Unit – 1
Inventory Management
Q1) Explain inventory?
A1) Inventory is the life blood of the industries. But an excess or shortage of inventory is harmful. It is the most important component of working capital.
The term inventory is used to denote the stock on hand at a particular time comprising raw materials, goods in the process of manufacture and finished goods. An inventory has a primary significance for accounting purposes to ascertain the correct income for a particular period. Inventory plays a very important part in the determination of profit of a business.
In the financial sector, inventory is defined as “the sum of the value of raw materials, fuels and lubricants, spare parts, maintenance consumables, semi-processed materials and finished goods stock at any given point of time”.
S.E. Walters states, “The term inventory refers to the stockpiles of the product a firm is offering for sales and the components that make up the product”.
James H. Green observed, “An inventory refers to the movable articles of the business which are eventually expected to go into the flow of trade.”
Inventory Examples
Real-world examples can make inventory models easier to understand. The following examples demonstrate how the different types of inventory work in retail and manufacturing businesses.
Raw Materials/Components:
A company that makes T-shirts has components that include fabric, thread, dyes and print designs.
Finished Goods:
A jewelry manufacturer makes charm necklaces. Staff attaches a necklace to a preprinted card and slips it into cellophane envelopes to create a finished good ready for sale. The cost of goods (COGS) of the finished good includes the packaging it comes in as well as the labor to make the item.
Work In Progress:
A cell phone consists of a case, a printed circuit board, and components. The process of assembling the pieces at a dedicated workstation is WIP.
Q2) Explain types of inventory
A2)
Raw Materials
These are the materials or goods purchased by the manufacturer. The manufacturing process is applied to the raw material to produce desired finished goods. For example, aluminum scrap is used to produce aluminum ingots. Flour is used to produce bread. Finished goods for someone can be raw material for someone. For example, the aluminum ingot can be used as raw material by utensils manufacturer.
The business importance of raw material as an inventory is mainly to protect any interruption in production planning. Other reasons can be availing price discount on bulk purchases, guard against market shortage situation, etc.
Work-In-Progress (WIP)
These are the partly processed raw materials lying on the production floor. They may or may not be saleable. These are also called semi-finished goods. It is unavoidable inventory which will be created in almost any manufacturing business.
This level of this inventory should be kept as low as possible. Since a lot of money is blocked over here which otherwise can be used to achieve better returns. Speeding up the manufacturing process, proper production planning, customer and supplier system integration etc. can diminish the levels of work in progress. Lean management considers it as waste.
Finished Goods
These are the final products after manufacturing process on raw materials. They are sold in the market.
There are two kinds of manufacturing industries. One, where the product is first manufactured and then sold. Second, where the order is received first and then it is manufactured as per specifications. In the first one, it is inevitable to keep finished goods inventory whereas it can be avoided in the second one.
Packing Material
Packing material is the inventory used for packing of goods. It can be primary packing and secondary packing. Primary packing is the packing without which the goods are not usable. Secondary packing is the packing done for convenient transportation of goods.
MRO Goods
MRO stands for maintenance, repair, and operating supplies. They are also called as consumables in various parts of the world. They are like a support function. Maintenance and repairs goods like bearings, lubricating oil, bolt, nuts etc are used in the machinery used for production. Operating supplies mean the stationery etc used for operating the business. Here is our detailed post on MRO Inventory.
Other Types of Inventories are classified on various basis are as follows:
Materially, there are 4 types of inventories only as explained above. Following types of inventories are either the reasons to hold those 4 basic inventory or business requirement for the same. Some of them are suitable strategies for certain businesses.
Goods in Transit
Under normal conditions, a business transports raw materials, WIP, finished goods etc. from one site to other for various purpose like sales, purchase, further processing etc. Due to long distances, the inventory stays on the way for days, weeks and even months depending on distances. These are called Inventory / Goods in Transit. Goods in transit may consist of any type of basic inventories.
