Unit - 5
Energy losses in steam turbines
Q1) Write a short note on energy losses in steam turbines
A1)
Admission losses
In exercise the go with the drift of steam thru nozzle isn't isentropic, however followed with losses which lower the kinetic power of steam popping out of the nozzle.
- The lower in kinetic power is because of the subsequent reasons
- Viscous forces among steam debris
- Heat loss from steam earlier than coming into the nozzle
- Boundary layer improvement with inside the nozzle
- Turbulence with inside the nozzle
The friction with inside the nozzle which reduces to be had enthalpy drop and for this reason real pace leaving the nozzle is much less than that received with is-entropic expansion
Leakage losses
Steam leaves the boiler and reaches the condenser after passing thru the principle valve, regulating valves, nozzles, clearance areas among nozzles and shifting blades, diaphragm and rotating shaft etc.
Further there's big strain distinction among inner of steam turbine and the ambient and additionally from one area to every other area throughout those devices.
- Therefore, steam leakage takes region thru Main valve and regulating valve
- Spaces among nozzles and shifting blades
- Spaces among diaphragm and shaft of turbine
- Space among shifting blade earrings and turbine casing leakage of steam thru those is a right away lack of power.
Friction losses
Frictional resistance is obtainable all through go with the drift of steam thru nozzles on shifting and desk bound blades.
In maximum of the generators the blade wheels rotate in a area complete of steam.
The viscous friction on the wheel floor reasons admission losses as steam passes from nozzle to wheel.
The floor of curved shifting blades and desk bound blades gives resistance, which will increase with boom in roughness of blade floor and relative pace among steam and rotating blade.
The power loss additionally takes region while the steam jets turns alongside the curvature of the blade floor.
The turning losses rely on the perspective of turning.
Exhaust loss
The power content material of steam isn't completely applied with inside the turbine. Despite of being at very low strain the exhaust popping out of the turbine and coming into the condenser consists of a number of kinetic power and beneficial enthalpy, that's direct power loss.
Radiation and convection losses
The steam turbine operates at an incredibly excessive temperature; consequently a number of the warmth power of steam is radiated and convicted from the frame of the turbine to its surrounding.
These direct losses are minimized via way of means of right insulation. Losses because of moisture
The steam passing thru the remaining level of turbine has excessive pace and big moisture content material.
The liquid debris have lesser pace than that of vapor debris and for this reason the liquid debris impede the go with the drift of vapor debris with inside the remaining level of turbine and consequently, part of kinetic power of steam is lost. If the dryness fraction of steam falls beneath 0.88, the erosion and corrosion of blades also can take region.
Carry over losses
When steam passes from one level to every other thru the diaphragm, a few power losses takes region, that are called deliver over losses and consequently, the kinetic power of steam to be had at succeeding level of shifting blades for usage is much less than that of the go out at previous level.
This is because of formation of eddies in annular area among the nozzle and shifting blades.
Q2) Explain flow of steam through turbine blades
A2)
- Steam is first heated in a steam technology machine (for instance, in boilers or waste warmness restoration systems), in which it reaches an excessive temperature, round 400°C to 600°C.
- The first valve that the steam encounters because it travels from the steam technology machine to the steam turbine is the primary forestall valve (primary experience or shutdown valve), that's both completely opened and completely closed. This valve frequently does now no longer manage the steam go with the drift aside from to absolutely forestall it. Screen Shot 2016 07 29 at four 25 forty five Pm 1
- Control or throttling valves in unique preparations and configurations also are used to govern the steam inlet.
- Combined experience and throttle valves also are common. In many steam mills, as a minimum impartial experience valves need to be furnished for correct redundancy.
- These valves are right now beforehand of the steam turbine and are designed to resist the total temperature and stress of the steam. These valves are important because, if the mechanical load is misplaced, the steam turbine could swiftly over-velocity and damage itself.
- This is an occasional occurrence. An uncommon root-cause, including coupling failure, would possibly bring about this. Other injuries are possible, helping the want for 2 or 3 impartial forestall valves, which carry protection and reliability however upload price to the machine.
- Steam turbine drives are ready with throttling valves or nozzle governors to modulate steam go with the drift and obtain variable velocity operation. The steam turbine force is able to serving the equal feature as a variable velocity force electric powered motor driver.
- Steam mills can generally function throughout a vast velocity variety and do now no longer fail while overloaded.
- They additionally produce the excessive beginning torque required for regular torque masses including with fine displacement pumps or compressors.
- The steam hits the primary row of blades at pressures so excessive that it may produce torque with only a small floor area.
- The steam’s effect reasons the rotor to turn. As the steam turbine ranges progress, however, the steam loses stress and energy, therefore, requiring more and more massive floor areas.
