Unit - 2
Operating Principles and Relay Construction
Q1) What are the different classification of Relay?
A1) The actuating quantity is normally in electrical signal. Sometimes the actuating quantity may be pressure and temp. Protective relay can be classified as
- According to the function in protection scheme.
- According to the nature of actuating quantity.
- According to the connection of the sensing element
- According to the method by which the relay acts upon the circuit breaker
Generally, the electrical protective relays can be broadly classified in two categories
(a) Electromagnetic relays- Electromagnetic relays are those relays which are operated by electromagnetic action. Modern electrical protection relays are mainly microprocessor based, but still electromagnetic relay holds its place. It will take much longer time to be replaced the all electromagnetic relays by microprocessor based static relays. So before going through detail of protection relay system we should review the various types of electromagnetic relays.
(b) Static relays- A relay in which the measurement or comparison of electrical quantities are done in a static network. The output signal operates a tripping device which may be electronic, semiconductor or electromagnetic. The static relays are classified according to the types of measuring units or the comparator 1) Electronic relays 2) Transducer (magnetic amplifier relay) 3) Rectifier bridge relay 4) Transistor relay 5) Hall effect relay 6) Gauss effect relay.
Q2) Explain the different type of Electromagnetic Relays?
A2) Depending upon working principle the electromagnetic relays can be divided into following types of electromagnetic relays.
- Attraction Armature Type Relay
This has four types i.e., plunger, hinged armature, balanced beam and moving iron polarized. These are the simplest types which responds to AC and DC.
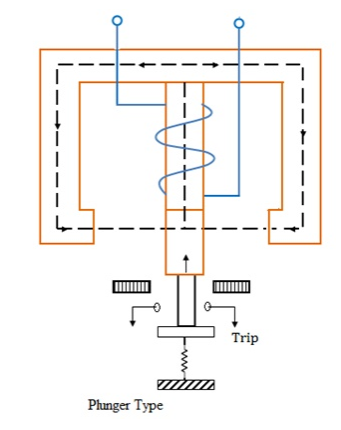
The force of attraction is given by-

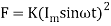
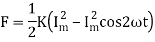
Where K is a constant & is pulsating
The coil is energized by current or voltage, a proportionate operating quantity, which produces a magnetic flux, thereby creating an electromagnetic force. This force is proportional to the square of the flux in the air gap or square of the current. This force increases, as the armature approaches the pole of electromagnet. This type of relay is used for protection of small machines and also used for auxiliary relays such as indicating relays (flags) alarm and annunciator relays etc.
Ii. Induction Disc Type Relay
a. Watt Meter Type or Non-Directional Relay- It has a metallic disc free to rotate between the poles of two electro magnets. The spindle of this disc carries a moving contact which bridges two fixed contacts when the disc rotates through an angle, which is adjustable between 0o to 360o. By adjusting this angle, the travel of moving contact can be adjusted so that the relay can be given any desired time setting which is indicated by a pointer. The dial is calibrated from 0-1. The relay time from name plate cure is to be multiplied by time multiplier setting.
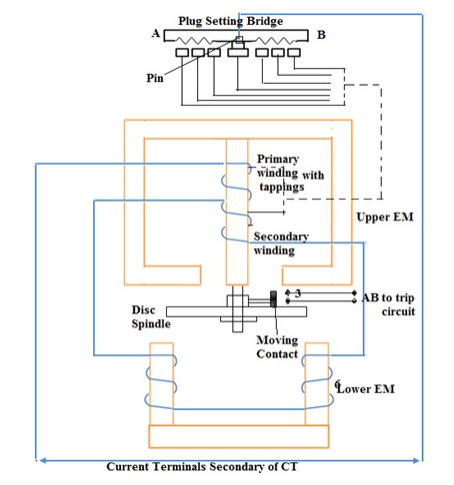
The upper magnet has two windings. The primary coil is connected to the secondary of CT through tappings in it. These tappings are connected to plug Settings Bridge. The secondary is connected to the lower electro magnet. The torque exerted on the disc is due to the interaction of eddy current produced therein by the flux from the upper EM and the lower EM. The relay setting is 50% to 200% in steps of 25%.
b. Shaded Pole Type or Non Directional Relay
The rotating disc is made of aluminum. In the above type one half of each of electromagnet shown in fig, is surrounded by a copper band called as the shading ring. The shaded portion of the pole products a flux which is displaced in space and time w.r.t the flux produced by the unshaded portion of the pole. These two alternating fluxes cut the disc and produce eddy currents in it. Torques are produced by the interaction of each flux with the eddy current produced by the other flux. The resultant torque causes the disc to rotate.
A spring is used to supply the resetting torque. A permanent magnet is employed to produce eddy current braking to the disc. The braking torque is proportional to the speed of the disc. When the operating current exceeds pick-up value, driving torque is produced and the disc accelerates to a speed where the braking torque balances the driving torque. The disc rotates at a speed proportional to the driving torque.
