Unit - 1
Introduction to Machining Parameters
Q1) Explain CAM Programming.
A1)
This is the more powerful of the two methods. Using this method, you import your part model into a CAM (computer-aided manufacturing) program and define the parameters associated with each, and every machined feature on the part. These parameters include tool diameter, and length, depth of cut, tool path geometry, etc.
Once the part has been designed using conventional mechanical design methods (structural analysis, FEA, fatigue study, etc. ), the part is manufactured using the following method.
1. Create a solid 3D model of the part to be produced. Any standard CAD format is acceptable.
2. Import the solid model into the CAM (computer-aided manufacturing) software. (this demonstration uses MasterCAM
3. Input the raw material stock size, and set the part’s coordinate origin.
4. Input the necessary information for each tool used in machining the part features. Typically, a tool library will exist, which is simply a database of tools, and their related parameters.
5. For each part feature, select the appropriate tool from the library and set the parameters necessary for machining that feature. Typical parameters include spindle speed, depth of cut, feed rate, number of passes, tool path pattern, etc.
There are two ways to program modern CNC machine tools.
Conversational Programming. This is the simpler of the two methods. In effect, this is a macro programming language used to instruct the machine to perform pre-programmed cycles (i. e. Facing, drilling holes in arrays, etc.) When writing a conversational program, you simply enter the appropriate parameters associated with each machining cycle. This is analogous to using the polar array function in SolidWorks or Pro/E; you don’t have to do the layout or trig to find the location of the features; you just specify the essential parameters, and the software does the rest for you.
Q2) What is cutting fluids?
A2)
In many device-device operations, slicing fluids or coolants are used to regulate the damaging results of friction and excessive temperatures. In general, the main capabilities of a coolant are to lubricate and cool.
When slicing a screw thread, both on a lathe or with a tap, the lubricating characteristic is maximum essential; in manufacturing-grinding operations, the cooling characteristic predominates. Water is an extraordinary cooling medium, however it corrodes ferrous substances. Lard oil has extraordinary lubricating qualities, however it has a tendency to come to be rancid. Sulfurized mineral oil is one of the maximum famous coolants.
The sulfur has a tendency to save you chips from the paintings from welding to the end of the device.
For sawing and grinding operations, soluble oil, that's an oily emulsion freely miscible in water, is usually used. Basic device gear Hundreds of sorts of metallic device gear, ranging in length from small machines set up on workbenches to large manufacturing machines weighing numerous hundred tons, are utilized in contemporary-day industry.
They hold the fundamental traits in their 19th- and early 20th-century ancestors and are nevertheless classed as one of the following:
(1) Turning machines (lathes and uninteresting turbines),
(2) Shapers and planers,
(3) Drilling machines,
(4) Milling machines,
(5) Grinding machines,
(6) Strength saws, and
(7) Presses.
Internal cylindrical operations consist of maximum of the not unusual place hollow-machining operations, consisting of drilling, uninteresting, reaming, counter boring, countersinking, and threading with a single-factor device or tap.
Boring includes enlarging and completing a hollow that has been cored or drilled.
Bored holes are extra correct in roundness, concentricity, and parallelism than drilled holes. A hollow is uninterested in a single-factor slicing device that feeds alongside the interior of the work piece.
Boring turbines have round horizontal tables that rotate approximately a vertical axis, and they're designed for uninteresting and turning operations on components which can be too big to be set up on a lathe.
Q3) What is Coating CVD?
A3)
Chemical Vapor Deposition (CVD) is an acronym for Chemical Vapor Deposition. Chemical reactions at temperatures ranging from 700 to 1050°C produce the CVD coating.
CVD coatings provide great adherence to cemented carbide and have a high wear resistance.
The single layer titanium carbide coating was the first CVD coated cemented carbide (TiC). Later on, alumina (Al2O3) and titanium nitride (TiN) coatings were developed. Modern titanium carbonitride coatings (MT-Ti(C,N) or MT-TiCN, also known as MT-CVD) were created more recently to increase grade qualities by keeping the cemented carbide interface intact.
MT-Ti(C,N), Al2O3, and TiN are all used in modern CVD coatings. Through microstructural optimizations and post-treatments, the coating qualities for adhesion, toughness, and wear have been constantly improved.
MT-Ti(C,N) - Its hardness makes it resistant to abrasive wear, resulting in less flank wear.
CVD-Al2O3 is chemically inert and has a low thermal conductivity, making it crater-resistant. It also serves as a thermal barrier to help prevent plastic deformation.
CVD-TiN - Increases wear resistance and can be used to monitor wear.
Post-treatments improve edge hardness and prevent smearing in interrupted cuts.
Applications
In a wide range of applications where wear resistance is critical, CVD coated grades are the first choice. General turning and boring of steel, with crater wear resistance provided by thick CVD coatings; general turning of stainless steels, and milling grades in ISO P, ISO M, and ISO K are examples of such uses. CVD grades are commonly utilised in the periphery insert for drilling.
Q4) Explain Coating PVD?
A4)
PVD coatings (Physical Vapor Deposition) are created at low temperatures (400-600°C). The method entails the evaporation of a metal, which then combines with nitrogen to generate a hard nitride coating on the cutting tool surface.
Due to its hardness, PVD coatings increase wear resistance to a grade. Edge toughness and comb crack resistance are also improved by their compressive stresses.
The key components of PVD coatings are listed below. These elements are combined in sequenced layers and/or lamellar coatings in modern coatings. Lamellar coatings have many thin layers in the Nano scale range, increasing the coating's hardness.
PVD-TiN - The first PVD coating was titanium nitride. It has a golden color and all-around characteristics.
PVD-Ti(C,N) - Titanium carbonitride is tougher than TiN and adds resistance to flank wear.
PVD-(Ti,Al)N - Titanium aluminum nitride has a high hardness and oxidation resistance, resulting in improved overall wear resistance.
PVD-oxide is employed because of its chemical inertness and increased crater resistance.
Applications
For robust, yet sharp, cutting edges, as well as smearing materials, PVD coated grades are recommended. All solid end mills and drills, as well as the majority of grades for grooving, threading, and milling, are used in this way. PVD-coated grades are also commonly utilised in finishing applications and as the drilling's central insert grade.
Q5) Explain Cemented Carbide.
A5)
- Cemented carbide is a powdery metallurgical material that is made up of tungsten carbide (WC) particles and a cobalt-rich binder (Co). More than 80% of hard phase WC is present in cemented carbides for metal cutting applications.
- Other essential components, particularly in gradient sintered grades, include additional cubic carbonitrides.
- The cemented carbide body is sintered to full density after being shaped into a body using powder pressing or injection molding techniques.
- The finer the grain size, the higher the hardness at a given binder phase content; the finer the grain size, the greater the hardness at a given binder phase content.
- The toughness and resistance to plastic deformation of the grade are controlled by the amount and content of the Co-rich binder.
- At the same WC grain size, adding more binder results in a harder grade that is more susceptible to plastic deformation wear. A brittle material can be caused by a low binder content.
- Cubic carbonitrides, also known as -phase, are commonly used to boost hot hardness and create gradients.
- To combine better plastic deformation resistance with edge toughness, gradients are used. Cubic carbonitrides concentrated on the cutting edge enhance hot hardness where it is required.
- A binder rich in tungsten carbide structure prevents cracks and chip hammering fractures beyond the cutting edge.
Cermet cutting tool material Cermet is a titanium-based cemented carbide with hard particles. Cermet is a combination of the words ceramic and metal. Cermet was originally made up of TiC and nickel. Modern cermet’s have a specified structure of titanium carbonitride Ti(C,N) core particles, a second hard phase of (Ti,Nb,W)(C,N), and a W-rich cobalt binder, and are nickel-free.
Wear resistance is added by Ti(C,N), plastic deformation resistance is increased by the second hard phase, and toughness is controlled by the amount of cobalt.
