UNIT 1
MATERIALS
QUESTIONS
Question 1) What Are the Main Differences Between Charpy and Izod Impact Testing?
Answer 1)
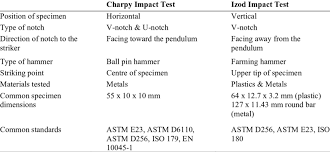
Question 2) What are the Factors which Affecting Izod Impact Energy
Answer 2) Factors that affect the Izod impact energy of a specimen will include:
• Yield strength and ductility
• Notches
• Temperature and strain rate
• Fracture mechanism
Yield Strength and Ductility
For a given material the impact energy will be seen to decrease if the yield strength is increased, i.e. if the material undergoes some process that makes it more brittle and less able to undergo plastic deformation. Such processes may include cold working or precipitation hardening.
Notches
The notch serves as a stress concentration zone and some materials are more sensitive towards notches than others. The notch depth and tip radius are therefore very important.
Temperature and Strain Rate
Most of the impact energy is absorbed by means of plastic deformation during the yielding of the specimen. Therefore, factors that affect the yield behaviour and hence ductility of the material such as temperature and strain rate will affect the impact energy.
This type of behaviour is more prominent in materials with a body centred cubic structure, where lowering the temperature reduces ductility more markedly than face centred cubic materials.
Fracture Mechanism
Metals tend to fail by one of two mechanisms, micro void coalescence or cleavage. Cleavage can occur in body centred cubic materials, where cleavage takes place along the {001} crystal plane. Micro void coalescence is the more common fracture mechanism where voids form as strain increases, and these voids eventually join together and failure occurs. Of the two fracture mechanisms cleavage involved far less plastic deformation ad hence absorbs far less fracture energy.
Ductile to Brittle Transition
Some materials such as carbon steels undergo what is known as a ‘ductile to brittle transition’. This behaviour is obvious when impact energy is plotted as a function of temperature. The resultant curve will show a rapid dropping off of impact energy as the temperature decreases. If the impact energy drops off very sharply, a transition temperature can be determined. This is often a good indicator of the minimum recommended service temperature for a material.
Question 3) Explain Izod Impact Testing Procedure?
Answer 3) once that the correct pendulum energy has been selected; clamp the specimen firmly in the vice. The specimen is clamped so that it is vertically cantilevered with the notch surface facing the direction of impact. The vice should be equipped with an adjustable stop and a notch centering jig which will aid in positioning the specimen in the same position for each determination. The pressure used to clamp the specimens can also be a source of variation in the test results. Too much pressure may damage a specimen while too little will cause the specimen too move in the vice resulting in erroneous readings. A torque wrench should be used to ensure consistent clamping pressure on the specimen.
Latch the pendulum in its upright position. After making sure that the swing plane of the pendulum arm is clear, release the pendulum and allow it to break the specimen.
Question 4) Draw a classification tree of engineering materials?
Answer 4)
Question 5) Explain the difference between cast iron and carbon steel?
Answer 5)
One of the most popular ways to make lasting and quality components is through castings. Casting allows for a high level of detail, which results in not needing and additional fabrication or assembly. While many different materials can be cast, steel and iron are the two most popular due to their excellent mechanical properties for a wide range of applications.
CAST IRON usually refers to gray iron, ductile iron and malleable iron. Which is an iron casting with carbon content higher than 2%.
CAST STEEL usually refers to normal carbon steel and alloy steel. Which is a steel casting with carbon content lower than 2%.
Therefore, no big difference from the chemical content and raw materials for cast iron vs cast steel.
Corrosion Resistance
When it comes to corrosion, iron has better corrosion resistance than steel. That doesn't mean that either is impervious to corrosion though. When left unprotected, both metals will oxidize in the presence of moisture. Eventually, they will completely decompose. To prevent this, the coating is recommended for both steel and iron castings.
Cost
Cast iron is often cheaper than cast steel because of the lower material costs, energy, and labor required to produce a final product. While raw steel is more expensive, there are, however, prefabricated forms of steel. Those include sheets, rods, bars, tubes, and beams.
Castability
Cast iron is relatively easy to cast, as it pours easily and doesn't shrink as much as steel. This flowability makes cast iron an ideal metal for architectural or ornate ironwork structures such as fencing and street furniture.
Question 6) Explain the advantage and disadvantage of cast iron and cast steel?
Answer 6) the advantage and disadvantage of cast iron are given below:
The grey cast iron's good casting properties are: good vibration damping, good wear resistance, good machinability and low notch sensitivity. However, its tensile strength and elongation are very low. So, it can only produce some metal parts with low physical requirements. Requirements such as protective cover, cover, oil pan, hand wheels, frame, floor, hammer, small handle, base, frame, box, knife, bed, bearing seat, table, wheels, cover, pump, valve, pipe, flywheel, motor blocks etc. As for the higher grades, grey cast iron can withstand greater load and a certain degree of tightness or corrosion resistance. This allows for some of the more important castings such as cylinder, gear, base, flywheels, bed, cylinder block, cylinder liner, piston, gear box, brake wheel, coupling plate, medium pressure valve, etc
The ductile iron and malleable iron have high strength, ductility and heat-resistance and toughness. So a wider application, in some cases, can replace the carbon steel. However, its production technology is high. The production process is more complex. This makes the production cost higher than normal grey cast iron and cast steel. Therefore, there are more casting defects for ductile iron. There are many fields that use ductile iron, such as pressure pipes and fittings, automotive applications, agriculture, road and construction applications and general engineering applications.
The advantage and disadvantage of cast steel
The main advantage of cast steel is the design flexibility. The designer of the casting has the greatest freedom of design choices. This allows for complex shapes and hollow cross-section parts.