At a current below the pick-up value, the disc remains stationary by the tension of the control spring acting against the normal direction of disc rotation. The disc rests against a backstop. The position of the back-stop is adjustable. So that the relay-contacts travel distance can be varied according to need. This is called time-setting of the relay.
Iii. Induction Cup Type Relay
It is a double actuating quantity relay (current & voltage) which is highly sensitive, high speed, steady & non-vibrating torque and ration of re-set to pickup is high (above 95%) as well as it has operating time less than 0.01 seconds.
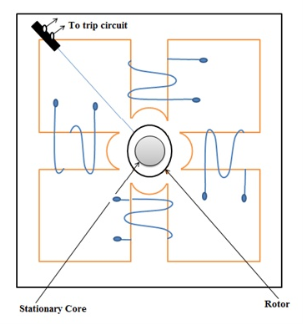
The operating is similar to induction motor. It consists of a stationary rotor iron core and moving rotor conductor (cup). The moving element is a hollow cylinder or cup which turns on its axis. The driving element is a four or eight pole structure placed radially around the outside of the cylinder and joined by a yoke. To shorten the air-gap, a stationary iron core is placed inside the rotate cylinder.
It is a high speed induction relay since inertia is less. The two pairs of coils are displaced by 90o. When these coils are excited, a rotating magnetic field is produced. The rotor cuts the magnetic field and an emf is induced in the rotor. Which results in a current due to short circuit nature of the rotor. A torque is produced due to the interaction between the rotating flux and the induced current which causes the rotation of the cylinder. The movement of the rotor closes the trip circuit. The torque produced is proportional to |I1||I2| sin α or Φ1 Φ2 sin α, where Φ1 Φ2 are the fluxes due to excitation currents I1 and I2 of coil pairs and α is the phase difference between the two fluxes.
Iv. Balanced Beam Relay
All these relays have the same principle. That is electromagnetic force produced by the magnetic flux which in turn is produced by the operating quantity. The force exerted on the moving element is proportional to the square of the flux in the air gap or square of the current. In DC electromagnetic relays this force is constant. If this force exceeds the restraining force, the relay operates.
This type of balanced beam relay has a fixed beam and an electromagnet (EM) as shown in the figure. The EM has two windings, one is energized by the voltage and the other energized by the current. Under normal conditions, the pull due to the voltage (restraint quantity) will be high and hence the contact remains open. When a fault occurs, the current increases, the pull due to current will be more than the pull due to voltage. This closes the contacts of the trip circuit.
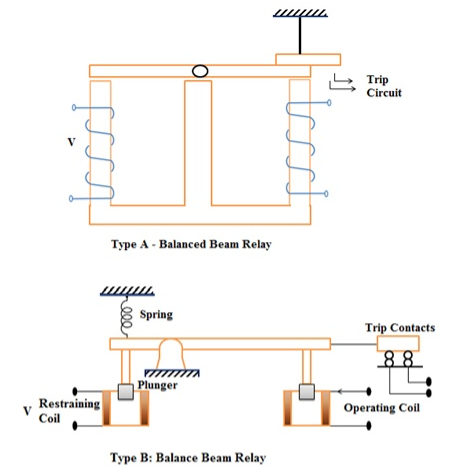
This balanced beam type relay shown in the figure consists of a horizontal beam pivoted centrally, with one armature attached to either side. There are two coils, one on each side. The beam remains horizontal till the operating force becomes greater than the restraining force. Current in coil gives the operating force and in the other, the restraining force. When the operating force or torque increases, the beam tilts and then the contact closes. The relay then actuates the tripping mechanism of the circuit breaker controlling the line / equipment.
v. Moving Coil Relays
It is of two types
- Rotary Moving Coil
It consists of a permanent magnet coil wound on a non-magnetic former, spring, spindle etc. as shown in the fig. The coil is energized by the fault current. Due to the interaction of the permanent magnetic field and the field due to the coil, moving torque is developed. Due to this the spindle rotates and closes the trip circuits. It has negative time-current characteristics as shown in the figure. It has high torque / weight ration.
F α NHIL
Where F = Force, N= No. Of turns, H=Magnetic Field, I=Current in the coil, L=Length of coil
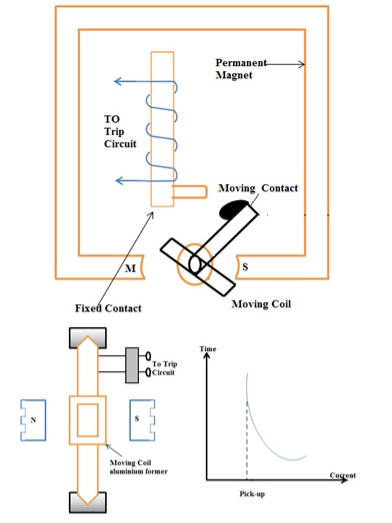
b. Axial Moving Coil
It has axially suspended coil wound on a former. The coil has only axial movement. When the coil is energized by the current, magnetic field is developed and this magnetic field is repelled by the already existing permanent magnet. Due to this, contacts get closed.
