Question Bank
Unit 05
Q- 1Explain the single component system of water.
Answer: In water there is only one component i.e., water and its phases: ice, water, steam that is solid, liquid and gaseous form.
In the figure given above, the horizontal movement leads to be responsible for temperature change while the vertical curve responsible for the pressure change. In the above figure there are three curves i.e., OA,OB,OC which represents the equilibrium conditions between two phases solid with vapour, vapour with liquid and liquid with solid phase of water. Curve OC represents the equilibrium between solid and liquid phase of water. The curve is known as the fusion pressure or melting point curve. Along this curve there are two phases in equilibrium that is ice and water. At atmospheric pressure ice and water can be in equilibrium only at one temperature i.e, the freezing point of the water.
Here, C=1,
P=2
F=C-P+2
=1
Curve OB represent the equilibrium between liquid and vapor. This is called as the vaporization curve. Here also it is necessary to state either temperature or pressure. Eg.: at atmospheric pressure water and vapor can exists in equilibrium only at 1 temperature i.e., the boiling point of the water. Water vapor has also one degree of freedom.
F=C-P+2
=1
Q-2Draw the chart of Binary Eutectic System.
Answer:
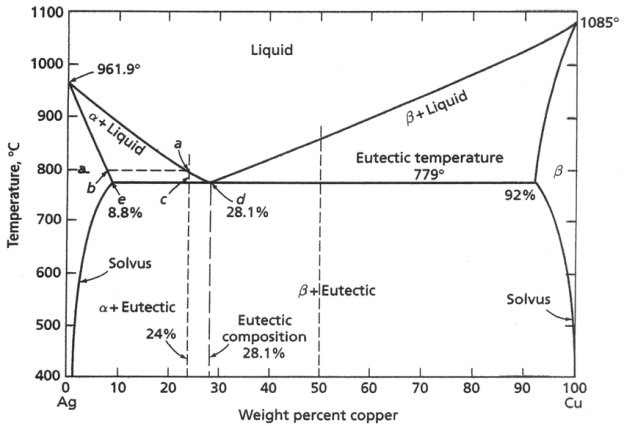
Q-3Explain Corrosion.
Answer: Corrosion is the electrochemical process that occurs in various forms such as chemical forms and atmospheric forms. On the contact of acid sucstance with iron it pretend to form rust. Rust is the result of corroding steel after the iron (Fe) particles have been exposed to oxygen and moisture. When steel is exposed to water, the iron particles are lost to the water’s acidic electrolytes. The iron particles then become oxidized, which results in the formation of Fe⁺⁺. When Fe⁺⁺ is formed, two electrons are released and flow through the steel to another area of the steel known as the cathodic area.
Q-4Explain about the dry and chemical corrosion.
Answer:
(I) Dry or Chemical Corrosion-
The reaction of metal with water vapour or gas at high temperature causes the metal to corrode chemically. This is the redox process in which the electron of the metal are passed directly to the substance in the environment. The metal corrodes generally in the metal which is in higher contact with water.
3Fe + 4H2O Fe3O4 + 4H2
3Fe + 2O2 Fe3O4
i)Due to oxygen
Mechanism of dry corrosion due to O2 gas there are 4 types: -
- Absorption of oxygen molecules on the metal surface
- Dissociation of oxygen atom into metal atom
- Loss of e- by metal atom
- Formation of oxide layer on the metal surface.
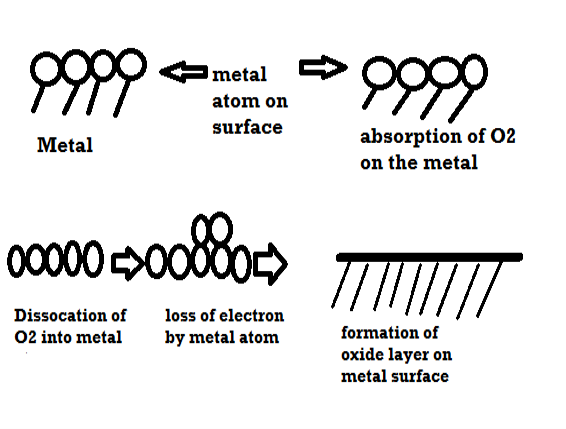
Q-5Explain electrochemical corrosion with its mechanism.
