Unit - 2
Energy-II
Q1) Compute the proximate analysis results 1.9 gms of a coal sample loses 0.285gm weight at 110°c.
- 1.5 gm of the same coal sample loses 0.36gm weight at 925°c.
- 2.15 gms of the coal sample leaves 0.26 gm ash.
A1)
Given data:
M=1.9 gm
( m – m1 )= 0.285 gm ( moisture loss )
Loss in weight due to moisture and VM = 0.36gm
Weight of coal = 2.15 gm
Weight of ash = 0.26gm
- Moisture % =
*100
= = 15 %
2. V.M %:
v.m = *10
= *100-15 = 24 – 15
= 9 %
3. Ash %:
Therefore,
Ash =
=
= 12 %
Q2) Calculate C, N, H, S from the following observation for a sample of coal.
- 2.05 gms of the coal is burnt in combustion tube. The increase in weight of any hydrous Cacl2 is 0.55 gm and increase in weight of KoH tube is 5.75gm.
- 0.75 of the coal is kjaldahl experiment released NH3 which is passed in 50ml 0.12 N NaoH to neutralize in back titration.
- Washings of the bomb pot when 1.8 gm.
A2)
Given data:
Increase in weight of any hydrous calcl2 = 0.55
Mass of coal = 0.75gms
Volume of 0.12 NHCL consumed by NH3 = 50 – 41
= 9 ml
Mass of coal = 1.8gms
Weight of Baso4 = 0.31 gm
- Weight of CO2 formed = increase in wt. Of KOH
Therefore,
C % = *
*100 = 76.5 %.
Increase in weight of any hydrous CaCl2
= weight of H2O formed
Mass of coal = 2.05gm
H % = *
*100
= 2.98 %
2. N % =
=
= 2.02 %
3. S % = *100
=
= 2.36 %
Q3) Explain different types of cracking?
A3) The different types of cracking are thermal cracking and catalytic cracking. Here is a brief elaboration on the two –
1. Thermal Cracking
The thermal method of cracking uses pressure and heat to break down large hydrocarbon molecules into lighter molecules. This process can be further categorised into –
a. Steam Cracking
This is an older process which uses the heat energy generated from steam. It is also referred to as Pyrolysis. Due to the presence of greater latent heat of energy in the steam, it is considered to be a useful technique for the production of alkenes.
The raw materials used in the process include propane-butane mixture, naptha (obtained from directly distilling crude, and gas oil (in rare instances).
b. Modern Thermal Cracking
Both high pressure and high temperature are used for this method. Homolytic fission takes place among carbon bonds of hydrocarbon compounds. This reaction gains industrial importance with the production of burner fuels.
By lowering the temperature, the delayed coking process takes place. It leads to the production of needle coke which is used for carbon electrodes.
2. Catalytic Cracking
As understood from the term, a catalytic cracking process is undertaken in presence of a catalyst. The large molecules are broken in such a manner that it leads to the maximisation of gasoline yield.
There are three sub-processes involved in this method –
- Reaction
- Regeneration
- Fractionation
Catalytic cracking can be further categorised into –
a. Hydrocracking
It involves a two-stage process that includes a combination of hydrogenation and catalytic cracking. In the presence of hydrogen, heavier feedstocks are being cracked to arrive at the desirable products.
This process needs high temperature, high pressure, hydrogen, and a catalyst. The process is also largely dependent on relative rates of the two reactions and the nature of the feedstock.
b. Fluid Catalytic Cracking
This process is a little distinct. The feedstock is subjected to moderate pressure and high temperature. It is subsequently brought into contact with powdered and hot catalysts. The long-chain molecules are broken down by such a catalyst into considerably shorter molecules.
Q4) Draw and explain Fisher- Tropsch process.
A4) Liquid transportation hydrocarbon fuels and various other chemical products can be produced from syngas via the well-known and established catalytic chemical process called Fischer-Tropsch (FT) synthesis.
Figure 1 shows a simplified block flow diagram of a process incorporating FT synthesis. The gasification island consists of all the supporting process technologies of coal handling & feed preparation, heat recovery, syngas cleanup and conditioning, water-gas-shift, sulphur recovery, etc. The clean syngas leaving the gasification island is sent onto the FT synthesis island, where the clean shifted syngas is converted into primary products of wax, hydrocarbon condensate, tail gas, and reaction water. The wax is sent on to an upgrading unit for hydrocracking in the presence of hydrogen, where it is chemically split into smaller molecular weight hydrocarbon liquids. A hydrogen recovery unit is used to extract the required quantity of hydrogen from the tail gas as shown, or alternatively from the feed syngas stream. The reaction products, along with that from the upgrading section, are fractionated into the final products of diesel, naphtha, and other light ends, depending on the desired product mix. The production facility is supported by several utility plants, including the power train.