This relay is more sensitive and faster than the rotary moving coil relay. This relay has inverse operating time-current characteristics.
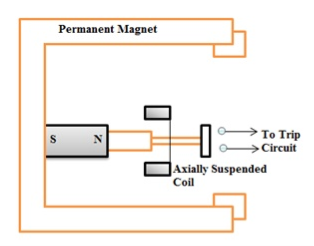
Q3) Explain in detail the relay design & its construction?
A3) The design of protective relay is normally divided into the following stages:
(a) Selection of the operating characteristics
(b) Selection of proper construction
(c) Design of the contact moment from the point of view of utmost reliability.
The relay operating characteristic must match with the abnormal operating characteristics of the system i.e., it should clearly show the conditions for tripping under various abnormal operating conditions. The most important considerations in the design for construction are:
- Reliability
- Simplicity of construction
- Circuitry
The construction of the relay is divided into the following:
- Contacts- Contact performance is probably the most important item affecting reliability of the relay. Corrosion or dust deposit can cause non-operation of relay. Thus, material and shape of relay are of considerable importance. A good contact system design provides restricted contact resistance, reduced contact wear. The contact material used is gold, gold alloy, platinum, palladium and silver. The selection of the contact material depends on a number of factors like:
(a) The voltage per contact break
(b) The current to break
(c) The type of atmospheric pollution under which the contacts are operate
The following factors are to be considered for selecting a suitable contact material: 1) The nature of the current to be interrupted (ac or dc) 2) Voltage at break and make operation 3) Value of current magnitude 4) Frequency of operation 5) The actual speed of contact at make or break 6) Contact shape
- Bearing-
(a) Single ball bearing
(b) Multi ball bearing
(c) Pivot and jewel bearing – This is the most common type for precision relay
- Electromechanical design- It consists of the design of the magnetic circuit and the mechanical features of core, yoke, and armature. The reluctance of the magnetic path is kept to a minimum by enlarging the pole face which makes the magnetic circuit more efficient.AC electromagnets made from soft iron, low carbon steel core having a slot for mounting shaded rings are more common. The relay coil current is usually limited to 5A and the coil voltage to 220 V but the insulation for the relay coil is designed to withstand at least 4kV.The relay coil is designed to carry about 15 times the normal current foe one second.
Termination & housing- Material used for springs are stainless steel; nickel steel, phosphorous bronze and Beryllium copper. The spring is insulated from the armature by molded blocks. For moulded blocks nylon is used.
Q4) Explain the theory of Induction Relay Torque?
A4) In Induction Relay Torque Equation, two magnetic fluxes Φ1 and Φ2 differing in time phase penetrate through a disc. These alternating fluxes induce emfs e1 and e2 in the disc which lag their respective fluxes by 90°. These emfs lead to the flow of eddy currents i1 and i2. By the interaction of Φ1 with i2 and Φ2 with i1 a driving torque is produced.
The currents i1 and i2 lag the voltages e1 and e2 by the impedance angle λ of the disc. Below figure shows the vector diagram.
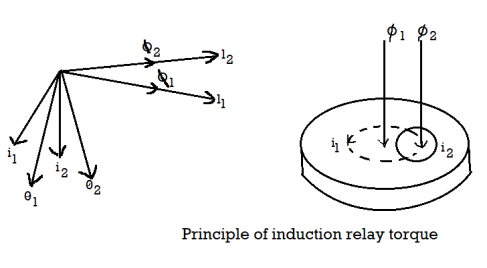
Let,


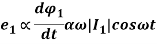
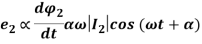


Therefore, the resultant torque is given as-
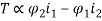


Thus, the induction relay is a sine comparator in which the maximum torque is developed when α is 90° or 270° and zero torque when α is 0° or 180°.
Q5) Write short notes on Equation for Comparators?
A5) Equation for Comparators
Let us first derive the general threshold equation assuming that there are two input signals S1 and S2 such that when the phase relationship or magnitude relationship fulfills pre-determined threshold conditions, tripping is initiated. The input signals are derived from the system through instrument transformers (CTs and/or PTs). In case the two quantities to be compared are different (i.e., voltage and current), some form of mixing device, such as current voltage transactor, is required.
Let the two input signals be represented as –


Where, A and B are the primary system quantities, K1 and K3 are the scalar numbers and |K2|and | K4| are the complex numbers with angles θ2 and θ4 respectively. Taking A as the reference phasor and phasor B to lag A by an angle ɸ. Then the above equation can be rewritten as –


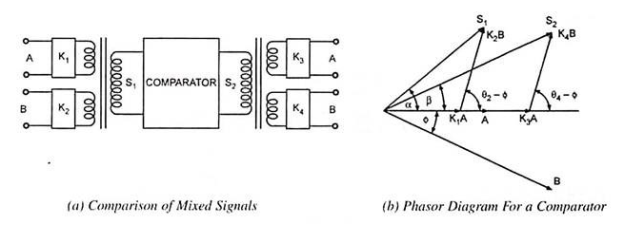
Q6) What are Over Current Relays?