Buffer Inventory
Buffer inventory is the inventory kept or purchased for the purpose of meeting future uncertainties. Also known as safety stock, it is the amount of inventory besides the current inventory requirement. The benefit is smooth business flow and customer satisfaction and disadvantage is the carrying cost of inventory. Raw material as buffer stock is kept for achieving nonstop production and finished goods for delivering any size, any type of order by the customer.
Anticipatory Stock
Based on the past experiences, a businessman is able to foresee the future trends of the market and takes certain decisions based on that. Expecting a price rise, a spurt in demand etc. some businessman invests money in stocking those goods. Such kind of inventory is known as anticipatory stock. It is normally the raw materials or finished goods and this strategy is executed by traders.
Decoupling Inventory
In manufacturing concern, plant and machinery should always keep running. The act of stopping machinery, costs to the entrepreneur in terms of additional set up costs, repairs, idle time depreciation, damages, trial runs etc. The reason for halt is not always the demand of the product. It may be because of the availability of input. In a production line, one machine/process uses the output of other machines/process. The speed of different machines may not always integrate with each other. For that reason, the stock of input for all the machines should be sufficient to keep the factory running. Such WIP inventory is called decoupling inventory.
Cycle Inventory
It is a type of inventory accumulated due to ordering in lots/sizes to avoid carrying the cost of inventory. In other words, it is the inventory to balance the carrying cost and holding cost for optimizing the inventory ordering cost as suggested by Economic Order Quantity (EOQ).
Q3) Explain need for holding inventory
A3) Holding of inventories involves tying up funds of the company and storage and handling costs. There are three general motives for holding inventories:
(i) The Transactions motive:
It expresses the need to maintain inventories to facilitate production and sales operation smoothly.
(ii) The Precautionary motive:
It necessitates holding of inventories to guard against the risk of unpredictable change in demand and supply forces.
(iii) The Speculative motive:
It influences the decision to increase or reduce inventory levels to take advantages of price fluctuation.
In order to maintain an uninterrupted flow of production it becomes necessary to hold adequate stock of materials since there is a time lag between the demand for materials and its supply due to some unavoidable circumstances. Besides, there are two other motives for holding of inventories—viz., to receive the benefit of quantity discount on account of bulk purchase and to avoid the anticipated rise in price of raw material.
The work-in-progress builds up since there is production cycle. Actually, the stock of work- in-progress is to be maintained till the production cycle is complete. Similarly, stock of finished goods has also to be held since there is a time lag between the production and sales. When goods are demanded by the customers, it cannot immediately be produced and, as such, for a continuous and regular supply of goods, minimum stock of finished goods is to be maintained. Stock of finished goods should also be maintained for sudden demands from customers and for seasonal sales.
Therefore, the primary objective of holding raw materials is:
(i) To separate purchase and production activities, and, for holding finished goods there should be separate production and sales activities;
(ii) To obtain quantity discount against bulk purchase, and
(iii) To avoid interruption in production.
At the same time, work-in-progress inventory is necessary since production is not instantaneous and finished goods should also be maintained for:
(i) Serving customer on a continuous basis;
(ii) Meeting the fluctuating demands.
Cost of Holding Inventory:
It has been highlighted above that the object of inventory management is to maintain the optimum level of inventory.
This optimum level depends on the following costs:
(i) Ordering/Acquisition/Set-up Costs, and
(ii) Carrying Costs.
(i) Ordering/Acquisition/Set-up Costs:
These are the variable costs of placing an order for the goods. Orders are placed by the firm with suppliers to replenish inventory of raw materials. Ordering costs include the cost of: requesting, purchasing, ordering, transporting, receiving, inspecting and storing. The ordering costs vary in proportion to the number of orders placed. They also include clerical costs and stationery costs (That is why it is called a set-up cost.).
Although these costs are almost fixed in nature, the larger the order placed, or the more frequent the acquisition of inventory made, the higher are such costs. Similarly, the fewer the orders, the lower the order cost will be for the firm. Thus, the ordering/acquisition costs are inversely related to the level of inventory.
(ii) Carrying Cost:
These are the expenses of storing goods, i.e., they are involved in carrying inventory.
