rate of 10,000 kg/h and at 120°C is condensed using cooling water at an average temperature of 20°C. The condenser contains 800 tubes which have an outer diameter of 18 mm. Estimate the heat transfer coefficient (a) if the condenser is vertical and (b) if the condenser is horizontal with tubes 3 m long and condensation takes place outside the tubes.
A2)
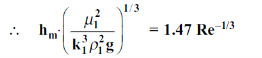
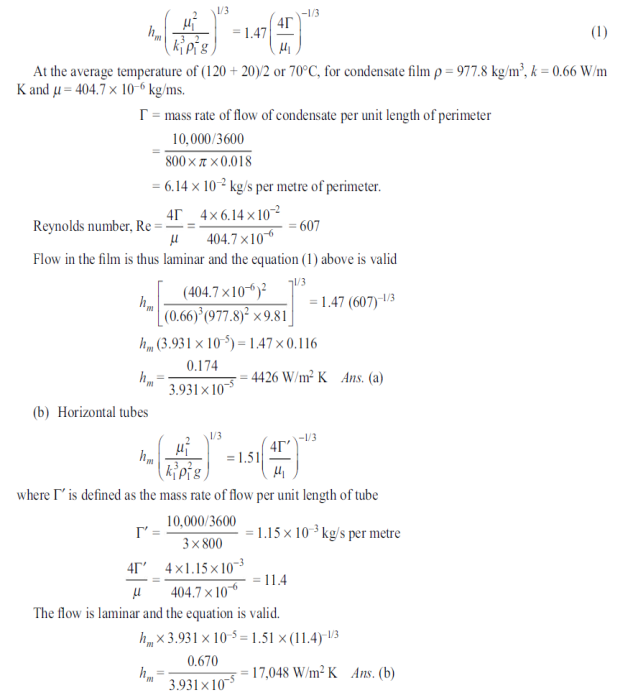
Q3) A square array of 400 tubes 15 mm outer diameter is used to condense steam at atmospheric pressure. The tube walls are maintained at 88°C by a coolant flowing through the tubes. Calculate the amount of steam condensed per hour per unit length of the tubes.
A3)

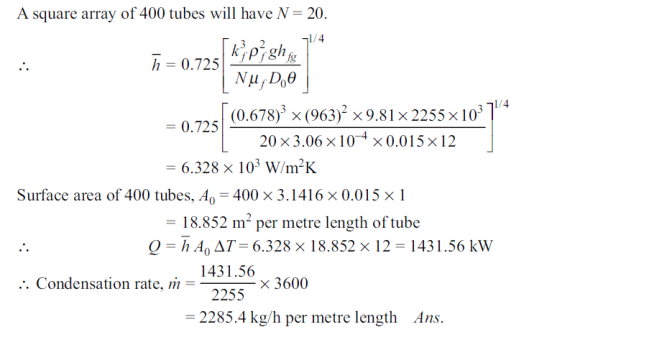
Q4) Explain significance of Reynold’s number in condensation heat transfer.
A4)
Reynolds number of the condensate flow is very important in determining condensation behaviour. It is often convenient to express the heat transfer coefficient directly in terms of Re.
Reynold’s number can be given as

By performing basic mathematical operations Eq.5.11 can be expressed as
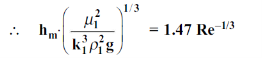
Similarly for flow over horizontal tube
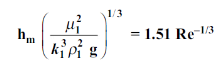
Q5) Compare film wise and drop wise condensation.
A5)
Sr.no | Film wise condensation | Drop wise condensation |
1. | Film of vapour is formed on surface. | Vapour droplets are formed on surface. |
2. | It wets the surface. | It does not wet the surface. |
3. | High thermal resistance due to film. | Low thermal resistance as there is no film. |
4. | Low heat transfer rate. | High heat transfer rate. |
5. | Rate of heat transfer from vapour to surface is low. | Rate of heat transfer from vapour to surface is more. |
6. | Usually occurs on clean surface. | Usually occurs on rough surface. |
Q6) Explain forced convection boiling.