A6) In an over current relay or o/c relay the actuating quantity is only current. There is only one current operated element in the relay, no voltage coil etc. are required to construct this protective relay.
In an over current relay, there would be essentially a current coil. When normal current flows through this coil, the magnetic effect generated by the coil is not sufficient to move the moving element of the relay, as in this condition the restraining force is greater than deflecting force. But when the current through the coil increases, the magnetic effect increases, and after a certain level of current, the deflecting force generated by the magnetic effect of the coil, crosses the restraining force. As a result, the moving element starts moving to change the contact position in the relay. Although there are different types of over current relays but basic working principle of over current relay is more or less same for all.
Q7) Explain the different types of Over Current Relays?
A7) Types of Over Current Relays
(i) Instantaneous Over Current Relay
Construction and working principle of instantaneous over current relay is quite simple.
Here generally a magnetic core is wound by a current coil. A piece of iron is so fitted by hinge support and restraining spring in the relay, that when there is not sufficient current in the coil, the NO contacts remain open. When the current in the coil crosses a preset value, the attractive force becomes enough to pull the iron piece towards the magnetic core, and consequently, the no contacts get closed.
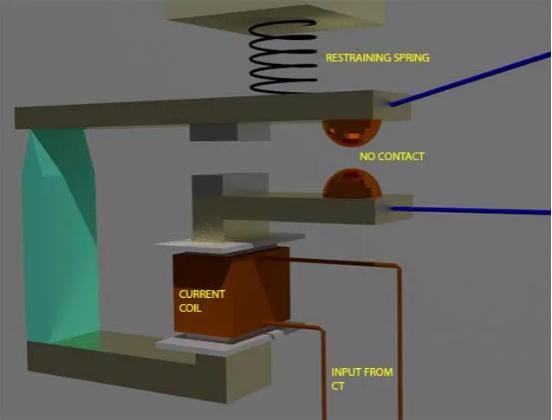
We refer the pre-set value of current in the relay coil as pickup setting current. This relay is referred as instantaneous over current relay, as ideally, the relay operates as soon as the current in the coil gets higher than pick upsetting current. There is no intentional time delay applied. But there is always an inherent time delay which we cannot avoid practically. In practice, the operating time of an instantaneous relay is of the order of a few milliseconds.
(ii) Definite Time Over Current Relay
This relay is created by applying intentional time delay after crossing pick up the value of the current. A definite time overcurrent relay can be adjusted to issue a trip output at an exact amount of time after it picks up. Thus, it has a time setting adjustment and pickup adjustment.
(iii) Inverse Time Over Current Relay
Inverse time is a natural character of any induction type rotating device. Here, the speed of rotation of rotating part of the device is faster if the input current is more. In other words, time of operation inversely varies with input current. This natural characteristic of electromechanical induction disc relay is very suitable for overcurrent protection. If the fault is severe, it will clear the fault faster. Although time inverse characteristic is inherent to electromechanical induction disc relay, the same characteristic can be achieved in microprocessor-based relay also by proper programming.
Q8) Explain the working of Directional Relays?
A8) Selective protection cannot be achieved with time graded overcurrent protection systems in ring or loop systems as well as in radial circuits with two end power supply. A directional feature is incorporated in the Directional Relays as shown in Fig.
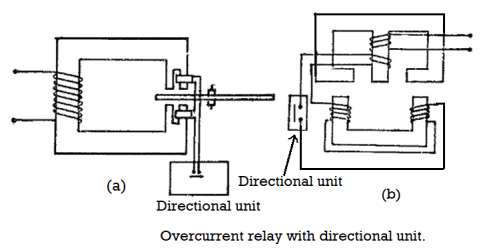
Figure (a) shows how an induction disc type over current relay with split-pole magnet, having in addition a directional unit consisting of capacitance or a resistance capacitance circuit works. Figure (b) shows the watt metric type of induction disc relay. Here the directional unit controls the angle between the two fluxes by varying the RX parameters of the lower electromagnet.
Another method of control in the watt metric element is to supply the lower winding from a separate voltage source. When the voltage of this source is equal and opposite to the output of the upper magnet secondary winding there is no current in the lower coil, and therefore no torque is produced. If it opposes and is less than the secondary output, or if it assists the secondary output, there is an operating torque. Conversely, if this source voltage opposes and exceeds the secondary output the current in the lower coif is reversed, giving a reverse torque. This latter method of control is the basis of the Translay balanced-voltage unit protection.
Q9) Explain the working of Distance Relay?