Answer: Corrosion occurs due to the electrochemical process of oxidation and reduction process. In the corroding solution electrons are released by the metal and that is gained by teh elements in the corroding solution. The release of electron from metal is called as the oxidation while vice-versa that is gain of electron by elements is reduction. The regular electron flow in the corrosion reaction can be measured and controlled electronically. This is why controlled electrochemical experimental methods are used to characterize the corrosion properties of metal.
For example,
(i) a thin film of moisture on a metal surface forms the electrolyte for atmospheric corrosion.
(ii) when wet concrete is the electrolyte for reinforcing rod corrosion in bridges. Although most corrosion takes place in water, corrosion in non-aqueous systems is not unknown.
Evolution of hydrogen type: Evolution of Hydrogen Electrochemical corrosion with evolution of H2 occurs in acidic Environment At anode
Fe →Fe2+ + 2e-(oxidation /corrosion)
At cathode
2H+ + + 2e-→H2
Overall reaction Fe +2H+ →Fe
Explanation (1) Iron tank which acts as an anode undergoes corrosion as Fe atoms from the tank pass into the acidic solution as Fe++ ions as shown in reaction above. Since nothing but loss of Fe atom as Fe++ ions i.e. corrosion. (2) Free electrons accumulate at cathode Hydrogen ions present in acidic solution take up these electrons forming H2 gas as shown in the reaction above. H2 gas liberates in the form of bubbles near the cathode. Thus, hydrogen evolution type of corrosion is nothing but displacement of H+ from acidic solution by metal ions. All the metals above H2 in the electro chemical series get dissolved in acidic solution with simultaneous evolution of hydrogen. In hydrogen evolution type of corrosion anode h as a large area (like metallic tank) and cathode has a smaller area.
Absorption of oxygen: Absorption of Oxygen If electrolyte is neutral or alkaline aqueous solution, corrosion takes place by absorption of O2 rusting of iron in water containing dissolved oxygen occurs by oxygen absorption mechanism. At anodic area iron will dissolve by oxidation. The surface of iron is usually coated with the thin film of iron oxide. But if this iron oxide film develops some cracks, anodic areas are created on the surface ; while the metal act as cathodes. Here the anodic areas are small surface while rest of the surface of the metal forms large cathodes.
At anode,
Fe →Fe2+→2e-
The electrons flow to cathodic area through and will be accepted by O2.
At Cathode
Fe2+ +2OH→Fe (OH)2
If enough O2 is present, ferrous hydroxide easily oxidizes to ferric hydroxide 2Fe (OH) 2 + ½ O2 +H2O→2Fe(OH)3
Ferric hydroxide rust This product called yellow rust, which is nothing but Fe2O3.H2O If O2 is limited, the corrosion product will be black unhydrous magnetite, Fe3O4. If environment is aqueous solution of NaCl containing dissolved O2 NaCl →H2O→Na+ + Cl-
At cathode
Na+ + OH→NaOH
At anode
Fe2+ + 2Cl→FeCl2
Ferrous Chloride Both the products NaOH, FeCl2 are soluble in water they react with each other and ferrous hydroxide precipitates which further oxidizes to ferric hydroxide Fe(OH)3. 4 Fe (OH)2 + 2H2O + O2 →4Fe(OH)3 -Fe2O3. H2O yellow rust.
Q-6What is Galvanic Cell Corrosion?
Answer: Galvanic corrosion is the most common corrosion which can be get in notice. This corrosion occurs when two different type of metals are in contact with each other in the presence of electrolyte. In this type of corrosion noble metal are safe while the active metals corrodes.
Q-7 Mention the differential aeration principle.
Answer: The uneven supply of oxygen to the same metal component leads to the formation of oxygen concentration cells that is called as the differential aeration theory of corrosion. It is the type of electrochemical corrosion that affects the metals such as steel and iron. The less oxygenated part behaves anodic while the more oxygenated part cathodic. Since cathodic reactions involve consumption of oxygen, the more oxygenated part behaves cathodic and less oxygenated pan behaves anodic. The reaction occurs because oppositely charged electrons flow between the smaller anode and larger cathode. Positively charged cations meeting negatively charged anions forming corrosion product and a resulting pit in the metal, otherwise known as pitting corrosion. In a gutter, pipe, tank or similar the anode is just below the waterline. This is where the oxidation occurs, corrosion product forms and a pit develops weakening the metal.
