Unit - 4
Cast Iron
Q1) What is cast iron?
A1)
Cast Iron
- Cast irons are a type of ferrous alloy with a carbon concentration greater than 2.14 weight percent; however, most cast irons possess between 3.0 and 4.5 weight percent C, as well as other alloying elements.
- A closer look at the iron–iron carbide phase diagram reveals that alloys in this composition range become entirely liquid at temperatures between 1150 and 1300C (2100 and 2350F), which is significantly lower than steel temperatures. As a result, they are easily melted and castable.
- Furthermore, some cast irons are extremely fragile, and casting is the most practical method of manufacturing.
- As a result, the actual equilibrium diagram for iron and carbon is displayed in Figure b rather than Figure a.
- On the iron-rich side, the two diagrams are nearly identical (eutectic and eutectoid temperatures for the Fe–Fe3C system are 1147 and 727C, respectively, compared to 1153 and 740C for Fe–C); however, Figure b extends to 100 wt% C, making graphite the carbon-rich phase rather than cementite at 6.7 wt% C.
- The composition and pace of cooling control the tendency to generate graphite. The inclusion of silicon in amounts larger than around 1 wt% promotes graphite production.
- In addition, graphitization is favoured by slower cooling rates during solidification (the formation of graphite). Carbon exists as graphite in most cast irons, and both microstructure and mechanical behaviour are affected by composition and heat treatment. Gray, nodular, white, malleable, and compacted graphite are the most frequent cast iron varieties.
Cast iron is a ferrous alloy containing high levels of carbon, generally greater than 2%. The carbon present in the cast iron can take the form of graphite or carbide. Cast irons have a low melting temperature which makes them well suited to casting.
Q2) Classify cast iron in detail.
A2)
Classification of cast iron
The cast iron is classified into seven major kinds as follows:
1) Grey cast iron
2) White cast iron
3) Mottled cast iron
4) Malleable cast iron
5) Nodular cast and ductile cast iron
6) Machanite cast iron
Gray Cast Iron
Gray cast iron is the most common type. The carbon is in the form of graphite flakes. Gray cast iron is a brittle material, and its compressive strength is much higher than its tensile strength. The fracture surface of gray cast iron has a gray color, which is how it got its name.
Ductile Cast Iron (Nodular Cast Iron)
The addition of magnesium to gray cast iron improves the ductility of the material. The resulting material is called nodular cast iron because the magnesium causes the graphite flakes to form into spherical nodules. It is also called ductile cast iron. Nodular cast iron has good strength, ductility, and machinability. Common uses include crankshafts, gears, pump bodies, valves, and machine parts.
White Cast Iron
White cast iron has carbon in the form of carbide, which makes the material hard, brittle, and difficult to machine. White cast iron is primarily used for wear-resisting components as well as for the production of malleable cast iron.
Malleable Cast Iron
Malleable cast iron is produced by heat treating white cast iron. The heat treatment improves the ductility of the material while maintaining its high strength.
Q3) Define white cast Iron.
A3)
- White cast irons are used in abrasion-resistant parts where its brittleness is of minimum concern such as shell liners, slurry pumps, ball mills, lifter bars, extrusion nozzles, cement mixers, pipe fittings, flanges, crushers and pump impellers.
- A popular grade of white iron is high chrome white irons, ASTM A532. This contains nickel and chromium for good low-impact abrasion applications.
Q4) Explain Gray Cast Iron.
A4)
- Gray cast irons have carbon and silicon concentrations of 2.5 to 4.0 wt percent and 1.0 to 3.0 wt percent, respectively.
- The graphite in most of these cast irons is in the form of flakes (like corn flakes), which are usually surrounded by an x-ferrite or pearlite matrix; this is the microstructure of a typical grey iron. A shattered surface takes on a grey look as a result of the graphite flakes, hence the name.
- Because of its microstructure, grey iron is comparatively weak and brittle in tension; the tips of the graphite flakes are sharp and pointed and may act as stress concentration locations when an external tensile load is applied. Under compressive loads, strength and ductility are substantially higher.
- Gray irons have several useful properties and are widely used. When comparing the respective damping capacities of steel and grey iron, they are quite effective in damping vibrational energy.
- This material is widely used to build the base constructions of machinery and heavy equipment that are subjected to vibrations. In addition, grey irons have a good wear resistance. Furthermore, they have a high fluidity at casting temperature in the molten state, allowing for the casting of intricately shaped objects, as well as reduced casting shrinkage. Finally, and perhaps most importantly, grey cast iron is one of the most affordable metals available.
Q5) What is Nodular Cast Iron?
A5)
- Before casting, a small quantity of magnesium and/or cerium is added to the grey iron, resulting in a specific microstructure and set of mechanical properties. Graphite still exists, albeit in the shape of nodules or spherelike particles rather than flakes.
- The resulting alloy has a characteristic microstructure and is known as ductile or nodular iron. Depending on the heat treatment, the matrix phase enclosing these particles is either pearlite or ferrite; for an as cast piece, the matrix phase is usually pearlite. However, a heat treatment at around 700C (1300F) for several hours will result in a ferrite matrix, as seen in this photomicrograph. Castings are substantially more ductile and stronger than grey iron.
Q6) Explain Malleable Cast Iron.
A6)
- Most of the carbon in low silicon cast irons (less than 1.0 wt percent Si) and quick cooling rates resides as cementite rather than graphite. Because the fracture surface of this alloy is white, it is known as white cast iron. Thick portions may only have a thin layer of white iron on the top that was "chilled" during the casting process; grey iron forms in the inside, which cools more slowly.
- White iron is highly hard but also extremely brittle, to the point of being essentially unmachinable, due to large concentrations of the cementite phase. Its applications are limited to those that require a highly hard and wear-resistant surface without a significant degree of ductility, such as rollers in rolling mills. White iron is typically utilised as a step between the manufacture of malleable iron and another type of cast iron.
- Heating white iron for a long time at temperatures between 800 and 900 degrees Celsius (1470- and 1650-degrees Fahrenheit) in a neutral atmosphere (to prevent oxidation) causes the cementite to decompose, forming graphite in the form of clusters or rosettes surrounded by a ferrite or pearlite matrix, depending on the cooling rate.
Q7) Explain chilled iron?
A7)
Chilled iron
- Chilled solid iron When a localized region of grey solid iron is cooled very swiftly from the melt, solid iron is fashioned on the region that has been cooled.
- This form of white solid iron is known as chilled solid iron. A chilled iron casting may be produced via way of means of adjusting the carbon composition of the white solid iron, in order that the regular cooling charge on the floor is simply speedy sufficient to supply white solid iron, while the slower cooling charge beneath the floor will produce grey iron.
- The intensity of kick back decreases, and the hardness of the chilled sector will increase with growing carbon content. Chromium in small quantities is frequently used to govern kick back intensity, due to the formation of chromium carbides.
- Chromium is utilized in quantity of 1%–4% in chilled iron to growth hardness and enhance abrasion resistance. It additionally stabilizes carbide and suppresses the formation of graphite in heavy sections. When introduced in quantities of 12%–35%, chromium will impart resistance to corrosion and oxidation at increased temperatures.
Q8) What is alloy cast iron?
A8)
Alloy Cast Iron
- Forged iron, an alloy of iron that incorporates 2 to four percentage carbon, at the side of various quantities of silicon and manganese and lines of impurities along with sulfur and phosphorus. It is made via way of means of decreasing iron ore in a blast furnace.
- The liquid iron is forged, or poured and hardened, into crude ingots known as pigs, and the pigs are in the end remelted at the side of scrap and alloying factors in cupola furnaces and recast into molds for generating a lot of products. The Chinese produced forged iron as early because the sixth century BC, and it changed into produced sporadically in Europe via way of means of the 14th century.
- It changed into added into England approximately 1500; the primary ironworks in America have been mounted at the James River, Virginia, in 1619. During the 18th and nineteenth centuries, forged iron changed into a inexpensive engineering fabric than wrought iron as it did now no longer require in depth refining and running with hammers, however it changed into greater brittle and inferior in tensile power.
