Question Paper
Unit 04
Q-1What are the different types of polymerization?
Answer:
- Addition polymerization or chain polymerization
- Condensation or step or step growth polymerization
- Copolymerisation
Q-2Explain Copolymerization.
Answer: Addition polymerisation involving a mixture of two or more suitable or compatible monomers gives a copolymer and the process is known as copolymerization. A reaction in which a mixture of two or more monomers is allowed to undergo polymerisation is known as copolymerization. The polymer is known as copolymer.
E.g.: Copolymerisation of styrene and methyl methacrylate
Q-3Explain in brief free radical polymerization.
Answer: The formation of polymer from the successive addition of free-radical building blocks through the polymerization is called as the free radical polymerization. In order to obtain the wide variety of different polymers and material composites the free radical polymerization plays a major role in it. The relatively non-specific nature of free-radical chemical interaction make it one of the most versatile forms of polymerization which allows a facile reactions of polymeric free radical chain ends and other chemical or substrates. The monomers from which addition polymers are made are alkenes. The most common and thermodynamically favored chemical transformations of alkenes are addition reactions. Many of these addition reactions are known to proceed in a stepwise fashion by way of reactive intermediates, and this is the mechanism followed by most polymerization. The monomers are initiated by traces of oxygen, the pure compounds are stabilized by radical inhibitors.
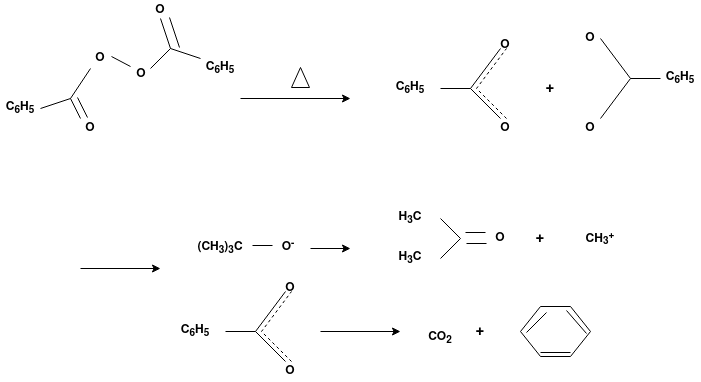
Radical Initiators
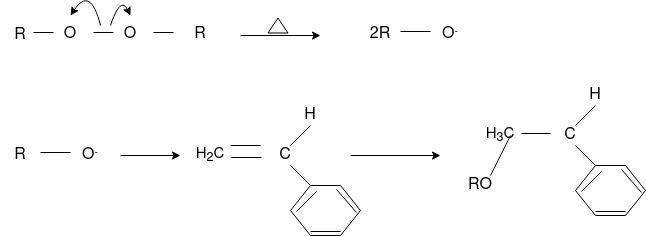
Chain Initiation
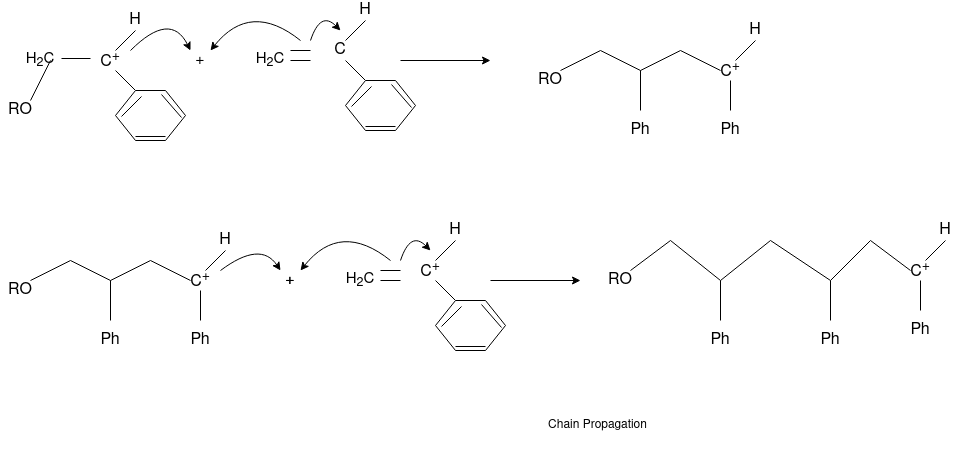
Chain Propagation
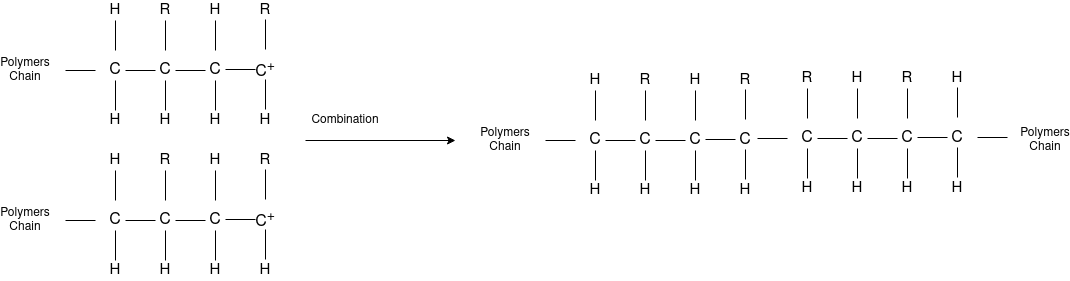
Chain Termination
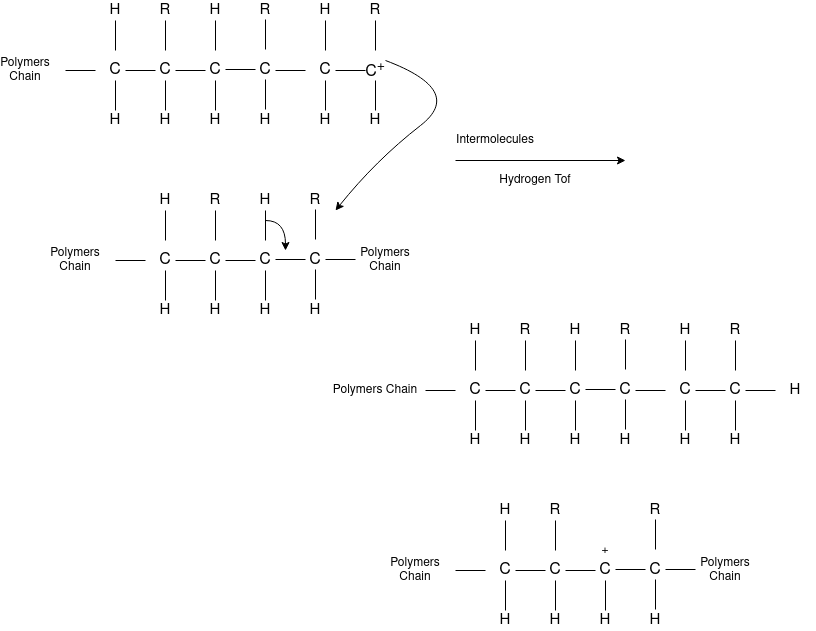
Chain Transfer Reaction
Q-4What is thermoplastic polymer?
