UNIT 1
Basic Equations of Elasticity
Q1) What is Hooke’s Law?
A1) When a material behaves elastically and exhibits a linear relationship between stress and strain, it is called linearly elastic material. In this case, stress is directly proportional to strain.
OR
You can say that “for small deformation, stress is directly proportional to strain”
Therefore, in simple terms, Hooke’s law states that the strain in a solid is proportional to the applied stress within the elastic limit of that solid.
Hooke’s Law Equation
Mathematically, Hooke’s Law is expressed as:
Stress α Strain
Stress = Young’s modulus of elasticity* Strain
σ = E ε
Where,
σ is the stress,
E is the modulus of elasticity also known as Young’s modulus of elasticity,
ε is the strain.
In SI units, the spring constant k, and each element of the tensor κ, is measured using units such as Newton per meter (N/m), or kilograms per second squared (kg/s2).
For continuous media, each element is therefore measured in units of pressure, namely Pascal’s (Pa, or N/m2, or kg/(m·s2). The elements of the strain tensor ε are also expressed in units of pressure
Q2) What is corrosion?
A2) Corrosion:
It is defined as the natural process that causes the transformation of pure metals to undesirable substances when they react with substances like water or air. This reaction causes damage and disintegration of the metal starting from the portion of the metal exposed to the environment and spreading to the entire bulk of the metal.
Metals placed higher in the reactivity series such as iron, zinc, etc. get corroded very easily and metals placed lower in the reactivity series like gold, platinum and palladium do not corrode. The explanation lies in the fact that corrosion involves oxidation of the metals. As we go down the reactivity series tendency to get oxidised is very low (oxidation potentials is very low).
Interestingly, aluminium doesn’t corrode unlike other metals even though it is reactive. This is because aluminium is covered by a layer of aluminium oxide already. This layer of aluminium oxide protects it from further corrosion.
Factors Affecting Corrosion
1. Exposure of the metals to air containing gases like CO2, SO2, SO3 etc.
2. Exposure of metals to moisture especially salt water (which increases the rate of corrosion).
3. Presence of impurities like salt (e.g. NaCl)
4. Temperature: An increase in temperature increases corrosion.
5. Nature of the first layer of oxide formed: some oxides like Al2O3 forms an insoluble protecting layer which can prevent further corrosion. Others like rust easily crumble and expose the rest of the metal.
6. Presence of acid in the atmosphere: acids can easily accelerate the process of corrosion.
Q3) Explain the types of Corrosion?
A3) some of the corrosion types include;
(i) Crevice Corrosion
Whenever there is a difference in ionic concentration between any two local areas of a metal, a localized form of corrosion know as crevice corrosion can occur. Examples of areas where crevice corrosion can occur are gaskets, the under surface of washers, and bolt heads.
Example: All grades of aluminium alloys and stainless steels undergo crevice corrosion.
(ii) Stress Corrosion Cracking
Stress Corrosion Cracking can be abbreviated to ‘SCC’ and refers to the cracking of the metal as a result of the corrosive environment and the tensile tress placed on the metal. It often occurs at high temperatures.
Example: Stress corrosion cracking of austenitic stainless steel in chloride solution.
(iii) Inter granular Corrosion
Inter granular corrosion occurs due to the presence of impurities in the grain boundaries that separate the grain formed during the solidification of the metal alloy. It can also occur via the depletion or enrichment of the alloy at these grain boundaries.
Example: Aluminium-base alloys are affected by IGC.
(iv) Galvanic Corrosion
When there exists an electric contact between two metals that are electrochemically dissimilar and are in an electrolytic environment, galvanic corrosion can arise. It refers to the degradation of one of these metals at a joint or at a junction. A good example of this type of corrosion would be the degradation that occurs when copper, in a salt-water environment, comes in contact with steel.
Example: When aluminium and carbon steel are connected and immersed in seawater, aluminium corrodes faster and steel is protected.
(iv) Pitting Corrosion
Pitting Corrosion is very unpredictable and therefore is difficult to detect. It is considered one of the most dangerous types of corrosion. It occurs at a local point and proceeds with the formation of a corrosion cell surrounded by the normal metallic surface. Once this ‘Pit’ is formed, it continues to grow and can take various shapes. The pit slowly penetrates metal from the surface in a vertical direction, eventually leading to structural failure it left unchecked.
Example: Consider a droplet of water on a steel surface, pitting will initiate at the centre of the water droplet (anodic site).