- Nevertheless, its load-bearing power made it the primary critical structural metal, and it changed into utilized in a number of the earliest skyscrapers. In the twentieth century, metal changed forged iron in construction, however forged iron keeps to have many commercial applications.
Q9) What is production route?
A9)
- Irregular eutectic systems shape while one of the levels facets. Most metal/nonmetal combinations, consisting of the industrially vital aluminum–silicon casting alloys and grey forged iron, shape abnormal systems consisting of the flake structure (vicinity D, Fig. 1). Growth anisotropy of the faceting section as opposed to warmth glide determines the neighborhood boom route.
- Also the presence of a side on the interface restricts its cappotential to house extrade easily main as a substitute to overgrowth and finally catastrophic breakdown. These traits imply that boom happens in a nonsteady-country way at a nonisothermal interface with a geometry of the shape proven in Fig. 2(e).
- Flakes develop at distinctive angles to the warmth glide route in advance of the nonfaceting section. Some develop toward every different till one is eliminated. This will increase the common spacing till it's far viable to create a brand new flake, for example, with the aid of using branching.
- The common spacing will rely upon the convenience with which new flakes can shape. This mode of solidification results in large measured undercoolings and spacings which do now no longer correspond to the extremum situation of the boom curve.
- The common spacing decreases as v and G increase. Any theoretical version should account for the elevated trouble of diffusion on the interface and for the extrade in temperature on the interface. Models superior thus far do now no longer offer a nice answer. For example, Magnin and Kurz (1987) taken into consideration the nonisothermal interface however used a aircraft the front diffusion answer and a spacing criterion associated with the intensity of a hole produced at the minor section.
- Subsequently, Magnin et al. (1991) equipped experimental undercooling and spacing measurements to the relationships for the extremum situation of ordinary lamellar boom in Sect. 2, with the common spacing given with the aid of using ϕλext. Their measurements counseled that ϕ is 3·2 for aluminum–silicon and 5·four for grey forged iron. No criterion for ϕ become counseled.
Q10) What is microstructure and applications
A10)
- The microstructure of a cloth consists of various stages of variable form, length and distribution (grains, precipitates, dendrites, spherulites, lamellae, pores, etc.).
- The stages are outstanding from every different with the aid of using their numerous crystalline, semi-crystalline or amorphous systems whilst discovered with an optical or electron microscope. The engineer can gain a huge variety of houses with the aid of using managed microstructural adjustments produced at some point of processing. To have a clean information of the cloth behaviour, it's miles had to set up relationships among the macroscopic houses and phenomena going on at the microstructural scale.
- The microstructures fashioned in substances rely now no longer handiest at the chemical composition and shape however additionally at the atomic mobility and at the presence of attention gradients at some point of processing. Microstructure formation is likewise strongly prompted with the aid of using the quantity of power required to create new interfaces. Appropriate warmness-remedies (quenching, annealing) produce a incredible sort of microstructures.
- Frequently, those have an inhomogeneous composition and are nearly usually metastable on the provider temperature. In the case of metals and alloys, warmness-remedies mixed with mechanical approaches inclusive of rolling have reached a totally excessive stage of class with a purpose to manipulate the microstructure.
- The majority of solidification microstructures are crystalline. However, a small range of substances having an abnormal molecular shape are not able to crystallise, regardless of the warmness remedies. These substances have a glassy shape withinside the stable state.
- It is the case of heterotactic vinyl polymers. Glass is usually much less solid than crystal whilst it exists and owes its transparency to a loss of microstructure.
- The microstructure of natural polymers is in general managed with the aid of using their chemical architecture. Macromolecules with a normal molecular shape are in wellknown capable of crystallise. However, crystallisation of polymer substances is by no means entire and, withinside the bulk, handiest semi-crystalline spherulites are fashioned.
Q11) Explain Effects of various parameters on structure and properties of Cast Iron.
A11)
- Wind electricity is a renewable, predictable, and smooth supply of electricity. Substantial potential may be constructed up quickly, presenting the electricity independence demanded with the aid of using the world’s biggest and fastest-developing economies.
- The majority of wind turbine elements are produced from the difficult ductile iron grade EN-GJS-400-18-LT; examples of DI castings for windmill. Therefore, interest is given for this grade of iron.
- The manufacturing of heavy phase ductile iron castings, however, nevertheless faces actual difficulties, represented withinside the formation of degenerated graphite morphologies withinside the ductile iron microstructures, which significantly reduces the effect in addition to fatigue residences.
- The necessities for excessive electricity and excessive effect residences in DI at low temperatures for a few packages as windmill are very strict. The European Standard EN-GJS-400-18U-LT usually called GGG 40.three is an example. This preferred now no longer simplest has the regular mechanical necessities for ferritic iron however additionally specifies V-notched Charpy effect necessities of 12 J at −20°C and minimal elongation of 18% .
- In order to gain those mechanical residences, the microstructure need to be properly managed in phrases of nodularity, nodule remember, and matrix stages. This is due to the fact excessive nodule remember impairs effect electricity and occasional nodule remember effects in intercellular brittle stages which can be negative to electricity and ductility.
- A minimal nodularity of 95% is critical; poorly formed nodules act as pressure riser and as initiation web website online for fracture beneathneath effect. Also, a matrix that is absolutely ferritic and freed from mobileular boundary stages is crucial to fulfill the mechanical residences of windmill castings
Q12) What is Alloy cast Iron such as Ni-resist?
A12)
- The term ‘forged iron’ covers a own circle of relatives of ferrous alloys. It is an iron alloy that carries greater than 2 carbon, and silicon withinside the variety 1 to 3%.
- The quantity of alloying and related manage of the warmth and cooling procedure can deliver a completely huge sort of houses to distinct grades of forged iron. Cast iron is used withinside the oil and fueloline enterprise for making water conduit pipes, packer parts, boilers, valve bodies, and valve parts.
- It is classed in step with the microstructure, which relies upon at the carbon content, the alloy and impurity content, the cooling charge at some stage in and after freezing, and warmth remedy after casting. The composition of forged iron varies significantly, relying upon the grade of pig iron, scrap used however it carries carbon withinside the variety of approximately 2–4% via way of means of weight.
- The carbon equal of a forged iron additionally enables to differentiate the grey irons, which cool right into a microstructure containing graphite, from the white irons wherein the carbon is gift particularly as cementite. Casting layout engineers need to catch up on the shrinkage of forged iron.
Q13) What is Ni-hard?
A13)
- The welding of solid irons has been notoriously referred to as a 'black-art'. Individual castings of equal kinds can range in reaction to welding, and so do the information of technique taken into consideration essential via way of means of skilled practitioners.
- Most castings are produced to internet shape, so welding is typically for restore and upkeep instead of fabrication. Structural load-bearing use is usually compressive, now no longer seriously tensile.
- The most common varieties of solid iron have round 3 and 2%Si. Flake graphite gray iron varies in pleasant and impurity content, with fairly low energy and ductility. Spheroidal graphite (SG), nodular or ductile iron is dealt with with magnesium, has fewer impurities, advanced mechanical properties, and greater dependable weldability.
- Electrodes primarily based totally on natural nickel and nickel-iron alloys are maximum extensively used. Electrode flux coverings are of simple kind plus graphite to present a weld deposit deoxidised and saturated with carbon. This mimics a number of the traits of solid iron however is non-hardenable and effortlessly machined. Recommended welding strategies are given on applicable facts sheets.
- Another group, excessive alloy austenitic irons (Ni-Resist kinds) also are produced in flake and SG grades. Electrodes of the NiFe kind are used due to the fact matching weld steel is simply too hard. Preheat of 300-350°C is needed for the flake graphite grades, however for the SG grades buttering at low temperatures is favored to keep away from HAZ warm cracking. Martensitic solid iron (Ni-Hard kinds) and the numerous white irons are commonly taken into consideration too crack-touchy or brittle to be welded satisfactorily.