Cermet outperforms cemented carbide in terms of wear resistance and smearing resistance. On the other side, it has a lower compressive strength and is less resistant to thermal shock. PVD coatings can also be applied on Cermets to improve wear resistance.
Applications
Cermet grades are utilised in smearing situations when there is a difficulty with a built-up edge. Even after long times in the cut, its self-sharpening wear pattern keeps cutting forces low. This allows for a long tool life and tight tolerances in finishing operations, as well as bright surfaces.
Stainless steel finishing, nodular cast iron finishing, low carbon steel finishing, and ferritic steel finishing are all common applications. Cermets can be used to troubleshoot problems in any ferrous material.
Q6) Explain Nomenclature of single point cutting tool?
A6)
- Shank: The part of single point cutting tool which goes into the tool holder. Shank is used to hold the tool.
- Flank: The surface below and adjacent of the cutting edges is called flank surface. There are two flank surfaces, first one is minor flank and second one major is flank. The minor flank surface lies below and adjacent to the end cutting edge. The major flank lies below and adjacent to the side cutting edge.
- Base: It is the portion of the shank that lies opposite to the top face of the shank.
- Face: Face is the top portion of the tool along which chips slides. It is designed in such a manner that the chips slides on it in upward direction.
- Cutting edge: The edge on the tool that removes materials from the work piece is called cutting edges. It lies on the face of the cutting tool. The single point cutting tool has two edges:
(i) Side cutting edge: The top edge of the major flank
(ii) End cutting edge: The top edge of the minor flank
- Nose or cutting point: It is the intersection point of major cutting edge and minor cutting edge.
- Nose radius: It is the radius of the nose. It increases the life of the tool and provides better surface finish.
- The angles of a single point cutting tool have great importance. Each angle has its own function and specialty.
- End Cutting Edge Angle: It is the angle formed in between the end cutting edge and a line perpendicular to the shank.
- Side Cutting Edge Angle: It is the angle formed in between the side cutting edge and a line parallel to the shank.
- Back Rack Angle (αb): It is the angle formed between the tool face and line parallel to the base.
- End Relief Angle: It is the angle formed between the minor flank and a line normal to the base of the tool. It is also known as front clearance angle. It avoids the rubbing of the work piece against tool.
Q7) Write short note on tool material properties.
A7)
1. Hot Hardness:
Generally hardness is measured at room temperature. But the time period Hot hardness shows that the hardness at expanded temperature. We recognize that the hardness decreases as temperature increases. In steel slicing, warmth is generated throughout the process. The device fabric need to be capable of preserve its hardness, put on resistance and electricity at this kind of excessive expanded temperature, which degrees almost 600°C to 1800°C. Fig. 9. 36 indicates the variant of hardness of various device fabric with growth in temperature. Variation of Hardness with Temperature
2. Toughness:
The device fabric need to be hard sufficient in order that it is able to paintings without fracture in effect forces takes place in interrupted slicing operations (along with milling, turning of splined shaft). It need to be capable of resist vibrations passed off throughout machining.
3. Wear Resistance:
The term wear means loss of material. As tool continues cutting, its cutting edge which is always in touch with the work piece and the rake face (over which the chip flows) lose their material gradually with time. Therefore the tool material must have wear resistance, so that an acceptable tool life is obtained before the tool is indexed or replaced.
4. Chemical Stability or Inertness:
Tool fabric need to have chemical balance or inertness with recognize to the paintings fabric, in order that any unwanted reactions among device fabric, and paintings fabric are avoided.
5. Shock Resistance:
Tool fabric need to have excessive resistance towards thermal and mechanical shocks, in particular in intermittent slicing wherein device-paintings engages and dis-engages at everyday intervals.
6. Low Friction:
Tool fabric need to have low coefficient of friction. So that the warmth generated could be lower, and device lifestyles increases.
Q8) What are the types of machine tools in use?
A8)
Machine Tools are extensively categorized into 3 groups, and people are:
- General Purpose Machine Tools
- Single Purpose Machine Tools
- Special motive device Tools
Let me talk one via way of means of one,
1. General Purpose Machine Tools:
General-motive device gear are designed to carry out a terrific style of machining operations with quite a few work pieces. For this sort of Machine, gear want a few attachments, like in case of lathe we use a mandrel, and in milling we use indexing head, like those. The call comes on this class of device gear are a lathe, drilling, milling, shaping, etc.
2. Single Purpose Machine Tools:
As the call denotes "unmarried motive" meaning this sort of device is designed to carry out an unmarried operation however it may device some of the work piece. This sort of device are typically appropriate for effective works.
These are the a few operation that fell into this class, Making of Crank Shaft Machining of Crank-pins machining of tools via way of means of tools hobbling process
3. Special Purpose Machine Tools:
The special-motive device is used for appearing a specific operation.
These sorts of device gear are synthetic individually.
We can use those sorts of device gear in big manufacturing in which the manufacturing price is pretty higher, even though we are able to use it for mass manufacturing too.
Q9) What is orthogonal cutting?
A9)
- By definition, orthogonal cutting uses a wedge-shaped tool during which the cutting edge is perpendicular to the direction of cutting speed.
- Because the tool is forced into the fabric, the chip is created by shear deformation on a plane referred to as the shear plane that is directed at angle Ø with the surface of the work.
- Solely at the sharp cutting edge of the tool will failure of the fabric occur, leading to separation of the chip from the parent material?
- On the shear plane, wherever the majority of the energy is consumed in machining, the fabric is plastically distorted. The tool in orthogonal cutting has solely 2 components of geometry:
(1) Rake angle and
(2) Clearance angle.
5. As indicated antecedently, the rake angle α determines the direction that the chip flows because it is created from the work part; and also the clearance angle provides a little clearance between the tool flank and the fresh generated surface.
6. Throughout cutting, the cutting edge of the tool is positioned an exact distance below the first surface. This corresponds to the thickness of the chip before chip formation, too.
7. Because the chip is created on the shear plane, its thickness will increase to tc.
8. The magnitude relation of two to tic is named the chip thickness ratio (or merely the chip ratio). Since the chip thickness once cutting is usually larger than the corresponding thickness before cutting, the chip magnitude relation can forever be not up to one.
9. Additionally to to, the orthogonal cut incorporates a breadth dimension w, even supposing this dimension doesn't contribute abundant to the analysis in orthogonal cutting.
10. The geometry of the orthogonal cutting model permits us to determine a very important relationship between the chip thickness magnitude relation, the rake angle, and also the shear angle.
Q10) what is oblique cutting?
A10)
Cuttings device geometry is simplified from the 3-D (oblique) geometry to a 2-D (orthogonal) geometry.
Chip Formation: Simplified Orthogonal Machining’s in-aircraft version of the slicing procedure
Assumptions Work-piece: a flat plate Cutting device: geometry is given through the lower back rake angles
(a) Only Shear: in a single singles aircraft, that's doing f levels with the path of speed. Chip is fashioned through shearing.
High shear pressure over a slim region big pressure and excessive pressure price plastic deformation because of radial compression.
The compressions area travels beforehand of the device.
Elastic to plastic deformations whilst yield pressure is exceeded.
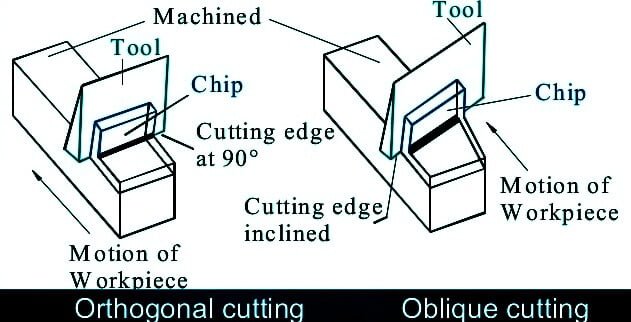
Fig: Orthogonal and oblique cutting
Q11) Explain Mechanics of metal cutting?