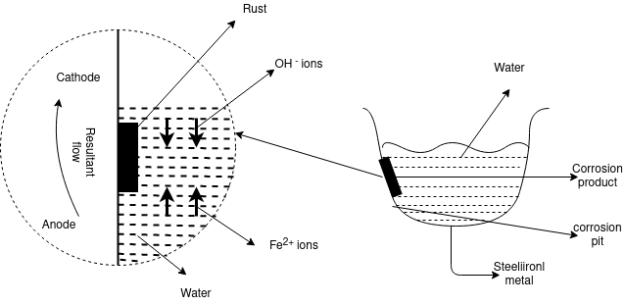
Q-8What is Pitting Corrosion?
Answer: This type of corrosion occurs at certain conditions, there is a accelerated corrosion in some areas rather than the uniform corrosion over the substance. This condition includes low level of concentration of oxygen or high concentration of chlorides.
Q-9What is stress corrosion?
Answer: Stress corrosion cracking (SCC) is the growth of crack formation in a corrosive environment. It can lead to unexpected and sudden failure of normally ductile metal alloys subjected to a tensile stress, especially at elevated temperature. SCC is highly chemically specific in that certain alloys are likely to undergo SCC only when exposed to a small number of chemical environments. The chemical environment that causes SCC for a given alloy is often one which is only mildly corrosive to the metal. Hence, metal parts with severe SCC can appear bright and shiny, while being filled with microscopic cracks. This factor makes it common for SCC to go undetected prior to failure. SCC often progresses rapidly, and is more common among alloys than pure metals. The specific environment is of crucial importance, and only very small concentrations of certain highly active chemicals are needed to produce catastrophic cracking, often leading to devastating and unexpected failure.
Q-10What are the factors that effects the rate of corrosion?
Answer: Factors affecting the rate of corrosion-
(i)Nature of metal:
Position of metal in galvanic series.
If position is higher in galvanic series then it carrode faster
While for 2 metal the difference between them shows the corrosion ratio.
(ii)Nature of corroding environment: Iron and steels are the most versatile, least expensive and most widely used materials for the construction of many engineering systems. They are unequaled in their range of mechanical and physical properties with which they can be endowed by alloying and heat treatment. Their main disadvantage is that they have poor corrosion resistance in even relatively mild environments unlike stainless steels. Corrosion can reduce the load-carrying capacity of a component either by reducing its size or by pitting. Pitting not only reduces the effective cross section in the pitted region but also introduce stress raisers, which initiate cracks. Any technique that reduces or eliminates corrosion will extend the life of a component and increase its reliability. In addition to corrosion prevention methods, it is important to design and select materials for improving the overall corrosion performance of components. The three interrelated factors that drive the selection of materials for corrosion control are the corrosivity of the environment, the corrosion resistance of the material and the acceptable rate of attack.
Corrosion failures during service are likely if suitable materials with appropriate coatings are not selected for the fabrication of components of critical systems. Corrosion significantly affects the efficiency of systems. Failures can be minimized or reduced significantly by controlling corrosion. The possible methods of controlling corrosion are the application of coatings, linings, metal cladding and corrosion inhibitors, and alloying. Among these, the application of suitable coatings appears to be a promising method of corrosion control in terms of cost effectiveness and service life. DMR-1700 is a recently developed ultrahigh-strength low-alloy steel with improved mechanical properties compared with other aerospace-grade low-alloy steels. However, its corrosion characteristics have not been investigated in detail, although some corrosion studies have been carried out.
In the present investigation, the effect of the environment on the corrosion characteristics of DMR-1700 steel is studied in detail, the properties of the steel under various environmental conditions are compared and the degradation mechanisms involved are considered. On the basis of the results of the investigation, we recommend the use of the material with a suitable protective coating for the fabrication of components for various applications. In the study, the surface morphologies of the corroded steels in different environments were observed using a scanning electron microscope (SEM) to determine the nature of corrosion. We also successfully developed a high-performance coating for DMR-1700 steel to enhance its resistance against corrosion. The developed coating is discussed, and its application is recommended for effective protection against corrosion. The use of such an advanced material with a high-performance coating will help enhance the efficiency of systems by reducing failures during service.