Q14) What is Non-Ferrous Alloys?
A14)
- Non-ferrous metals have a tendency to be extra steeply-priced than ferrous metals however are used for his or her suitable homes, which include mild weight (aluminium), excessive conductivity (copper), non magnetic homes or resistance to corrosion (zinc). Some non-ferrous substances are used withinside the iron and metallic industries, together with bauxite, that's used for flux in blast furnaces.
- Other non-ferrous metals, which include chromite, pyrolusite and wolframite, are used to make ferrous alloys. However, many non-ferrous metals have low melting points, making them much less appropriate for packages at excessive temperatures.
- There are a huge quantity of non-ferrous substances, masking each metallic and alloy that doesn't include iron. Non-ferrous metals encompass aluminium, copper, lead, nickel, tin, titanium and zinc, in addition to copper alloys like brass and bronze.
- Other uncommon or valuable non-ferrous metals encompass gold, silver and platinum, cobalt, mercury, tungsten, beryllium, bismuth, cerium, cadmium, niobium, indium, gallium, germanium, lithium, selenium, tantalum, tellurium, vanadium, and zirconium.
- Non-ferrous metals are typically acquired from minerals like carbonates, silicates and sulphides earlier than being subtle thru electrolysis. The distinction among ferrous and non-ferrous metals is that ferrous metals include iron.
- Ferrous metals, together with forged irons or carbon metallic, have a excessive carbon content, which usually makes them liable to rust while uncovered to moisture. However, this isn't always the case for wrought iron, which resists rust because of its purity, and stainless metallic, that's included from corrosion through the presence of chromium.
Q15) Explain Study of non-ferrous alloys such as brasses (Cu-Zn diagram), Bronzes (Cu-Sn diagram).
A15)
- The essential nonferrous alloys in refinery and herbal fueloline processing gadget are the copper-primarily based totally and copper–nickel alloys. However, the usage of copper-primarily based totally alloys in ammonia (NH3) or ammonium salt (NH4+) environments need to be avoided—there may be a excessive capability for corrosion/destruction of the alloy structure.
- Aluminum brass, containing 2% w/w aluminum, has been discovered to be quite extra proof against erosion in saltwater. Inhibition with arsenic is essential to save you de-zincification, as withinside the case of admiralty brass.
- The more potent naval brass is frequently decided on because the tube sheet fabric while admiralty brass (wherein a small quantity of tin improves resistance to seawater) tubes are utilized in condensers. Generally, bronze is a tin alloy of copper, despite the fact that the time period has been broadly used for different alloys, along with a few brass alloys. Cast brass or bronze alloys for valves and fittings are normally copper–tin–zinc compositions, plus lead for machinability.
- Aluminum bronzes are frequently used as tube sheet and channel fabric for exchangers with admiralty brass or titanium tubes uncovered to cooling water. The 70/30 copper–nickel alloy is used for exchanger tubes while higher saltwater corrosion resistance than in aluminum brass is needed, or while excessive steel temperatures in water-cooled exchangers might also additionally reason de-zincification in brass.
- Monel is a nickel–copper alloy with 67% w/w nickel and 30% w/w copper, which has superb resistance to saltwater and, below nonoxidizing conditions, to acids together with hydrochloric acid and hydrofluoric acid. Monel has a higher excessive-temperature resistance to cooling water than 70/30 copper–nickel.
- In fact, Monel cladding and Monel trays are usually exact on the pinnacle of crude towers to withstand corrosion with the aid of using hydrogen chloride vapor and in which the temperature is beneathneath 205°C (400°F). At temperatures in extra of 205°C (400°F), nickel-primarily based totally alloys are attacked with the aid of using hydrogen sulfide.
- For excessive-temperature power and/or corrosion resistance, numerous nickel-primarily based totally alloys are used for unique applications, together with enlargement bellows in fluid catalytic cracking procedure units (Alloy 625), stems in flue fueloline butterfly valves (Alloy X 750), and is derived uncovered to excessive-temperature corrosive gases and liquids (Alloy X).
- Titanium has superb resistance to seawater, and it's also used for tubing in crude tower overhead condensers.
Cu-Zn diagram
![Equilibrium Cu-Zn phase diagram [5] | Download Scientific Diagram](https://glossaread-contain.s3.ap-south-1.amazonaws.com/epub/1650446414_9592533.jpeg)
Fig: Cu-Zn diagram
Bronzes (Cu-Sn diagram)
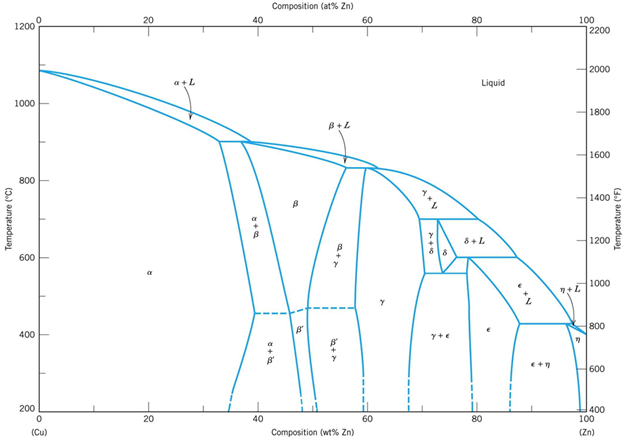
Fig: Bronzes (Cu-Sn diagram)
Unit - 4
Cast Iron
Q1) What is cast iron?
A1)
Cast Iron
- Cast irons are a type of ferrous alloy with a carbon concentration greater than 2.14 weight percent; however, most cast irons possess between 3.0 and 4.5 weight percent C, as well as other alloying elements.
- A closer look at the iron–iron carbide phase diagram reveals that alloys in this composition range become entirely liquid at temperatures between 1150 and 1300C (2100 and 2350F), which is significantly lower than steel temperatures. As a result, they are easily melted and castable.
- Furthermore, some cast irons are extremely fragile, and casting is the most practical method of manufacturing.
- As a result, the actual equilibrium diagram for iron and carbon is displayed in Figure b rather than Figure a.
- On the iron-rich side, the two diagrams are nearly identical (eutectic and eutectoid temperatures for the Fe–Fe3C system are 1147 and 727C, respectively, compared to 1153 and 740C for Fe–C); however, Figure b extends to 100 wt% C, making graphite the carbon-rich phase rather than cementite at 6.7 wt% C.
- The composition and pace of cooling control the tendency to generate graphite. The inclusion of silicon in amounts larger than around 1 wt% promotes graphite production.
- In addition, graphitization is favoured by slower cooling rates during solidification (the formation of graphite). Carbon exists as graphite in most cast irons, and both microstructure and mechanical behaviour are affected by composition and heat treatment. Gray, nodular, white, malleable, and compacted graphite are the most frequent cast iron varieties.
Cast iron is a ferrous alloy containing high levels of carbon, generally greater than 2%. The carbon present in the cast iron can take the form of graphite or carbide. Cast irons have a low melting temperature which makes them well suited to casting.
Q2) Classify cast iron in detail.
A2)
Classification of cast iron
The cast iron is classified into seven major kinds as follows:
1) Grey cast iron
2) White cast iron
3) Mottled cast iron
4) Malleable cast iron
5) Nodular cast and ductile cast iron
6) Machanite cast iron
Gray Cast Iron
Gray cast iron is the most common type. The carbon is in the form of graphite flakes. Gray cast iron is a brittle material, and its compressive strength is much higher than its tensile strength. The fracture surface of gray cast iron has a gray color, which is how it got its name.
Ductile Cast Iron (Nodular Cast Iron)
The addition of magnesium to gray cast iron improves the ductility of the material. The resulting material is called nodular cast iron because the magnesium causes the graphite flakes to form into spherical nodules. It is also called ductile cast iron. Nodular cast iron has good strength, ductility, and machinability. Common uses include crankshafts, gears, pump bodies, valves, and machine parts.