The cost of holding inventory may be divided into:
(i) Cost of Storing the Inventory, and
(ii) Opportunity Cost of Funds.
(i) Cost of Storing the Inventory:
This include—
(a) Storage Cost (i.e., tax, depreciation, insurance, maintenance of building, etc.,)
(b) Insurance (for fire and theft);
(c) Obsolescence and Spoilage;
(d) Damage or Theft;
(e) Servicing Costs (i.e., clerical, accounting costs etc.)
(f) Cost of running out of goods.
(ii) Opportunity Cost of Funds:
This includes the expenses in raising funds (i.e., Interest on Capital) which are used for financing the acquisition of inventory.
The level of inventory and the carrying costs are positively related and move in the same direction, i.e., if inventory level decreases, the carrying costs also decrease, and vice versa.
Q4) Explain risk and cost associated with excessive inventory
A4) Holding of inventory exposes the manufacturing and merchandising firms to a number of risks and costs. The various risks and costs of maintaining higher levels of inventory have been highlighted as follows:
1. Risk of price decline
Holding Inventory may increase the risk of decline in price. This may be due to increase in the supply of products in market by competitors, introduction of a new competitive product, competitive pricing policy of competitors etc.
2. Risk of obsolescence
The is a risk of inventory becoming obsolescence. The inventory may become obsolete/outdated due to improved technology, improvements in product design, changes in customers’ taste etc.
3. Purchase cost
A firm has to pay high price for managing inventory. Inventory management has to take into account of the price paid to the suppliers and the expense of transport for bringing the material to stores, insurance and transportation cost.
4. Ordering cost
Cost of ordering is one another factor that a firm has to consider in Inventory management. Ordering costs includes cost of requisitioning, preparation of purchase order, transportation of inventory, receiving the supplies at the warehouse etc.
5. Carrying cost
Carrying cost includes the cost of storing the inventory in warehouse, handling expenses, insurance and rent paid for managing the inventory, opportunity cost locked up in stocks etc. Opportunity cost here refers to the alternative use of funds that the firm would have used to invest in stocks.
6. Stock out (shortage) cost
Stocks results in higher costs when they fall short of demand. Shortage of stocks also results in higher cost, dissatisfaction among customers, decrease in sales and increase of loss to firm.
Measurement of shortage cost is relatively difficult because of its intangible nature. In practice, the lost contribution resulting from failure to meet demand provides a reasonable approximation. In cases where stock out does not result in loss in business, additional cost for crash procurement etc. may be considered as shortage cost.
Q5) Explain meaning and types of inventory
A5) Inventory is the life blood of the industries. But an excess or shortage of inventory is harmful. It is the most important component of working capital.
The term inventory is used to denote the stock on hand at a particular time comprising raw materials, goods in the process of manufacture and finished goods. An inventory has a primary significance for accounting purposes to ascertain the correct income for a particular period. Inventory plays a very important part in the determination of profit of a business.
In the financial sector, inventory is defined as “the sum of the value of raw materials, fuels and lubricants, spare parts, maintenance consumables, semi-processed materials and finished goods stock at any given point of time”.
S.E. Walters states, “The term inventory refers to the stockpiles of the product a firm is offering for sales and the components that make up the product”.
James H. Green observed, “An inventory refers to the movable articles of the business which are eventually expected to go into the flow of trade.”
Inventory Examples
Real-world examples can make inventory models easier to understand. The following examples demonstrate how the different types of inventory work in retail and manufacturing businesses.
Raw Materials/Components:
A company that makes T-shirts has components that include fabric, thread, dyes and print designs.
Finished Goods:
A jewelry manufacturer makes charm necklaces. Staff attaches a necklace to a preprinted card and slips it into cellophane envelopes to create a finished good ready for sale. The cost of goods (COGS) of the finished good includes the packaging it comes in as well as the labor to make the item.
Work In Progress:
A cell phone consists of a case, a printed circuit board, and components. The process of assembling the pieces at a dedicated workstation is WIP.