A9) Distance protection relay is the name given to the protection, whose action depends on the distance of the feeding point to the fault. The time of operation of such protection is a function of the ratio of voltage and current, i.e., impedance. This impedance between the relay and the fault depends on the electrical distance between them. The principal type of distance relays is impedance relays, reactance relays, and the reactance relays. Distance protection relay principle differs from other forms of protection because their performance does not depend on the magnitude of the current or voltage in the protective circuit but it depends on the ratio of these two quantities. It is a double actuating quantity relay with one of their coils is energized by voltage and the other coil is energized by the current. The current element produces a positive or pick-up torque while the voltages element has caused a negative and reset torque.
The relay operates only when the ratio of voltage and current falls below a set value. During the fault the magnitude of current increases and the voltage at the fault point decreases. The ratio of the current and voltage is measured at the point of the current and potential transformer. The voltage at potential transformer region depends on the distance between the PT and the fault.
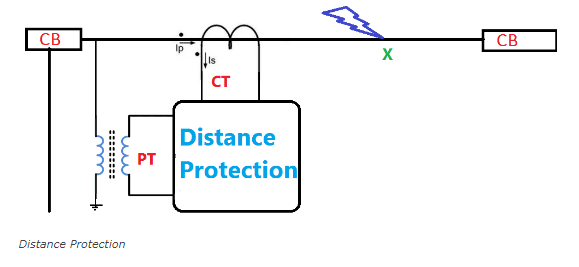
If the fault is nearer, measured voltage is lesser, and if the fault is farther, measured voltage is more. Hence, assuming constant fault impedance each value of the ratio of voltage and current measured from relay location comparable to the distance between the relaying point and fault point along the line. Hence such protection is called the distance protection or impedance protection.
Distance zone is non-unit protection, i.e., the protection zone is not exact. The distance protection is high-speed protection and is simply to apply. It can be employed as a primary as well as backup protection. It is very commonly used in the protection of transmission lines.
Distance relays are used for both phase fault and ground fault protection, and they provide higher speed for clearing the fault. It is also independent of changes in the magnitude of the short circuits, current and hence they are not much affected by the change in the generation capacity and the system configuration. Thus, they eliminate long clearing times for the fault near the power sources required by overcurrent relay if used for the purpose.
Q10) Write short notes on equation for Electromagnetic Relays?
A10) When not more than two quantities are involved, the equation for the characteristic of the relay at the threshold of operation under steady state conditions, when plotted on complex planes is a circle. The General Equation for Electromagnetic Relay can be represented in a general form as-

Where, |A| & |B| are two quantities being compared
= Electrical Angle between A & B
= Relay characteristic angle, which is the value of
for maximum torque
K & K’ = Scalar Constants
K’’ = Mechanical restraining toque
If the two input quantities are current I and voltage V then the equation for threshold operation becomes:
Which can also be explained as: the current winding produces a torque KI2 and the potential winding a torque K’V2, while the torque due to interaction of current and potential windings will be VI cos (Φ-θ).
K” is finite only in singe quantity relays, where it is used as a level indicator; it is made negligibly small in relays with more than one input so K” = 0 and dividing throughout by K′ |I|2
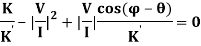

It can be represented as a circle on a complex plane, having

As coordinates, i.e., on the R-X plane as shown in the figure below
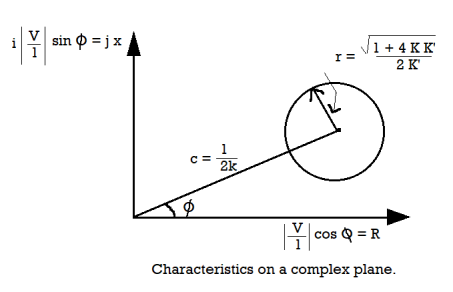
Q11) Explain the working of Differential Relays?
A11) The relay whose operation depends on the phase difference of two or more electrical quantities is known as the differential protection relay. It works on the principle of comparison between the phase angle and the magnitude of the same electrical quantities. For example: Consider the comparison of the input and output current of the transmission line. If the magnitude of the input current of the transmission line is more than that of output current that means the additional current flows through it because of the fault. The difference in the current can operate the differential protection relay.
The following are the essential condition requires for the working of the differential protection relay.
- The network in which the relay use should have two or more similar electrical quantities.
- The quantities have the phase displacement of approximately 180º.
The differential protection relay is used for the protection of the generator, transformer, feeder, large motor, bus-bars etc. The following are the classification of the differential protection relay.