White Cast Iron
White cast iron has carbon in the form of carbide, which makes the material hard, brittle, and difficult to machine. White cast iron is primarily used for wear-resisting components as well as for the production of malleable cast iron.
Malleable Cast Iron
Malleable cast iron is produced by heat treating white cast iron. The heat treatment improves the ductility of the material while maintaining its high strength.
Q3) Define white cast Iron.
A3)
- White cast irons are used in abrasion-resistant parts where its brittleness is of minimum concern such as shell liners, slurry pumps, ball mills, lifter bars, extrusion nozzles, cement mixers, pipe fittings, flanges, crushers and pump impellers.
- A popular grade of white iron is high chrome white irons, ASTM A532. This contains nickel and chromium for good low-impact abrasion applications.
Q4) Explain Gray Cast Iron.
A4)
- Gray cast irons have carbon and silicon concentrations of 2.5 to 4.0 wt percent and 1.0 to 3.0 wt percent, respectively.
- The graphite in most of these cast irons is in the form of flakes (like corn flakes), which are usually surrounded by an x-ferrite or pearlite matrix; this is the microstructure of a typical grey iron. A shattered surface takes on a grey look as a result of the graphite flakes, hence the name.
- Because of its microstructure, grey iron is comparatively weak and brittle in tension; the tips of the graphite flakes are sharp and pointed and may act as stress concentration locations when an external tensile load is applied. Under compressive loads, strength and ductility are substantially higher.
- Gray irons have several useful properties and are widely used. When comparing the respective damping capacities of steel and grey iron, they are quite effective in damping vibrational energy.
- This material is widely used to build the base constructions of machinery and heavy equipment that are subjected to vibrations. In addition, grey irons have a good wear resistance. Furthermore, they have a high fluidity at casting temperature in the molten state, allowing for the casting of intricately shaped objects, as well as reduced casting shrinkage. Finally, and perhaps most importantly, grey cast iron is one of the most affordable metals available.
Q5) What is Nodular Cast Iron?
A5)
- Before casting, a small quantity of magnesium and/or cerium is added to the grey iron, resulting in a specific microstructure and set of mechanical properties. Graphite still exists, albeit in the shape of nodules or spherelike particles rather than flakes.
- The resulting alloy has a characteristic microstructure and is known as ductile or nodular iron. Depending on the heat treatment, the matrix phase enclosing these particles is either pearlite or ferrite; for an as cast piece, the matrix phase is usually pearlite. However, a heat treatment at around 700C (1300F) for several hours will result in a ferrite matrix, as seen in this photomicrograph. Castings are substantially more ductile and stronger than grey iron.
Q6) Explain Malleable Cast Iron.
A6)
- Most of the carbon in low silicon cast irons (less than 1.0 wt percent Si) and quick cooling rates resides as cementite rather than graphite. Because the fracture surface of this alloy is white, it is known as white cast iron. Thick portions may only have a thin layer of white iron on the top that was "chilled" during the casting process; grey iron forms in the inside, which cools more slowly.
- White iron is highly hard but also extremely brittle, to the point of being essentially unmachinable, due to large concentrations of the cementite phase. Its applications are limited to those that require a highly hard and wear-resistant surface without a significant degree of ductility, such as rollers in rolling mills. White iron is typically utilised as a step between the manufacture of malleable iron and another type of cast iron.
- Heating white iron for a long time at temperatures between 800 and 900 degrees Celsius (1470- and 1650-degrees Fahrenheit) in a neutral atmosphere (to prevent oxidation) causes the cementite to decompose, forming graphite in the form of clusters or rosettes surrounded by a ferrite or pearlite matrix, depending on the cooling rate.
Q7) Explain chilled iron?
A7)
Chilled iron
- Chilled solid iron When a localized region of grey solid iron is cooled very swiftly from the melt, solid iron is fashioned on the region that has been cooled.
- This form of white solid iron is known as chilled solid iron. A chilled iron casting may be produced via way of means of adjusting the carbon composition of the white solid iron, in order that the regular cooling charge on the floor is simply speedy sufficient to supply white solid iron, while the slower cooling charge beneath the floor will produce grey iron.
- The intensity of kick back decreases, and the hardness of the chilled sector will increase with growing carbon content. Chromium in small quantities is frequently used to govern kick back intensity, due to the formation of chromium carbides.
- Chromium is utilized in quantity of 1%–4% in chilled iron to growth hardness and enhance abrasion resistance. It additionally stabilizes carbide and suppresses the formation of graphite in heavy sections. When introduced in quantities of 12%–35%, chromium will impart resistance to corrosion and oxidation at increased temperatures.
Q8) What is alloy cast iron?
A8)
Alloy Cast Iron
- Forged iron, an alloy of iron that incorporates 2 to four percentage carbon, at the side of various quantities of silicon and manganese and lines of impurities along with sulfur and phosphorus. It is made via way of means of decreasing iron ore in a blast furnace.
- The liquid iron is forged, or poured and hardened, into crude ingots known as pigs, and the pigs are in the end remelted at the side of scrap and alloying factors in cupola furnaces and recast into molds for generating a lot of products. The Chinese produced forged iron as early because the sixth century BC, and it changed into produced sporadically in Europe via way of means of the 14th century.
- It changed into added into England approximately 1500; the primary ironworks in America have been mounted at the James River, Virginia, in 1619. During the 18th and nineteenth centuries, forged iron changed into a inexpensive engineering fabric than wrought iron as it did now no longer require in depth refining and running with hammers, however it changed into greater brittle and inferior in tensile power.
- Nevertheless, its load-bearing power made it the primary critical structural metal, and it changed into utilized in a number of the earliest skyscrapers. In the twentieth century, metal changed forged iron in construction, however forged iron keeps to have many commercial applications.
Q9) What is production route?
A9)
- Irregular eutectic systems shape while one of the levels facets. Most metal/nonmetal combinations, consisting of the industrially vital aluminum–silicon casting alloys and grey forged iron, shape abnormal systems consisting of the flake structure (vicinity D, Fig. 1). Growth anisotropy of the faceting section as opposed to warmth glide determines the neighborhood boom route.
- Also the presence of a side on the interface restricts its cappotential to house extrade easily main as a substitute to overgrowth and finally catastrophic breakdown. These traits imply that boom happens in a nonsteady-country way at a nonisothermal interface with a geometry of the shape proven in Fig. 2(e).
- Flakes develop at distinctive angles to the warmth glide route in advance of the nonfaceting section. Some develop toward every different till one is eliminated. This will increase the common spacing till it's far viable to create a brand new flake, for example, with the aid of using branching.
- The common spacing will rely upon the convenience with which new flakes can shape. This mode of solidification results in large measured undercoolings and spacings which do now no longer correspond to the extremum situation of the boom curve.
- The common spacing decreases as v and G increase. Any theoretical version should account for the elevated trouble of diffusion on the interface and for the extrade in temperature on the interface. Models superior thus far do now no longer offer a nice answer. For example, Magnin and Kurz (1987) taken into consideration the nonisothermal interface however used a aircraft the front diffusion answer and a spacing criterion associated with the intensity of a hole produced at the minor section.
- Subsequently, Magnin et al. (1991) equipped experimental undercooling and spacing measurements to the relationships for the extremum situation of ordinary lamellar boom in Sect. 2, with the common spacing given with the aid of using ϕλext. Their measurements counseled that ϕ is 3·2 for aluminum–silicon and 5·four for grey forged iron. No criterion for ϕ become counseled.
Q10) What is microstructure and applications
A10)
- The microstructure of a cloth consists of various stages of variable form, length and distribution (grains, precipitates, dendrites, spherulites, lamellae, pores, etc.).
- The stages are outstanding from every different with the aid of using their numerous crystalline, semi-crystalline or amorphous systems whilst discovered with an optical or electron microscope. The engineer can gain a huge variety of houses with the aid of using managed microstructural adjustments produced at some point of processing. To have a clean information of the cloth behaviour, it's miles had to set up relationships among the macroscopic houses and phenomena going on at the microstructural scale.