A11)
- Metal cutting is a process in which a wedge-shaped cutting tool is used that engages the work piece to remove a layer of material in the form of chips.
- Metal cutting is a process of extensive plastic deformation to form a chip that is removed afterward. The basic mechanism of chip formation is same for all machining operations. By assuming the cutting action to be continuous, we can develop continuous model of cutting process.
- To perform the operation, relative motion is required between the tool and work. This relative motion is achieved in most of the machining operations by means of a primary motion, called cutting speed, and a secondary motion, called feed.
- The shape of the tool and tool penetration into the work surface, combined with these motions, produces the desired geometry of the resulting work piece surface.
- Metal reducing operation is illustrated in Fig.1. The paintings piece is securely clamped in a gadget device vice or clamps or chuck or collet.
- A wedge form device is ready to a sure intensity of reduce and is pressured to transport in path as proven in figure.
All conventional machining strategies require a reducing device having a simple wedge form on the reducing area. The device will reduce or shear off the steel, supplied
(i) The device is more difficult than the steel,
(ii) The device is nicely fashioned in order that its area may be powerful in reducing the steel,
(iii) The device is robust sufficient to withstand reducing pressures however eager sufficient to sever the steel, and
(iv) Supplied there's motion of device relative to the fabric or vice versa, which will make reducing motion possible.
Most steel reducing is accomplished with the aid of using excessive pace metallic equipment or carbide equipment. In steel reducing, the device does now no longer slide thru steel as a jack knife does thru wood, now no longer does the device break up the steel as an awl does a log.
Actually, the steel is pressured off the work piece with the aid of using being compressed, shearing off, and sliding alongside the face of the reducing device. The manner a reducing device cuts the steel may be defined as follows. All metals with inside the strong country have a function crystalline shape, often known as grain shape.
The grain or crystals range in length from very great to very coarse, relying upon the kind of steel and its heat-treatment.
The reducing device advances once more with inside the paintings piece. Heavy forces are exerted at the crystals in the front of the device face.
These crystals, in flip exert comparable pressures on crystals in advance of them, with inside the path of the reduce or pressure carried out with the aid of using the cutter. As the device keeps to advance, the fabric at sheared factor is sheared with the aid of using the reducing fringe of the device or it can be torn unfastened with the aid of using the motion of the bending chip that's being formed.
As the device advances, most pressure is exerted alongside sheared line, that's known as the shear aircraft. This aircraft is about perpendicular to the reducing face of the device.
There exists a shear region on each aspects of the shear aircraft, whilst the pressure of the device exceeds the energy of the fabric on the shear aircraft, rupture or slippage of the crystalline grain shape occurs, accordingly forming the steel chip.
The chip receives separated from the work piece fabric and movements up alongside the device face. In addition, whilst the steel is sheared, the crystals are elongated, the path of elongation being specific from that of shear.
Q12) Explain Merchants circle.
A12)
Merchant represented various cutting forces and their components in a circle which is known a Merchant’s Circle Diagram. For establishing the relationship between measurable and actual forces Merchant’s circle diagram is used.
Merchant circle diagram is used to analyze the forces that are acting in metal cutting.
In the analysis of three forces system, which balance each other for cutting to occur.
Each system represents a triangle of forces.
α = Back rake angle.
φ = Share angle.
ƞ = Angle of friction
Merchant’s method for orthogonal cutting is based on the assumptions that shear plane angle following assumptions are made
- Orthogonal cutting process with single point cutting tool is to be considered.
- The chip is considered to be in equilibrium under action of two equal and opposite collinear forces.
- The stress is maximum at the shear plane and it remains constant.
- The shearing takes place in a direction in which the energy required for shearing is minimum.
- The cutting tool has sharp cutting edge.
- The cutting velocity remains constant.
- There is no sideway flow of chip.
- There is no inertial force on chip.
- The work material is perfectly rigid and perfectly plastic
The three triangles of forces in merchant’s circle diagram are listed below:
A triangle of forces for the cutting forces,
- A triangle of forces for the shear forces,
- A triangle of forces for the frictional forces.
- From the figure following relations were obtained:
- Proper use of Merchant’s Circle Diagram enables the followings:
- Easy, reasonably accurate and quick determination of several other forces from a few known forces involved in machining.
- Friction at chip tool interface and dynamic yield shear strength can be determined.
- Equations relating the different forces in machining are easily developed.
Some limitations of use of Merchant’s Circle Diagram:
- Merchant’s circle diagram (MCD) is only valid for orthogonal cutting process.
- By the ratio, F/N, the Merchant’s Circle Diagram gives apparent coefficient of friction.
- It is based on single shear plane theory.
Q13) Explain terminologies in Merchant circle.
A13)
Shear Plane
The work piece material deforms plastically ahead of the cutting tool edge. It slides on the rake face of the tool and forms a chip. The region between the start of the chip formation and the unreformed (elastically deformed) work piece is called the zone of plastic deformation.
The size of the zone of plastic deformation depends on cutting parameters. The size of this plastic deformation zone decreases with the increase of cutting speed. In the analysis of thin zones, it is always assumed that the work material shears across a plane, and forms the chip. This plane is called the shear plane.
Shear Plane Angle
A shear plane angle is an angle between the cutting velocity vector, and the shear plane. The chip is formed by plastic deformation of work material, and the material flow is continuous.
Discontinuous chip: Once comparatively brittle materials (e.g., solid irons) are machined at low cutting speeds, the chips typically kind into separate segments (sometimes the segments are loosely attached). This tends to impart irregular texture to the machined surface. High tool–chip friction and enormous feed and depth of cut promote the formation of this chip kind.
Continuous chip: Once ductile work materials are cut at high speeds and comparatively little feeds and depths, long continuous chips are fashioned. An honest surface finish usually results once this chip kind is created. a pointy cutting edge on the tool and low tool–chip friction encourage the formation of continuous chips. Long, continuous chips (as in turning) will cause issues with respect to chip disposal and/or tangling regarding the tool. To resolve these issues, turning tools are typically equipped with chip breakers.
Serrated chips: These chips are semi-continuous within the sense that they possess a saw-tooth look that's made by a rotary chip formation of alternating high shear strain followed by low shear strain. This fourth form of chip is most closely related to sure difficult-to-machine metals admire metal alloys, nickel-base super alloys, and primary solid solution unstained steels after they are machined at higher cutting speeds. However, the development is additionally found with additional common work metals (e.g., steels) after they are cut at high speeds.
Q14) Derive an expression for Cutting Speed.
A14)
F.W. Taylor has conducted numerous experiments in the field of metal cutting. In 1907, he gave the following relationship between tool life and cutting speed, which is known as Taylor’s Tool Life Equation.
VCTn = C
Where, V= Cutting speed (m/min)
T= Tool life (min) C = Constant or machining constant
n = Tool life index. It depends on tool and work material combination and cutting conditions.
If T = 1 min
Then C = Vc
So, the constant C can be interpreted physically as the cutting speed for which the tool life is equal to one min. The tool life equation can be represented on log-log paper; it becomes straight line
Q15) How can we calculate tool life?
A15)
Every device or tool has its functional and expected life of work. At the expiry of which it may still be operational, but not efficiently. During it usage, the tool losses its material, i.e., it gets worn out. As the wearing of tool increases, the tool starts to lose its efficiency. Therefore, its life has to be defined and on the expiry of its life, it should be reground for fresh use.
The tool life can be defined as:
(i) The time elapsed between two successive grindings.
(ii) The period during which a tool cuts satisfactorily.
(iii) The total time duration accumulated before tool failure occurs.
Tool life is expressed in minutes.