- Current Differential Relay
- Voltage Differential Relay
- Biased or Percentage Differential Relay
- Voltage Balance Differential Relay
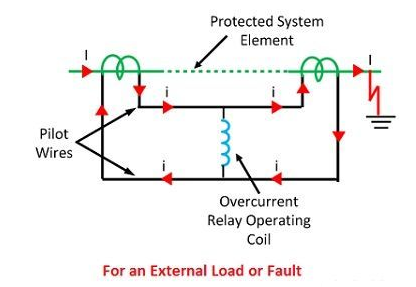
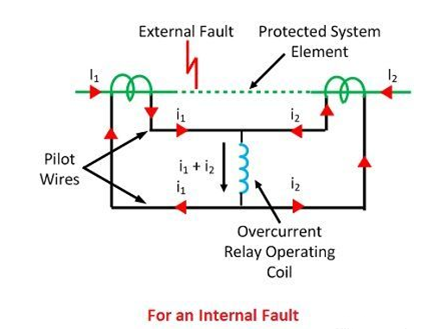
Q12) How are Pilot Wires schemes helps in Feeder Protection?
A12) Pilot Wire Schemes for Feeder Protection
In differential protection scheme, the current entering at one end of the line and leaving from other end of the line is compared. The pilot wires are used to connect the relays. Under normal working condition, the two currents at both ends are equal and pilot wires do not carry any current, keeping relays inoperative. Under an internal fault condition, the two currents at both the ends are no longer same, this causes circulating current flow through pilot wires and makes the relay to trip. The various schemes used with this method of protection are,
1. Merz-Price Voltage Balance System
2. Translay Scheme
Q13) Explain the working of Merz-Price Voltage Balance System?
A13) The working principle of Merz Price Balance system is quite simple. In this scheme of line protection, identical CT is connected to each of the both ends of the line. The polarity of the CTs is same. The secondary of these current transformer and operating coil of two instantaneous relays are formed a closed loop as shown in the figure below. In the loop pilot wire is used to connect both CT secondary and both relay coil as shown.
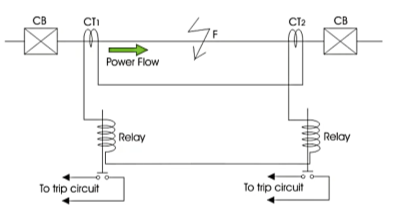
Now, from the figure it is quite clear that when the system is under normal condition, there would not be any current flowing through the loop as the secondary current of one CT will cancel out secondary current of other CT.
Now, if any fault occurs in the portion of the line between these two CTs, the secondary current of one CT will no longer equal and opposite of secondary current of other CT. Hence there would be a resultant circulating current in the loop. Due to this circulating current, the coil of both relays will close the trip circuit of associate circuit breaker. Hence, the faulty line will be isolated from both ends.
Q14) What ae the advantages & disadvantages of Differential Pilot Wire Protection?
A14) Advantages of Differential Pilot Wire Protection:
- This system can be used for ring mains as well as parallel feeders,
- This system provides instantaneous protection for ground faults. This decreases the possibility of these faults involving other phases.
- This system provides instantaneous relaying which reduces the amount of damage to overhead conductors resulting from arcing faults.
Disadvantages of Differential Pilot Wire Protection:
- Accurate matching of current transformers is very essential.
- If there is a break in the pilot-wire circuit, the system will not operate.
- This system is very expensive owing to the greater length of pilot wires required.
- In case of long lines, charging current due to pilot-wire capacitance effects may be sufficient to cause relay operation even under normal conditions.
- This system cannot be used for line voltages beyond 33 kV because of constructional difficulties in matching the current transformers.
Q15) How are Over Current Relay helpful in Feeder Protection?
A15) Over Current relay for Feeder Protection
It is customary to have two elements of over current and one element of earth fault protection system in the most elementary form of protection of three phase feeders. Different types of feeders employ the over current protection along with the directional relay so that proper discrimination of an internal fault is possible. Some examples are illustrated below.
(a) Application of directional relays to parallel feeders
It may be seen from the below given parallel feeders that the relays placed at the load side of both the lines use directional element which respond to a direction away from the bus bars. Similarly, the relays placed at the source side do not require any directional element.
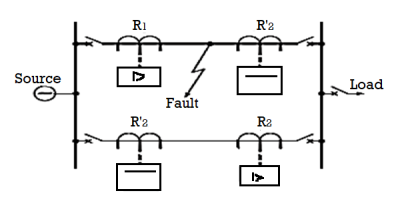
(b) Application of directional relays to ring mains
A similar concept of discrimination is also utilized in the below given ring main feeder and a feeder fed from both the sides. It can be observed that relays placed near the bus connecting the sources, don’t have any directional feature, whereas the rest of the buses, respond to a direction always away from the source. It is good practice to locate a fault anywhere among different sections of the feeders and check whether that particular section only is isolated without disrupting the power flow in other sections.
(c) Over current protection radial system
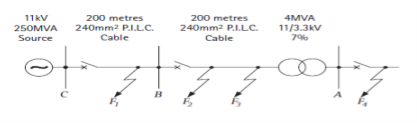
Q16) Explain the Translay Scheme for Feeder protection?