- The microstructures fashioned in substances rely now no longer handiest at the chemical composition and shape however additionally at the atomic mobility and at the presence of attention gradients at some point of processing. Microstructure formation is likewise strongly prompted with the aid of using the quantity of power required to create new interfaces. Appropriate warmness-remedies (quenching, annealing) produce a incredible sort of microstructures.
- Frequently, those have an inhomogeneous composition and are nearly usually metastable on the provider temperature. In the case of metals and alloys, warmness-remedies mixed with mechanical approaches inclusive of rolling have reached a totally excessive stage of class with a purpose to manipulate the microstructure.
- The majority of solidification microstructures are crystalline. However, a small range of substances having an abnormal molecular shape are not able to crystallise, regardless of the warmness remedies. These substances have a glassy shape withinside the stable state.
- It is the case of heterotactic vinyl polymers. Glass is usually much less solid than crystal whilst it exists and owes its transparency to a loss of microstructure.
- The microstructure of natural polymers is in general managed with the aid of using their chemical architecture. Macromolecules with a normal molecular shape are in wellknown capable of crystallise. However, crystallisation of polymer substances is by no means entire and, withinside the bulk, handiest semi-crystalline spherulites are fashioned.
Q11) Explain Effects of various parameters on structure and properties of Cast Iron.
A11)
- Wind electricity is a renewable, predictable, and smooth supply of electricity. Substantial potential may be constructed up quickly, presenting the electricity independence demanded with the aid of using the world’s biggest and fastest-developing economies.
- The majority of wind turbine elements are produced from the difficult ductile iron grade EN-GJS-400-18-LT; examples of DI castings for windmill. Therefore, interest is given for this grade of iron.
- The manufacturing of heavy phase ductile iron castings, however, nevertheless faces actual difficulties, represented withinside the formation of degenerated graphite morphologies withinside the ductile iron microstructures, which significantly reduces the effect in addition to fatigue residences.
- The necessities for excessive electricity and excessive effect residences in DI at low temperatures for a few packages as windmill are very strict. The European Standard EN-GJS-400-18U-LT usually called GGG 40.three is an example. This preferred now no longer simplest has the regular mechanical necessities for ferritic iron however additionally specifies V-notched Charpy effect necessities of 12 J at −20°C and minimal elongation of 18% .
- In order to gain those mechanical residences, the microstructure need to be properly managed in phrases of nodularity, nodule remember, and matrix stages. This is due to the fact excessive nodule remember impairs effect electricity and occasional nodule remember effects in intercellular brittle stages which can be negative to electricity and ductility.
- A minimal nodularity of 95% is critical; poorly formed nodules act as pressure riser and as initiation web website online for fracture beneathneath effect. Also, a matrix that is absolutely ferritic and freed from mobileular boundary stages is crucial to fulfill the mechanical residences of windmill castings
Q12) What is Alloy cast Iron such as Ni-resist?
A12)
- The term ‘forged iron’ covers a own circle of relatives of ferrous alloys. It is an iron alloy that carries greater than 2 carbon, and silicon withinside the variety 1 to 3%.
- The quantity of alloying and related manage of the warmth and cooling procedure can deliver a completely huge sort of houses to distinct grades of forged iron. Cast iron is used withinside the oil and fueloline enterprise for making water conduit pipes, packer parts, boilers, valve bodies, and valve parts.
- It is classed in step with the microstructure, which relies upon at the carbon content, the alloy and impurity content, the cooling charge at some stage in and after freezing, and warmth remedy after casting. The composition of forged iron varies significantly, relying upon the grade of pig iron, scrap used however it carries carbon withinside the variety of approximately 2–4% via way of means of weight.
- The carbon equal of a forged iron additionally enables to differentiate the grey irons, which cool right into a microstructure containing graphite, from the white irons wherein the carbon is gift particularly as cementite. Casting layout engineers need to catch up on the shrinkage of forged iron.
Q13) What is Ni-hard?
A13)
- The welding of solid irons has been notoriously referred to as a 'black-art'. Individual castings of equal kinds can range in reaction to welding, and so do the information of technique taken into consideration essential via way of means of skilled practitioners.
- Most castings are produced to internet shape, so welding is typically for restore and upkeep instead of fabrication. Structural load-bearing use is usually compressive, now no longer seriously tensile.
- The most common varieties of solid iron have round 3 and 2%Si. Flake graphite gray iron varies in pleasant and impurity content, with fairly low energy and ductility. Spheroidal graphite (SG), nodular or ductile iron is dealt with with magnesium, has fewer impurities, advanced mechanical properties, and greater dependable weldability.
- Electrodes primarily based totally on natural nickel and nickel-iron alloys are maximum extensively used. Electrode flux coverings are of simple kind plus graphite to present a weld deposit deoxidised and saturated with carbon. This mimics a number of the traits of solid iron however is non-hardenable and effortlessly machined. Recommended welding strategies are given on applicable facts sheets.
- Another group, excessive alloy austenitic irons (Ni-Resist kinds) also are produced in flake and SG grades. Electrodes of the NiFe kind are used due to the fact matching weld steel is simply too hard. Preheat of 300-350°C is needed for the flake graphite grades, however for the SG grades buttering at low temperatures is favored to keep away from HAZ warm cracking. Martensitic solid iron (Ni-Hard kinds) and the numerous white irons are commonly taken into consideration too crack-touchy or brittle to be welded satisfactorily.
Q14) What is Non-Ferrous Alloys?
A14)
- Non-ferrous metals have a tendency to be extra steeply-priced than ferrous metals however are used for his or her suitable homes, which include mild weight (aluminium), excessive conductivity (copper), non magnetic homes or resistance to corrosion (zinc). Some non-ferrous substances are used withinside the iron and metallic industries, together with bauxite, that's used for flux in blast furnaces.
- Other non-ferrous metals, which include chromite, pyrolusite and wolframite, are used to make ferrous alloys. However, many non-ferrous metals have low melting points, making them much less appropriate for packages at excessive temperatures.
- There are a huge quantity of non-ferrous substances, masking each metallic and alloy that doesn't include iron. Non-ferrous metals encompass aluminium, copper, lead, nickel, tin, titanium and zinc, in addition to copper alloys like brass and bronze.
- Other uncommon or valuable non-ferrous metals encompass gold, silver and platinum, cobalt, mercury, tungsten, beryllium, bismuth, cerium, cadmium, niobium, indium, gallium, germanium, lithium, selenium, tantalum, tellurium, vanadium, and zirconium.
- Non-ferrous metals are typically acquired from minerals like carbonates, silicates and sulphides earlier than being subtle thru electrolysis. The distinction among ferrous and non-ferrous metals is that ferrous metals include iron.
- Ferrous metals, together with forged irons or carbon metallic, have a excessive carbon content, which usually makes them liable to rust while uncovered to moisture. However, this isn't always the case for wrought iron, which resists rust because of its purity, and stainless metallic, that's included from corrosion through the presence of chromium.
Q15) Explain Study of non-ferrous alloys such as brasses (Cu-Zn diagram), Bronzes (Cu-Sn diagram).
A15)
- The essential nonferrous alloys in refinery and herbal fueloline processing gadget are the copper-primarily based totally and copper–nickel alloys. However, the usage of copper-primarily based totally alloys in ammonia (NH3) or ammonium salt (NH4+) environments need to be avoided—there may be a excessive capability for corrosion/destruction of the alloy structure.
- Aluminum brass, containing 2% w/w aluminum, has been discovered to be quite extra proof against erosion in saltwater. Inhibition with arsenic is essential to save you de-zincification, as withinside the case of admiralty brass.
- The more potent naval brass is frequently decided on because the tube sheet fabric while admiralty brass (wherein a small quantity of tin improves resistance to seawater) tubes are utilized in condensers. Generally, bronze is a tin alloy of copper, despite the fact that the time period has been broadly used for different alloys, along with a few brass alloys. Cast brass or bronze alloys for valves and fittings are normally copper–tin–zinc compositions, plus lead for machinability.