The relation between cutting speed and tool life can be obtained by the Taylor’s tool life equation:
VTn = C
Methods for Tool Life Measurements:
The most commonly used methods for tool life measurements are:
- Machining Time:
- Elapsed time of operation of machine tool.
- Actual Cutting Time:
- The time during which the tool actually cuts.
- A fixed size of Wear Land on Flank Surface:
- On carbide and ceramic tools where crater wear is negligible, tool life can be taken as corresponding to 0.038 or 0.076 mm of wear land on the flank surface for finishing respectively.
- Volume of metal removed.
- Number of pieces machined.
The tool life between replacement and re-conditioning can be defined in a number of ways, as:
(a) Actual cutting time taken to failure.
(b) Volume of metal removed to failure.
(c) Number of parts produced to failure.
(d) Cutting speed for a time to failure.
(e) Length of work machined to failure.
- Tool Life Expectancy (Taylor’s Tool Life Equation):
- In 1907, F. W. Taylor developed the relation between tool life, cutting speed and temperature keeping feed as constant. The Taylor’s Equation for Tool Life Expectancy provides good approximation.
- VCTn = C
- A more general form of the equation considering depth of cut and feed rate is given as
- VcTnDxFy = C
- Where, KC = Cutting speed (m/min)
- T = Tool life (min)
- D = Depth of cut (mm)
- F = Feed rate (mm/rev)
- x, y = Exponents, that are determined experimentally for each cutting conditions.
- n = Exponent, that depends on tool materials.
- Value of n = 0.1 - 0.2; for H.S.S. Tools
- 0.2 -0.4; for Carbide tools
- 0.4 - 0.6; for Ceramic tools
C = Machining constant, computed by experimentation or published data-book. It depends on properties of tool material, work piece and feed rate.
Q16) What is the criteria for tool life calculation?
A16)
- Due to wear on the tool, the cutting force increases and surface finish deteriorates. Therefore, when should we say that a tool has failed and it should be reground? In other words, certain criterion is required for judging the tool failure.
- A tool fails when it no longer performs its function properly. This may have different meaning under different circumstances. In a roughing operation, where, surface finish and dimensional accuracy are of little importance, a tool failure can mean an excessive rise in cutting forces and power requirements.
- In a finishing operation, where, surface finish and dimensional accuracy are prime important, a tool failure will mean that the specified conditions of surface finish and dimensional accuracy can no longer be achieved. All of these failures are basically related to the wear on the clearance face of the tool.
The following are some criterion for judging tool life/failure:
(i) Complete failure.
(ii) Flank or crater failure.
(iii) Finish failure.
(iv) Size failure.
(v) Cutting force failure.
(i) Complete Failure:
- According to this criterion, the cutting with the tool is continued till it is able to cut. So when the tool fails to cut, then only it should be reground. This criterion is not used in practice because of its obvious disadvantages.
(ii) Flank or Crater Failure:
- According to this criterion, when the wear on the flank reaches a certain height the cutting with the tool is discontinued and grinding is done. Say when the flank wear height h equals to 0.3 mm, for example, the tool is said to have failed. Some common recommended values of wear land are given in Table (a, b).
- Due to wear on the flank, the actual depth of cut decreases from AC to BC as shown in Fig. The work piece becomes taper if cutting continued. This is the most usual criterion followed in practice. The flank wear is measured with a tool maker’s microscope.
- Also, it is important to note that, the flank wear is not uniform along the active cutting edge, therefore, it is necessary to specify the locations and the degree of wear, when deciding tool life criterion, before regrinding.
(iii) Finish Failure:
- According to this criterion, when the surface roughness reaches a specified high value, the cutting with the tool is stopped and grinding is done. Say at a particular cutting condition the surface roughness, comes to be 0.7 microns. As in process of cutting the flank wear develops so the cutting edge becomes rough and irregular so the surface roughness gradually increases, as shown in Fig. Say 1.3 microns, for example, are kept as a criterion.
- The roughness of the surface is measured continuously along its length. When the roughness reaches the specified value, the cutting is discontinued. For example, this maximum specified value of surface roughness may be occurs on the 10th work piece, so the 11th and next work pieces won’t be machined with the same tool, without regrinding.
- This criterion becomes especially important when close fitting objects are machined. Due to rough and uneven surfaces, the proper fitting may not be done.
(iv) Size Failure:
- According to this criterion, a tool will be considered to have failed if there is a deviation in the size of a produced finished component from its specified value.
(v) Cutting Force Failure:
- According to this criterion, a tool will be considered to have failed, if the amount of cutting force increases by certain specified amount. This is due to flank wear. Flank wear increases the area of contact between the work piece and the tool, resulting into increase in the cutting force. Fig. Shows that an increase in cutting force with development to flank wear.
Q17) What are the important factors related to tool life?
A17)
The following factors play an important role in tool life:
(i) Cutting speed.
(ii) Feed rate and Depth of cut.
(iii) Hardness of work piece.
(iv) Microstructure of work piece.
(v) Tool material.
(vi) Tool geometry.
(vii) Type of cutting fluid and its method of application.
(viii) Nature of cutting.
(ix) Grain size of work piece.
(x) Rigidity of work piece machine-tool system.
Q18) What are the machining parameters.
A18)
When planning a successful metal cutting operation, selecting the right cutting tool material and grade is critical.
When choosing the right choice, it's necessary to have a fundamental understanding of each cutting tool's material and performance. The work piece material to be machined, the component type and shape, the machining circumstances, and the level of surface quality required for each operation are all factors to consider.
This section explains the different types of cutting tools, their benefits, and how to use them properly.
Cutting tool materials come in a variety of hardness, toughness, and wear resistance combinations, and are classified into a number of grades with various qualities. In general, a cutting tool material that is effective in its use should be:
• Tough, to resist wear and distortion on the flanks
• Tough enough to withstand mass breakage
• Non-reactive with the material of the work piece
• Chemically stable, so it won't oxidase or diffuse.
• Resistant to extreme temperature changes
Q19) Write note on CNC machine.
A19)
- CNC stands for computer numeric controlled.
- It refers to any machine tool (i. e. Mill, lathe, drill press, etc.) which uses a computer to electronically control the motion of one or more axes on the machine.
- The development of NC machine tools started from a task supported by the US Air Force in the early 1950s, involving MIT, and several machine-tool manufacturing companies. The need was recognized for machines to be able to manufacture complex jet aircraft parts.
- As computer technology evolved, computers replaced the more inflexible controllers found on the NC machines, hence the dawn of the CNC era.
- CNC machine tools use software programs to provide the instructions necessary to control the axis motions, spindle speeds, tool changes, and so on.
- CNC machine tools allow multiple axes of motion simultaneously, resulting in 2D, and 3D contouring ability.
- CNC technology also increases productivity, and quality control by allowing multiple parts to be produced using the same program, and tooling.
Q20) Explain Operations in CNC programming.
A20)
The following cycles are typical of the machining operations available when programming a 3-axis CNC milling machine.
Position. Used to move the XYZ coordinates at rapid federate.
Drill one. Used to position the tool at a specific XYZ coordinate position to automatically drill a hole. The automatic drill cycles allow for simple drilling, peck drilling, spot-facing, and bore cycles.
Drill pattern. Used to define polar or rectangular whole arrays for automatic drilling.
Line. Used to cut straight lines along an axis or a diagonal at the desired feed rate.
Arc. Used to cut a circle or partial circle that is part of a series of cuts that usually includes lines as well.
Face. Used to define a rectangular zigzag pattern used to clean off a part surface.
Pocket. Used to clear the material out of a rectangle, circle, or polygon.
Frame. Used to cut the inside or outside outline of a rectangle, circle, or polygon.
Tool. Used to enter tool parameters, machine function parameters, and program pause/stop codes.
Scale/mirror. Used to scale, and/or mirror other part features.
Rotate. Used to repeat other part features around a specific center of rotation.
