UNIT-4
CORROSION
Q1)Define corrosion and classify them?
Corrosion: -
- The destruction of metal by chemical or electrochemical attack of environment this process starting at the surface of metal known as corrosion.
Classification of corrosion – Dry and Wet corrosion
2 types of corrosion on basis of corrodent / corrosion material
- Dry corrosion
- Wet corrosion
Dry corrosion: -
- Corrosion occurring due to direct attack of atmospheric gases like o2, co 2, so2, c12 moisture etc and by not flowing liquids is called as dry corrosion.
Rate of dry corrosion depends upon: -
- Temperature
- Moisture
- Chemical affinity between metal and gases
- Nature of oxide layer
Wet or Electrochemical theory of Corrosion: This corrosion occurs in metals that come in direct contact with a conducting liquid of two different metals are dissolved in a solution partly. There is formation of galvanic cell on the metal, as part of the metal acts as an anode and the rest is the cathode, the chemical in the solution along with the humidity acts as the electrolyte. Oxidation takes place in such conditions resulting in corrosion at the anode surface and reduction occurs at the cathode surface of the metal. In this case corrosion occurs at the anode but rust gets deposited on the cathode.
Q2)List the factors that influence corrosion?
A] Nature of metal
B] nature of environment
Nature of metal: -
Position of metal in galvanic series: -
- When 2 metals are in the contact in the presence of the electrolyte then more active metal undergo corrosion.
- Greater the difference in their positions, higher is the rate of corrosion.
Relative areas of anode and cathode: -
- If the anode < cathode then rate of corrosion.
- If the cathode < anode
Purity of metal: -
- Pure metal resists the corrosion
- Rate of corrosion increases with increases in of impurities which from galvanic cells.
Physical state: -
- Smaller the grain size of metal alloy greater the mate of corrosion.
e.g: - steel get corroded fast than the cost iron because
Grain size of steel < grain size of cast ion.
Nature of oxide film: -
- If oxide layer – porous
Then corrosion take place
- If oxide layer – nonporous
Then no corrosion takes place
Over – vtg (over – potential): -
- To restore position of metal some extra VTG is required is called as over –vtg
- Higher the over vtg less is the rate of corrosion.
e.g.: -Zn, Pb, Cr, Ni, etc.
B] nature of environment: -
1) temperature: -
- Higher is temperature higher is the rate of dry corrosion because attacking gas and metal get activated @ higher temp.
- Higher is the temperature higher is rate of wet corrosion because: -
High tempo, according to nearest equation electrode potential is high.
2) Moisture: -
- Higher is the moisture
Higher is the rate of dry and wet corrosion
3) PH: -
- Generally acidic media have more corrosive effect on metals.
4) conductivity of medium: -
- High the electrical conductivity of aq. Conducting medium higher is the rate of corrosion.
5) nature of ions: -
- Cl -, no3 – have the ability break nonporous oxide layer and cause wet corrosion.
- Presence of oxalate, m phosphate and silicate ions have the ability to slow down rate of wet corrosion.
Q3)Wet corrosion mechanism elaborate?
Mechanism of wet corrosion: -
- Reaction on anode: -
- Metal atoms on the surface of anode pass into conducting medium by forming metal ions, leaving behind electrons.
M – m+n + ne-
2. Reaction on cathode: -
- The electrons left on anodic part, flow to the cathodic part depending upon the nature of conducting medium they bring about one of the following reactions: -
a) H2 liberation (H2 Evolution): -
- If the corroding medium is acidic then H + ions from the medium capture the electrons from the cathode and there is liberation of H2 gas taking place.
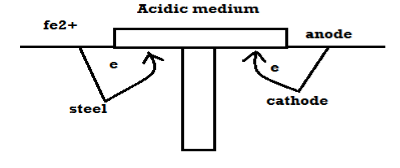
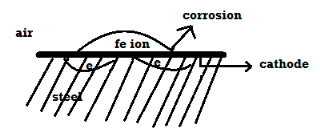
b) O2 absorption: -
- If the corroding medium is neutral or slightly alkaline containing some oxygen gas dissolved the reaction of o2 absorption takes place on the cathode.
A) Plating: -
- If the cathodic part is in the contact with ions of lower plotted metal in the galvanic series, then the ions deposit on the cathode.
+ 2e- - cl (atcathode)
Q4)Differentiate between Galvanic series and EMF series?
EMF series and galvanic series
EMF series | Galvanic series |
|
|
|
|
|
|
|
|
|
|
|
|
|
|
Q5)Explain the four types of oxide layers?
