Unit - 2
Introduction to Riveted, Bolted and Pinned Connections
Q1) Explain the terms Riveted, Bolted and Pinned Connections?
A1)
Riveted connections:
The riveted connections are these days obsolete. The know-how of this kind of connections for the power assessment and rehabilitation for an older shape is essential. While the relationship technique for riveted connections is equal as that of the bolted connections.
Rivet:
A rivet is made of spherical ductile metallic bar that is known as etc. ‘shank’ and with a head at the only quit. It is made of moderate metallic or excessive tensile metallic.
Riveting:
Riveting is the unique technique of connecting collectively portions of metallic. This technique is carried out through putting the ductile metallic pins known as etc. rivet into the holes of portions to be joined and shaped a head on the quit of the rivet to prevent every metallic piece from coming out.
The shank of the rivet is made of the period to the quantity via the unique elements that is to be linked and with enough greater period for a second head to be made at the opposite quit.
The rivets are commonly categorized as follows:
- Hot pushed rivets: The rivets which might be pushed within side the warm conditions
- Shop rivets: The rivets which might be located in workshop
- Field rivets: The rivets which might be located within side the site/field.
- Cold pushed rivets: Since excessive strain is needed to shape the top at room temperature this kind of rivet is limited.
Clamp movement:
When warm pushed rivets are well cooled down then the diameter and shank period get reduced. Because of this, the compression of the plates happens and those outcomes in friction among the plates, this technique is known as categorized clamp movement.
Disadvantages of riveted connections are as follows:
- It is related to very excessive stage of noise pollution
- There is a want to warmth the rivet until purple warm color.
- Skilled labors are vital to investigate the relationship.
- The fee to get rid of the poorly hooked up rivet could be very excessive.
- The excessive-fee set up within side the connection.
Bolted Connection:
Most generally used connections consist of the bolted connections. This connection has the benefit of pliability in assembling elements of the shape as well as dissembling it and that is vital if there may be inspection or a few routine maintenances. This kind of connections is relevant for participants subjected to anxiety or shear or each anxiety and shear.
A bolt is a metallic pin with a head shaped at one quit and the shank threaded on the different quit in order that nut may be received. Generally, the bolts are used to attach the portions of metals through putting them via the holes within side the metals; on the threaded quit, nuts ought to be tightened.
The blessings of bolted connections are as follows:
- The technique of erection of shape may be made faster.
- Skilled labors aren't vital.
- Connections do now no longer contain the noise.
- Requirement of labors is less.
- Immediate use of shape is feasible in case of bolted connection.
- The opportunity association of structural participants is feasible if required.
- Lesser running place is needed.
The risks of bolted connections are as follows:
- The cloth fee could be very excessive.
- Due to the place discount at the basis of the thread and because of concentration of pressure, the tensile power of this kind of connection is reduced.
- Bolts get free if it's far subjected to vibrations or shocks.
Classification of bolted connections:
The classifications of bolted connections are made on the premise of resultant pressure transferred, kind of pressure and pressure mechanism.
On the premise of resultant pressure transferred:
- Concentric connections: When the burden of structural member passes via the CG of the segment then this kind of connections are made.
- Eccentric connections: Whenever the ensuring pressure is performing far from the CG of the connections.
- Moment resisting connections: Whenever the connections are subjected to moments.
On the premise of kind of pressure:
- The connections are categorized as shear connections whilst the switch of load passed off via shear. Example: lap joint, butt joint
- Tension connection: Whenever the switch of load passed off via anxiety at the bolts.
- Combined anxiety shear connections: on every occasion the bracket connection is used to join the willing member to the column of the shape.
On the premise of pressure mechanism:
- Bearing kind connections: To switch the pressure bolts under go towards the hole
- Friction kind connections: Due to tensioning of the bolts the pressure is transferred via friction among the plates.
The layout philosophy:
The traditional technique to research the relationship is primarily based totally at the following conditions:
- The deformation of the relationship is omitted because the linked factors of the systems is taken into consideration as inflexible connections
- The connectors used to at technique factors of the segment behave like linear – elastic manner till it fails.
- The ductility belongings of connectors of the systems are unlimited.
In sensible situations, the linked sections like angles, gusset plates, etc. are bendy deformation happens on the low depth of load also.
The bearing pressure performing at the bolt is proven at (c) and the shear pressure at (d) and (e). The most shear performing at the bolt, P, happen son the touch surface of the plates. The shear pressure at the bolt on the vital shear aircraft is
Fv= P/Ab
Where
Ab is nominal cross-sectional place of the bolt = pie*d2/4
The slip-vital bolt proven in Fig. 10.3a, relies upon Fl the friction brought about among the linked elements through the clamping movement of the pretension bolts to switch the burden from one linked part to another. No slip happens at carrier hundreds and, as proven at (b), the pressure among the linked plates is transferred through friction.
A lap joint isn't always a desired connection due to the bending stresses produced within side the participants through the eccentricity of the hundreds. A greater appropriate connection is the butt splice and that is proven in Fig. The bolts in a splice joint are in double shear
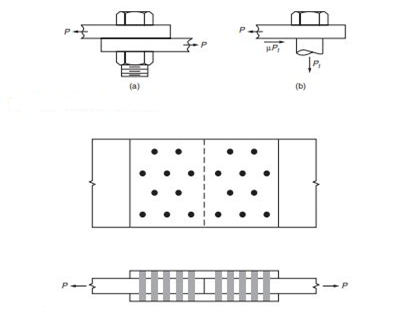
With two critical shear planes. Hence, each bolt has twice the shear capacity of a bolt in a lap joint. Figure shows a hanger connected by bolts to the bottom flange of a girder. Here the bolts are in tension. An example of a situation where bolts are subjected to combined shear and tension is shown in Fig. In this connection, all bolts are equally loaded in shear. However, because of the eccentricity of the applied load, the top row of bolts also resists tensile stress.
Q2) Bolts in Shear and Bearing with Deformation a Design Consideration The connection shown in Fig. Consists of four, grade A490, ¾-in-diameter bolts. The bolts are snug-tight and threads are excluded from the shear planes. Deformation around the bolt holes is a design consideration and the bolt spacing is as indicated. The angles and gusset plate are fabricated from A36 steel. Assuming that the angles and gusset plate are satisfactory, determine the shear force that may be applied to the bolts in the connection. The bolt edge distance perpendicular to the direction of the tensile force is obtained from Fig.
A2)
L=1.75 in
The bolt edge distance in the direction of the tensile force is obtained from Fig. 10.7
Lc=2 in
Lc= clear distance, in the direction of force, between the edge of the hole and the edge of the 3/4-in gusset plate
= Lc- (d+1/16)/2
= 1.59 in
The bolt pitch is obtained from Fig. 10.7 as s = 3 in
4d
>3d +1/16 ... Full bearing capacity possible on all bolts \
Hence, tear out does not govern and a nominal bearing stress of 2.4Fu is applicable. The available bearing capacity of the four bolts on the 3/4-in plate material is
LRFD | ASD
|
The design bearing strength is ![]() ![]() ![]() | The allowable bearing strength is ![]() ![]() ![]() |
The double shear capacity of the for, grade in diameter bolts with threads excluded from the shear planes is
LRFD | ASD
|
The design shear strength is ![]() ![]() ![]() ![]()
| The allowable shear strength is ![]() ![]() ![]() |
Q3) Explain Riveted Connections, Patterns of Riveted Joints?
A3)
A rivet is a ductile steel pin with a manufactured head at one end and a straight portion known as shank.
Riveting is the process of the driving of rivets in to the holes made in the metal parts so that to metal parts are inseparable. The size of rivet hale is kept slightly more (1.5 to 2 mm) than the size of rivet.
The rivet is heated uniformly in a furnace so that it becomes red hot. Then, it is inserted in to the holes drilled in the metal parts.
The projected portion of red-hot shank is then hammered and it results in to expansion of the rivet.
Then desired shape given to head, on cooling, the rivet contracts in length so that plate firmly in contact. Normally, the rivet is driven by the pneumatic process in the workshops.
Q4) What is Bolted Connections?
A4)
A bolt may be defined as a metal pin with head at one end and a shank threaded at the other end to receive a nut as shown in Fig. Steel washers are usually provided under the bolt as well as under the nut to serve two purposes:
To distribute the clamping pressure of the bolted member, and
To prevent the threaded portion of the bolt from bearing on the connecting pieces
In order to assure proper functioning of the connections the parts to be connected must be tightly on clamped between the bolt head and nut. If the connections subjected to vibrations, the nuts must be locked in position. Bolted connections are quite similar to riveted connections in behavior but have some distinct advantages and disadvantages as follows:
Advantages
1. Connections can be made quickly so that the erection of the structure can be put to use immediately.
2. Less skilled labour required.
3. Making connections/joints is noiseless.
4. Need less labour
5. Accommodates minor discrepancies in dimensions.
6. Expansion and alteration can be done easily.
7. Working area required in the field is less.
Disadvantages
1. Tensile strength is reduced considerably due to stress concentrations and reduction of area at the root of the threads.
2. Cost of material is high about double that of rivets.
3. Rigidity of joints is reduced due to loose fit, hence their strength reduced.
4. Due to vibrations nuts are likely to loosen may danger to the safely of the structures.
Q5) What are types of bolts?
A5)
Types of Bolts
There are several types of bolts used to connect the structural elements. Some of the bolts commonly used are:
(a) Unfinished or black bolts
(b) Finished or turned bolts
(c) High strength bolts
a. Unfinished or Black Bolts
These are bearing type of bolts. Unfinished bolts are also called ordinary, common, rough or black bolts. These bolts are made from mild steel rods with square or hexagonal head. The shank is left unfinished i.e., rough as rolled shown in Fig.
The black bolts of nominal diameters are 16, 20, 24, 30 and 36 are commonly used and they are designated as M16, M20, M24 etc. The ratio of net tensile area at threads to nominal plain shank area of bolt is 0.78 given in IS-1367 (Part-1).
Nominal shank area