- For this reason, the blades’ sizes boom with every level. When the steam leaves the turbine, its temperature has dropped, and it has misplaced nearly all its accelerated stress. Some of the stress drop additionally happens throughout the diaphragm, which is a part among the outer wall and internal web.
- The steam need to strike the blades at a selected perspective with the intention to maximize the beneficial paintings of the steam’s stress. This is in which nozzles come into play.
- Stationary jewelry of nozzles are located among the blade wheels to “turn” the steam on the best perspective for putting the blades. A thrust bearing is established at one cease of the primary shaft to hold its axial role and hold the transferring elements from colliding with the desk bound elements. The magazine bearing helps the primary shaft and restricts it from springing out of its casing at excessive speeds.
- An exhaust hood publications steam from the remaining level of the steam turbine, and its miles designed to reduce stress loss, which could lower the thermal performance of the steam turbine. After the steam leaves the exhaust section, it enters a condenser, in which its miles cooled to a liquid state. The technique of condensing the steam generally creates a vacuum, which then brings in greater steam from the steam turbine. The water is again to the steam technology machine, reheated and reused.
- The governor is a tool that controls the turbine’s velocity. Modern steam mills have a digital governor that makes use of sensors to display the rate with the aid of using inspecting the rotor teeth.
- To lay out a greater green steam turbine, a casing with right nozzles and vanes to restrict the steam and valves to govern the admission of steam to the nozzles need to be used.
- The thick-walled castings used for the stress-containing turbine sections are referred to as shells and are generally crafted from alloy metallic materials. Some designs encompass internal and outer shells, which serve to stability the stress drop and decrease the shell’s thickness for thermal stress, beginning and loading.
- Multistage designs are used to boom performance. The kind and range of turbine ranges and the form and length of the blades range. They are decided primarily based totally at the steam stress and temperature, the exhaust stress, and the rate.
- When the steam turbine’s rotor is desk bound, the steam flowing via the nozzle will hit the blades with complete force, exerting the finest quantity of torque. However, due to the fact that this happens at the same time as the rotor is at a standstill, the paintings achieved is 0. On the opposite hand, if the rate of the rotor is identical to that of the steam, the steam will don't have any pace element relative to the blades, and the blades will now no longer turn.
- Therefore, this example results in 0 torque and, as soon as again, 0 paintings. The most performance happens among those extremes. Proper optimization need to be achieved to attain perfect running situations and height performance.
- Because of the excessive pressures utilized in steam mills, the casing is pretty thick, and therefore steam mills show off massive thermal inertia. They need to be warmed up and cooled down slowly to reduce the differential growth among the rotating blades and the desk bound additives. Large steam mills might also additionally require about 5 to 9 hours to heat up.
- While smaller devices have greater fast begin-up instances, steam mills vary drastically from reciprocating engines, which begin up swiftly, and from fuelling mills, which could begin up in a mild quantity of time and cargo observe with affordable rapidity.
- Steam turbine packages generally function constantly for prolonged intervals of time, despite the fact that the steam fed to the unit and the mechanical electricity added might also additionally range all through such intervals of non-stop operation.
- Because maximum steam mills are decided on for packages with excessive-responsibility factors, the character in their software frequently looks after the want to have simplest sluggish temperature adjustments all through operation, and lengthy startup instances may be tolerated. Steam boilers further have lengthy startup instances.
Q3) What is reheat factor?
A3)
The Rankine Cycle geared up with a reheated may have at the least stages of steam turbine: high-strain turbine and low-strain turbine. High-strain steam turbine output steam, typically called bloodless reheat steam, has decrease strain and temperature of major steam, earlier than getting into the turbine.
Although the bloodless reheat strain drops significantly, it nevertheless has now no longer reached its saturation point. So, if this steam reheated, it'll go back to superheated steam. Therefore the bloodless reheat steam that exits the high-strain turbine, may be reheated again into the boiler. Modern boilers geared up with reheated pipes, particularly designed in order that the reheated steam soak up warmth similar to the principle steam.
The reheated steam, additionally referred to as warm warmth reheat steam, will attain the identical temperature as the principle steam vapor. To acquire this, the reheated pipes may be located now no longer some distance from the very last pipes of the superheated.
More specifically, allow us to confer with the subsequent supercritical boiler diagram. Seen in above boiler diagram, reheated pipes are divided into heating tiers.
First, the bloodless reheat steam passes thru the Low-Temperature Reheated pipes, which proven with the aid of using the name “LTRH” on the diagram. Furthermore, LTRH output steam flows to the pipes referred to as Final Reheated.
The steam produced with the aid of using the Final Reheated is then referred to as Hot Reheat steam. Hot Reheat steam then is going to the low-strain steam turbine, in order that the warmth power contained in its miles transformed into mechanical power of the turbine shaft rotation.