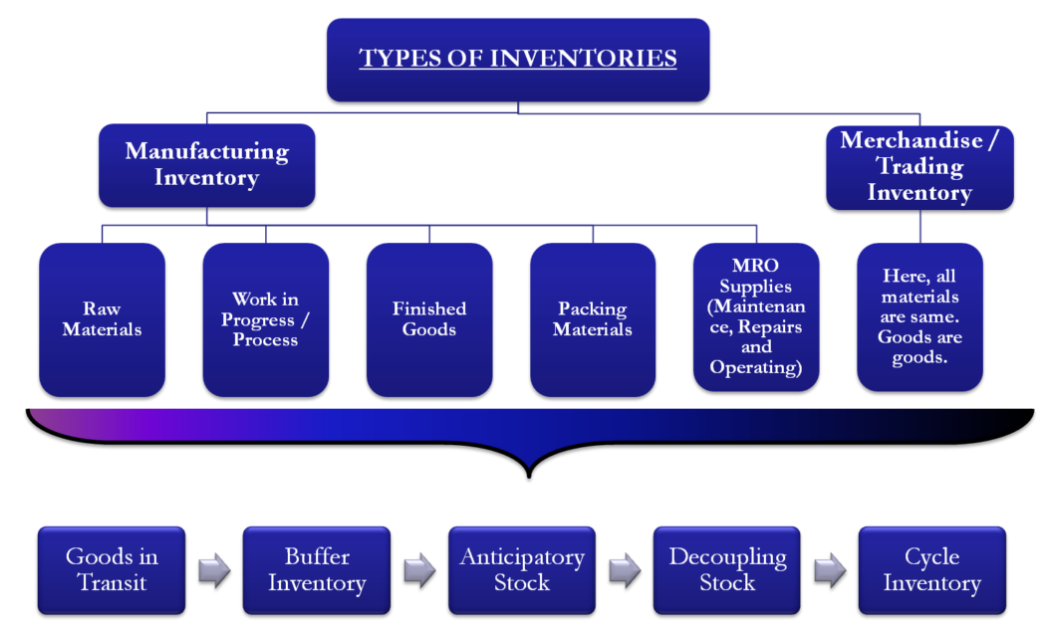
Raw Materials
These are the materials or goods purchased by the manufacturer. The manufacturing process is applied to the raw material to produce desired finished goods. For example, aluminum scrap is used to produce aluminum ingots. Flour is used to produce bread. Finished goods for someone can be raw material for someone. For example, the aluminum ingot can be used as raw material by utensils manufacturer.
The business importance of raw material as an inventory is mainly to protect any interruption in production planning. Other reasons can be availing price discount on bulk purchases, guard against market shortage situation, etc.
Work-In-Progress (WIP)
These are the partly processed raw materials lying on the production floor. They may or may not be saleable. These are also called semi-finished goods. It is unavoidable inventory which will be created in almost any manufacturing business.
This level of this inventory should be kept as low as possible. Since a lot of money is blocked over here which otherwise can be used to achieve better returns. Speeding up the manufacturing process, proper production planning, customer and supplier system integration etc. can diminish the levels of work in progress. Lean management considers it as waste.
Finished Goods
These are the final products after manufacturing process on raw materials. They are sold in the market.
There are two kinds of manufacturing industries. One, where the product is first manufactured and then sold. Second, where the order is received first and then it is manufactured as per specifications. In the first one, it is inevitable to keep finished goods inventory whereas it can be avoided in the second one.
Packing Material
Packing material is the inventory used for packing of goods. It can be primary packing and secondary packing. Primary packing is the packing without which the goods are not usable. Secondary packing is the packing done for convenient transportation of goods.
MRO Goods
MRO stands for maintenance, repair, and operating supplies. They are also called as consumables in various parts of the world. They are like a support function. Maintenance and repairs goods like bearings, lubricating oil, bolt, nuts etc are used in the machinery used for production. Operating supplies mean the stationery etc used for operating the business. Here is our detailed post on MRO Inventory.