Cast steel has the metallurgy manufacturing flexibility and strongest variability. One can choose a different chemical composition and control that is adapted to the various requirements of different projects. This offers different heat treatment choices in the larger context of the mechanical properties and performance. Also offering good weld-ability and workability.
Cast steel is a kind of isotropic material and can be made into the overall structural strength steel castings. This improves the reliability of the project. Coupled with the design and weight, the advantages of short delivery time, price and economy gives cast steel a competitive advantage.
The weight range of steel castings is larger. Little weight can be only a few dozen grams of molten mould precision castings. The weight of large steel castings goes up to several tons, dozens of tons or hundreds of tons.
Steel castings can be used for a variety of working conditions. Its mechanical properties are superior to any other casting alloys and a variety of high-alloy steel for special purposes. To withstand high tensile stress or dynamic load of components, it is important to consider pressure vessel castings. In low or high temperature, large and important part load key parts should give priority to steel castings.
However, cast steel has comparatively bad shake-suction, wear resistance and mobility. The casting performance, compared to cast iron, is bad. Also, the costs are higher than normal cast iron.
Question 7) What is Stress?
Answer 7) when the deforming force is applied to an object. The object deforms. In order to bring the object back to the original shape and size, there will be an opposing force generated inside the object.
This restoring force will be equal in magnitude and opposite in direction to the applied deforming force. The measure of this restoring force generated per unit area of the material is called stress.
Thus, Stress is defined as “The restoring force per unit area of the material”. It is a tensor quantity. Denoted by Greek letter σ. Measured using Pascal or N/m2. Mathematically expressed as –
σ=F / A
Where,
- F is the restoring force measured in Newton or N.
- A is the area of cross-section measured in m2.
- σ is the stress measured using N/m2 or Pa.
Stress Units
Stress can be expressed using multiple units. Refer to the table given below for Stress units.
System of units | Stress units |
Fundamental units | Kg.m-1.s-2 |
SI (derived units) | N.m2 |
SI (derived units) | Pa or Pascal |
SI (mm)(derived units) | M.Pa or N/(mm)2 |
US unit (ft) | Lbf/ft2 |
US unit (inch) | Psi (lbf/inch2) |
Types of Stress
There are several types of stress in physics but mainly it is categorized into two forms that are Normal Stress and Tangential or Shearing Stress. Some stress types are discussed in the points below.
Normal Stress:
As the name suggests, Stress is said to be Normal stress when the direction of the deforming force is perpendicular to the cross-sectional area of the body. The length of the wire or the volume of the body changes stress will be at normal. Normal stress can be further classified into two types based on the dimension of force-
- Longitudinal stress
- Bulk Stress or Volumetric stress
Longitudinal Stress:
Consider a cylinder. When two cross-sectional areas of the cylinder are subjected to equal and opposite forces the stress experienced by the cylinder is called longitudinal stress.
Longitudinal Stress = Deforming Force / Area of cross-section = F/A
As the name suggests, when the body is under longitudinal stress-
- The deforming force will be acting along the length of the body.
- Longitudinal stress results in the change in the length of the body, Hence thereby it affects slight change in diameter.
The Longitudinal Stress either stretch the object or compress the object along its length. Thus, it can be further classified into two types based on the direction of deforming force-
- Tensile stress
- Compressive stress
Tensile Stress
If the deforming force or applied force results in the increase in the object’s length then the resulting stress is termed as tensile stress. For example: When a rod or wire is stretched by pulling it with equal and opposite forces(outwards) at both ends.
Compressive Stress
If the deforming force or applied force results in the decrease in the object’s length then the resulting stress is termed as compressive stress. For example: When a rod or wire is compressed/squeezed by pushing it with equal and opposite forces(inwards) at both ends.
Bulk Stress or Volume Stress
When the deforming force or applied force acts from all dimension resulting in the change of volume of the object then such stress in called volumetric stress or Bulk stress. In short, when the volume of body changes due to the deforming force it is termed as Volume stress.
Shearing Stress or Tangential Stress
When the direction of the deforming force or external force is parallel to the cross-sectional area, the stress experienced by the object is called shearing stress or tangential stress. This results in the change in the shape of the body
Question 8) what is Strain?
Answer 8)
The strain is the amount of deformation experienced by the body in the direction of force applied, divided by initial dimensions of the body. The relation for deformation in terms of length of a solid is given below.
ϵ= δl / L
Where,
ϵ is the strain due to stress applied
δl is the change in length
L is the original length of the material.
The strain is a dimensionless quantity as it just defines the relative change in shape.
Depending on stress application, strain experienced in a body can be of two types. They are:
● Tensile Strain: It is the change in length (or area) of a body due to the application of tensile stress.
● Compressive Strain: It is the change in length (or area) of a body due to the application of compressive strain
When we study solids and their mechanical properties, information regarding their elastic properties is most important. These can be obtained by studying the stress-strain relationships, under different loads, in these materials.
Question 9) writes the types of alloy steel?
Answer 9) Types of alloy steel
There are multiple subcategories of alloy steel. These include:
1) Low-alloy steel
2) High-strength low alloy (HSLA) steel
3) High-alloy steel
4) Stainless steel
5) Micro alloyed steel
6) Advanced high-strength steel (AHSS)
7) Maraging steel
8) Tool steel
Question 10) Explain Stress Concentration?
Answer 10)
When an axial load is applied to a piece of material with a uniform cross-section, the norm al stress will be uniformly distributed over the cross-section. However, if a hole is drilled in the material, the stress distribution will no longer be uniform. Since the material that has been removed from the hole is no longer available to carry any load, the load must be redistributed over the remaining material. It is not redistributed evenly over the entire remaining cross-sectional area but instead will be redistributed in an uneven pattern that is highest at the edges of the hole as shown in the image. This phenomenon is known as stress concentration.