4 types of oxide layers: -
- Porous oxide layer (non – protective): -
- If the oxide layer is porous then through pores – penetration of o2 gas taking place and metal get corroded.
e.g.: - fe,Mg,Na,K,Ca, etc
Reaction: - 2fe + o2 – 2feO
2Mg + o2 – 2MgO
2. Non – porous oxide layer (protective): -
- If the oxide layer is stable non – porous strong then further corrosion of metal will be stopped.
e.g.: - chromium, nickel, Sn (tin), lead, aluminium, zinc, bronze, various metal alloys.
Reaction: - 1. 2AL + O2 – AL2O3
3. Unstable oxide layer: -
- When oxide layer is unstable, and it decomposes back into metal and o2 gas then there is no corrosion of metal taking place.
e.g.: -Ag, AU, Pt.
4. Volatile oxide layer: -
- If the oxide layer is volatile, then its evaporation taking place the under lying metal gets exposed for further attack of o2 gas and corrosion taking place.
e.g.: - MO2O3 (molybdenumoxide)
Dillingbedworth rule / ratio (PBR)
- This rule gives an idea about nature of oxide film, whether it is porous or nonporous.
- The rule states that, Metal ‘if the volume of oxide < volume of metal consumed
Then,
Oxide layer – porous
Else, oxide layer – nonporous
PBR =
If, PBR > 1 but PBR < 1.45
Metal oxide layer – nonporous(protective)
Q6)Explain the mechanism of dry corrosion to other gases?
Mechanism of dry corrosion due to other gases: -
a) Dry corrosion due to chlorine: -
Reaction: - 1. 2Ag + Cl2 – 2AgCl
Agcl forms thin protective (non-porous) layer on the metal surface.
Non corrosion taking place
Sn + 2cl2 – SnCl4
SnCl4 forms thin, non-protective layer on the metal surface
Corrosion taking place
b) Due to So2: -
- Sulphur oxide is produced due to combustion of fossil fuels. When So2 attacks on metallic surface in the form of H2So4, corrosion of metal taking place.
Reaction: - SO2 + H2O – H2SO3
SO2 + H2O ½ O2 – H2SO4
c) Due to oxides of nitrogen: -
- Oxides of nitrogen are produced due to combustion of fuels it forms HNO3 which cause corrosion of metal.
Reaction: - NO2 + O3 – NO3 + O2
NO 2 + NO3 – N2O5
N2O5 + H2O – 2HNO3
d) Decarburisation: -
- The processes of removal of carbon of carbide from the metal by action of hydrogen at higher temperature is called as decarburisation.
e) H2 embrittlement: -
- Breaking of metal at the weekend region by hydrogen accumulation in metal called as H2 embrittlement.
f) Presence of co2: -
- Due to co2 formation of h2co3 taking place and it reacts with metal to occur corrosion.
H2O + co2 – H2CO3
Fe + CO2 – FeO + CO
Q7) Determine any one method to measure corrosion?
The internal and external corrosion of metallic structures, is monitored and measured through a quantitative method called, weight loss method. This method involves recording the difference in weight over specific time intervals. Since this method deals with time and weight it is one of the simplest methods for monitoring corrosion. It is carried out in a certain environment and the design of the material also is counted.
Coupons are the main characteristic of the weight loss analysis, in the process the coupons are placed in a specific environment, the specimen is removed after a specific interval of time, they are then cleaned for the net weight, and finally the difference in weight according to the specified time is recorded.
The recorded data is put on a known engineering formula and thus generate the corrosion rates. The time period for the exposure of the coupon is around 60-180 days this depends on the efficiency required. For accurate information the analysis requires a reliable equipment, but most laboratories prefer 90 days’ time period.
It also forms a suitable method to determine the levels of corrosion in intricate structures. Apart from corrosion rates, the data from the analysis can be used to estimate the thickness reduction
. A weighed sample (coupon) of the metal or alloy under consideration is introduced into the process, and later removed after a reasonable time interval. The coupon is then cleaned of all corrosion product and is reweighed. The weight loss is converted to a corrosion rate (CR) or a metal loss (ML), as follows:

Q8) Define tinning?
Tinning: -
Method: -
- Coating of tin on a base metal i.e., steel iron is called as tinning.
- The steel article is cleaned well and then passes through molten tin bath which is maintained at temp 240c.
- Then, the article is allowed to pass through palm oil bath which protects the hot tin coated surface against corrosion.
- Then the article is allowed to pass through to make uniform coating layer to remove excess of tin.