Unit - 1
Introduction to Machining Parameters
Q1) Explain CAM Programming.
A1)
This is the more powerful of the two methods. Using this method, you import your part model into a CAM (computer-aided manufacturing) program and define the parameters associated with each, and every machined feature on the part. These parameters include tool diameter, and length, depth of cut, tool path geometry, etc.
Once the part has been designed using conventional mechanical design methods (structural analysis, FEA, fatigue study, etc. ), the part is manufactured using the following method.
1. Create a solid 3D model of the part to be produced. Any standard CAD format is acceptable.
2. Import the solid model into the CAM (computer-aided manufacturing) software. (this demonstration uses MasterCAM
3. Input the raw material stock size, and set the part’s coordinate origin.
4. Input the necessary information for each tool used in machining the part features. Typically, a tool library will exist, which is simply a database of tools, and their related parameters.
5. For each part feature, select the appropriate tool from the library and set the parameters necessary for machining that feature. Typical parameters include spindle speed, depth of cut, feed rate, number of passes, tool path pattern, etc.
There are two ways to program modern CNC machine tools.
Conversational Programming. This is the simpler of the two methods. In effect, this is a macro programming language used to instruct the machine to perform pre-programmed cycles (i. e. Facing, drilling holes in arrays, etc.) When writing a conversational program, you simply enter the appropriate parameters associated with each machining cycle. This is analogous to using the polar array function in SolidWorks or Pro/E; you don’t have to do the layout or trig to find the location of the features; you just specify the essential parameters, and the software does the rest for you.
Q2) What is cutting fluids?
A2)
In many device-device operations, slicing fluids or coolants are used to regulate the damaging results of friction and excessive temperatures. In general, the main capabilities of a coolant are to lubricate and cool.
When slicing a screw thread, both on a lathe or with a tap, the lubricating characteristic is maximum essential; in manufacturing-grinding operations, the cooling characteristic predominates. Water is an extraordinary cooling medium, however it corrodes ferrous substances. Lard oil has extraordinary lubricating qualities, however it has a tendency to come to be rancid. Sulfurized mineral oil is one of the maximum famous coolants.
The sulfur has a tendency to save you chips from the paintings from welding to the end of the device.
For sawing and grinding operations, soluble oil, that's an oily emulsion freely miscible in water, is usually used. Basic device gear Hundreds of sorts of metallic device gear, ranging in length from small machines set up on workbenches to large manufacturing machines weighing numerous hundred tons, are utilized in contemporary-day industry.
They hold the fundamental traits in their 19th- and early 20th-century ancestors and are nevertheless classed as one of the following:
(1) Turning machines (lathes and uninteresting turbines),
(2) Shapers and planers,
(3) Drilling machines,
(4) Milling machines,
(5) Grinding machines,
(6) Strength saws, and
(7) Presses.
Internal cylindrical operations consist of maximum of the not unusual place hollow-machining operations, consisting of drilling, uninteresting, reaming, counter boring, countersinking, and threading with a single-factor device or tap.
Boring includes enlarging and completing a hollow that has been cored or drilled.
Bored holes are extra correct in roundness, concentricity, and parallelism than drilled holes. A hollow is uninterested in a single-factor slicing device that feeds alongside the interior of the work piece.
Boring turbines have round horizontal tables that rotate approximately a vertical axis, and they're designed for uninteresting and turning operations on components which can be too big to be set up on a lathe.
Q3) What is Coating CVD?
A3)
Chemical Vapor Deposition (CVD) is an acronym for Chemical Vapor Deposition. Chemical reactions at temperatures ranging from 700 to 1050°C produce the CVD coating.
CVD coatings provide great adherence to cemented carbide and have a high wear resistance.
The single layer titanium carbide coating was the first CVD coated cemented carbide (TiC). Later on, alumina (Al2O3) and titanium nitride (TiN) coatings were developed. Modern titanium carbonitride coatings (MT-Ti(C,N) or MT-TiCN, also known as MT-CVD) were created more recently to increase grade qualities by keeping the cemented carbide interface intact.
MT-Ti(C,N), Al2O3, and TiN are all used in modern CVD coatings. Through microstructural optimizations and post-treatments, the coating qualities for adhesion, toughness, and wear have been constantly improved.
MT-Ti(C,N) - Its hardness makes it resistant to abrasive wear, resulting in less flank wear.
CVD-Al2O3 is chemically inert and has a low thermal conductivity, making it crater-resistant. It also serves as a thermal barrier to help prevent plastic deformation.
CVD-TiN - Increases wear resistance and can be used to monitor wear.
Post-treatments improve edge hardness and prevent smearing in interrupted cuts.
Applications
In a wide range of applications where wear resistance is critical, CVD coated grades are the first choice. General turning and boring of steel, with crater wear resistance provided by thick CVD coatings; general turning of stainless steels, and milling grades in ISO P, ISO M, and ISO K are examples of such uses. CVD grades are commonly utilised in the periphery insert for drilling.
Q4) Explain Coating PVD?
A4)
PVD coatings (Physical Vapor Deposition) are created at low temperatures (400-600°C). The method entails the evaporation of a metal, which then combines with nitrogen to generate a hard nitride coating on the cutting tool surface.
Due to its hardness, PVD coatings increase wear resistance to a grade. Edge toughness and comb crack resistance are also improved by their compressive stresses.
The key components of PVD coatings are listed below. These elements are combined in sequenced layers and/or lamellar coatings in modern coatings. Lamellar coatings have many thin layers in the Nano scale range, increasing the coating's hardness.
PVD-TiN - The first PVD coating was titanium nitride. It has a golden color and all-around characteristics.
PVD-Ti(C,N) - Titanium carbonitride is tougher than TiN and adds resistance to flank wear.
PVD-(Ti,Al)N - Titanium aluminum nitride has a high hardness and oxidation resistance, resulting in improved overall wear resistance.
PVD-oxide is employed because of its chemical inertness and increased crater resistance.
Applications
For robust, yet sharp, cutting edges, as well as smearing materials, PVD coated grades are recommended. All solid end mills and drills, as well as the majority of grades for grooving, threading, and milling, are used in this way. PVD-coated grades are also commonly utilised in finishing applications and as the drilling's central insert grade.
Q5) Explain Cemented Carbide.
A5)
- Cemented carbide is a powdery metallurgical material that is made up of tungsten carbide (WC) particles and a cobalt-rich binder (Co). More than 80% of hard phase WC is present in cemented carbides for metal cutting applications.
- Other essential components, particularly in gradient sintered grades, include additional cubic carbonitrides.
- The cemented carbide body is sintered to full density after being shaped into a body using powder pressing or injection molding techniques.
- The finer the grain size, the higher the hardness at a given binder phase content; the finer the grain size, the greater the hardness at a given binder phase content.
- The toughness and resistance to plastic deformation of the grade are controlled by the amount and content of the Co-rich binder.
- At the same WC grain size, adding more binder results in a harder grade that is more susceptible to plastic deformation wear. A brittle material can be caused by a low binder content.
- Cubic carbonitrides, also known as -phase, are commonly used to boost hot hardness and create gradients.
- To combine better plastic deformation resistance with edge toughness, gradients are used. Cubic carbonitrides concentrated on the cutting edge enhance hot hardness where it is required.
- A binder rich in tungsten carbide structure prevents cracks and chip hammering fractures beyond the cutting edge.
Cermet cutting tool material Cermet is a titanium-based cemented carbide with hard particles. Cermet is a combination of the words ceramic and metal. Cermet was originally made up of TiC and nickel. Modern cermet’s have a specified structure of titanium carbonitride Ti(C,N) core particles, a second hard phase of (Ti,Nb,W)(C,N), and a W-rich cobalt binder, and are nickel-free.
Wear resistance is added by Ti(C,N), plastic deformation resistance is increased by the second hard phase, and toughness is controlled by the amount of cobalt.