A6)
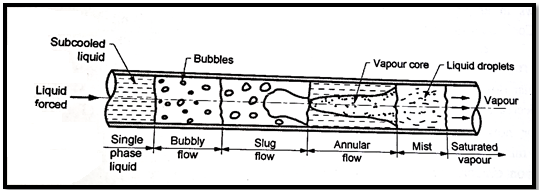
Fig 1. Forced convection boiling
Unlike pool boiling in forced convection boiling, directed motion is provided to fluid from external source. Various regions involved in forced convection boiling are
- Bubbly flow region:
In this region, bubbles formed at inner surface of the heated tube are mixed and carried by saturated liquid being forced to flow. The bubble growth depends on flow velocity.
- Slug flow region:
Individual bubbles combine to form larger bubbles or slugs of vapour. Volume of bubble keeps on increasing.
- Annular flow region:
In this region, vapour formed earlier combine and flow at larger velocity in central core of tube while fluid flows through annular passage around the curve.
- Mist flow region:
In this region, thickness of annular liquid ring keeps on decreasing and finally it is vanished. Vapour now flows with suspended liquid known as mist. Mist region continues until all the liquid is converted into vapour.
Q7) Enlist the methods to increase heat transfer rate by condensation boiling.
A7)
- For drop wise condensation to occur, the heat transfer surfaces are given special coating such as zinc.
- Certain additives like oleic acid are added to condensing fluid to promote drop condensation. These additives are called promoters.
- Sometimes condenser surfaces are slightly inclined to horizontal so that droplets vacate contacting surface.
- By keeping higher temperature differential between temperature of surface and vapour.
Q8) Explain modes of boiling.
A8)
- Pool boiling:
It refers to a condition in which the heating surface is submerged beneath a free surface of liquid. Heat transfer takes place due to free convection only.
- Forced convection boiling:
In this case the fluid motion over a heated surface is provided by external means like pump in order to increase heat transfer coefficient.
- Sub-cooled or local boiling:
In a boiling process, the average liquid temperature may remain well below the saturation temperature with the wall temperature above saturation thus producing “local” boiling at the wall with subsequent condensation in the colder bulk of the liquid. This is known as Sub-cooled or local boiling.
- Saturated or bulk boiling:
Boiling in a liquid at saturation temperature is known as saturated or bulk boiling.
Q9) Explain nucleate boiling regime in pool boiling curve.
A9)
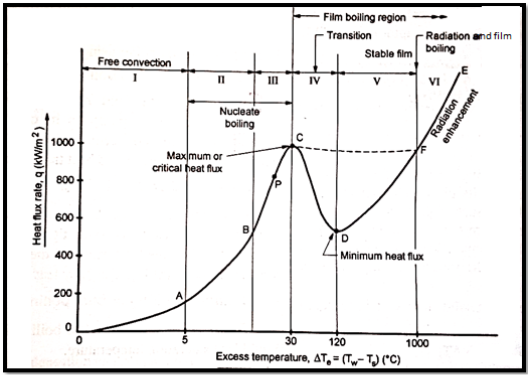
Fig 2. Pool boiling curve
- Nucleate boiling(Regimes 2 and 3):
Heat flux increases rapidly with increase in excess temperature. Value of is in range 5oC to 30oC. Nucleate boiling consist of two regimes viz. 2 and 3.
During period A to B that is 2nd region of pool boiling, bubbles formed are very few in numbers. These bubbles condense in liquid and do not reach to the free surface. This region is also called unstable nucleate boiling due to instability of bubbles.
With further increase in temperature excess temperature in region 3, large number of bubbles are formed. These bubbles grow in size and rise to free surface of liquid. This region B to C is called stable nucleate boiling. As bubbles formed leave the surface almost immediately, the heating surface becomes available for new bubble formation. Hence, heat transfer continuously increases and reaches to a maximum value at point C. This maximum value is called critical heat flux.
Q10) What is significance of critical heat flux?
A10)
- The point C represents the point of maximum critical heat flux on pool boiling curve at which the nucleate boiling ends and film boiling is initiated.
- Point E also represents point at which maximum heat flux occurs. At this point temperature is very high.
- Any increase in heat flux beyond critical heat flux will cause sharp departure from boiling curve in which the surface conditions change abruptly. This may cause damage to metal surface and may even cause melting of metal surface.
- For this reason, point of maximum heat flux is called burn out point. Evaporators and boilers are always designed for values less than critical heat flux.