And net tensile area at threads
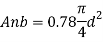
Where d is the nominal diameter of bolt. These bolts are used for light structures under static loads such as trusses, bracings and also temporary connection required during erections. IS 1367(Part-3) gives tensile properties of bolts given below in
b. Finished Bolt or Turned Bolt
These are similar to unfinished bolts, with the differences that the shank of these bolts is formed from anal rod. The surfaces of the bolts are prepared candy and are machined to fit in the hole.
Tolerances allowed are very small. These bolts have high shear and bearing resistance as compared to unfinished bolts. However, these bolts are absolute now days. The specifications for turned bolts are given in IS-2591-1969. These are also bearing type of bolts.
c. High Strength (HSFG)
The HSFG bolts are made from high strength steel rods. The surface of shank kept unfinished as in the case of black bolts. These bolts are tightened to a proof load using calibrated wrenches. Hence, they grip the members tightly.
In addition, nuts are prevented by using clamping devices. If the joint is subjected to shearing load, it is primarily resisted by frictional force between members and washers shown in Fig.
The shank of the bolt is not subjected to any shearing these results in to no-slippage in the joint. Hence such bolts can be used to connect members subjected to dynamic loads also. IS 3757- 1972 specifies various dimensions for such bolts and washers and nuts for such bolts.
Advantages of high strength bolts
- These provide a rigid joint. There is no slip between the elements connected.
- As load transfer is mainly by friction, the bolts are not subjected to shearing and bearing stresses. Thus, the possibility of failure at the net section is minimized.
- High fatigue strength since nuts are prevented from loosening and stress concentrations avoided due to friction grip.
- Smaller number of bolts results into smaller sizes of gusset plate.
- Alterations can be done easily.
Disadvantages of HSFG bolts
- Material cost is high.
- The special attention is to be given to workmanship especially to give them right amount of tension.
Q6) What are types of Bolted Joints?
A6)
These are two types of bolted joints (1) Lap joint (2) Butt joint
1) Lap Joint
It is simplest type of joints. The two members to be connected are overlapped and connected together such a joint is called a lap joint as shown in Fig. A single bolted lap joint and a double bolted lap joint are shown in Fig.
The load in the lap joint has eccentricity as centre of gravity of load in one member and the centre of gravity of load in the second member are not in the same line as shown in Fig. Single line, double line, chain bolting and zigzag bolting can be provided over a lap joint. Due to eccentricity the stresses are distributed un-evenly across the contact area between rivets and the members to be connected. This puts a limitation on use of lap joint.
2) Butt Joint
The two members to be connected are placed end to end and additional plate/plates provided on either one or both sides, called butt joint. If the cover plate is provided on one side called a single cover butt joint i shown in Fig. If the cover plates are provided on both the sides of main plates it is a called a double cover butt joint as shown in Fig. It is more desirable to provide a butt joint than a lap joint for two main reasons:
(1) In the case of double cover butt joint the total shear force to be transmitted by the members is split into two parts and the force acts on each half as shown in Fig. But in the case of lap joint there is an only one plane on which the shear force acts and therefore the shear carrying capacity of a bolt in a butt joint is double that of a bolt in lap joint.
(2) In the case of a double cover butt joint eccentricity of force does not exist and hence bending is eliminated, whereas it exists in the case of a lap joint.
Q7) Explain Load Transfer Mechanism?
A7)
The bolt includes the pressure via way of means of shear to the adjoining related plate in which its miles transferred to the plate via way of means of bearing among the bolt and the threshold of the hole.
The technique of switch of uncovered load from one structural detail to the alternative structural detail is known as load switch mechanism.
Based at the load direction the sample of load switch mechanism varies which in flip rely upon the sort of load which the shape has to switch.
As the burden is steadily carried out to the relationship, the primary pressure switch among the related plates could be via way of means of friction.
The friction capability is the end result of the everyday pressure (N) among the plates created via way of means of the bolt anxiety and the roughness of the touch surfaces (quantified via way of means of the friction coefficient, m).
From your statics course, you'll bear in mind that the friction capability equals mN. Once the carried-out pressure exceeds the friction capability (i.e., the nominal slip capability), the related participants slip relative to every different till they endure at the bolts. (Recall that the bolt diameters are smaller than the hollow diameters, which lets in this slip occur.) After slip takes place, the pressure is then transferred via way of means of bearing among the brink of the hollow and the bolt to the bolt.
The bolt incorporates the pressure via way of means of shear to the adjoining related plate wherein its miles transferred to the plate via way of means of bearing among the bolt and the brink of the hollow.
Failure of the relationship then effects from exceeding the shear capability of the bolt or one of the bearings restricts states mentioned with anxiety participants.
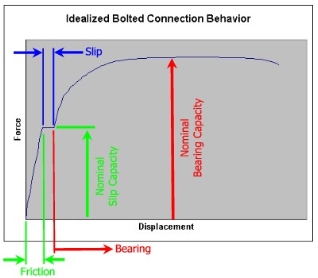
Each connection can have shear capacities:
The potential to hold load without slip and the potential to hold load without shear failure of the bolts
The first is known as the NOMINAL SLIP CRITICAL potential. The 2d is known as the NOMINAL BEARING potential.
The SCM gives equations for computing those portions for numerous bolts. In a cushy tight connection slip happens at lots smaller masses so the nominal slip potential is negligible. The handiest potential to be had for a cushy tight connection is the nominal bearing potential. To apprehend the pressure switch in bearing a chunk better, let's take a better have a take a observe a loose frame diagram of the bolt.
The plates every endure on a separate aspect of the bolt. We will idealize the pressure distribution as a uniformly disbursed load alongside the bolt in every case. The ensuing shear diagram is shown.
The most shear within side the bolt happens on the touch floor of the related plates. The energy ability of the bolt, then, is the shear energy of the bolt wherein the shear is at its most. If the most shear pressure exceeds the ability of the bolt, then the bolt will enjoy a shear failure.
The shear ability of the bolt may be idealized as a few fabrics primarily based totally shear energy instance’s location of the failure floor (i.e., the move sectional location of the bolt). The area of most shear within side the bolt is normally known as a SHEAR PLANE. The bolt depicted four is known as an "unmarried shear bolt" because it has handiest one vital shear plane. It is viable to have a couple of vital shear plane.
Five suggests a bolt that has vital shear planes. These bolts are stated to be in "double shear" and might switch two times as a whole lot pressure as a bolt in unmarried shear. It is viable to have even greater planes of shear.
Q8) What is Failure of Bolted Joints?
A8)
The bolted joint may fail in any one of the Following six ways, out of which some failures can be checked by adherence to the specifications of edge distances. Therefore, they are not much important whereas the others require due to consideration. They are given below:
(a) Shear Failure of Bolt
(b) Bearing Failure of Bolt/Plate
(c) Rupture/Tearing Failure of Plate
(d) Tension Failure of Bolt
(e) Splitting of Plates/Shear
(f) Block (shear) Failure of Plate End
A. Shear Failure of Bolt
A bolt may fail due to shearing. The shearing may take place at one section (known as single shear) or two sections (known as double shear) depending on the type of connection.
B. Bearing Failure of Bolt/Plate
The force in the connecting parts is transferred through the bolts by bearing action. Due to this action, the portion of the plate in contact with the bolt may get crushed and/or the portion of the bolt in contact with the hole edge may get deformed.
C. Rupture/Tearing Failure of Plate
This type of failure takes place along the weakest section of the plate due to the presence of holes. It may be prevented by having fewer holes at a section or the holes may be staggered. The tensile strength of a connection depends on the net sectional area of the plate.
D. Tension Failure of Bolt
In some connections, the bolts may be subject to tension. Fracture may take place at the root of thread since it is the weakest section.
E. Splitting of Plates/Shear Failure d Plate End
Bolts may have been placed at a lesser edge distance than required causing the plates of split f shear dot.
F. Block (Shear) Failure of Plate
A portion of the plate may fail by shearing and rupture known as block failure. The shearing of the block takes place in the direction of the force (along 1-2 and 3-4) whereas rupture of the block takes place perpendicular to the direction of force (along 2-3).
Q9) What is Specification for Bolted Joints?
A9)
1. Shear capacity of a bolt (cl. 10.3.3)
The design strength of a bolt in shear Vdsb is given by

