Unit-IV
Cost Accounting
Question and answers
Q1. Define costing with its method.
Ans. Costing is an accounting method that records and analyses all costs associated with the execution of a process, project, or product. Such analysis helps management make strategic decisions.
Costing uses a variety of techniques to make your organization cost-effective. Everything you need to know about the different costing methods. The term "costing method" can be used to refer to the various processes or procedures used to determine and display costs.
There are different costing methods in different industries, depending on the nature of the job. Costing methods can be studied under the head below. -1. Method based on the principle of job costing 2. Method based on the principle of process costing.
Costing methods can be studied under the head below. -1. Method based on the principle of job costing 2. Method based on the principle of process costing.
Some of the methods based on the principles of process costing are: -
1. Process costing
2. Operating costing
3. Department costing
4. Single or unit or output costing
5. Operation or operation or work or service costing
6. Multiple or combined costing.
In addition, some other costing methods are: -
1. Uniform costing
2. Multiple or combined costing
3. Department costing
4. Cost plus method
5. Target costing method 6. Farm costing
7. Activity-based costing.
Different types of costing methods: job costing, contract costing, batch costing, process costing, and operating costing.
Q2. Explain the different methods of costing.
Ans, The costing method refers to the cost confirmation and costing system. Industries differ in their nature, the products they produce, and the services they provide. Therefore, different costing methods are used in different industries. For example, the costing method used by building contractors is different from that of shipping companies.
Job costing and process costing are two basic methods of costing. Job costing is suitable for industries that manufacture or perform work according to customer specifications. Process costing is suitable for industries where production is continuous and the units of production are the same. All other methods are a combination, extension, or improvement of these basic methods.
Let's take a closer look at how to calculate costs.
Method # 1 Job costing:
This is also known as specific order costing. There is no standard product and each job or work order is adopted in a different industry. The work is done strictly according to the customer's specifications, and the work is usually completed in a short time. The purpose of job costing is to see the cost of each job individually. Job costing is used in printing presses, motor repair shops, car garages, movie studios, the engineering industry, and more.
Method # 2 Contract Costing:
This is also known as terminal costing. Basically, this method is similar to job costing. However, it is used when the work is large and it takes a long time. The work will be done according to the customer's specifications.
The purpose of contract costing is to see the costs incurred in each contract individually. Therefore, a separate account is provided for each contract. This method is used by companies engaged in the construction of ships, buildings, bridges, dams and roads.
Method # 3 Batch Costing:
This is an extension of job costing. A batch is a group of identical products. All units in a particular batch are uniform in nature and size. Therefore, each batch is treated as a cost unit and is costed separately. The total cost of the batch is checked and divided by the number of units in the batch to determine the cost per unit. Batch costing is adopted by manufacturers of biscuits, ready-made garments, spare parts medicines and more.
Method # 4 Process Costing:
This is called continuous costing. In certain industries, raw materials go through various processes before they take the form of final products. In other words, the finished product of one process becomes the raw material for the next process. Process costing is used in these industries.
A separate account is opened for each process to see the total cost and cost per unit at the end of each process. Process costing applies to continuous process industries such as chemicals, textiles, paper, soaps and foam.
Method # 5 unit costing:
This method is also known as single costing or output costing. It is suitable for industries with continuous production and the same unit. The purpose of this method is to see the total cost and the cost per unit. Create a cost sheet considering material costs, labor costs, and overhead costs. Unit costing applies to mines, oil rig units, cement factories, brick factories and unit manufacturing cycles, radios, washing machines, etc.
Method # 6 Operating cost:
This method is followed by the industry that provides the service. To determine the cost of such services, use composite units such as passenger kilometers and tone kilometers to determine the cost. For example, for a bus company, operating costs represent the cost of carrying passengers per kilometer. Operating costs are used in air railways, road transport companies (commodities and passengers) hotels, movie theatres, power plants, etc.
Method # 7 Operating cost:
This is a more detailed application of process costing. It includes costing by all operations. This method is used when there is a repetitive mass production with many operations. The main purpose of this method is to see the cost of each operation.