Other Types of Inventories are classified on various basis are as follows:
Materially, there are 4 types of inventories only as explained above. Following types of inventories are either the reasons to hold those 4 basic inventory or business requirement for the same. Some of them are suitable strategies for certain businesses.
Goods in Transit
Under normal conditions, a business transports raw materials, WIP, finished goods etc. from one site to other for various purpose like sales, purchase, further processing etc. Due to long distances, the inventory stays on the way for days, weeks and even months depending on distances. These are called Inventory / Goods in Transit. Goods in transit may consist of any type of basic inventories.
Buffer Inventory
Buffer inventory is the inventory kept or purchased for the purpose of meeting future uncertainties. Also known as safety stock, it is the amount of inventory besides the current inventory requirement. The benefit is smooth business flow and customer satisfaction and disadvantage is the carrying cost of inventory. Raw material as buffer stock is kept for achieving nonstop production and finished goods for delivering any size, any type of order by the customer.
Anticipatory Stock
Based on the past experiences, a businessman is able to foresee the future trends of the market and takes certain decisions based on that. Expecting a price rise, a spurt in demand etc. some businessman invests money in stocking those goods. Such kind of inventory is known as anticipatory stock. It is normally the raw materials or finished goods and this strategy is executed by traders.
Decoupling Inventory
In manufacturing concern, plant and machinery should always keep running. The act of stopping machinery, costs to the entrepreneur in terms of additional set up costs, repairs, idle time depreciation, damages, trial runs etc. The reason for halt is not always the demand of the product. It may be because of the availability of input. In a production line, one machine/process uses the output of other machines/process. The speed of different machines may not always integrate with each other. For that reason, the stock of input for all the machines should be sufficient to keep the factory running. Such WIP inventory is called decoupling inventory.
Cycle Inventory
It is a type of inventory accumulated due to ordering in lots/sizes to avoid carrying the cost of inventory. In other words, it is the inventory to balance the carrying cost and holding cost for optimizing the inventory ordering cost as suggested by Economic Order Quantity (EOQ).
Q6) Explain types and need for holding inventory
A6)
Raw Materials
These are the materials or goods purchased by the manufacturer. The manufacturing process is applied to the raw material to produce desired finished goods. For example, aluminum scrap is used to produce aluminum ingots. Flour is used to produce bread. Finished goods for someone can be raw material for someone. For example, the aluminum ingot can be used as raw material by utensils manufacturer.
The business importance of raw material as an inventory is mainly to protect any interruption in production planning. Other reasons can be availing price discount on bulk purchases, guard against market shortage situation, etc.
Work-In-Progress (WIP)
These are the partly processed raw materials lying on the production floor. They may or may not be saleable. These are also called semi-finished goods. It is unavoidable inventory which will be created in almost any manufacturing business.
This level of this inventory should be kept as low as possible. Since a lot of money is blocked over here which otherwise can be used to achieve better returns. Speeding up the manufacturing process, proper production planning, customer and supplier system integration etc. can diminish the levels of work in progress. Lean management considers it as waste.
Finished Goods
These are the final products after manufacturing process on raw materials. They are sold in the market.
There are two kinds of manufacturing industries. One, where the product is first manufactured and then sold. Second, where the order is received first and then it is manufactured as per specifications. In the first one, it is inevitable to keep finished goods inventory whereas it can be avoided in the second one.
Packing Material
Packing material is the inventory used for packing of goods. It can be primary packing and secondary packing. Primary packing is the packing without which the goods are not usable. Secondary packing is the packing done for convenient transportation of goods.
MRO Goods
MRO stands for maintenance, repair, and operating supplies. They are also called as consumables in various parts of the world. They are like a support function. Maintenance and repairs goods like bearings, lubricating oil, bolt, nuts etc are used in the machinery used for production. Operating supplies mean the stationery etc used for operating the business. Here is our detailed post on MRO Inventory.
Other Types of Inventories are classified on various basis are as follows:
Materially, there are 4 types of inventories only as explained above. Following types of inventories are either the reasons to hold those 4 basic inventory or business requirement for the same. Some of them are suitable strategies for certain businesses.