Where,

2. Bearing capacity of a bolt
The design strength of a bolt bearing Vdpb is given by,

Where,

3. Tension capacity of a bolt
The design strength of a bolt in tension Tdb is the least of
1) The design strength of the bolt due to yielding of gross section
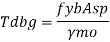
2) The design strength of bolt due to rupture at the net section

4. Tension capacity of plate
The design strength of a plate in tension due to rupture at the net section
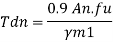
- If bolt holes are not staggered

b. If hoes are staggered
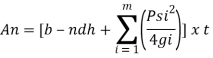
5. Design strength due to block shear
The block shear strength Tdh of the bolted connection is the least of
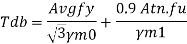
6. Bolt subjected to combined shear and tension
A bolt subjected to shear and tension simultaneously should satisfy the condition
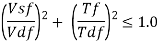
Where



Q10) Explain Bearing‐Type Connections?
A10)
A bearing kind connection is one wherein the bolts are in shear due to the fact there isn't giant sufficient friction within side the joint to save you slip. There are predominant classifications of bearing kind connections. The following bolt hole/slot kinds can be used with a bearing kind connection
Bearing kind connection is one wherein the bolts are in shear due to the fact there isn't massive sufficient friction within side the joint to save you slip. There are predominant classifications of bearing kind connections;
a. Connections with threads in shear plane (Type N)
b. Connections without threads in shear plane (Type X)
The following bolt hole/slot sorts can be used with a bearing kind connection;
a. STD: Standard spherical holes, d + 1/16” b. NSL: Long Slotted holes Paint is appropriate for all sorts of bearing connections. The price to put in friction kind connections is variable relying at the diploma of exertions required to supply the joint. In general, the relative charges of every form of joint are as follows (from most inexpensive to maximum expensive): a. Snug tightened (X): 1.0 b. Pre-tensioned (X): 1.2 c. Snug tightened (N): 1.3 d. Pre-tensioned (N): 1.6 e. Slip Critical (N or X): 3.1
The failure of connections with bearing bolts in shear entails both bolt failure and the failure of the linked plates. In this segment, the failure modes are defined alongside the codal provisions for layout and detailing shear connections. In connections made with bearing form of bolts, the behaviour is linear till
i) yielding takes area on the internet segment of the plate beneath blended anxiety and flexure or
Ii) Shearing takes area on the bolt shear aircraft
Iii) Failure of bolt takes area in bearing
Iv) Failure of plate takes area in bearing
v) Block shear failure occurs.
Of these, i) and v) are mentioned within side the bankruptcy on anxiety members. The last are defined below.
Shearing of bolts:
The shearing of bolts can take area within side the threaded part of the bolt and so the vicinity at the basis of the threads, additionally referred to as the tensile pressure vicinity At, is taken because the shear vicinity As. Since threads can arise within side the shear aircraft, the vicinity Ae for resisting shear ought to usually be taken because the internet tensile pressure vicinity, An, of the bolts. The shear vicinity is detailed within side the code and is generally approximately 0. Eight instances the shank vicinity. However, if it's far ensured that the threads will now no longer lie within side the shear aircraft then the overall vicinity may be taken because the shear vicinity.
Q11) What is Prying Action?
A11)
Prying movement is a phenomenon (in bolted creation only) wherein the deformation of a becoming beneath a tensile pressure will increase the tensile pressures within side the bolt. It is broadly speaking a characteristic of the energy and stiffness of the relationship elements.
The idea of prying motion may be maximum effortlessly provided in phrases of a T-stub loaded via way of means of a tensile pressure FT. The carried-out pressure isn't concentric to the centre of the bolt and extra forces (Q) can be evolved close to the flange tip, growing the bolt pressure itself. The anxiety brought about within side the bolts, from equilibrium, is accordingly FB= FT/2 + Q This phenomenon is illustrated
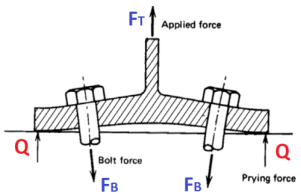
Prying motion in excessive electricity friction grip bolts is decreased most effective at a noticeably low degree of load and the behaviour of the bolts at final load isn't always drastically affected.
Even if prying motion is low, the distortion of the related components consequences in widespread bending of the bolt and nearby bending of the bolt nut or head.
Q12) What is Tensile Strength of Plate?
A12)
The design tensile strength Tdn of angle governed by rupture of net cross-sectional area is given by