Cermet outperforms cemented carbide in terms of wear resistance and smearing resistance. On the other side, it has a lower compressive strength and is less resistant to thermal shock. PVD coatings can also be applied on Cermets to improve wear resistance.
Applications
Cermet grades are utilised in smearing situations when there is a difficulty with a built-up edge. Even after long times in the cut, its self-sharpening wear pattern keeps cutting forces low. This allows for a long tool life and tight tolerances in finishing operations, as well as bright surfaces.
Stainless steel finishing, nodular cast iron finishing, low carbon steel finishing, and ferritic steel finishing are all common applications. Cermets can be used to troubleshoot problems in any ferrous material.
Q6) Explain Nomenclature of single point cutting tool?
A6)
- Shank: The part of single point cutting tool which goes into the tool holder. Shank is used to hold the tool.
- Flank: The surface below and adjacent of the cutting edges is called flank surface. There are two flank surfaces, first one is minor flank and second one major is flank. The minor flank surface lies below and adjacent to the end cutting edge. The major flank lies below and adjacent to the side cutting edge.
- Base: It is the portion of the shank that lies opposite to the top face of the shank.
- Face: Face is the top portion of the tool along which chips slides. It is designed in such a manner that the chips slides on it in upward direction.
- Cutting edge: The edge on the tool that removes materials from the work piece is called cutting edges. It lies on the face of the cutting tool. The single point cutting tool has two edges:
(i) Side cutting edge: The top edge of the major flank
(ii) End cutting edge: The top edge of the minor flank
- Nose or cutting point: It is the intersection point of major cutting edge and minor cutting edge.
- Nose radius: It is the radius of the nose. It increases the life of the tool and provides better surface finish.
- The angles of a single point cutting tool have great importance. Each angle has its own function and specialty.
- End Cutting Edge Angle: It is the angle formed in between the end cutting edge and a line perpendicular to the shank.
- Side Cutting Edge Angle: It is the angle formed in between the side cutting edge and a line parallel to the shank.
- Back Rack Angle (αb): It is the angle formed between the tool face and line parallel to the base.
- End Relief Angle: It is the angle formed between the minor flank and a line normal to the base of the tool. It is also known as front clearance angle. It avoids the rubbing of the work piece against tool.
Q7) Write short note on tool material properties.
A7)
1. Hot Hardness:
Generally hardness is measured at room temperature. But the time period Hot hardness shows that the hardness at expanded temperature. We recognize that the hardness decreases as temperature increases. In steel slicing, warmth is generated throughout the process. The device fabric need to be capable of preserve its hardness, put on resistance and electricity at this kind of excessive expanded temperature, which degrees almost 600°C to 1800°C. Fig. 9. 36 indicates the variant of hardness of various device fabric with growth in temperature. Variation of Hardness with Temperature
2. Toughness:
The device fabric need to be hard sufficient in order that it is able to paintings without fracture in effect forces takes place in interrupted slicing operations (along with milling, turning of splined shaft). It need to be capable of resist vibrations passed off throughout machining.
3. Wear Resistance:
The term wear means loss of material. As tool continues cutting, its cutting edge which is always in touch with the work piece and the rake face (over which the chip flows) lose their material gradually with time. Therefore the tool material must have wear resistance, so that an acceptable tool life is obtained before the tool is indexed or replaced.
4. Chemical Stability or Inertness:
Tool fabric need to have chemical balance or inertness with recognize to the paintings fabric, in order that any unwanted reactions among device fabric, and paintings fabric are avoided.
5. Shock Resistance:
Tool fabric need to have excessive resistance towards thermal and mechanical shocks, in particular in intermittent slicing wherein device-paintings engages and dis-engages at everyday intervals.
6. Low Friction:
Tool fabric need to have low coefficient of friction. So that the warmth generated could be lower, and device lifestyles increases.
Q8) What are the types of machine tools in use?
A8)
Machine Tools are extensively categorized into 3 groups, and people are:
- General Purpose Machine Tools
- Single Purpose Machine Tools
- Special motive device Tools
Let me talk one via way of means of one,
1. General Purpose Machine Tools:
General-motive device gear are designed to carry out a terrific style of machining operations with quite a few work pieces. For this sort of Machine, gear want a few attachments, like in case of lathe we use a mandrel, and in milling we use indexing head, like those. The call comes on this class of device gear are a lathe, drilling, milling, shaping, etc.
2. Single Purpose Machine Tools:
As the call denotes "unmarried motive" meaning this sort of device is designed to carry out an unmarried operation however it may device some of the work piece. This sort of device are typically appropriate for effective works.
These are the a few operation that fell into this class, Making of Crank Shaft Machining of Crank-pins machining of tools via way of means of tools hobbling process
3. Special Purpose Machine Tools:
The special-motive device is used for appearing a specific operation.
These sorts of device gear are synthetic individually.
We can use those sorts of device gear in big manufacturing in which the manufacturing price is pretty higher, even though we are able to use it for mass manufacturing too.
Q9) What is orthogonal cutting?
A9)
- By definition, orthogonal cutting uses a wedge-shaped tool during which the cutting edge is perpendicular to the direction of cutting speed.
- Because the tool is forced into the fabric, the chip is created by shear deformation on a plane referred to as the shear plane that is directed at angle Ø with the surface of the work.
- Solely at the sharp cutting edge of the tool will failure of the fabric occur, leading to separation of the chip from the parent material?
- On the shear plane, wherever the majority of the energy is consumed in machining, the fabric is plastically distorted. The tool in orthogonal cutting has solely 2 components of geometry:
(1) Rake angle and
(2) Clearance angle.
5. As indicated antecedently, the rake angle α determines the direction that the chip flows because it is created from the work part; and also the clearance angle provides a little clearance between the tool flank and the fresh generated surface.
6. Throughout cutting, the cutting edge of the tool is positioned an exact distance below the first surface. This corresponds to the thickness of the chip before chip formation, too.
7. Because the chip is created on the shear plane, its thickness will increase to tc.
8. The magnitude relation of two to tic is named the chip thickness ratio (or merely the chip ratio). Since the chip thickness once cutting is usually larger than the corresponding thickness before cutting, the chip magnitude relation can forever be not up to one.
9. Additionally to to, the orthogonal cut incorporates a breadth dimension w, even supposing this dimension doesn't contribute abundant to the analysis in orthogonal cutting.
10. The geometry of the orthogonal cutting model permits us to determine a very important relationship between the chip thickness magnitude relation, the rake angle, and also the shear angle.
Q10) what is oblique cutting?
A10)
Cuttings device geometry is simplified from the 3-D (oblique) geometry to a 2-D (orthogonal) geometry.
Chip Formation: Simplified Orthogonal Machining’s in-aircraft version of the slicing procedure
Assumptions Work-piece: a flat plate Cutting device: geometry is given through the lower back rake angles
(a) Only Shear: in a single singles aircraft, that's doing f levels with the path of speed. Chip is fashioned through shearing.
High shear pressure over a slim region big pressure and excessive pressure price plastic deformation because of radial compression.
The compressions area travels beforehand of the device.
Elastic to plastic deformations whilst yield pressure is exceeded.
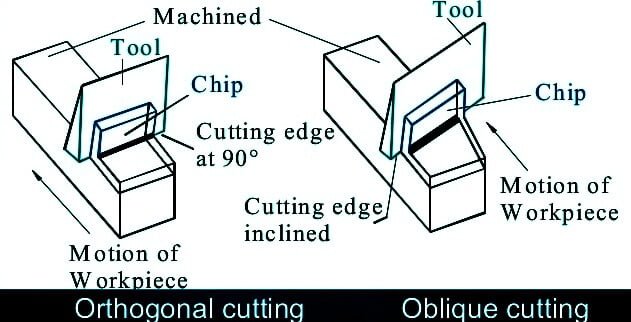
Fig: Orthogonal and oblique cutting
Q11) Explain Mechanics of metal cutting?