Answer: A thermoplastic is a resin that is solid at room temperature but becomes plastic and soft upon heating, flowing due to crystal melting or by virtue of crossing the glass transition temperature (Tg). Upon processing, usually via injection-molding or blow-molding-like processes, thermoplastics take the shape of the mould within which they are poured as melt, and cool to solidify into the desired shape. The significant aspect of thermoplastics is their reversibility, the ability to undergo reheating, melt again, and change shape. This allows for additional processing of the same material, even after being prepared as a solid. Processes such as extrusion, thermoforming, and injection molding rely on such resin behavior. Some common thermoplastic materials include polyethylene (PE), polycarbonate (PC), and polyvinyl chloride (PVC).
Q-5Explain the properties of thermosetting polymer and thermoplastic polymer.
Property | Thermoplastics Polymer | Thermosetting Polymer |
Molecular Structure | Linear polymer: weak molecular bonds in a straight-chain formation | Network polymers: high level of crosslinking with strong chemical molecular bonds |
Melting point | Melting point lower than the degradation temperature | Melting point higher than the degradation temperature |
Mechanical | Flexible and elastic. High resistance to impact (10x more than thermosets). Strength comes from crystallinity | Inelastic and brittle. Strong and rigid. Strength comes from crosslinking. |
Polymerization | Addition polymerisation: repolymerised during manufacture (before processing) | Polycondensation polymerisation: polymerised during processing |
Microstructure | Comprised of hard crystalline and elastic amorphous regions in its solid state | Comprised of thermosetting resin and reinforcing fibre in its solid state |
Size | Size is expressed by molecular weight | Size is expressed by crosslink density |
Solubility | Can dissolve in organic solvents | Do not dissolve in organic solvents |
Service temperature | Lower continuous use temperature (CUT) than thermosets | Higher CUT than thermoplastics |
Q-6Explain the preparation of PMMA.
Answer: Preparation:
This is an important thermoplastic resin. It is obtained by polymerization of methyl methacrylate which is an ester of methyl acrylic acid, CH2=C(CH3)COOH, in presence of acetyl peroxide or hydrogen peroxide. It is an acrylic polymer.