Goods in Transit
Under normal conditions, a business transports raw materials, WIP, finished goods etc from one site to other for various purpose like sales, purchase, further processing etc. Due to long distances, the inventory stays on the way for days, weeks and even months depending on distances. These are called Inventory / Goods in Transit. Goods in transit may consist of any type of basic inventories.
Buffer Inventory
Buffer inventory is the inventory kept or purchased for the purpose of meeting future uncertainties. Also known as safety stock, it is the amount of inventory besides the current inventory requirement. The benefit is smooth business flow and customer satisfaction and disadvantage is the carrying cost of inventory. Raw material as buffer stock is kept for achieving nonstop production and finished goods for delivering any size, any type of order by the customer.
Anticipatory Stock
Based on the past experiences, a businessman is able to foresee the future trends of the market and takes certain decisions based on that. Expecting a price rise, a spurt in demand etc. some businessman invests money in stocking those goods. Such kind of inventory is known as anticipatory stock. It is normally the raw materials or finished goods and this strategy is executed by traders.
Decoupling Inventory
In manufacturing concern, plant and machinery should always keep running. The act of stopping machinery, costs to the entrepreneur in terms of additional set up costs, repairs, idle time depreciation, damages, trial runs etc. The reason for halt is not always the demand of the product. It may be because of the availability of input. In a production line, one machine/process uses the output of other machines/process. The speed of different machines may not always integrate with each other. For that reason, the stock of input for all the machines should be sufficient to keep the factory running. Such WIP inventory is called decoupling inventory.
Cycle Inventory
It is a type of inventory accumulated due to ordering in lots/sizes to avoid carrying the cost of inventory. In other words, it is the inventory to balance the carrying cost and holding cost for optimizing the inventory ordering cost as suggested by Economic Order Quantity (EOQ).
Need for holding inventory
Holding of inventories involves tying up funds of the company and storage and handling costs. There are three general motives for holding inventories:
(i) The Transactions motive:
It expresses the need to maintain inventories to facilitate production and sales operation smoothly.
(ii) The Precautionary motive:
It necessitates holding of inventories to guard against the risk of unpredictable change in demand and supply forces.
(iii) The Speculative motive:
It influences the decision to increase or reduce inventory levels to take advantages of price fluctuation.
In order to maintain an uninterrupted flow of production it becomes necessary to hold adequate stock of materials since there is a time lag between the demand for materials and its supply due to some unavoidable circumstances. Besides, there are two other motives for holding of inventories—viz., to receive the benefit of quantity discount on account of bulk purchase and to avoid the anticipated rise in price of raw material.
The work-in-progress builds up since there is production cycle. Actually, the stock of work- in-progress is to be maintained till the production cycle is complete. Similarly, stock of finished goods has also to be held since there is a time lag between the production and sales. When goods are demanded by the customers, it cannot immediately be produced and, as such, for a continuous and regular supply of goods, minimum stock of finished goods is to be maintained. Stock of finished goods should also be maintained for sudden demands from customers and for seasonal sales.
Therefore, the primary objective of holding raw materials is:
(i) To separate purchase and production activities, and, for holding finished goods there should be separate production and sales activities;
(ii) To obtain quantity discount against bulk purchase, and
(iii) To avoid interruption in production.
At the same time, work-in-progress inventory is necessary since production is not instantaneous and finished goods should also be maintained for:
(i) Serving customer on a continuous basis;
(ii) Meeting the fluctuating demands.
Cost of Holding Inventory:
It has been highlighted above that the object of inventory management is to maintain the optimum level of inventory.
This optimum level depends on the following costs:
(i) Ordering/Acquisition/Set-up Costs, and
(ii) Carrying Costs.
(i) Ordering/Acquisition/Set-up Costs:
These are the variable costs of placing an order for the goods. Orders are placed by the firm with suppliers to replenish inventory of raw materials. Ordering costs include the cost of: requesting, purchasing, ordering, transporting, receiving, inspecting and storing. The ordering costs vary in proportion to the number of orders placed. They also include clerical costs and stationery costs (That is why it is called a set-up cost.).