A11)
- Metal cutting is a process in which a wedge-shaped cutting tool is used that engages the work piece to remove a layer of material in the form of chips.
- Metal cutting is a process of extensive plastic deformation to form a chip that is removed afterward. The basic mechanism of chip formation is same for all machining operations. By assuming the cutting action to be continuous, we can develop continuous model of cutting process.
- To perform the operation, relative motion is required between the tool and work. This relative motion is achieved in most of the machining operations by means of a primary motion, called cutting speed, and a secondary motion, called feed.
- The shape of the tool and tool penetration into the work surface, combined with these motions, produces the desired geometry of the resulting work piece surface.
- Metal reducing operation is illustrated in Fig.1. The paintings piece is securely clamped in a gadget device vice or clamps or chuck or collet.
- A wedge form device is ready to a sure intensity of reduce and is pressured to transport in path as proven in figure.
All conventional machining strategies require a reducing device having a simple wedge form on the reducing area. The device will reduce or shear off the steel, supplied
(i) The device is more difficult than the steel,
(ii) The device is nicely fashioned in order that its area may be powerful in reducing the steel,
(iii) The device is robust sufficient to withstand reducing pressures however eager sufficient to sever the steel, and
(iv) Supplied there's motion of device relative to the fabric or vice versa, which will make reducing motion possible.
Most steel reducing is accomplished with the aid of using excessive pace metallic equipment or carbide equipment. In steel reducing, the device does now no longer slide thru steel as a jack knife does thru wood, now no longer does the device break up the steel as an awl does a log.
Actually, the steel is pressured off the work piece with the aid of using being compressed, shearing off, and sliding alongside the face of the reducing device. The manner a reducing device cuts the steel may be defined as follows. All metals with inside the strong country have a function crystalline shape, often known as grain shape.
The grain or crystals range in length from very great to very coarse, relying upon the kind of steel and its heat-treatment.
The reducing device advances once more with inside the paintings piece. Heavy forces are exerted at the crystals in the front of the device face.
These crystals, in flip exert comparable pressures on crystals in advance of them, with inside the path of the reduce or pressure carried out with the aid of using the cutter. As the device keeps to advance, the fabric at sheared factor is sheared with the aid of using the reducing fringe of the device or it can be torn unfastened with the aid of using the motion of the bending chip that's being formed.
As the device advances, most pressure is exerted alongside sheared line, that's known as the shear aircraft. This aircraft is about perpendicular to the reducing face of the device.
There exists a shear region on each aspects of the shear aircraft, whilst the pressure of the device exceeds the energy of the fabric on the shear aircraft, rupture or slippage of the crystalline grain shape occurs, accordingly forming the steel chip.
The chip receives separated from the work piece fabric and movements up alongside the device face. In addition, whilst the steel is sheared, the crystals are elongated, the path of elongation being specific from that of shear.
Q12) Explain Merchants circle.
A12)
Merchant represented various cutting forces and their components in a circle which is known a Merchant’s Circle Diagram. For establishing the relationship between measurable and actual forces Merchant’s circle diagram is used.
Merchant circle diagram is used to analyze the forces that are acting in metal cutting.
In the analysis of three forces system, which balance each other for cutting to occur.
Each system represents a triangle of forces.
α = Back rake angle.
φ = Share angle.
ƞ = Angle of friction
Merchant’s method for orthogonal cutting is based on the assumptions that shear plane angle following assumptions are made
- Orthogonal cutting process with single point cutting tool is to be considered.
- The chip is considered to be in equilibrium under action of two equal and opposite collinear forces.
- The stress is maximum at the shear plane and it remains constant.
- The shearing takes place in a direction in which the energy required for shearing is minimum.
- The cutting tool has sharp cutting edge.
- The cutting velocity remains constant.
- There is no sideway flow of chip.
- There is no inertial force on chip.
- The work material is perfectly rigid and perfectly plastic
The three triangles of forces in merchant’s circle diagram are listed below:
A triangle of forces for the cutting forces,
- A triangle of forces for the shear forces,
- A triangle of forces for the frictional forces.
- From the figure following relations were obtained:
- Proper use of Merchant’s Circle Diagram enables the followings:
- Easy, reasonably accurate and quick determination of several other forces from a few known forces involved in machining.
- Friction at chip tool interface and dynamic yield shear strength can be determined.
- Equations relating the different forces in machining are easily developed.
Some limitations of use of Merchant’s Circle Diagram:
- Merchant’s circle diagram (MCD) is only valid for orthogonal cutting process.
- By the ratio, F/N, the Merchant’s Circle Diagram gives apparent coefficient of friction.
- It is based on single shear plane theory.
Q13) Explain terminologies in Merchant circle.
A13)
Shear Plane
The work piece material deforms plastically ahead of the cutting tool edge. It slides on the rake face of the tool and forms a chip. The region between the start of the chip formation and the unreformed (elastically deformed) work piece is called the zone of plastic deformation.
The size of the zone of plastic deformation depends on cutting parameters. The size of this plastic deformation zone decreases with the increase of cutting speed. In the analysis of thin zones, it is always assumed that the work material shears across a plane, and forms the chip. This plane is called the shear plane.
Shear Plane Angle
A shear plane angle is an angle between the cutting velocity vector, and the shear plane. The chip is formed by plastic deformation of work material, and the material flow is continuous.
Discontinuous chip: Once comparatively brittle materials (e.g., solid irons) are machined at low cutting speeds, the chips typically kind into separate segments (sometimes the segments are loosely attached). This tends to impart irregular texture to the machined surface. High tool–chip friction and enormous feed and depth of cut promote the formation of this chip kind.
Continuous chip: Once ductile work materials are cut at high speeds and comparatively little feeds and depths, long continuous chips are fashioned. An honest surface finish usually results once this chip kind is created. a pointy cutting edge on the tool and low tool–chip friction encourage the formation of continuous chips. Long, continuous chips (as in turning) will cause issues with respect to chip disposal and/or tangling regarding the tool. To resolve these issues, turning tools are typically equipped with chip breakers.
Serrated chips: These chips are semi-continuous within the sense that they possess a saw-tooth look that's made by a rotary chip formation of alternating high shear strain followed by low shear strain. This fourth form of chip is most closely related to sure difficult-to-machine metals admire metal alloys, nickel-base super alloys, and primary solid solution unstained steels after they are machined at higher cutting speeds. However, the development is additionally found with additional common work metals (e.g., steels) after they are cut at high speeds.
Q14) Derive an expression for Cutting Speed.
A14)
F.W. Taylor has conducted numerous experiments in the field of metal cutting. In 1907, he gave the following relationship between tool life and cutting speed, which is known as Taylor’s Tool Life Equation.
VCTn = C
Where, V= Cutting speed (m/min)
T= Tool life (min) C = Constant or machining constant
n = Tool life index. It depends on tool and work material combination and cutting conditions.
If T = 1 min
Then C = Vc
So, the constant C can be interpreted physically as the cutting speed for which the tool life is equal to one min. The tool life equation can be represented on log-log paper; it becomes straight line
Q15) How can we calculate tool life?
A15)
Every device or tool has its functional and expected life of work. At the expiry of which it may still be operational, but not efficiently. During it usage, the tool losses its material, i.e., it gets worn out. As the wearing of tool increases, the tool starts to lose its efficiency. Therefore, its life has to be defined and on the expiry of its life, it should be reground for fresh use.
The tool life can be defined as:
(i) The time elapsed between two successive grindings.
(ii) The period during which a tool cuts satisfactorily.
(iii) The total time duration accumulated before tool failure occurs.
Tool life is expressed in minutes.