For example, manufacturing a bicycle handlebar involves many operations such as cutting a steel plate into appropriate strips, forming, machining, and finally polishing. The cost of these operations can be viewed individually. Operating costs provide a detailed analysis of costs to achieve accuracy and apply to industries such as spare parts, toy manufacturing, and engineering.
Method # 8 Multiple Costing:
Also known as compound costing. This refers to a combination of two or more of the above costing methods. It is used in the industry where multiple parts are manufactured separately and assembled into a single product.
Q3. How do we prepare cost sheet.
Ans. Cost statements may be displayed in the form of ledger accounts called "production accounts." Production accounts analytically present production cost information according to double-entry bookkeeping. Production costs and profits can be calculated in this ledger. The cost sheet and production account are as follows:
Cost sheet
A cost sheet is a device used to determine and display costs in unit costing. This is a statement of costs incurred at each level of manufacturing a product or service. The cost sheet takes into account all the factors of cost. This includes prime costs, factory / manufacturing costs, manufacturing costs, selling costs, profits / losses, and more.
According to C.I.M.A, London
Cost schedule or document that provides a detailed cost assembly estimated for a cost center or cost unit."
Items excluded from the cost sheet:
1. Pure financial costs such as capital interest, interest on loans, discounts on corporate bonds, loss on sale of allowance for doubtful accounts, amortization of bad debts, copyrights and reserves.
2. Pure financial income such as interest received, gain on sale of investment, dividend received, rent received, commission received, discount received.
In addition to the above, the budget limit does not include the budget limit.
Q4. Define Production account with its format.
Ans. A production account is a statement in a ledger account format cost or cost sheet that shows the output for a particular period, the total and unit costs incurred during that period, and its components, and the profits or losses for that period.
According to Glover and Williams, "The term manufacturing account is used to describe a particular type of manufacturing account created in combination with a financial account to indicate the actual manufacturing cost of goods manufactured during the review period. Used. These accounts may be created at short intervals. Monthly.
The production account is created in the format in which the transaction account is created. There are usually two parts. The first part shows the total cost and the cost per unit. The second part shows the cost of goods sold and the cost of goods sold.
When the details of a cost table or production statement are displayed in the form of a ledger account, it is called a production account. In addition to manufacturing costs, selling and distribution costs are also included. It is created in three parts. The first part shows the manufacturing cost, the second part shows the cost of goods sold, and the third part shows the cost of goods sold or total cost for that period. Here is a sample production account:
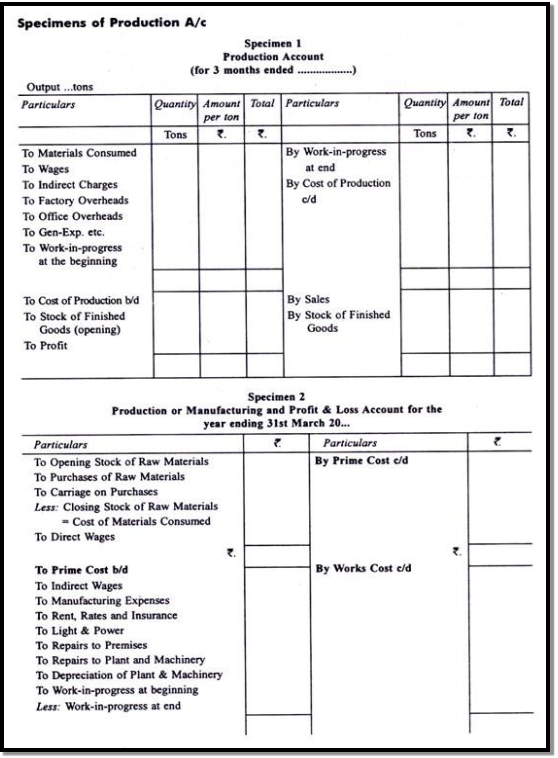
Q5. Write note on Process costing.
Ans. Process costing is a method of costing under which all costs are accumulated for each stage of production or process, and the cost per unit of product is ascertained at each stage of production by dividing the cost of each process by the normal output of that process.