- Aluminum bronzes are frequently used as tube sheet and channel fabric for exchangers with admiralty brass or titanium tubes uncovered to cooling water. The 70/30 copper–nickel alloy is used for exchanger tubes while higher saltwater corrosion resistance than in aluminum brass is needed, or while excessive steel temperatures in water-cooled exchangers might also additionally reason de-zincification in brass.
- Monel is a nickel–copper alloy with 67% w/w nickel and 30% w/w copper, which has superb resistance to saltwater and, below nonoxidizing conditions, to acids together with hydrochloric acid and hydrofluoric acid. Monel has a higher excessive-temperature resistance to cooling water than 70/30 copper–nickel.
- In fact, Monel cladding and Monel trays are usually exact on the pinnacle of crude towers to withstand corrosion with the aid of using hydrogen chloride vapor and in which the temperature is beneathneath 205°C (400°F). At temperatures in extra of 205°C (400°F), nickel-primarily based totally alloys are attacked with the aid of using hydrogen sulfide.
- For excessive-temperature power and/or corrosion resistance, numerous nickel-primarily based totally alloys are used for unique applications, together with enlargement bellows in fluid catalytic cracking procedure units (Alloy 625), stems in flue fueloline butterfly valves (Alloy X 750), and is derived uncovered to excessive-temperature corrosive gases and liquids (Alloy X).
- Titanium has superb resistance to seawater, and it's also used for tubing in crude tower overhead condensers.
Cu-Zn diagram
![Equilibrium Cu-Zn phase diagram [5] | Download Scientific Diagram](https://glossaread-contain.s3.ap-south-1.amazonaws.com/epub/1650889878_6459713.jpeg)
Fig: Cu-Zn diagram
Bronzes (Cu-Sn diagram)
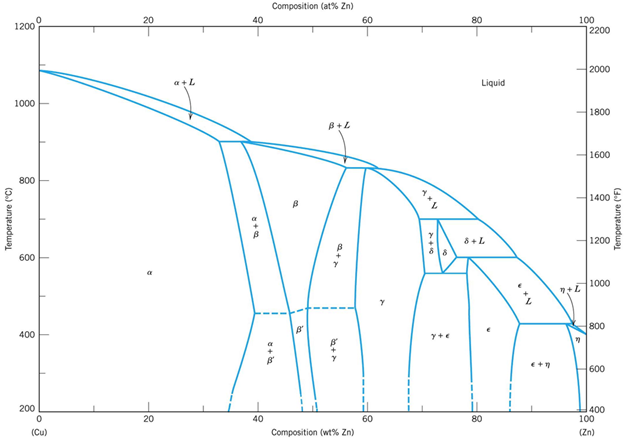
Fig: Bronzes (Cu-Sn diagram)
Unit - 4
Cast Iron
Q1) What is cast iron?
A1)
Cast Iron
- Cast irons are a type of ferrous alloy with a carbon concentration greater than 2.14 weight percent; however, most cast irons possess between 3.0 and 4.5 weight percent C, as well as other alloying elements.
- A closer look at the iron–iron carbide phase diagram reveals that alloys in this composition range become entirely liquid at temperatures between 1150 and 1300C (2100 and 2350F), which is significantly lower than steel temperatures. As a result, they are easily melted and castable.
- Furthermore, some cast irons are extremely fragile, and casting is the most practical method of manufacturing.
- As a result, the actual equilibrium diagram for iron and carbon is displayed in Figure b rather than Figure a.
- On the iron-rich side, the two diagrams are nearly identical (eutectic and eutectoid temperatures for the Fe–Fe3C system are 1147 and 727C, respectively, compared to 1153 and 740C for Fe–C); however, Figure b extends to 100 wt% C, making graphite the carbon-rich phase rather than cementite at 6.7 wt% C.
- The composition and pace of cooling control the tendency to generate graphite. The inclusion of silicon in amounts larger than around 1 wt% promotes graphite production.
- In addition, graphitization is favoured by slower cooling rates during solidification (the formation of graphite). Carbon exists as graphite in most cast irons, and both microstructure and mechanical behaviour are affected by composition and heat treatment. Gray, nodular, white, malleable, and compacted graphite are the most frequent cast iron varieties.
Cast iron is a ferrous alloy containing high levels of carbon, generally greater than 2%. The carbon present in the cast iron can take the form of graphite or carbide. Cast irons have a low melting temperature which makes them well suited to casting.
Q2) Classify cast iron in detail.
A2)
Classification of cast iron
The cast iron is classified into seven major kinds as follows:
1) Grey cast iron
2) White cast iron
3) Mottled cast iron
4) Malleable cast iron
5) Nodular cast and ductile cast iron
6) Machanite cast iron
Gray Cast Iron
Gray cast iron is the most common type. The carbon is in the form of graphite flakes. Gray cast iron is a brittle material, and its compressive strength is much higher than its tensile strength. The fracture surface of gray cast iron has a gray color, which is how it got its name.
Ductile Cast Iron (Nodular Cast Iron)
The addition of magnesium to gray cast iron improves the ductility of the material. The resulting material is called nodular cast iron because the magnesium causes the graphite flakes to form into spherical nodules. It is also called ductile cast iron. Nodular cast iron has good strength, ductility, and machinability. Common uses include crankshafts, gears, pump bodies, valves, and machine parts.
White Cast Iron
White cast iron has carbon in the form of carbide, which makes the material hard, brittle, and difficult to machine. White cast iron is primarily used for wear-resisting components as well as for the production of malleable cast iron.
Malleable Cast Iron
Malleable cast iron is produced by heat treating white cast iron. The heat treatment improves the ductility of the material while maintaining its high strength.
Q3) Define white cast Iron.
A3)
- White cast irons are used in abrasion-resistant parts where its brittleness is of minimum concern such as shell liners, slurry pumps, ball mills, lifter bars, extrusion nozzles, cement mixers, pipe fittings, flanges, crushers and pump impellers.
- A popular grade of white iron is high chrome white irons, ASTM A532. This contains nickel and chromium for good low-impact abrasion applications.
Q4) Explain Gray Cast Iron.
A4)
- Gray cast irons have carbon and silicon concentrations of 2.5 to 4.0 wt percent and 1.0 to 3.0 wt percent, respectively.
- The graphite in most of these cast irons is in the form of flakes (like corn flakes), which are usually surrounded by an x-ferrite or pearlite matrix; this is the microstructure of a typical grey iron. A shattered surface takes on a grey look as a result of the graphite flakes, hence the name.
- Because of its microstructure, grey iron is comparatively weak and brittle in tension; the tips of the graphite flakes are sharp and pointed and may act as stress concentration locations when an external tensile load is applied. Under compressive loads, strength and ductility are substantially higher.
- Gray irons have several useful properties and are widely used. When comparing the respective damping capacities of steel and grey iron, they are quite effective in damping vibrational energy.
- This material is widely used to build the base constructions of machinery and heavy equipment that are subjected to vibrations. In addition, grey irons have a good wear resistance. Furthermore, they have a high fluidity at casting temperature in the molten state, allowing for the casting of intricately shaped objects, as well as reduced casting shrinkage. Finally, and perhaps most importantly, grey cast iron is one of the most affordable metals available.
Q5) What is Nodular Cast Iron?
A5)
- Before casting, a small quantity of magnesium and/or cerium is added to the grey iron, resulting in a specific microstructure and set of mechanical properties. Graphite still exists, albeit in the shape of nodules or spherelike particles rather than flakes.
- The resulting alloy has a characteristic microstructure and is known as ductile or nodular iron. Depending on the heat treatment, the matrix phase enclosing these particles is either pearlite or ferrite; for an as cast piece, the matrix phase is usually pearlite. However, a heat treatment at around 700C (1300F) for several hours will result in a ferrite matrix, as seen in this photomicrograph. Castings are substantially more ductile and stronger than grey iron.
Q6) Explain Malleable Cast Iron.