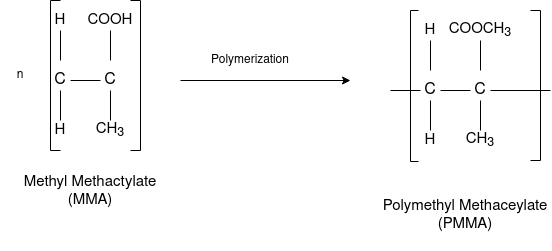
Q-7What are the uses and properties of PMMA?
Answer: Properties:
(i) It is hard, fairly rigid material with a high softening point of about 130-14rfC.
(ii) It becomes rubber like at a temperature above 6oC.
(iii) It has outstanding shape-forming properties due to wide span of temperature from its rigid state to viscous.
(iv) It has high optical transparency.
(v) It has high resistance to sunlight and ability of transmission light accurately.
Uses:
They are used for making lenses, optical parts of instruments, air craft, light fixture, artificial eyes, wind screen, bone splints, decorative articles etc. PMMA is found in paint and used in window glasses.
Q-8Explain Nylon-6 with its applications.
Answer: Nylon-6:
Nylon 6 is also called as the Polycaprolactam which is developed by Paul Schlack. They are semicrystalline polyamide.They have smooth surface and are featureless as a glass rods. Nylon 6 can be modified using comonomers or stabilizers during polymerization to introduce new chain end or functional groups, which changes the reactivity and chemical properties. It's often done to change its dyeability or flame retardance. Nylon 6 is synthesized by ring-opening polymerization of caprolactam. When caprolactam is heated at about 533 K in an inert atmosphere of nitrogen for about 4–5 hours, the ring breaks and undergoes polymerization. Then the molten mass is passed through spinnerets to form fibres of nylon 6.
On further heating of Caprolactam at 533K with inert atmosphere of nitrogen for about 4-5 hours it gives
(Nylon-6)
Application:
(i) Nylon 6 is widely used for gears, fittings, bearings and automotive industry for various parts and as a material for power tools and housings.
(ii) It is used as threads in bristles for toothbrushes, surgical sutures and strings for acoustic and classical instruments.
(iii) It is used in production of large variety of ropes, filaments, nets as well as knitted garments.
Q-9Explain Buna-S with its properties.
Answer:Buna-S is also known as the styrene-butadiene. It is a copolymer of butadiene (75%) and styrene (24%). Buna is derived from the Bu-Butadiene while Na is Sodium or Natrium and S is Styrine. Buna-S is the replacement of natural rubber while styrene, 2 monomers and butadiene play a major role in its derivation where as these 2 monomers is polymerized by two basically different process i.e., from solution (S-SBR) or as an emulsion (E-SBR). It is prepared by the copolymerization of butadiene & styrene.
It is a random co-polymer formed by the emulsion polymerization of a mixture of 1:3 butadiene and styrene in the presence of peroxide as a catalyst at 5o C and this is the reason why the product is called as cold rubber. The obtained rubber is called as the Styrene Butadiene Rubber (SBR).
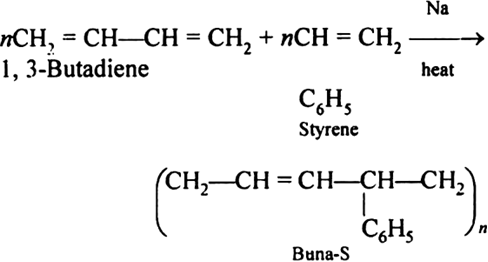
Applications:
(i) Buna-S is used as the natural rubber i.e., they are widely used in pneumatic tyres.
(ii) SBR is extensively used in coated papers.
(iii) They are highly used in building materials as a binding material.
SBR is also used as binder in lithium-ion battery electrodes.
Q-10Explain the stages involved in the Vulcanization of rubber.
Answer:
- Mixing of crude rubber with about 5-30% of sulfur (cross-linking agent) and other additives such as:
- Activator (commonly zinc oxide or stearic acid),
- Accelerator (guanidines, thiazoles, dithiocarbamates, xanthates, thiurams) ,
- Coagulants (acetic acid, calcium chloride),
- Anti-oxidants (amines, phenolics, phosphites),
- Color pigments,
- Surfacants,
- Softeners,
- Ant-foaming agents,
- Anti-tack agents (Rosin derivates, coumarone-indene resins, aliphatic petroleum resins, alkyl-modified phenol-formaldehyde resins).
Slow cross-linking starts at this stage. It is neccessary to avoid active vulcanization during mixing, which may cause cracks formation at the molding stage.
- Molding (shaping) the rubber mixture. The rubber must be shaped prior to heating stage since cross-linking makes shaping impossible.
- Heating the mixture to 250-400ºF (120-200ºC). Increased temperature speeds up the vulcanization process resulting in fast and complete cross-linking. C-S bonds replace C-H bonds linking chain polyisoprene molecules. Each link is formed by one to seven sulfur atoms.