The relation between cutting speed and tool life can be obtained by the Taylor’s tool life equation:
VTn = C
Methods for Tool Life Measurements:
The most commonly used methods for tool life measurements are:
- Machining Time:
- Elapsed time of operation of machine tool.
- Actual Cutting Time:
- The time during which the tool actually cuts.
- A fixed size of Wear Land on Flank Surface:
- On carbide and ceramic tools where crater wear is negligible, tool life can be taken as corresponding to 0.038 or 0.076 mm of wear land on the flank surface for finishing respectively.
- Volume of metal removed.
- Number of pieces machined.
The tool life between replacement and re-conditioning can be defined in a number of ways, as:
(a) Actual cutting time taken to failure.
(b) Volume of metal removed to failure.
(c) Number of parts produced to failure.
(d) Cutting speed for a time to failure.
(e) Length of work machined to failure.
- Tool Life Expectancy (Taylor’s Tool Life Equation):
- In 1907, F. W. Taylor developed the relation between tool life, cutting speed and temperature keeping feed as constant. The Taylor’s Equation for Tool Life Expectancy provides good approximation.
- VCTn = C
- A more general form of the equation considering depth of cut and feed rate is given as
- VcTnDxFy = C
- Where, KC = Cutting speed (m/min)
- T = Tool life (min)
- D = Depth of cut (mm)
- F = Feed rate (mm/rev)
- x, y = Exponents, that are determined experimentally for each cutting conditions.
- n = Exponent, that depends on tool materials.
- Value of n = 0.1 - 0.2; for H.S.S. Tools
- 0.2 -0.4; for Carbide tools
- 0.4 - 0.6; for Ceramic tools
C = Machining constant, computed by experimentation or published data-book. It depends on properties of tool material, work piece and feed rate.
Q16) What is the criteria for tool life calculation?
A16)
- Due to wear on the tool, the cutting force increases and surface finish deteriorates. Therefore, when should we say that a tool has failed and it should be reground? In other words, certain criterion is required for judging the tool failure.
- A tool fails when it no longer performs its function properly. This may have different meaning under different circumstances. In a roughing operation, where, surface finish and dimensional accuracy are of little importance, a tool failure can mean an excessive rise in cutting forces and power requirements.
- In a finishing operation, where, surface finish and dimensional accuracy are prime important, a tool failure will mean that the specified conditions of surface finish and dimensional accuracy can no longer be achieved. All of these failures are basically related to the wear on the clearance face of the tool.
The following are some criterion for judging tool life/failure:
(i) Complete failure.
(ii) Flank or crater failure.
(iii) Finish failure.
(iv) Size failure.
(v) Cutting force failure.
(i) Complete Failure:
- According to this criterion, the cutting with the tool is continued till it is able to cut. So when the tool fails to cut, then only it should be reground. This criterion is not used in practice because of its obvious disadvantages.
(ii) Flank or Crater Failure:
- According to this criterion, when the wear on the flank reaches a certain height the cutting with the tool is discontinued and grinding is done. Say when the flank wear height h equals to 0.3 mm, for example, the tool is said to have failed. Some common recommended values of wear land are given in Table (a, b).
- Due to wear on the flank, the actual depth of cut decreases from AC to BC as shown in Fig. The work piece becomes taper if cutting continued. This is the most usual criterion followed in practice. The flank wear is measured with a tool maker’s microscope.
- Also, it is important to note that, the flank wear is not uniform along the active cutting edge, therefore, it is necessary to specify the locations and the degree of wear, when deciding tool life criterion, before regrinding.
(iii) Finish Failure:
- According to this criterion, when the surface roughness reaches a specified high value, the cutting with the tool is stopped and grinding is done. Say at a particular cutting condition the surface roughness, comes to be 0.7 microns. As in process of cutting the flank wear develops so the cutting edge becomes rough and irregular so the surface roughness gradually increases, as shown in Fig. Say 1.3 microns, for example, are kept as a criterion.
- The roughness of the surface is measured continuously along its length. When the roughness reaches the specified value, the cutting is discontinued. For example, this maximum specified value of surface roughness may be occurs on the 10th work piece, so the 11th and next work pieces won’t be machined with the same tool, without regrinding.
- This criterion becomes especially important when close fitting objects are machined. Due to rough and uneven surfaces, the proper fitting may not be done.
(iv) Size Failure:
- According to this criterion, a tool will be considered to have failed if there is a deviation in the size of a produced finished component from its specified value.
(v) Cutting Force Failure:
- According to this criterion, a tool will be considered to have failed, if the amount of cutting force increases by certain specified amount. This is due to flank wear. Flank wear increases the area of contact between the work piece and the tool, resulting into increase in the cutting force. Fig. Shows that an increase in cutting force with development to flank wear.
Q17) What are the important factors related to tool life?
A17)
The following factors play an important role in tool life:
(i) Cutting speed.
(ii) Feed rate and Depth of cut.
(iii) Hardness of work piece.
(iv) Microstructure of work piece.
(v) Tool material.
(vi) Tool geometry.
(vii) Type of cutting fluid and its method of application.
(viii) Nature of cutting.
(ix) Grain size of work piece.
(x) Rigidity of work piece machine-tool system.
Q18) What are the machining parameters.
A18)
When planning a successful metal cutting operation, selecting the right cutting tool material and grade is critical.
When choosing the right choice, it's necessary to have a fundamental understanding of each cutting tool's material and performance. The work piece material to be machined, the component type and shape, the machining circumstances, and the level of surface quality required for each operation are all factors to consider.
This section explains the different types of cutting tools, their benefits, and how to use them properly.
Cutting tool materials come in a variety of hardness, toughness, and wear resistance combinations, and are classified into a number of grades with various qualities. In general, a cutting tool material that is effective in its use should be:
• Tough, to resist wear and distortion on the flanks
• Tough enough to withstand mass breakage
• Non-reactive with the material of the work piece
• Chemically stable, so it won't oxidase or diffuse.
• Resistant to extreme temperature changes
Q19) Write note on CNC machine.
A19)
- CNC stands for computer numeric controlled.
- It refers to any machine tool (i. e. Mill, lathe, drill press, etc.) which uses a computer to electronically control the motion of one or more axes on the machine.
- The development of NC machine tools started from a task supported by the US Air Force in the early 1950s, involving MIT, and several machine-tool manufacturing companies. The need was recognized for machines to be able to manufacture complex jet aircraft parts.
- As computer technology evolved, computers replaced the more inflexible controllers found on the NC machines, hence the dawn of the CNC era.
- CNC machine tools use software programs to provide the instructions necessary to control the axis motions, spindle speeds, tool changes, and so on.
- CNC machine tools allow multiple axes of motion simultaneously, resulting in 2D, and 3D contouring ability.
- CNC technology also increases productivity, and quality control by allowing multiple parts to be produced using the same program, and tooling.
Q20) Explain Operations in CNC programming.
A20)
The following cycles are typical of the machining operations available when programming a 3-axis CNC milling machine.
Position. Used to move the XYZ coordinates at rapid federate.
Drill one. Used to position the tool at a specific XYZ coordinate position to automatically drill a hole. The automatic drill cycles allow for simple drilling, peck drilling, spot-facing, and bore cycles.
Drill pattern. Used to define polar or rectangular whole arrays for automatic drilling.
Line. Used to cut straight lines along an axis or a diagonal at the desired feed rate.
Arc. Used to cut a circle or partial circle that is part of a series of cuts that usually includes lines as well.
Face. Used to define a rectangular zigzag pattern used to clean off a part surface.
Pocket. Used to clear the material out of a rectangle, circle, or polygon.
Frame. Used to cut the inside or outside outline of a rectangle, circle, or polygon.
Tool. Used to enter tool parameters, machine function parameters, and program pause/stop codes.
Scale/mirror. Used to scale, and/or mirror other part features.
Rotate. Used to repeat other part features around a specific center of rotation.