A16) This system is similar to voltage balance system except that here balance or opposition is between the voltages induced in the secondary windings wound on the relay magnets and not between the secondary voltages of the line current transformers. This permits to use current transformers of normal design and eliminates one of the most serious limitations of original voltage balance system, namely; its limitation to the system operating at voltages not exceeding 33 kV.
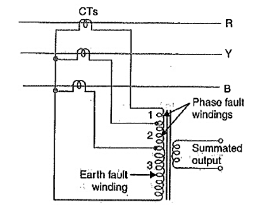
The application of Translay scheme for a single-phase line has already been discussed in Art. 21.20. This can be extended to 3-phase system by applying one relay at each end of each phase of the 3-phase line. However, it is possible to make fur her simplification by combining currents derived from all phases in a single relay at each end, using the principle of summation transformer. A summation transformer is a device that reproduces the poly phase line currents as a single-phase quantity. The three lines CTs are connected to the tapped primary of summation transformer. Each line. CT energizes a different number of turns (from line to neutral) with a resulting single-phase output. The use of summation transformer permits two advantages viz (i) primary windings 1 and 2 can be used for phase faults whereas winding 3 can be used for earth fault (ii) the number of pilot wires required is only two.
Schematic arrangement: The Translay scheme for the protection of a 3-phase line is shown in the below figure. The relays used in the scheme are essentially overcurrent induction type relays. Each relay has two electromagnetic elements. The upper element carries a winding (11 or 11 a) which is energized as a summation transformer from the secondaries of the line CTs connected in the phases of the line to be protected. The upper element also carries a secondary winding (12 or 12 a) which is connected is series with the operating winding (13 or 13 a) on the lower magnet. The secondary windings 12, 12 a and operating windings 13, 13a are connected in series in such a way that voltages induced in them oppose each other. Note that relay discs and tripping circuits have been omitted in the diagram for clarity.
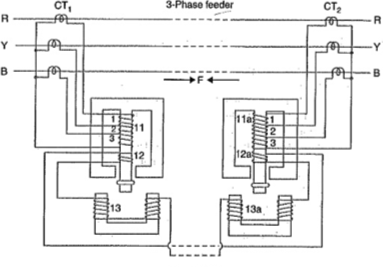
Operation: When the feeder is sound, the currents at its two ends are equal so that the secondary currents in both sets of CTs are equal. Consequently, the currents flowing in the relay primary winding 11 and 11 a will be equal and they will induce equal voltages in the secondary windings 12 and 12a. Since these windings are connected in opposition, no current flows in them or in the operating windings 13 and 13a. In the event of a fault on the protected line, the line current at one end must carry a greater current than that at the other end. The result is that voltages induced in the secondary windings 12 and 12 a will be different and the current will flow through the operating coils 13, 13a and the pilot circuit. Under these conditions, both upper and lower elements of each relay are energized and a forward torque act on each relay disc. The operation of the relays will open the circuit breakers at both ends of the line.
Q17) Explain the working of Amplitude Comparator?
A17) Amplitude comparator compares the amplitudes of two (or more) input quantities. The phase angle between the quantities under comparison (inputs) is not recognized or noticed by the amplitude comparator.
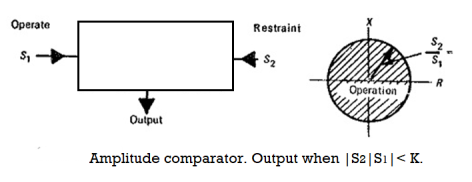
If the two input signals are S1 and S2 (say S1 the operating and S2 restraining), the amplitude comparator gives positive output only if –
S2/S1 < K.
The function is represented by a circle in the complex plane with its centre at the origin. This defines the boundary of the marginal operation. The main purpose of amplitude comparators is to provide direction and distance protection.
Mainly there are three types of amplitude comparators
- Integrating Comparators
- Instantaneous Comparators
- Sampling Comparators
Q18) Explain the working of Coincidence Phase Comparator?
A18) The basic concept of phase comparison is simpler in that it is possible to deal with signals of equal strength whose coincidence (or non-coincidence) is readily measurable. Considering two sinusoidal signals S1 and S2, the period of coincidence of S1 and S2 will depend on the phase difference between S1 and S2. Figure below illustrates the coincidence of signals for different phase relationships in Coincidence Type Phase Comparator.
It can be seen that the period of coincidence is equal to the period of non-coincidence for a phase difference of ±90°, the period of coincidence is less than the period of non-coincidence and vice versa when the phase difference is less than ±90°.
Depending upon the phase relation of the input signals it is possible to design the circuit to give an output a Yes or a No, by measuring the period of Coincidence Type Phase Comparator. The period of coincidence of two signals with a phase difference of θ is ψ=180-θ.