Definition:
CIMA London defines process costing as “that form of operation costing which applies where standardize goods are produced”
Features of Process Costing:
(a) The production is continuous
(b) The product is homogeneous
(c) The process is standardized
(d) Output of one process become raw material of another process
(e) The output of the last process is transferred to finished stock
(f) Costs are collected process-wise
(g) Both direct and indirect costs are accumulated in each process
(h) If the revise stock of semi-finished goods, it is expressed in terms of equal units
(i) The total cost of each process is divided by the normal output of that process to find out cost per unit of that process.
Advantages of process costing:
1. Costs are be computed periodically at the end of a particular period
2. It is simple and involves less clerical work that job costing
3. It is easy to allocate the expenses to processes in order to have accurate costs.
4. Use of standard costing systems in very effective in process costing situations.
5. Process costing helps in preparation of tender, quotations
6. Since cost data is available for each process, operation and department, good managerial control impossible.
Limitations:
1. Cost obtained at each process is only historical cost and are not very useful for effective control.
2. Process costing is based on average cost method, which is not that suitable for performance analysis, evaluation and managerial control.
3. Work-in-progress is generally done on estimated basis which leads to inaccuracy in total cost calculations.
4. The computation of average cost is more difficult in those cases where more than one type of products is manufactured and a division of the cost element is necessary.
5. Where different products arise in the same process and common costs are prorated to various costs units. Such individual products costs may be taken as only approximation and hence not reliable.
Q6. How do we allocate joint costs?
Ans. There are two common ways to allocate joint costs. The calculation method is as follows.
Allocate based on sales. Sum all manufacturing costs up to the split point, determine the sales value of all joint products at the same split point, and assign costs based on the sales price. If there are by-products, do not allocate costs to them. Instead, you charge the cost of goods sold as revenue from the sale. This is the simpler of the two methods.
Allocate based on gross profit. Sum the costs of all processing costs incurred by each joint product after the split point and deduct this amount from the total revenue each product ultimately earns. This approach requires additional cost accumulation work, but may be the only viable alternative if the selling price of each product at the point of split cannot be determined (of the calculation method described above). As in the case).
Pricing for joint products and by-products
The costs allocated to joint products and by-products should not be related to the pricing of these products, as they are not related to the value of the items sold. Prior to the split point, all costs incurred are sunk costs and do not affect future decisions such as product prices.
The situation is quite different when it comes to costs incurred after the split point. Do not set the product price below the total cost incurred after the split point, as these costs can be attributed to a particular product.
If the lower limit of the price of a product is only the total cost incurred after the split point, this may result in a lower price than the total cost incurred (including the cost incurred before the split point). A strange scenario occurs. .. Obviously, charging such a low price is not a viable alternative in the long run, as companies will continue to suffer losses. This offers two alternative prices.
Short-term price. If market prices cannot be raised to sustainable levels in the long run, it may be necessary to allow very low product prices in the short run, even if they are close to the sum of costs incurred after the split point.
Long-term price. In the long run, companies need to set prices to achieve revenue levels that exceed total production costs. Otherwise, there is a risk of bankruptcy.
That is, if the individual product price cannot be set high enough than to offset the production cost, and the customer does not want to accept the higher price, then the different co-products can be set.
An important point to remember about cost allocation related to joint products and by-products is that the allocation is simply an expression, not related to the value of the product to which the cost is allocated. The only reason to use these allocations is to achieve valid sales costs and inventory valuations under the requirements of various accounting standards.
Q7. Define Contract Costing.
Ans. Contract costing, unlike short-term jobs, is a special system of job costing that applies to long-term contracts. Contract costing applies primarily to civil engineering and engineering projects, shipbuilding, road and rail contracts, bridge construction, and more. Contract costing may be a sort of specific order costing. This applies to contracts that take a considerable amount of time to complete and fall into different accounting periods. However, periods longer than one year are not an essential feature of long-term contracts. Some contracts with a term shorter than one year should be accounted for as long-term contracts if they are significant enough for the activity of that term.
CIMA defines contract costs and contract costs as follows:
The total price related to one contract specified as a price unit."
Features of contract costing:
Contracts to which contract costing applies have the following features:
(A) The contract is based on the special requirements of the customer.