Although these costs are almost fixed in nature, the larger the order placed, or the more frequent the acquisition of inventory made, the higher are such costs. Similarly, the fewer the orders, the lower the order cost will be for the firm. Thus, the ordering/acquisition costs are inversely related to the level of inventory.
(ii) Carrying Cost:
These are the expenses of storing goods, i.e., they are involved in carrying inventory.
The cost of holding inventory may be divided into:
(i) Cost of Storing the Inventory, and
(ii) Opportunity Cost of Funds.
(i) Cost of Storing the Inventory:
This includes—
(a) Storage Cost (i.e., tax, depreciation, insurance, maintenance of building, etc.,)
(b) Insurance (for fire and theft);
(c) Obsolescence and Spoilage;
(d) Damage or Theft;
(e) Servicing Costs (i.e., clerical, accounting costs etc.)
(f) Cost of running out of goods.
(ii) Opportunity Cost of Funds:
This includes the expenses in raising funds (i.e., Interest on Capital) which are used for financing the acquisition of inventory.
The level of inventory and the carrying costs are positively related and move in the same direction, i.e., if inventory level decreases, the carrying costs also decrease, and vice versa.
Q7) Explain the need for holding inventory and risk and cost associated with excessive inventory?
A7) Need for holding inventory
Holding of inventories involves tying up funds of the company and storage and handling costs. There are three general motives for holding inventories:
(i) The Transactions motive:
It expresses the need to maintain inventories to facilitate production and sales operation smoothly.
(ii) The Precautionary motive:
It necessitates holding of inventories to guard against the risk of unpredictable change in demand and supply forces.
(iii) The Speculative motive:
It influences the decision to increase or reduce inventory levels to take advantages of price fluctuation.
In order to maintain an uninterrupted flow of production it becomes necessary to hold adequate stock of materials since there is a time lag between the demand for materials and its supply due to some unavoidable circumstances. Besides, there are two other motives for holding of inventories—viz., to receive the benefit of quantity discount on account of bulk purchase and to avoid the anticipated rise in price of raw material.
The work-in-progress builds up since there is production cycle. Actually, the stock of work- in-progress is to be maintained till the production cycle is complete. Similarly, stock of finished goods has also to be held since there is a time lag between the production and sales. When goods are demanded by the customers, it cannot immediately be produced and, as such, for a continuous and regular supply of goods, minimum stock of finished goods is to be maintained. Stock of finished goods should also be maintained for sudden demands from customers and for seasonal sales.
Therefore, the primary objective of holding raw materials is:
(i) To separate purchase and production activities, and, for holding finished goods there should be separate production and sales activities;
(ii) To obtain quantity discount against bulk purchase, and
(iii) To avoid interruption in production.
At the same time, work-in-progress inventory is necessary since production is not instantaneous and finished goods should also be maintained for:
(i) Serving customer on a continuous basis;
(ii) Meeting the fluctuating demands.
Cost of Holding Inventory:
It has been highlighted above that the object of inventory management is to maintain the optimum level of inventory.
This optimum level depends on the following costs:
(i) Ordering/Acquisition/Set-up Costs, and
(ii) Carrying Costs.
(i) Ordering/Acquisition/Set-up Costs:
These are the variable costs of placing an order for the goods. Orders are placed by the firm with suppliers to replenish inventory of raw materials. Ordering costs include the cost of: requesting, purchasing, ordering, transporting, receiving, inspecting and storing. The ordering costs vary in proportion to the number of orders placed. They also include clerical costs and stationery costs (That is why it is called a set-up cost.).
Although these costs are almost fixed in nature, the larger the order placed, or the more frequent the acquisition of inventory made, the higher are such costs. Similarly, the fewer the orders, the lower the order cost will be for the firm. Thus, the ordering/acquisition costs are inversely related to the level of inventory.