Where,
= Shear lag coefficient
w = outstand leg width
Bs= shear lag width
For preliminary sizing the rupture strength of net section may be approximately taken as

Where,
= 0.6 for one or two bolt
An = Net area of the total cross section
Anc= Net area of the outstanding leg
Ago = Gross area of the outstanding leg
t = thickness of the leg
Lc= length of the end connection
Q13) Explain Efficiency of the Joint?
A13)
Joint Efficiency is a time period utilized in ASME codes for the layout of welded joints in strain vessels. Joint Efficiency refers back to the energy of a welded joint with admire to the energy of the bottom metal.
Concurrently, a performance of 0.50 suggests that the joint has 1/2 of the energy of the bottom metal
Joint Efficiency is a time period utilized in ASME codes for the layout of welded joints in stress vessels. Joint Efficiency refers back to the energy of a welded joint with recognize to the energy of the bottom metallic. A Joint Efficiency of 1.00 (100%) suggests that the weld has the equal energy of the bottom metallic, and its miles assumed as though it's miles seamless. Concurrently, a performance of 0.50 (50%) suggests that the joint has 1/2 of the energy of the bottom metallic. Joint performance is an essential thing to be taken into consideration within side the layout stage.
When designing the minimal thickness of the shell or the layout stress, the energy of the bottom metallic have to be increased through the Joint Efficiency value. According to ASME, the energy of the welding electrode is best taken into consideration all through the choice of the electrode.
Its energy has to be extra than or identical to the energy of the bottom metallic. If this circumstance is guaranteed, then the layout has to recall the weakest hyperlink within side the chain, that's the bottom metallic.
With that being said, ASME proposes statistical values for this parameter in Table UW-12 primarily based totally at the kind of joint, and the quantity of examination. Joint performance relies upon up on the kind of weld joint and the quantity of the NDT.
Q14) What is Combined Shear and Tension?
A14)
A bolt subjected to shear and tension simultaneously should satisfy the condition
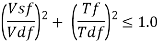
Where



Q15) Explain Slip‐Critical Connections?
A15)
Slip-vital joint, from structural engineering, is a form of bolted structural metal connection which is based on friction among the 2 linked factors in place of bolt shear or bolt bearing to sign up for structural factors.
Shear (and anxiety) masses may be transferred among structural factors with the aid of using both a bearing-kind connection or a slip-vital connection. In a slip-vital connection, masses are transferred from one detail to some other thru friction forces evolved among the faying surfaces of the relationship.
These friction forces are generated with the aid of using the intense tightness of the structural bolts maintaining the relationship together. These bolts, commonly anxiety manipulate bolts or compressible washing machine anxiety indicating kind bolts, are tensioned to a minimal required quantity to generate huge sufficient friction forces among the faying surfaces such that the shear (or anxiety) load is transferred with the aid of using the structural individuals and now no longer with the aid of using the bolts (in shear) and the relationship plates (in bearing). The "flip of the nut" approach is likewise extensively used to reap that nation of friction.
If slip-vital connections fail (through slipping), they revert to bearing-kind connections, with structural forces now transferred thru bolt shear and connection plate bearing.
Thus, a slippage failure of a slip-vital connection isn't always a catastrophic failure. However, slippage of a slip-vital connection in columns may also cause column instability. Slippage of a slip vital joint in a roof truss may want to bring about unintentional pending effects. The faying surfaces of slip-vital connections need to be nicely organized with a view to maximize friction forces among the surfaces joined.
Usually, this calls for cleaning, decaling, roughening, and/or blasting of the faying surfaces. Painting the faying surfaces with a category B primer additionally lets in being according with maximum of the layout that asks for Slip-vital joint.
Slip-Critical Bolted Connections Design of this kind of connection assumes that the fastener, below excessive preliminary tensioning, develops frictional resistance among the linked parts, stopping slippage notwithstanding outside load. Properly hooked up A307 bolts offer a few frictions, however because it isn't always reliable its miles ignored.
High-energy metal bolts tightened almost to their yield strengths, however, broaden substantial, dependable friction. No slippage will arise at layout hundreds if the touch surfaces are easy and freed from paint or have handiest scored galvanized coatings, inorganic zinc-wealthy paint, or metalized zinc or aluminum coatings. The AISC ‘‘Specification for Structural Steel for Buildings,’’ ASD and LRFD, lists allowable shear for excessive-energy bolts in slip-vital connections.
Though there certainly isn't always shear at the bolt shank, the shear idea is handy for measuring bolt capacity.
Since maximum joints in constructing production can tolerate tiny slippage, bearing type joints, which might be allowed tons better shears for the identical excessive-electricity bolts while the threads aren't in shear planes, may, for motives of economy, reduce the usage of slip-vital joints.
The ability of a slip-vital connection does now no longer rely on the bearing of the bolts in opposition to the perimeters in their holes. Hence, popular specification necessities for safety in opposition to excessive bearing stresses or bending within side the bolts can be ignored.
Q16) What is Combined Shear and Tension for Slip‐Critical Connections?
A16)
When a slip critical shear connection is also subject to tension the applied tensile force counteracts the bolt preload.
The slip resistance of the bolt must be reduced by the following factor:
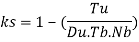
Where,
Tu= applied tensile load
Tb= minimum bolt pre-tension from AISC
Nb= number of bolts carrying load factored load tension Tn
Du=1.13
Q17) Explain Working Load Design?
A17)
In a standard sense, the layout load is the most quantity of something a gadget is designed to address or the most quantity of something that the gadget can produce, which can be very distinct meanings. For example, a crane with a layout load of 20 heaps is designed which will carry hundreds that weigh 20 heaps or less
His approach of layout became the oldest one. It is primarily based totally at the elastic principle and assumes that each metallic and urban and elastic and obey Hook’s law.
It way that the strain is without delay proportional to pressure as much as the factor of collapse
Based at the elastic principle, and assuming that the bond among metallic and urban is perfect, permissible stresses of the substances are obtained. The foundation of this approach is that the permissible stresses aren't passed any wherein within side the shape whilst its miles subjected to worst mixture of running loads. In this approach, the closing electricity of concrete and yield electricity or 0.2% evidence strain of metallic are divided via way of means of elements of protection to attain permissible stresses.
These elements of protection don't forget the uncertainties in production of those substances. As consistent with IS456, an element of protection of three is for use for bending compressive stresses in concrete and 1.78 for yield.
The important drawbacks of the running strain approach of layout are as follows:
(i) It assumes that concrete is elastic which isn't always proper because the concrete behaves in-elastically even on low stage of stresses.
(ii) It makes use of elements of protection for stresses simplest and now no longer for hundreds. Hence, this approach does now no longer provide proper margin of protection with appreciate to hundreds due to the fact we do now no longer understand the failure load.
(iii) It does now no longer use any component of protection with appreciate to hundreds. It means, there's no provision for the uncertainties related to the estimation of hundreds.
(iv) It does now no longer account for shrinkage and creep which can be time based and plastic in nature.
(v) This approach offers uneconomical sections.
(vi) It can pay no interest to the situations that get up on the time of collapse.
The running strain approach is quite simple and dependable however as according to IS 456:2000 the running strain approach is for use simplest if it isn’t always feasible to apply restricts nation approach of layout. Working strain approach is the primary approach and its expertise is important for information the standards of layout.
Q18) Explain Design of eccentric bolted connections?
A18)
Design steps:
Step 1) Design strength of the plate due to rupture of the net section
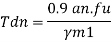
As bolt are not staggered