(B) The contract period is relatively long.
(C) Contract work is done on-site, unlike manufacturing under the roof.
(D) Contract work mainly consists of construction activities.
Accounting procedure for contract costing:
If there are many contracts, an identification number and name are given to each contract for accounting and management reasons. A separate contract account is maintained for every contract.
All costs associated with the contract will be charged to each contract account. In the contract cost structure, the majority of spending is of a direct nature in the form of materials, wages, plant and store use, direct costs, etc., and only a small portion is charged as allocated overheads.
Q8.What is the accounting procedure of cost?
Ans. Accounting Treatment of Costs:
1. Material:
(A) All materials purchased for the contract or sent to the site will be charged for the contract.
(B) If the material is returned to the store, or is on an unused site, or if the material is transferred to another contract site, it will be credited to the contract account.
(C) If the material is not needed immediately, the material will be stored and its costs will be debited to the stock account.
2. Labor:
All labor employed or worked in the field is treated as direct labor and all costs associated with them are charged to the contract account. Salaries and incentives for management and supervisory staff of a particular contract are also charged for that particular contract.
3. Plants:
(A) If the plant is hired, the employment fee will be charged to the contract account.
(B) If the plant was specially purchased for a contract or the plant was sent to the site, the value of the plant is debited to the contract account. The value of the returned or remaining on-site plant will be credited to the contract account. The balance between the debited amount and the credited amount in the contract represents the value of the plant used in the field.
(C) The depreciation amount provided by the plant may be debited to the contract account instead of displaying the value of the plant issued to the site and remaining on the site.
4. Subcontract fee:
Part of the contract work may be provided on a subcontract basis and payments made in the subcontract work may be debited to the contract account.
5. Overhead:
General overhead and head office expenses are fairly distributed to different contracts, and some overhead is charged to the contract account.
6. Difficulty of cost control:
Contracts are generally large and contract work is done on-site. This causes some problems with material use, labor utilization, labor supervision, plant and work damage, material and tool theft, and more. This site-based work makes it difficult to control the cost of contracts.
7. Surveyor Certificate and Deposit:
In contract work, surveyors, architects, and civil engineers visit the site on a regular basis to inspect the completed work. He issues a certificate stating the completion stage of the work and the value of the work completed by the certificate issuance date. Payment will be released to the contractor by the contractor based on the certificate.
Payments are typically released only up to a certain percentage, for example 80% of certified work. The balance of certified work is retained by the contractor until the entire contract is successfully completed.
The amount of money so reserved is called a "reservation". The contractor does so to protect itself from the risks that may arise from the contractor. Generally, the percentage of retained earnings is up to 20% of the amount of certified work.
8. Work in progress:
The amount of work in process includes the value of certified and uncertified work in process as it appears in your contract account.
9. Cost of running contract:
Due to the long-term nature of the contract, it was necessary to determine the profit attributable to each accounting period. For long-term contracts, it is believed that the results can be evaluated with reasonable certainty before they are signed, and imputed profits should be carefully calculated and included in the current account.
The profits taken up should be based on the principles of standard costing. For completed contracts, all profits arising from the contract can be transferred to the income statement.
However, in the case of an incomplete contract, preparations are made to deal with unforeseen circumstances and unexpected losses, so depending on the scope of work completed in the contract, only part of the profit is reflected in the income statement will be done. There are no strict rules for calculating profits reflected in the income statement.
However, in general, the following principles are followed:
(1) If an incomplete contract causes a loss, the entire loss will be debited to the income statement.
(2) Profit should only be considered for certified jobs. Uncertified work should be evaluated at cost.
(3) Contract completion is less than 25% of the contract price – no profit should be recorded on the income statement and the entire amount is retained as a reserve for contingencies.
(4) Contract completion up to 25% or more, less than 50% of the contract price – in this case, one-third of the profit, a decrease in the ratio of cash received to the certified work will be reflected in the profit and loss account. The balance remains as a reserve in case of contingency.