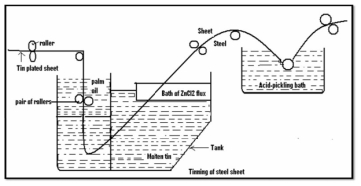
Applications: -
- Tin has greater corrosion resistivity and better glaze
- Food material can be stored in tin containers
- CV wire before involution by rubber are tinned.
- Tinned or brass vessels or sheets are used for making cooking vensiles and parts of reflectors.
Q9) Explain the methods of corrosion control?
Principle: -
The metal to be protected is forced to behave as cathode.
2 types: -
A) By using sacrificial anode
Methods / processes: -
- The metallic structure to be protected from corrosion is connected to the anodic metal by insulated wire.
- Anodic metal is more reactive like Zn etc.
- Anodic metal corrosion itself but it protects the cathodic metal from corrosion .it is called as sacrificial metal.
- Anodic metal is kept in back fill (mixture of coal and Nacl) to increase electrical contact with surrounding soil.
- When anodic metal consumed completely then it is replaced with fresh piece of metal
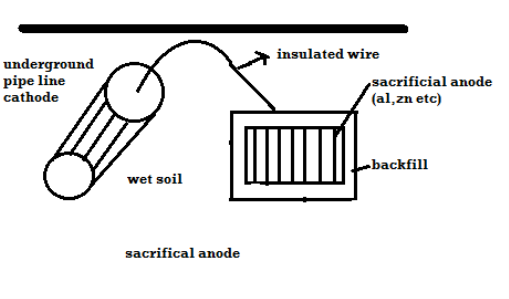
B) By using impressed current: -
Method: -
- In this method an impressed current is applied in opposite to nullify the corrosion current and convert the corroding metal from anode to the cathode.
- The impressed current Is derived from DC source and given to insoluble anode like graphite, stainless steel which buried in soil.
- The –ve terminal of DC source is connected to pipeline to be protected from corrosion.
- Anodic metal is kept in black fill to increase electrical contact with the surrounding soil.
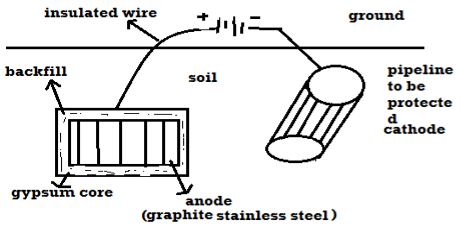
Limitations: -
- Highly investment and maintenance cost
- Special case needs to be taken to see the structure is not over protected otherwise H2 liberation maybe occur.
B] anodic protection: -
Principle: -
A metal or alloy having wider range of passivity vtg, is made anode and the vtg is passivity range is applied over it do control its corrosion even by strong corroding media.
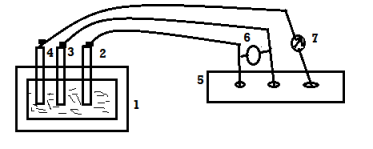
- The metallic installation (reactor, water, tank, water coolers, industrial condensers, etc.) is made anode by using reference electrode and axillary electrode.
- There is a potentiostatfor applying the desired ammeter to watch the corrosion current. The min or negligible current indicates that anodic protection take place successfully if the system goes out of corrosion control, then immediately remove all electrical connection.
Application: -
- Chemical reactors
- Industrial water coolers
- Complex metallic installations on ground or under sea water.
- Industrial metals condensers
- Pipelines for carrying corrosive liquids.
Advantages: -
- Low operating cost
- It is applicable for highly corrosive media
- Suitable to protect complex structures
- Protection current gives an idea about rate of corrosion.
Limitations: -
- High installation cost
- High starting current is req.
- In case system goes out of control then high is the rate of corrosion
It is applicable for only those metals which show active – passive behaviour.
Q10)What do you understand by galvanizing?
Galvanizing: -
Method: -
- Coating of Zn on the steel or iron is called as galvanizing.
- Steel article is cleaned well with dil H2SO4 then with water and dry it.
- Then the steel article is dipped in molten Zn bath and it is maintained at the temp 425 – 450 c.
- The molten Zn bath is covered with flux.
- Then the article is allowed to pass through to mate uniform coating layer and to remove excesses of Zn.
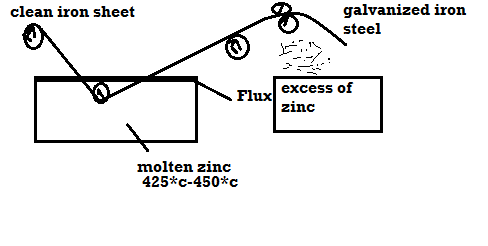
Applications: -
- Various galvanized iron (G.I) articles are used.
- It is useful for the protection of iron.