Step 2) Design shear strength of the bolt

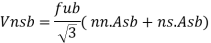
Step 3) Design bearing strength of the bolt



Step 4) Design strength due to block shear
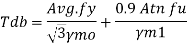
Q19) Determine the ultimate load carrying capacity in tension of lap joint shown in fig. If bolt threads are outside of the shear plane. Use M16 bolts of product grade C and property class 4.6 the yield and ultimate strengths of the flats are 250 MPa and 410 MPa respectively.
A19)
Ultimate strength of bolt= 4x100= 400MPa
Since property of class bolt is 4.6
The diameter of the hole (d0) = 16+2 = 18m
- Design strength of the plate due to rupture of the net section
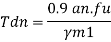
As bolt are not staggered



2. Design shear strength of the bolt


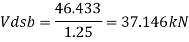
3. Design bearing strength of the bolt





4. Design strength due to block shear
Avg= 2(80 +30) x 12= 2640 mm^2
Avn= 2(80+30-1.5X18) x 12= 1992 mm^2
Atg= 60 x 12= 720 mm^2
Atn= (60-18) x 12 = 504 mm^2
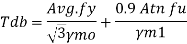
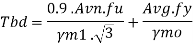

Ultimate load carrying capacity of the joint is the least of




Ultimate load carrying capacity = 148.58 kN
Q20) Explain the terms Simple Welded Connections, Types, Symbols?
A20)
Simple Welded Connections
Welding is the process of becoming a member of steel quantities within side the molten country without or with pressure.
Electric-arc-welding is typically used.
Part of steel to be welded is melted through the usage of electric powered arc or oxyacetylene flame at the side of a weld rod.
Arc warmth will soften each the steel element and rod on the equal time.
Fusion takes place as welding rod fabric flows throughout the arc.
Welding rod used can be shielded or unshielded.
In the shielded kind, electrode could be lined with mineral compounds (flux) generating a gaseous defend which enables to keep away from oxygen and as a result stabilizing the arc.
Shielded kind improves the fine of work.
Types of welded connection
There are two types of welded connection
- Butt weld
- Fillet weld
1. Butt weld
Butt weld is also known as groove weld. The various shape of the groove made are
- Square butt weld
- Single V butt weld
- Double V butt weld
- Single U butt weld
- Double U butt weld
The size of butt weld is the effective throat thickness. In case of double butt weld when complete penetration is achieves, the thickness of weld is taken as thickness of thinner plate.
For single butt weld when complete penetration is not achieved the thickness of weld is taken as 5/8 times thickness of thinner plate.
Effective length of butt weld is equal to length of full-size weld
Minimum length of weld= 4x size of weld
2. Fillet weld
Fillet weld is approximately triangular cross sectional joining two surfaces which are perpendicular to each other standard fillet weld when the cross section of fillet weld is isosceles triangle.
Minimum size of fillet weld is 3 mm
In drawing only effective length is shown. Actual weld length is equal to effective length + twice the size of weld.
Design strength of fillet weld is