(ii) Carrying Cost:
These are the expenses of storing goods, i.e., they are involved in carrying inventory.
The cost of holding inventory may be divided into:
(i) Cost of Storing the Inventory, and
(ii) Opportunity Cost of Funds.
(i) Cost of Storing the Inventory:
This include—
(a) Storage Cost (i.e., tax, depreciation, insurance, maintenance of building, etc.,)
(b) Insurance (for fire and theft);
(c) Obsolescence and Spoilage;
(d) Damage or Theft;
(e) Servicing Costs (i.e., clerical, accounting costs etc.)
(f) Cost of running out of goods.
(ii) Opportunity Cost of Funds:
This includes the expenses in raising funds (i.e., Interest on Capital) which are used for financing the acquisition of inventory.
The level of inventory and the carrying costs are positively related and move in the same direction, i.e., if inventory level decreases, the carrying costs also decrease, and vice versa.
Risk associated with excessive inventory
Holding of inventory exposes the manufacturing and merchandising firms to a number of risks and costs. The various risks and costs of maintaining higher levels of inventory have been highlighted as follows:
1. Risk of price decline
Holding Inventory may increase the risk of decline in price. This may be due to increase in the supply of products in market by competitors, introduction of a new competitive product, competitive pricing policy of competitors etc.
2. Risk of obsolescence
The is a risk of inventory becoming obsolescence. The inventory may become obsolete/outdated due to improved technology, improvements in product design, changes in customers’ taste etc.
3. Purchase cost
A firm has to pay high price for managing inventory. Inventory management has to take into account of the price paid to the suppliers and the expense of transport for bringing the material to stores, insurance and transportation cost.
4. Ordering cost
Cost of ordering is one another factor that a firm has to consider in Inventory management. Ordering costs includes cost of requisitioning, preparation of purchase order, transportation of inventory, receiving the supplies at the warehouse etc.
5. Carrying cost
Carrying cost includes the cost of storing the inventory in warehouse, handling expenses, insurance and rent paid for managing the inventory, opportunity cost locked up in stocks etc. Opportunity cost here refers to the alternative use of funds that the firm would have used to invest in stocks.
6. Stock out (shortage) cost
Stocks results in higher costs when they fall short of demand. Shortage of stocks also results in higher cost, dissatisfaction among customers, decrease in sales and increase of loss to firm.
Measurement of shortage cost is relatively difficult because of its intangible nature. In practice, the lost contribution resulting from failure to meet demand provides a reasonable approximation. In cases where stock out does not result in loss in business, additional cost for crash procurement etc. may be considered as shortage cost.
Q8) Write a short note on meaning and definition of inventory
A8) Inventory is the life blood of the industries. But an excess or shortage of inventory is harmful. It is the most important component of working capital.
The term inventory is used to denote the stock on hand at a particular time comprising raw materials, goods in the process of manufacture and finished goods. An inventory has a primary significance for accounting purposes to ascertain the correct income for a particular period. Inventory plays a very important part in the determination of profit of a business.
In the financial sector, inventory is defined as “the sum of the value of raw materials, fuels and lubricants, spare parts, maintenance consumables, semi-processed materials and finished goods stock at any given point of time”.
S.E. Walters states, “The term inventory refers to the stockpiles of the product a firm is offering for sales and the components that make up the product”.
James H. Green observed, “An inventory refers to the movable articles of the business which are eventually expected to go into the flow of trade.”
Inventory Examples
Real-world examples can make inventory models easier to understand. The following examples demonstrate how the different types of inventory work in retail and manufacturing businesses.
Raw Materials/Components:
A company that makes T-shirts has components that include fabric, thread, dyes and print designs.
Finished Goods:
A jewelry manufacturer makes charm necklaces. Staff attaches a necklace to a preprinted card and slips it into cellophane envelopes to create a finished good ready for sale. The cost of goods (COGS) of the finished good includes the packaging it comes in as well as the labor to make the item.
Work In Progress:
A cell phone consists of a case, a printed circuit board, and components. The process of assembling the pieces at a dedicated workstation is WIP.