Theoretically, the addition of 1 level reheated usage will boom the thermal performance of the Rankine cycle with the aid of using 3–4%, the addition of tiers of the reheated will increase the performance with the aid of using 1. 5–2%, the addition of the three-level reheated will increase performance with the aid of using 0.75–1%, and so on.
Commonly, present day boiler simplest makes use of one or level re-heater.
Reheat factor = Cumulative heat drop / isentropic heat drop (Overall)
Q4) What is velocity diagram?
A4)
The picture shows steam turbine velocity diagram.
The upper portion represents the inlet condition of steam and lower portion represents the outlet portion of steam.
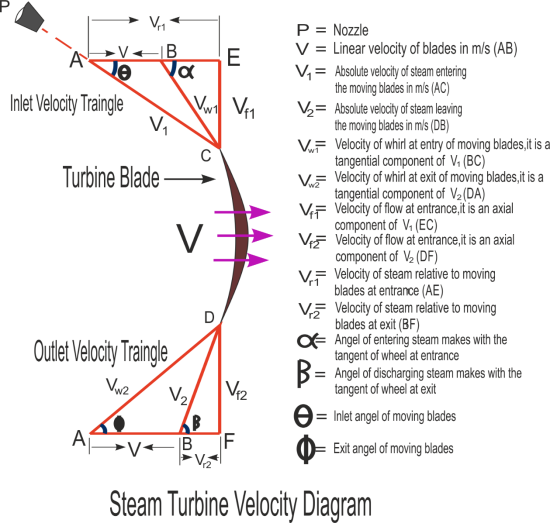
Let the steam jet is coming from nozzle P. After that it coming into a curved blade and leaving the nozzle at C. The jet glides over the internal floor and leaves the blade at D. Let us draw the steam turbine speed diagram.
Assume, it creates at a perspective a to the tangent of the wheel with a speed V1 that's absolutely the speed of steam.
This absolute speed V1 has components. One tangential thing Vw1 and any other axial thing Vf1.
Vf1 is the speed of go with the drift at entrance, so it's miles perpendicular to the path of blade's movement and it does now no longer any paintings, however that is the thing that's completely answerable for go with the drift of steam thru the turbine.
Now shifting blades begin to circulate at a tangential speed V with inside the horizontal path and the jet of steam is V1 speed create an perspective a to the a few horizontal path.
So each shifting blades and jet of steam are shifting with inside the equal path and steam input the shifting blades with a relative speed Vr which may be discovered through subtracting the V and V1 thing and count on it create a few perspective T1.
For clean flowing of steam whilst passing the shifting blades, the jet of steam input the shifting blade's tip and it additionally creates a few perspective of shifting blade T. T and T1 are equal.
When T1 and T could be equal the steam's go with the drift will easily strike the shifting blades. In real exercise T and Tthita1 is equal and that’s why we denote it T.
Similarly suffix 2 represents the opening speed of steam. Here steam leaving from shifting blades at a perspective β which makes with the tangent of the wheel with a speed V2 and its miles absolutely the speed of steam leaving of shifting blades. This speed V2 has components. One Vw2 that's tangential thing and any other is Vf2 that's axial thing.
Vw2 is the speed thing of whirl to go out and its miles the real thing for which steam leaving from the shifting blades. Vf2 is go with the drift thing and its miles answerable for speed of go with the drift of steam to go out.
The shifting blades are going for walks at horizontal path with a tangential speed V and V2 absolutely the speed of steam leaving of shifting blades create an perspective β with a relative speed Vr2 to shifting the blade to go out.
This Vr2 may be acquire through subtracting the V and V2 and it create a few perspective F1.
But for clean flowing of the steam at the same time as existing, it creates a perspective of shifting blades i.e.
Now F and F1 are equal. So, we denote it F. When F1 is same to F then steam go out easily and steadily.
Q5) Write a shot note on graphical and analytical methods
A5)
A steam turbine is a key unit in a steam strength plant from which we get strength.
A steam turbine is a faster system and a top mover wherein strength of stem is converted into kinetic strength and this kinetic strength is then converted into mechanical strength of rotation of shaft of turbine.
The cutting-edge steam turbine changed into invented in 1884 via way of means of Sir Charles Parsons, whose first model changed into related to a dynamo that generated 7.five kW (10 hp) of electricity.
The Parsons turbine additionally grew to become out to be smooth to scale up. Parsons had the pride of seeing his invention followed for all predominant global strength stations, and the scale of mills had extended from his first 7.5 kW installation to devices of 500MW capacity.
Steam mills are essential additives of technique plant application systems.
They provide possibilities for optimizing steam deliver reliability, in addition to site-extensive strength efficiency.
Steam mills are maximum not unusual place with inside the oil refining, ammonia and urea, methanol, ethylene, and pulp and paper industries, in which they may be normally sized to provide 10–60 MW of strength.