Symbol
1. Fillet welds

The fillet weld (pronounced "fill-it") is used to make lap joints, nook joints and T joints. As its image suggests, the fillet weld is kind of triangular in cross-section, despite the fact that its form isn't always constantly a proper triangle or an isosceles triangle.
Weld metallic is deposited in a nook fashioned through the fit-up of the 2 individuals and penetrates and fuses with the bottom metallic to shape the joint. (Note: for the sake of graphical clarity, the drawings underneath do now no longer display the penetration of the weld metallic. Recognize, however, that the diploma of penetration is essential in figuring out the pleasant of the weld.)
2. Groove welds
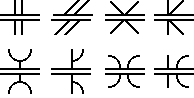
The groove weld is usually used to make part-to-part joints, even though it's also regularly utilized in nook joints, T joints, and joints among curved and flat pieces. As recommended via way of means of the type of groove weld symbols, there are numerous methods to make a groove weld, the variations relying typically at the geometry of the components to be joined and the coaching in their edges. Weld steel is deposited inside the groove and penetrates and fuses with the bottom steel to shape the joint.
(Note: for the sake of graphical clarity, the drawings beneath commonly do now no longer display the penetration of the weld steel. The numerous forms of groove weld are:
3. Square groove welds
The groove is created via way of means of both a decent healthy or a moderate separation of the edges. The quantity of separation, if any, is given at the weld symbol
.
4. V-groove welds
The edges of each portion are chamfered, both singly or doubly, to create the groove. The attitude of the V is given at the weld symbol, as is the separation on the root (if any).
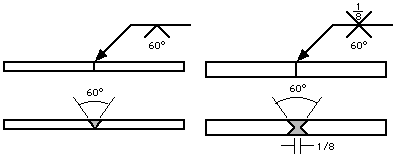
Q21) Explain Welding Process?
A21)
Welding is a fabrication procedure wherein or extra elements are fused collectively via heat, stress or each forming a be a part of because the elements cool. The finished welded joint can be known as a weldment. The 4 major varieties of welding are:
- Gas Metal Arc Welding (GMAW/MIG)
- Gas Tungsten Arc Welding (GTAW/TIG)
- Shielded Metal Arc Welding (SMAW)
- Flux Cored Arc Welding (FCAW
- Gas Metal Arc Welding (GMAW/MIG)
Also called Metal Inert Gas or MIG welding, this technique makes use of a skinny cord as an electrode. The cord heats up as it's far fed via the welding tool and toward the welding site. Shielding fuel line need to be used to defend the weld from contaminants within side the air.
Typically, this comes within side the shape of carbon dioxide, oxygen, argon or helium. This approach is frequently used to paintings on metals which include stainless steel, copper, nickel, carbon steel, aluminum, and more. Of all of the welding processes, this one is maximum famous throughout the development and car industries.
Gas steel arc welding is thought to be one of the less difficult welding strategies to learn, which makes it an exceptional vicinity of consciousness for starting welders. It additionally requires minimum cleanup, gives excessive welding speeds and higher manipulate over thinner substances.
Some downsides related to this sort of welding method revolve across the charges of having protective fuel line in conjunction with an incapacity to weld thicker metals or carry out vertical or overhead welding.
2. Gas Tungsten Arc Welding (GTAW/TIG)
This sort of welding method, additionally called Tungsten Inert Gas or TIG welding, is typically used to weld collectively skinny and non-ferrous substances like aluminum, copper, lead, or nickel. It’s typically carried out to bicycle or plane manufacturing. Unlike different styles of welding processes, TIG welding makes use of a non-consumable tungsten electrode to provide the weld. You will nevertheless want an outside fuel line supply, normally argon or a mixture of argon and helium. This is taken into consideration one of the maximum hard welding techniques to master, and one which produces the maximum great welds.
Because there may be simplest a tiny vicinity among the arc and the vicinity being welded, it takes a sizeable quantity of precision and ability to complete. Welds born of this technique are recognized to be extraordinarily strong.
3. Shielded Metal Arc Welding (SMAW)
This sort of welding manner is based on a guide approach the use of a consumable electrode covered in flux. This approach has a tendency to be maximum famous amongst home-store welders. This manner is likewise extra informally referred to as stick welding.
The nickname references the electrode used to weld the metallic, which comes within side the shape of a “stick.” Because shielded metallic arc welding calls for minimum equipment, it’s one of the maximum low-value methods round. This sort of welding does now no longer require defensive fuel line and may be accomplished exterior within side the wind or rain. It additionally works properly on dust and rusty materials.
That said downsides do exist. Stick welds don’t generally produce the exceptional fine products. They are susceptible to porosity, cracks, and shallow penetration. In general, stick welds are much less long lasting than what different forms of welding will produce.
4. Flux Cored Arc Welding (FCAW)
Similar to MIG welding, flux cored arc welding revolves round a non-stop cord feed manner. There are separate methods related to flux cored arc welding. One includes using defensive fuel line at the same time as the alternative is based on self-defensive marketers produced while fluxing marketers decompose within side the cord.
This sort of welding is thought for being cheaper and clean to learn. Much just like the MIG welding manner, it’s a top-notch manner for starting welders to kick off their careers within side the field
It additionally permits welders to carry out their painting’s exterior (windy situations won’t have an effect on the weld). The semi-automated arc gives excessive welding velocity and portability, making it a famous manner to hire on production projects.
Q22) What is Weld Defects?
A22)
Defects are not unusual place in any sort of manufacturing, welding including. In the system, there may be deviations within side the form and length of the metallic structure
It may be resulting from using the wrong welding system or incorrect welding technique. So beneath we’ll find out about the 7 maximum not unusual place welding defects, their types, reasons and remedies.
- Weld Crack
The maximum extreme kind of welding illness is a weld crack and it’s now no longer everyday nearly through all requirements within side the industry. It can seem at the surface, within side the weld metallic or the place laid low with the acute heat. There are specific sorts of cracks, relying at the temperature at which they arise: 7 maximum not unusual place welding defects and causes
- Hot cracks.
These can arise at some stage in the welding manner or at some stage in the crystallization manner of the weld joint.
The temperature at this factor can upward thrust over 10,000C.
B. Cold cracks.
These cracks seem after the weld has been finished and the temperature of the metallic has long gone down. They can shape hours or maybe days after welding. It mainly takes place while welding steel. The motive of this illness is generally deformities within side the shape of steel.
C. Crater cracks.
These arise on the quit of the welding manner earlier than the operator finishes a by skip at the weld joint. They generally shape close to the quit of the weld. When the weld pool cools and solidifies, it wishes to have sufficient extent to conquer shrinkage of the weld metallic. Otherwise, it's going to shape a crater crack.
Causes of cracks:
- Use of hydrogen while welding ferrous metals.
- Residual strain because of the solidification shrinkage.
- Base steel contamination.
- High welding pace however low current.
- No preheat earlier than beginning welding.
- Poor joint design.
- An excessive content material of sulfur and carbon within side the steel.
Remedies:
- Preheat the steel as required. Provide right cooling of the weld area.
- Use right joint design.
- Remove impurities.
- Use suitable steel.
- Make positive to weld an enough sectional area.
- Use right welding pace and amperage current.
- To save you crater cracks ensure that the crater is nicely crammed.
2. Porosity
Porosity takes place due to weld steel contamination. The trapped gases create a bubble-crammed weld that will become vulnerable and may with time collapse.
Causes of porosity:
- Porosity Inadequate electrode deoxidant.
- Using an extended arc.
- The presence of moisture.
- Improper fuel line shield. Incorrect floor treatment.
- Use of too excessive fuel line waft.
- Contaminated floor.
- Presence of rust, paint, grease or oil.
Remedies:
- Clean the substances earlier than you start welding.
- Use dry electrodes and substances.
- Use accurate arc distance.
- Check the fuel line waft meter and ensure that it’s optimized as required with right with strain and waft settings.
- Reduce arc journey speed, in order to permit the gases to escape.
- Use the proper electrodes.
- Use a right weld technique.
3. Undercut
This welding imperfection is the groove formation on the weld toe, decreasing the cross-sectional thickness of the bottom metal. The end result is the weakened weld and work piece.
Causes:
- Undercut Too excessive weld current.
- Too speedy weld speed.
- The use of a wrong angle, that allows you to direct extra warmness to unfastened edges.
- The electrode is just too large.
- Incorrect utilization of fuel line shielding. Incorrect filler metal. Poor weld technique.
Remedies:
- Use right electrode angle.
- Reduce the arc length.
- Reduce the electrode’s tour speed, however it additionally shouldn’t be too slow.
4. Incomplete Fusion
This form of welding disorder happens while there’s a loss of right fusion among the bottom steel and the weld steel. It also can seem among adjacent weld beads. This creates an opening within side the joint that isn't always packed with molten steel.
Causes:
- Incomplete fusion Low warmth input.
- Surface contamination. Electrode perspective is inaccurate.
- The electrode diameter is inaccurate for the cloth thickness you’re welding.
- Travel velocity is just too fast.
- The weld pool is just too massive and it runs in advance of the arc.
Remedies:
- Use a sufficiently excessive welding contemporary with an appropriate arc voltage.
- Before you start welding, smooth the steel.
- Avoid molten pool from flooding the arc.
5. Incomplete Penetration
Incomplete penetration takes place while the groove of the metallic isn't always crammed completely, which means the weld metallic doesn’t absolutely increase thru the joint thickness.
Causes:
- Incomplete penetration
- There become an excessive amount of area among the metallic you’re welding together.
- You’re shifting the bead too quickly, which doesn’t permit sufficient metallic to be deposited within side the joint.
- You’re the usage of a too low amperage setting, which ends up within side the present day now no longer being sturdy sufficient to nicely soften the metallic.
- Large electrode diameter.
- Misalignment.
- Improper joint.
Remedies:
- Use right joint geometry.
- Use a nicely sized electrode.
- Reduce arc tour speed.
Q23) What is Inspection of Welds?
A23)
The welding inspection characteristic is regularly divided into 3 areas. First, and regularly the least utilized, is pre-weld inspection. Second, inspection at some stage in the welding operation can regularly save you issues within side the finished weld thru verification of the welding situations and procedural requirements.
- Pre-Weld Inspection
This inspection is performed previous to the begin of the welding operation. This form of inspection is normally related to checking the training of the welding joint and verification of parameters that could be tough or not possible to verify at some stage in or after welding.
This is the vicinity of inspection wherein we are able to excellent introduce controls that can save you faulty welding. Some regions of pre-weld inspection are joint training inspection/pre-weld setup.
This might also additionally contain the dimensional inspection of root openings. Root openings which are too tight can purpose insufficient root penetration. Root openings which are too huge can purpose over- penetration.
Groove weld bevel angles, if too small, might also additionally purpose loss of fusion, and if too huge, can bring about distortion of the weld joint from overheating and immoderate shrinkage pressure. Joint alignment (misalignment of the weld joint) can bring about issue in generating a legitimate weld and pressure attention at its vicinity, ensuing in a discount of fatigue life.
Plate floor situation and cleanliness, pre-cleansing previous to welding, can regularly be of excessive importance. Improper or insufficient cleansing can bring about unacceptable stages of porosity within side the finished weld. Other pre-weld inspections might also additionally encompass preheat verification, temperature and heating method, presence and vicinity of warmth remedy tracking devices, and kind and efficacy of fuel line purging, if applicable.
Pre-weld inspection may encompass assessment and verification of documentation, fabric certification, filler alloy certification, welder overall performance qualification, welding process qualification, and welder and weld identification, for traceability, if applicable.
2. Inspection During Welding
This is the inspection this is executed throughout the welding operation and is involved specifically with the necessities of the welding method specification (WPS). This inspection consists of such objects as inter pass cleansing techniques, inter pass temperature control, welding modern settings, welding journey speed, protective fuel line type, fuel line float rate, and welding sequence, if applicable. Also, any environmental situations that could have an effect on the first-class of the weld which include, rain, wind, and intense temperatures
3. Post-Weld Inspection
This inspection commonly carried out to confirm the integrity of the finished weld. Many non-unfavorable testing (NDT) techniques are used for post-weld inspection. However, even supposing the weld is to be subjected to NDT, it's far commonly sensible to behavior visible inspection first. One motive for that is that floor discontinuities, which can be detected via way of means of visible inspection, can once in a while motive misinterpretation of NDT outcomes or cover different discontinuities inside the frame of the weld.
The maximum not unusual place welding discontinuities determined throughout visible inspection are situations which include undersized welds, undercut, overlap, floor cracking, floor porosity, beneath fill, incomplete root penetration, immoderate root penetration, burn through, and immoderate reinforcement.
A right pre-weld inspection plan might also additionally offer us with a super possibility to save you welding troubles earlier than they start, via the detection and correction of conditions that could motive welding troubles or welding discontinuities.
Inspection performed in the course of the welding operation can frequently discover troubles earlier than they strengthen and additionally facilitates to offer self-belief within side the very last welded product.
Post-weld inspection can frequently offer a cheap technique of figuring out a weld’s acceptability in regards to many floor discontinuities.
Q24) What is Assumptions in the Analysis of Welded Joints?
A24)
- Welds connecting numerous joints are homogenous, isotropic and elastic elements
- Components linked with the aid of using weld are inflexible and their deformations are neglected
- Best stresses because of outside forces are considered.
Q25) What is Design of Groove Welds?
A25)
Groove weld is also known as butt weld.
Butt welds shall be treated as parent metal with a thickness equal to the throat thickness, and the stresses shall not exceed those permitted in the parent metal.
Butt welds
Check for the combination of stresses in butt welds need not be carried out provided that:
a) Butt welds are axially loaded, and
b) In single and double bevel welds the sum of normal and shear stresses does not exceed the design normal stress, and the shear stress does not exceed 50 percent of the design shear stress.
Combined bearing, bending and shear
Where bearing stress, for is combined with bending (tensile or compressive), f, and shear stresses, q under the most unfavorable conditions of loading in butt welds, the equivalent stress, fe as obtained from the following formula, shall not exceed the values allowed for the parent metal:

Where
Fe = equivalent stress;
Fb = calculated stress due to bending, in N/am²;
Fbr= calculated stress due to bearing, in N/mm²; and
q=shear stress, in N/mm².
Q26) What is Design of Fillet Welds?
A26)
1. Effective Throat
a. Calculation: The powerful throat will be the shortest distance from the joint root to the weld face of the diagrammatic weld (see Annex I). Note: See Annex II for formulation governing the calculation of powerful throats for fillet welds in skewed T-joints. A tabulation of measured legs (W) and ideal root openings (R) related to powerful throats (E) has been furnished for dihedral angles among 60° and 135°.
b. Shear Stress
Stress at the powerful throat of fillet welds is taken into consideration as shear pressure irrespective of the path of the application.
c. Reinforcing Fillet Welds
The powerful throat of a mixture partial joint penetration groove weld and a fillet weld will be the shortest distance from the joint root to the weld face of the diagrammatic weld minus 1/eight in. (three mm) for any groove element requiring such deduction.
2. Length
a. Effective Length (Straight):
The powerful period of a directly fillet weld will be the general period of the huge fillet, together with boxing. No discount in powerful period will be assumed in layout calculations to permit for the begin or forestall crater of the weld.
b. Minimum Length:
The minimal powerful duration of a fillet weld will be at the least 4 instances the nominal length, or the powerful length of the weld will be taken into consideration now no longer to exceed 25% of its powerful duration.
c. Effective Area:
The powerful vicinity will be the powerful weld duration improved with the aid of using the powerful throat. Stress in a fillet weld will be taken into consideration as implemented to this powerful vicinity, for any course of implemented load.
d. Minimum Leg Size:
Minimum size leg required fillet weld
E. Maximum Fillet Weld Size:
The most fillet weld length precise alongside edges of fabric will be the following: (1) the thickness of the bottom steel, for steel much less than 1/four in. (6 mm) thick (Detail A) (2) 1/sixteen in. (2 mm) much less than the thickness of base steel, for steel 1/four in. (6 mm) or extra in thickness (Detail B), until the weld is specific on the drawing to be constructed out to attain complete throat thickness. In the as-welded condition, the gap among the fringe of the bottom steel and the toe of the weld might also additionally be much less than 1/sixteen in. (2 mm), furnished the weld length is virtually verifiable.
Q27) Explain Fillet Weld Applied to the Edge of a Plate or Section?
A27)
Where a fillet weld is applied to the square edge of a part, the specified size of the weld should generally be at least 1.5 mm less than the edge thickness in order to avoid washing down of the exposed arise
Where the fillet weld is applied to the rounded toe of a rolled section, the specified size of the weld should generally not exceed 3/4 of the thickness of the section at the toe
Where the size specified for a fillet weld is such that the parent metal will not project beyond the weld, no melting of the outer cover or covers shall be allowed to occur to such an extent as to reduce the throat thickness
When fillet welds are applied to the edges of a plate, or section in members subject to dynamic loading, the fillet weld shall be of full size with its leg length equal to the thickness of the plate or section
End fillet weld, normal to the direction of force shall be of unequal size with a throat thickness not less than 0.5t, where t is the thickness of the part. The difference in thickness of the welds shall be negotiated at a uniform slope.
Q28) Explain Fillet Weld for Truss Members?
A28)
This sort of weld is used while the participants to be related overlap every different. A fillet weld is a weld of about triangular pass segment becoming a member of surfaces about as proper angles to every different in lap joint or tee joint. A fillet weld is proven.
When the pass segment of fillet weld is 45˚, isosceles triangle as proven its miles called a general fillet weld. The general 45˚ fillet weld is commonly used. When the pass segment of the fillet weld is 30˚ and 60˚ triangle as proven its miles called a unique fillet weld.
A fillet weld is called as concave fillet weld or convex fillet weld or miter fillet weld relying at the weld face in concave or convex or about flat as respectively.
A fillet weld is called as everyday fillet weld or deep penetration fillet weld relying upon the intensity of penetration past the foundation is much less than 2. Four mm or greater respectively.
Q29) What are Design of Intermittent Fillet Welds, Plug and Slot Welds?
A29)
A. Design if intermittent fillet weld
The minimal duration of an intermittent fillet weld shall be 1-half of in. (forty mm). Minimum length: The minimal powerful duration of a fillet weld will be at the least 4 instances the nominal length, or the powerful length of the weld will be taken into consideration now no longer to exceed 25% of its powerful duration
B. Design of plug and slot weld
1) Effective Area:
The powerful place will be the nominal place of the hollow or slot within side the aircraft of the faying surface
2) Minimum Spacing (Plug Welds):
The minimal middle-to-middle spacing of plug welds will be 4 instances the diameter of the hollow.
3) Minimum Spacing (Slot Welds):
The minimal spacing of strains of slot welds in a route transverse to their duration will be 4 instances the width of the slot.
Minimal middle-to-middle spacing in a longitudinal route on any line will be instances the duration of the slot.
4) Slot Ends:
The ends of the slot will be semicircular or shall have the corners rounded to a radius now no longer less than the thickness of the component containing it, besides those ends which expand to the brink of the component.
5) Prequalified Dimensions:
For plug and slot weld dimensions which are prequalified, see three.
Prohibition in Q&T Steel. Plug and slot welds aren't authorized in quenched and tempered steels
6) Limitation:
Plug or slot weld length layout will be primarily based totally on shear within side the aircraft of the faying surfaces.
Q30) Explain Stresses Due to Individual Forces, Combination of Stresses?
A30)
Stresses Due to Individual Forces
When subjected to either compressive or tensile or shear force alone, the stress in the weld is given by:
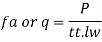
Where
f = calculated normal stress due to axial force, in N/mm²;
q = shear stress, in N/mm²;
P = force transmitted (axial force N or the shear force Q);
Tt= effective throat thickness of weld, in mm; and
Lw = effective length of weld, in mm.
Combination of Stresses
Fillet welds
When subjected to a combination of normal and shear stress, the equivalent stress f shall satisfy the following:

Where
Fa = normal stresses, compression or tension, due to axial force or bending moment and
q = shear stress due to shear force or tension (see 10.5.9).
Check for the combination of stresses need not be done for:
a) side fillet welds joining cover plates and flange plates, and
b) fillet welds where sum of normal and shear stresses does not exceed f (see
Butt welds
Check for the combination of stresses in butt welds need not be carried out provided that:
a) butt welds are axially loaded, and
b) in single and double bevel welds the sum of normal and shear stresses does not exceed the design normal stress, and the shear stress does not exceed 50 percent of the design shear stress.
Combined bearing, bending and shear
Where bearing stress, for is combined with bending (tensile or compressive), f, and shear stresses, q under the most unfavorable conditions of loading in butt welds, the equivalent stress, fe as obtained from the following formula, shall not exceed the values allowed for the parent metal:

Where
Fe = equivalent stress;
Fb = calculated stress due to bending, in N/am²;
Fbr= calculated stress due to bearing, in N/mm²; and
q=shear stress, in N/mm².
Q31) What are Failure of Welds?
A31)
Failure of a welded joint may be of types:
(a) The ones "failed' in the course of inspection after fabrication,
(b) The ones failed in the course of carrier.
The defects which can also additionally fail a weld joint in the course of carrier if left in an aspect undetected are the following: creaks, loss of penetration, loss of fusion, porosity etc.
Among those defects, the linear ones which include the shortage of penetration, loss of aspect wall fusions etc. and particularly the cracks are extra harmful.
Linear defects at the floor or within side the subsurface vicinity is once more extra critical due to the fact the 2 modes of screw ups e.g., fatigue and strain corrosion cracking which might be the maximum ordinary mechanisms of screw ups in business additives W2 originate from the floor or subsurface regions.
Q32) What is mean by Distortion of Welded Parts?
A32)
Distortion in weld outcomes from the enlargement and contraction of the weld steel and adjoining base steel in the course of the heating and cooling cycle of the welding process
Doing all welding on one aspect of a component will motive a lot greater distortion than if the welds are alternated from one aspect to the other.
Distortion in a weld effect from the growth and contraction of the weld metallic and adjoining base metallic at some point of the heating and cooling cycle of the welding process.
Doing all welding on one facet of an element will motive a whole lot greater distortion than if the welds are alternated from one facet to the other. During this heating and cooling cycle, many elements have an effect on shrinkage of the metallic and result in distortion, together with bodily and mechanical homes that extrade as warmth is applied.
For example, because the temperature of the weld region increases, yield strength, elasticity, and thermal conductivity of the metal plate decrease, even as thermal growth and unique warmth increase
These changes, in turn, have an effect on warmth glide and uniformity of warmth distribution.
Reasons for Distortion
To apprehend how and why distortion happens at some point of heating and cooling of a metallic, take into account the bar of metal.
As the bar is uniformly heated, it expands in all directions. As the metallic cools to room temperature, it contracts uniformly to its unique dimensions.
Q33) What is difference between Fillet Weld Vs Butt Weld?
A33)
Sr. No | Butt weld | Fillet weld |
1 | Butt weld is also known as groove weld. The various shape of the groove made are: 1) Square butt weld 2) Double V butt weld 3) Single V butt weld 4) Single U butt weld 5) Single J butt weld | Fillet weld is a weld of approximately triangular cross section joining two surface which are perpendicular to each other. Standard fillet weld when the cross section of fillet weld is isosceles triangles. |
2 | The size of butt weld is the effective throat thickness. In case of double butt weld when complete penetration is achieved, the thickness of weld is taken as thickness of thinner plate. | Minimum size of fillet weld is 3 m
|
3 | Effective length of butt weld is equal to length of full-size weld.
| In drawing only effective length is shown. Actual weld length is equal to effective length plus twice the size of the weld. Effective length < 4x size of weld |
4 | Minimum length of weld = 4 size of weld. | Design strength of fillet weld fwd= fwn/ ![]()
|
Q34) What is difference between Welded Jointed Vs Bolted and Riveted Joints?
A34)
A. Welded joints Vs Bolted joint
Sr. No | Welded joint | Bolted joint |
1. | Good aesthetical look | Bad aesthetical look |
2 | Skilled labour required | Skilled labour is not required |
3 | Difficult in inspect welded joint | Inspection of connection is very easy |
4 | Not necessary to drill the hole | Necessary to drill the hole |
5 | Welding requirement are more expensive it required initial investment | Less rigid connection |
6 | More rigid connection | Not required initial investment |
7 | Connection required constant power supply | Connection can be done at site |
B. Welded joint Vs Riveted joint
Sr. No | Welded joint | Riveted joint |
1 | Skilled labour required | It is related to very excessive stage of noise pollution
|
2 | Difficult in inspect welded joint | There is a want to warmth the rivet until purple warm color.
|
3 | Not necessary to drill the hole | Skilled labors are vital to investigate the relationship.
|
4 | Welding requirement are more expensive it required initial investment | The fee to get rid of the poorly hooked up rivet could be very excessive.
|
5 | More rigid connection | The excessive-fee set up within side the connection.
|
Q35) Explain Design of eccentric welded connections?
A35)
Steps for design of welded connection:
Step 1) Assume maximum size of weld =S
Thickness of member-1.5 mm
Step 2) calculate design shear strength of weld

Consider fu = 410 MPa if not given
= 1.25 for shop weld
= 1.5 field weld
Step 3) calculate strength of weld /mm
= fwd x thickness of weld = fwd (0.7 x S)
Step 4) calculate length of weld required Lw
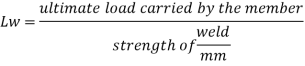
Step 5) arrange the weld length taking moment of weld length @ c.g. And equating them for equilibrium
Q36) A 20 mm thick plate is connected to 18 mm thick plate by 240 mm long butt weld. Determine the strength of joint i) single U butt weld is used ii) double U butt weld is used.
Consider fu= 410N/mm^2
A36)
Given: Le= 240mm
i) For single U butt weld
As complete penetration is not achieved
t = thickness of weld
= 5/8 X thickness of thinner plate
= 5/8 X 18 = 11.25 mm
Design strength of weld

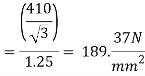
Total strength of weld


Ii) For Double U butt weld
As complete penetration is achieved
T= thickness of weld= thickness of thinner plate= 18mm
Total strength of weld