(v) Uniform Corrosion
This is considered the most common form of corrosion wherein an attack on the surface of the metal is executed by the atmosphere. The extent of the corrosion is easily discernible. This type of corrosion has a relatively low impact on the performance of the material.
Example: A piece of zinc and steel immersed in diluted sulphuric acid would usually dissolve over its entire surface at a constant rate.
Q4) Explain the reaction performed in corrosion?
A4) Corrosion Examples and Reactions
Here are some of the typical examples of corrosion as seen mostly in metals.
1. Copper Corrosion
When copper metal is exposed to the environment it reacts with the oxygen in the atmosphere to form copper (I) oxide which is red in colour.
2Cu(s) + ½ O2(g) → Cu2O(s)
Cu2O further gets oxidised to form CuO which is black in colour.
Cu2O(s) + ½ O2(g) → 2CuO(s)
This CuO reacts with CO2, SO3 and H2O (present in the atmosphere to form Cu2(OH)2(s) (Malachite) which is blue in colour and Cu4SO4(OH)6(s) (Brochantite) which is green in colour.
This is why we observe copper turning bluish-green in colour.
A typical example of this is the colour of the statue of liberty which has the copper coating on it turning blue-green in colour.
2. Silver Tarnishing
Silver reacts with sulphur and sulphur compounds in the air give silver sulphide (Ag2S) which is black in colour. Exposed silver forms Ag2S as it reacts with the H2S(g) in the atmosphere which is present due to certain industrial process.
2Ag(s) + H2S(g) → Ag2S(s) + H+2+(g)
3. Corrosion of Iron (Rusting)
Rusting of iron which is the most commonly seen example happens when iron comes in contact with air or water. The reaction could be seen as a typical electrochemical cell reaction. Consider the diagram given below.
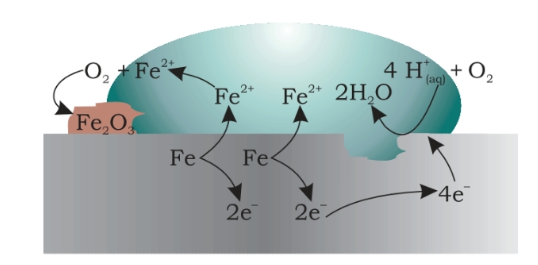
Here metal iron loses electrons and gets converted to Fe{aq}2+ (this could be considered as the anode position). The electrons lost will move to the other side where they combine with H+ ions. H+ ions are released either by H2O or by H2CO3 present in the atmosphere (this could be considered as the cathode position).
H2O ⇌ H+ + OH–
H2CO3 ⇌ 2H+ + CO32
The Hydrogen thus formed by the reaction of H+ and electrons react with oxygen to form H2O.
Anode reaction
2Fe(s) → 2Fe2+ + 4e– = – 0.44 V
Cathode reaction
O2(g)+4H+(aq)+4e−⟶2H2O(l)EoH+/O2/H2/O=1.23V
Overall reaction
2Fe(s) + O2(g) + 4H+(aq) → 2Fe2+(aq) + 2H2O(l)Eocell = 1.67V
The Fe2+ ions formed at the anode react with oxygen in the atmosphere, thereby getting oxidised to Fe3+ thereby forming Fe2O3 which comes out in the hydrated form as Fe2O3.xH2O
Fe2+ + 3O2 → 2Fe2O3
Fe2O3 + xH2O → Fe2O3. XH2O (rust)
Other examples include,
- Corrosion of Zinc when it reacts with oxygen and HCl to form white coloured ZnCl2.
- Corrosion of Tin to form black coloured Na2[Sn(OH)2].
Q5) Explain ideas of Prevention of Corrosion?
A5) Preventing corrosion is of utmost importance in order to avoid huge losses. Majority of the structures we use are made out of metals. This includes bridges, automobiles, machinery, household goods like window grill, doors, railway lines, etc.
There are various methods to prevent corrosion. These include,
1. Electroplating
It is the process by which a metal (I) is coated with a thin layer of another metal (II) using electrolysis. In this way, the new metal coating protects the metal (I) from corrosion.
In the process, a metal is used as the coating, (metal II) is kept as the anode and metal (I) (metal to be plated) is kept as the cathode. i.e, metal ‘I’ is connected to the negative terminal and metal II is connected to the positive terminal. These 2 electrodes are immersed in an electrolyte and when power is supplied, oxidation happens in the anode, thereby dissolving metal II ions in the electrolyte. These dissolved metal II ions are reduced at the cathode thereby providing a coating on metal I.