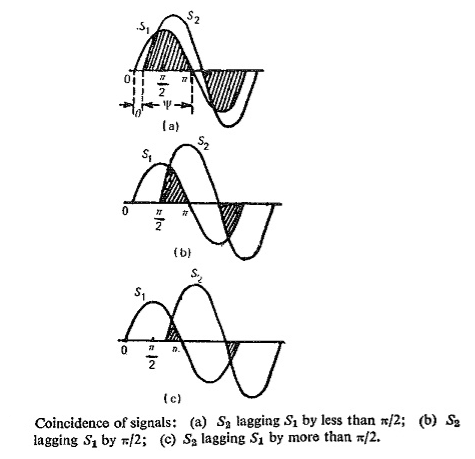
Q19) What are the basic elements of Static Relays?
A19) The static relay is the combination of both the static and the electromagnetic relay. In this relay, there is no armature and moving contacts and response is developed by the components without mechanical motion. The solid-state components used are transistors, diodes, resistors, 0and capacitor and so on. In the static relay, the measurement is performed by electronic, magnetic, optical or another component without mechanical motion.
Static relay consists of the following functional circuits:
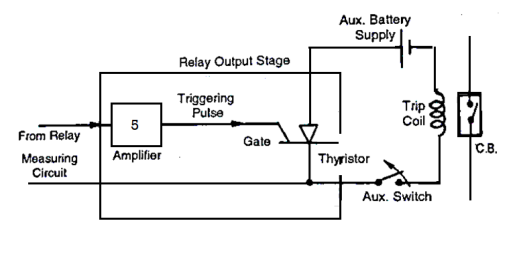
- Input stage with CT’s and PT’s:
The input to the relay is obtained from the CT/PT. This output of CT/PT is given to the auxiliary CT/PT. The input stage has CT’s and PT’s, summation units, auxiliary CT’s and PT’s, filter.
- Rectifiers and smoothing circuits:
In these circuits, the input given from auxiliary CT/PT is given to the single bridge rectifier to rectify the fluctuating quantities. This rectifier output is then smoothened to avoid any ripples and is provided it to a level detector which levels the quantities.
- Comparator:
The output which is smoothened is given to the comparator to compare it with a fixed input. Thus, the output is then fed to the measuring unit. The comparators used are of amplitude, hybrid and phase comparators.
- Measuring unit:
If the input of the comparator is above the threshold value, then the level detector gives an output otherwise it doesn’t produce output if it’s below the threshold value.
There are amplifiers, logic circuits as well as level detector circuits to complete the job.
- Output stage:
The output of the level detector is then fed to the output stage of the relay in which it has a PMMC (Permanent magnet moving coil) relay, a Thyristor in series with the trip coil and auxiliary switch.
Whenever there is a fault the relay operates, and it gives gate signal to the Thyristor which then energizes the trip coil so that the circuit breaker contacts get open and the circuit is tripped. These relays do not have any arcing problems as all the entire relay system is static.
Q20) Explain the working of Differential Protection in Feeder protection?
A20) A differential relay is the relay which operates when the phasor difference of two or more similar electrical quantities exceeds a predetermined value.
In static differential relay, two similar quantities either voltages or currents are compared. The comparator measures the vector difference between the two similar input signals. The rectifier bridge type comparator is generally used in the static differential relay. The block diagram is shown in the figure
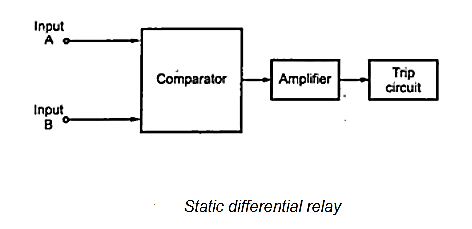
In normal conditions, the two quantities balance each other and the comparator output is zero and the relay us inoperative.
For any internal fault conditions, the comparator senses the phase difference between the two quantities and produces the output. This is amplified and given to the trip circuit which operates the relay. This scheme is used for protection of the generators and transformers against any type of internal fault.
The various advantages of static differential relay over electromagnetic differential relay are, highly sensitive, compact, and very fast in operation, low power consumption, less burden on input CTs and inrush current proof characteristics.
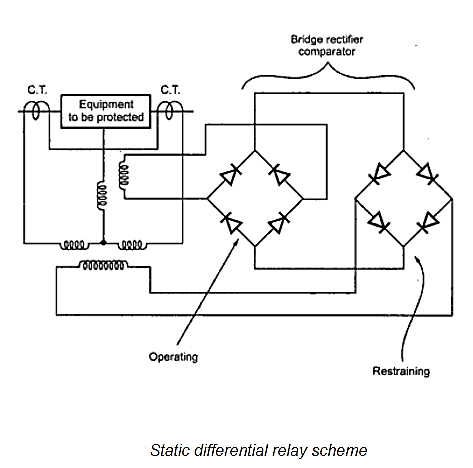
The basic static differential relay scheme is shown in the above figure.
Let no and nr be the number of turns of operating and restraining coils respectively. Then the relay operates when,
K1 no Io > K2 nr Ir + K'
Where k1 and k2 are design constants while K' is the spring control torque.