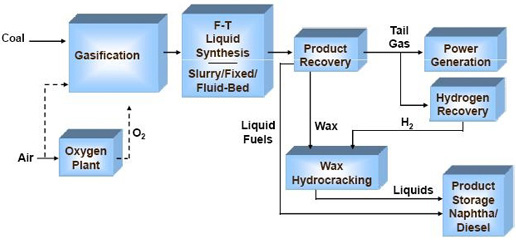
Fig.1: Fisher- Tropsch process
The Fischer-Tropsch process is a catalytic chemical reaction in which carbon monoxide (CO) and hydrogen (H2) in the syngas are converted into hydrocarbons of various molecular weights according to the following equation:
(2n+1) H2 + n CO → Cn H(2n+2) + n H2O
Where n is an integer. Thus, for n=1, the reaction represents the formation of methane, which in most CTL or GTL applications is considered an undesirable byproduct. The Fischer-Tropsch process conditions are usually chosen to maximize the formation of higher molecular weight hydrocarbon liquid fuels which are higher value products. There are other side reactions taking place in the process, among which the water-gas-shift reaction
CO + H2O → H2 + CO2
Is predominant. Depending on the catalyst, temperature, and type of process employed, hydrocarbons ranging from methane to higher molecular paraffins and olefins can be obtained. Small amounts of low molecular weight oxygenate (e.g., alcohol and organic acids) are also formed. The Fischer-Tropsch synthesis reaction, in theory, is a condensation polymerization reaction of CO. Its products obey a well-defined molecular weight distribution according to a relationship known as Shultz-Flory distribution.
Q5) Define octane and cetane number.
A5) Cetane number and octane number both are used to measure the tendency of the fuel ignition. The cetane number refers to the ease with which fuel ignites easily at a relatively low temperature. The Research Octane number and Motor Octane number used in determination of a single cylinder test engine in the laboratory while Road Octane Number measures the anti-knock performance in an actual vehicle under road driving conditions. Cetane rating indicates the cold starting ability of diesel fuel that are mostly recommended by the automakers of about 45. High cetane rating means the fuel will ignite easily from heat and pressure and burn quickly.
Q6) Explain Knocking and chemical constitution of fuel.
A6) Knocking, in an internal-combustion engine, sharp sounds caused by premature combustion of part of the compressed air-fuel mixture in the cylinder. In a properly functioning engine, the charge burns with the flame front progressing smoothly from the point of ignition across the combustion chamber.
Gasoline is a refined product of petroleum consisting of a mixture of hydrocarbons, additives, and blending agents. The composition of gasolines varies widely, depending on the crude oils used, the refinery processes available, the overall balance of product demand, and the product specifications. The typical composition of gasoline hydrocarbons (% volume) is as follows: 4-8% alkanes; 2-5% alkenes; 25-40% isoalkanes; 3-7% cycloalkanes; l-4% cycloalkenes; and 20-50% total aromatics (0.5-2.5% benzene) (IARC 1989). Additives and blending agents are added to the hydrocarbon mixture to improve the performance and stability of gasoline (IARC 1989; Lane 1980). These compounds include anti-knock agents, anti-oxidants, metal deactivators, lead scavengers, anti-rust agents, anti-icing agents, upper-cylinder lubricants, detergents, and dyes (IARC 1989; Lane 1980). At the end of the production process, finished gasoline typically contains more than 150 separate compounds although as many as 1,000 compounds have been identified in some blends.
Q7) Write the Elemental Composition of Petroleum.
A7) Although there is considerable variation between the ratios of organic molecules, the elemental composition of petroleum is well-defined:
- Carbon - 83 to 87%
- Hydrogen - 10 to 14%
- Nitrogen - 0.1 to 2%
- Oxygen - 0.05 to 1.5%
- Sulphur - 0.05 to 6.0%
- Metals - < 0.1%
Q8) Write the Classification of liquid fuels.
A8) The hydrocarbons in crude oil can generally be divided into four categories:
- Paraffins: These have a carbon ratio of 1:2 and form up to 15 to 60% of crude, the ratio 1:2 means that they contain twice the amount as they do for carbon. They are compounds that are never circular they are either in straight or branched chains. The shorter the paraffins are, the lighter the crude is.
- Napthenes: They are also called as cyclic paraffins, they possess cyclic compounds and have the carbon and hydrogen ratio of 1:2. They form about 30-60% of crude. They are generally more viscous and higher in density than paraffins.
- Aromatics: Burning aromatics form soot hence they are undesirable and form around 3 to 30% of crude. They show much less hydrogen in comparison to carbons that are present in paraffins. They have a much less hydrogen in comparison to carbon than is found in paraffins. They are also more viscous. They may exist in a solid or semi-solid when an equivalent paraffin would be a viscous liquid under the same conditions.
- Asphaltic: The hydrogen carbon ratio is1:1 and form about 6% of the crude, they are dense in nature and undesirable, but their 'stickiness' makes them excellent for use in road construction.