(5) Contract completions up to 50% or more and less than 90% – in this case, two-thirds of the profit is reduced by the percentage of cash received for the work authorized to be brought into the income statement, leaving the rest Keep up. The amount of reserve.
The formula is given below:
Q9.How do we calculate Profit of unfinished contracts.
Ans. Contracts that start and end during the same fiscal year do not cause accounting problems. However, for contracts that take more than a year to complete, the question arises whether the profits of the contract are calculated only at the completion of the contract or at the end of each fiscal year for partially completed work. If you calculate the profit only when the contract is completed, the profit in the year when the contract is completed will be high, but as in the years of other contract work, the profit will be zero.
This will not only distort profit patterns, but will also result in higher tax obligations as you may have to pay higher tax rates of income tax. Therefore, if the contract period exceeds one year, it is necessary to consider the profits and losses gained from each year's business. This helps avoid distortions in the business's year-to-year profit trends.
There are two aspects to profit calculation.
(1) Calculation of expected profit or estimated profit, and
(2) Calculation of the portion of such profit that is transferred to the income statement.
The portion of the expected or estimated profit transferred to the income statement depends on the stage of completion of the contract. Prudent demands that the sum of the expected profits should not be transferred to the income statement, some of which should be withheld as reserves for unforeseen future costs or contingencies. There are no strict rules in this regard. However, in this context, you can follow the following general rules:
1. First rule:
If the certified work is less than 1/4 of the contract price, the profit will not be transferred to the income statement. It is based on the principle that profits should not be taken into account unless the contract is reasonably advanced.
2. Second rule:
If the certified job is more than 1/4 of the contract price and less than 1/2, one-third of the profit is usually remitted to the income statement. The balance will be treated as a reserve. Therefore, the profit transferred to the income statement is calculated by the following formula –
3. Third rule:
If the certified work is more than 1/2 (i.e. 50%) of the contract price and less than 9/10 (i.e. 90%), the profit transferred to the income statement is calculated by:
4. Fourth rule:
If the contract is nearly complete, the estimated profit should be calculated for the entire contract. The percentage of estimated profit transferred to the income statement is calculated using one of the following formulas:
5. Fifth Rule – Loss of Incomplete Contracts:
If you incur losses on an incomplete contract, you must transfer them all to your income statement.
Q10. What is Work in process account?
Ans. If the contract is not completed by the end of the fiscal year, the incomplete work is recorded in the work in process account. The work-in-process account is created by debiting this account, the account for authenticated and unauthenticated work, and crediting the reserve profit, that is, part of the profit that was not transferred to the profit and loss account. The difference between a debit and a credit is work in process, but all cash received for such an incomplete contract is shown as a deduction while it is shown on the balance sheet.
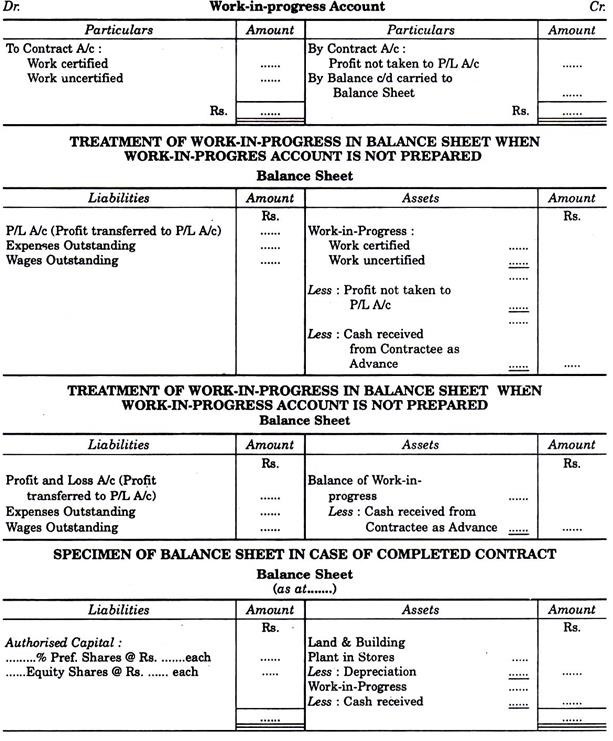