The metals most commonly used as the anode are Copper, Nickel, Gold, Silver, and Zinc. Etc.,
2. Cathodic Protection
In this process, the base metal is connected to a sacrificial metal that corrodes instead of the base metal. By doing so this sacrificial metal (which is more reactive than the base metal) will give out electrons and get oxidised. The ions thus formed takes part in the corrosion reactions thereby saving the base metal.
3. Galvanization
This process involves coating iron with a thin layer of zinc. It is generally done by dipping iron in molten zinc. The zinc layer coating thus protect the iron inside from corrosion
4. Painting and Greasing
Providing a layer of paint or grease on the metal can prevent the exposure of the metal with the external environment thereby preventing corrosion.
5. Choosing the right material can also help prevent corrosion. Eg: Aluminium and stainless steel are highly corrosion resistant
6. Using corrosion Inhibitor
Corrosion inhibitors are chemicals which when added to the corrosion environment has the ability to cut down the rate of corrosion.
Q6) Explain Relation between stress and strain?
A6) To understand the relationship between stress and strain we plot a graph with different-different load and corresponding stress and strain. The sample is given bellow-
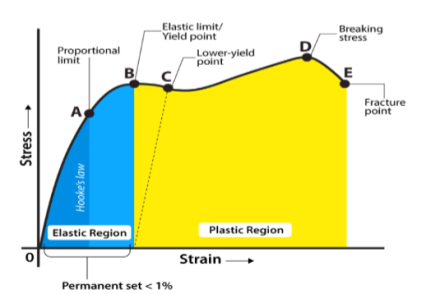
Fig.Stress-strain Relation
- In the initial region OA the stress is proportional to strain, here Hooke law is applicable. And in the region OB the body show elastic behaviour hence this region is called an elastic region. Point B is called the elastic limit.
- Point C is the yield point from where the body starts plastic deformation.
- Ultimate stress is a point that is the maximum possible stress beyond which the failure starts.
- The fracture point is the point where the breakage occurs.
Q7) Explain Stress Invariants?
A7) The characteristics equation of the stress matrix is –
The roots of the above equation do not depend on the selection of coordinate axis therefore I1, I2, and I3 must be independent of coordinates, hence they are called stress invariants. If stress matrix is given as-
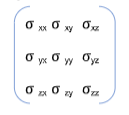
Then invariant I1 = σxx + σyy + σzz
And:
I2 = minor of σxx +minor of σyy +minor of σzz
And: I3 = Determinant of stress matrix
These I1, I 2 and I3 stress invariants.
Q8) Explain buckling?
A8) Buckling
Buckling occurs when a material subjected to compressive or torsional stresses can no longer support the load, and it consequently fails by bulging, bending, bowing or forming a kink or other unnatural characteristic. Bars, tubes, and columns are shapes that are commonly susceptible to failure by buckling. In addition, I-beams and other more complex geometries may experience buckling under compressive or torsional loads. Strength and hardness properties do not indicate a material’s susceptibility to buckling. Buckling is dependent on the shape and respective dimensions of the material as well as the modulus of elasticity, which is dependent on temperature. Therefore, buckling is more likely to occur at higher temperatures where the modulus of elasticity is lower, since materials have a tendency to soften when they are heated.
Q9) Explain high cycle and low cycle fatigue?
A9) High-Cycle Fatigue
High-cycle fatigue is defined as fatigue where the material is subjected to a relatively large number of cycles before failure occurs. Generally, for the fatigue mechanism to be considered high-cycle fatigue the number of cycles required to produce failure is greater than 10,000. The deformation exhibited by a material subjected to high-cycle fatigue is typically elastic.
Low-Cycle Fatigue
A fatigue failure that occurs after a relatively small number of cycles is considered to be low-cycle fatigue. Typically, when a material fails due to fatigue after less than 10,000 cycles, it is considered to be low-cycle fatigue. The mechanisms of crack
Q10) What is stress rupture?
A10) Stress rupture, also known as creep fracture, is a mechanism that is closely related to creep except that the material eventually fractures under the applied load. Creep is the time- and temperature-dependent elongation of a material that is subjected to a stress. When this stress overcomes the material’s ability to strain, it will rupture. Cracking that proceeds the rupture of the material can be either Trans granular or inter granular.