A6)
- Most of the carbon in low silicon cast irons (less than 1.0 wt percent Si) and quick cooling rates resides as cementite rather than graphite. Because the fracture surface of this alloy is white, it is known as white cast iron. Thick portions may only have a thin layer of white iron on the top that was "chilled" during the casting process; grey iron forms in the inside, which cools more slowly.
- White iron is highly hard but also extremely brittle, to the point of being essentially unmachinable, due to large concentrations of the cementite phase. Its applications are limited to those that require a highly hard and wear-resistant surface without a significant degree of ductility, such as rollers in rolling mills. White iron is typically utilised as a step between the manufacture of malleable iron and another type of cast iron.
- Heating white iron for a long time at temperatures between 800 and 900 degrees Celsius (1470- and 1650-degrees Fahrenheit) in a neutral atmosphere (to prevent oxidation) causes the cementite to decompose, forming graphite in the form of clusters or rosettes surrounded by a ferrite or pearlite matrix, depending on the cooling rate.
Q7) Explain chilled iron?
A7)
Chilled iron
- Chilled solid iron When a localized region of grey solid iron is cooled very swiftly from the melt, solid iron is fashioned on the region that has been cooled.
- This form of white solid iron is known as chilled solid iron. A chilled iron casting may be produced via way of means of adjusting the carbon composition of the white solid iron, in order that the regular cooling charge on the floor is simply speedy sufficient to supply white solid iron, while the slower cooling charge beneath the floor will produce grey iron.
- The intensity of kick back decreases, and the hardness of the chilled sector will increase with growing carbon content. Chromium in small quantities is frequently used to govern kick back intensity, due to the formation of chromium carbides.
- Chromium is utilized in quantity of 1%–4% in chilled iron to growth hardness and enhance abrasion resistance. It additionally stabilizes carbide and suppresses the formation of graphite in heavy sections. When introduced in quantities of 12%–35%, chromium will impart resistance to corrosion and oxidation at increased temperatures.
Q8) What is alloy cast iron?
A8)
Alloy Cast Iron
- Forged iron, an alloy of iron that incorporates 2 to four percentage carbon, at the side of various quantities of silicon and manganese and lines of impurities along with sulfur and phosphorus. It is made via way of means of decreasing iron ore in a blast furnace.
- The liquid iron is forged, or poured and hardened, into crude ingots known as pigs, and the pigs are in the end remelted at the side of scrap and alloying factors in cupola furnaces and recast into molds for generating a lot of products. The Chinese produced forged iron as early because the sixth century BC, and it changed into produced sporadically in Europe via way of means of the 14th century.
- It changed into added into England approximately 1500; the primary ironworks in America have been mounted at the James River, Virginia, in 1619. During the 18th and nineteenth centuries, forged iron changed into a inexpensive engineering fabric than wrought iron as it did now no longer require in depth refining and running with hammers, however it changed into greater brittle and inferior in tensile power.
- Nevertheless, its load-bearing power made it the primary critical structural metal, and it changed into utilized in a number of the earliest skyscrapers. In the twentieth century, metal changed forged iron in construction, however forged iron keeps to have many commercial applications.
Q9) What is production route?
A9)
- Irregular eutectic systems shape while one of the levels facets. Most metal/nonmetal combinations, consisting of the industrially vital aluminum–silicon casting alloys and grey forged iron, shape abnormal systems consisting of the flake structure (vicinity D, Fig. 1). Growth anisotropy of the faceting section as opposed to warmth glide determines the neighborhood boom route.
- Also the presence of a side on the interface restricts its cappotential to house extrade easily main as a substitute to overgrowth and finally catastrophic breakdown. These traits imply that boom happens in a nonsteady-country way at a nonisothermal interface with a geometry of the shape proven in Fig. 2(e).
- Flakes develop at distinctive angles to the warmth glide route in advance of the nonfaceting section. Some develop toward every different till one is eliminated. This will increase the common spacing till it's far viable to create a brand new flake, for example, with the aid of using branching.
- The common spacing will rely upon the convenience with which new flakes can shape. This mode of solidification results in large measured undercoolings and spacings which do now no longer correspond to the extremum situation of the boom curve.
- The common spacing decreases as v and G increase. Any theoretical version should account for the elevated trouble of diffusion on the interface and for the extrade in temperature on the interface. Models superior thus far do now no longer offer a nice answer. For example, Magnin and Kurz (1987) taken into consideration the nonisothermal interface however used a aircraft the front diffusion answer and a spacing criterion associated with the intensity of a hole produced at the minor section.
- Subsequently, Magnin et al. (1991) equipped experimental undercooling and spacing measurements to the relationships for the extremum situation of ordinary lamellar boom in Sect. 2, with the common spacing given with the aid of using ϕλext. Their measurements counseled that ϕ is 3·2 for aluminum–silicon and 5·four for grey forged iron. No criterion for ϕ become counseled.
Q10) What is microstructure and applications
A10)
- The microstructure of a cloth consists of various stages of variable form, length and distribution (grains, precipitates, dendrites, spherulites, lamellae, pores, etc.).
- The stages are outstanding from every different with the aid of using their numerous crystalline, semi-crystalline or amorphous systems whilst discovered with an optical or electron microscope. The engineer can gain a huge variety of houses with the aid of using managed microstructural adjustments produced at some point of processing. To have a clean information of the cloth behaviour, it's miles had to set up relationships among the macroscopic houses and phenomena going on at the microstructural scale.
- The microstructures fashioned in substances rely now no longer handiest at the chemical composition and shape however additionally at the atomic mobility and at the presence of attention gradients at some point of processing. Microstructure formation is likewise strongly prompted with the aid of using the quantity of power required to create new interfaces. Appropriate warmness-remedies (quenching, annealing) produce a incredible sort of microstructures.
- Frequently, those have an inhomogeneous composition and are nearly usually metastable on the provider temperature. In the case of metals and alloys, warmness-remedies mixed with mechanical approaches inclusive of rolling have reached a totally excessive stage of class with a purpose to manipulate the microstructure.
- The majority of solidification microstructures are crystalline. However, a small range of substances having an abnormal molecular shape are not able to crystallise, regardless of the warmness remedies. These substances have a glassy shape withinside the stable state.
- It is the case of heterotactic vinyl polymers. Glass is usually much less solid than crystal whilst it exists and owes its transparency to a loss of microstructure.
- The microstructure of natural polymers is in general managed with the aid of using their chemical architecture. Macromolecules with a normal molecular shape are in wellknown capable of crystallise. However, crystallisation of polymer substances is by no means entire and, withinside the bulk, handiest semi-crystalline spherulites are fashioned.
Q11) Explain Effects of various parameters on structure and properties of Cast Iron.
A11)
- Wind electricity is a renewable, predictable, and smooth supply of electricity. Substantial potential may be constructed up quickly, presenting the electricity independence demanded with the aid of using the world’s biggest and fastest-developing economies.
- The majority of wind turbine elements are produced from the difficult ductile iron grade EN-GJS-400-18-LT; examples of DI castings for windmill. Therefore, interest is given for this grade of iron.
- The manufacturing of heavy phase ductile iron castings, however, nevertheless faces actual difficulties, represented withinside the formation of degenerated graphite morphologies withinside the ductile iron microstructures, which significantly reduces the effect in addition to fatigue residences.
- The necessities for excessive electricity and excessive effect residences in DI at low temperatures for a few packages as windmill are very strict. The European Standard EN-GJS-400-18U-LT usually called GGG 40.three is an example. This preferred now no longer simplest has the regular mechanical necessities for ferritic iron however additionally specifies V-notched Charpy effect necessities of 12 J at −20°C and minimal elongation of 18% .
- In order to gain those mechanical residences, the microstructure need to be properly managed in phrases of nodularity, nodule remember, and matrix stages. This is due to the fact excessive nodule remember impairs effect electricity and occasional nodule remember effects in intercellular brittle stages which can be negative to electricity and ductility.
- A minimal nodularity of 95% is critical; poorly formed nodules act as pressure riser and as initiation web website online for fracture beneathneath effect. Also, a matrix that is absolutely ferritic and freed from mobileular boundary stages is crucial to fulfill the mechanical residences of windmill castings
Q12) What is Alloy cast Iron such as Ni-resist?
A12)
- The term ‘forged iron’ covers a own circle of relatives of ferrous alloys. It is an iron alloy that carries greater than 2 carbon, and silicon withinside the variety 1 to 3%.
- The quantity of alloying and related manage of the warmth and cooling procedure can deliver a completely huge sort of houses to distinct grades of forged iron. Cast iron is used withinside the oil and fueloline enterprise for making water conduit pipes, packer parts, boilers, valve bodies, and valve parts.
- It is classed in step with the microstructure, which relies upon at the carbon content, the alloy and impurity content, the cooling charge at some stage in and after freezing, and warmth remedy after casting. The composition of forged iron varies significantly, relying upon the grade of pig iron, scrap used however it carries carbon withinside the variety of approximately 2–4% via way of means of weight.
- The carbon equal of a forged iron additionally enables to differentiate the grey irons, which cool right into a microstructure containing graphite, from the white irons wherein the carbon is gift particularly as cementite. Casting layout engineers need to catch up on the shrinkage of forged iron.
Q13) What is Ni-hard?
A13)
- The welding of solid irons has been notoriously referred to as a 'black-art'. Individual castings of equal kinds can range in reaction to welding, and so do the information of technique taken into consideration essential via way of means of skilled practitioners.
- Most castings are produced to internet shape, so welding is typically for restore and upkeep instead of fabrication. Structural load-bearing use is usually compressive, now no longer seriously tensile.
- The most common varieties of solid iron have round 3 and 2%Si. Flake graphite gray iron varies in pleasant and impurity content, with fairly low energy and ductility. Spheroidal graphite (SG), nodular or ductile iron is dealt with with magnesium, has fewer impurities, advanced mechanical properties, and greater dependable weldability.
- Electrodes primarily based totally on natural nickel and nickel-iron alloys are maximum extensively used. Electrode flux coverings are of simple kind plus graphite to present a weld deposit deoxidised and saturated with carbon. This mimics a number of the traits of solid iron however is non-hardenable and effortlessly machined. Recommended welding strategies are given on applicable facts sheets.
- Another group, excessive alloy austenitic irons (Ni-Resist kinds) also are produced in flake and SG grades. Electrodes of the NiFe kind are used due to the fact matching weld steel is simply too hard. Preheat of 300-350°C is needed for the flake graphite grades, however for the SG grades buttering at low temperatures is favored to keep away from HAZ warm cracking. Martensitic solid iron (Ni-Hard kinds) and the numerous white irons are commonly taken into consideration too crack-touchy or brittle to be welded satisfactorily.
Q14) What is Non-Ferrous Alloys?
A14)
- Non-ferrous metals have a tendency to be extra steeply-priced than ferrous metals however are used for his or her suitable homes, which include mild weight (aluminium), excessive conductivity (copper), non magnetic homes or resistance to corrosion (zinc). Some non-ferrous substances are used withinside the iron and metallic industries, together with bauxite, that's used for flux in blast furnaces.
- Other non-ferrous metals, which include chromite, pyrolusite and wolframite, are used to make ferrous alloys. However, many non-ferrous metals have low melting points, making them much less appropriate for packages at excessive temperatures.
- There are a huge quantity of non-ferrous substances, masking each metallic and alloy that doesn't include iron. Non-ferrous metals encompass aluminium, copper, lead, nickel, tin, titanium and zinc, in addition to copper alloys like brass and bronze.
- Other uncommon or valuable non-ferrous metals encompass gold, silver and platinum, cobalt, mercury, tungsten, beryllium, bismuth, cerium, cadmium, niobium, indium, gallium, germanium, lithium, selenium, tantalum, tellurium, vanadium, and zirconium.
- Non-ferrous metals are typically acquired from minerals like carbonates, silicates and sulphides earlier than being subtle thru electrolysis. The distinction among ferrous and non-ferrous metals is that ferrous metals include iron.
- Ferrous metals, together with forged irons or carbon metallic, have a excessive carbon content, which usually makes them liable to rust while uncovered to moisture. However, this isn't always the case for wrought iron, which resists rust because of its purity, and stainless metallic, that's included from corrosion through the presence of chromium.
Q15) Explain Study of non-ferrous alloys such as brasses (Cu-Zn diagram), Bronzes (Cu-Sn diagram).
A15)
- The essential nonferrous alloys in refinery and herbal fueloline processing gadget are the copper-primarily based totally and copper–nickel alloys. However, the usage of copper-primarily based totally alloys in ammonia (NH3) or ammonium salt (NH4+) environments need to be avoided—there may be a excessive capability for corrosion/destruction of the alloy structure.
- Aluminum brass, containing 2% w/w aluminum, has been discovered to be quite extra proof against erosion in saltwater. Inhibition with arsenic is essential to save you de-zincification, as withinside the case of admiralty brass.
- The more potent naval brass is frequently decided on because the tube sheet fabric while admiralty brass (wherein a small quantity of tin improves resistance to seawater) tubes are utilized in condensers. Generally, bronze is a tin alloy of copper, despite the fact that the time period has been broadly used for different alloys, along with a few brass alloys. Cast brass or bronze alloys for valves and fittings are normally copper–tin–zinc compositions, plus lead for machinability.
- Aluminum bronzes are frequently used as tube sheet and channel fabric for exchangers with admiralty brass or titanium tubes uncovered to cooling water. The 70/30 copper–nickel alloy is used for exchanger tubes while higher saltwater corrosion resistance than in aluminum brass is needed, or while excessive steel temperatures in water-cooled exchangers might also additionally reason de-zincification in brass.
- Monel is a nickel–copper alloy with 67% w/w nickel and 30% w/w copper, which has superb resistance to saltwater and, below nonoxidizing conditions, to acids together with hydrochloric acid and hydrofluoric acid. Monel has a higher excessive-temperature resistance to cooling water than 70/30 copper–nickel.
- In fact, Monel cladding and Monel trays are usually exact on the pinnacle of crude towers to withstand corrosion with the aid of using hydrogen chloride vapor and in which the temperature is beneathneath 205°C (400°F). At temperatures in extra of 205°C (400°F), nickel-primarily based totally alloys are attacked with the aid of using hydrogen sulfide.
- For excessive-temperature power and/or corrosion resistance, numerous nickel-primarily based totally alloys are used for unique applications, together with enlargement bellows in fluid catalytic cracking procedure units (Alloy 625), stems in flue fueloline butterfly valves (Alloy X 750), and is derived uncovered to excessive-temperature corrosive gases and liquids (Alloy X).
- Titanium has superb resistance to seawater, and it's also used for tubing in crude tower overhead condensers.
Cu-Zn diagram
![Equilibrium Cu-Zn phase diagram [5] | Download Scientific Diagram](https://glossaread-contain.s3.ap-south-1.amazonaws.com/epub/1650889881_1756022.jpeg)
Fig: Cu-Zn diagram
Bronzes (Cu-Sn diagram)
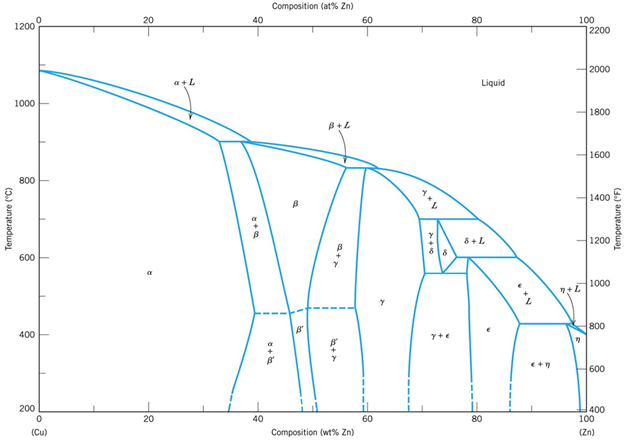
Fig: Bronzes (Cu-Sn diagram)