Good economics also are feasible at smaller sizes as little as 2 MW, which can be greater not unusual place with inside the meals and beverage industries, in addition to in small to medium-sized flora with inside the chemical technique industries (CPI).
Achieving favorable steam turbine economics relies upon on selecting the proper sort of turbine (e.g., backpressure vs. Condensing) with inside the proper size, in addition to integrating it successfully with the warmth exchanger network (HEN) according with the ideal placement precept of pinch analysis.
This article critiques the thermodynamic relationships and equations that hyperlink steam float situations and strength output, which can be beneficial for estimating initial economics of recent mills and studying the overall performance of present devices.
Backpressure steam generators (BPSTs) produce low-stress (LP) exhaust steam that may be used for one or extra method heating duties (Figure 1a). The targets are to offer the method with steam of the amount and stress required with the aid of using the method, even as producing the most quantity of energy which will lessen the want for bought energy. Because BPSTs cogenerate electricity products (i.e., steam and energy) simultaneously, they have got a powerful warmness charge of 4,500–5,500 Btu/kWh, which represents an electricity performance to 3 instances higher than that of a condensing turbine, even after deliberating each boiler and turbine electricity losses.
(Heat charge is the quantity of gasoline this is transformed with the aid of using a warmness engine into beneficial energy — the decrease the number, the higher.
The minimal feasible warmness charge is 3,413 Btu/kWh, representing a hundred% conversion of gasoline electricity into energy.)
Pure BPSTs are used typically in commercial centers that perform continuously, wherein the intention is excessive thermodynamic performance and the electricity needs are notably stable.
They are normally sized for 3–60 MW. Condensing steam generators (CSTs) exhaust steam to a condenser at atmospheric stress or the bottom feasible stress at which it may be condensed with the to be had cooling software (Figure 1b).
In places with a prepared deliver of water, cooling is commonly done thru a closed loop that circulates thru an evaporative cooling tower.
In arid regions, along with the Middle East, North Africa, and the Southwestern U.S., air-cooled warmness exchangers are commonly extra realistic than moist cooling towers.
Power plant CSTs are normally sized in extra of a hundred MW and feature warmness fees of 11,000–16,000 Btu/kWh, relying on elements along with the stress and temperature of the inlet steam, the temperature of the cooling medium, and the turbine isentropic performance.
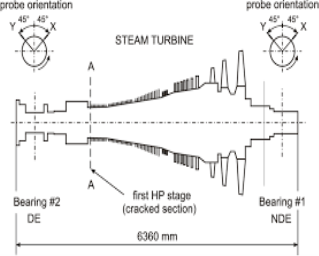
Extraction-condensing generators (ECTs) are hybrids, wherein a number of the exhaust steam is extracted at pressures excessive sufficient for method heating (cogeneration mode) and the relaxation is condensed with the aid of using a cooling software for energy technology (no cogeneration mode) (Figure 1c).
ECTs are much less not unusual place in industry, due to the fact they're extra highly-priced to shop for and hold and are extra tough to control.
They normally get hold of reasserts of inlet steam at unique pressures (e.g., excessive stress and medium stress) and exhaust at an unmarried decrease stress (e.g., ambient stress or vacuum). Figure 1d illustrates an easy case wherein an induction turbine could be appropriate.
The method is exothermic and generates extra LP steam than is wanted for method heating duties, however it desires excessive-stress (HP) steam for different higher-temperature duties.
With best steam stress levels, the desired quantity of HP steam is dispatched instantly to the tactics that want it, even as the excess exhaust from the turbine is condensed with the aid of using a cooling software for extra energy technology (no cogeneration mode).
Induction generators are even much less not unusual place than extraction generators, due to the fact they're extra highly-priced to shop for and hold and extra tough to control.
Q6) Write a short note on work done.
A6)
Work done
Everyone is aware of infant boomers with inside the electricity region have reached retirement age, that means many new hires could be thrust into technical positions in which essential records is valuable.
One such place is steam producing efficiency. It’s consequently profitable to cope with some basics of steam production.
For many people, even a few with technical backgrounds, the word “thermodynamics” evokes visions of complicated mathematics. Yet fantastically easy thermodynamic formulation give an explanation for a whole lot approximately the basics of steam generation.
Q – WS = m2[V22/2 + gz2 + u2 + P2Ï…2] – m1[V12/2 + gz1 + u1 + P1Ï…1] + dEC.V./dt
In this equation,
Q = Heat input per unit time
WS = Shaft work such as that done by a turbine per unit time
m2 = Mass flow out of the system per unit time
m1 = Mass flow into the system per unit time
(V22 – V12)/2 = Change in kinetic energy
Gz2 – gz1 = Change in potential energy
u2 = Internal energy of the exiting fluid
u1 = Internal energy of the entering fluid
P2Ï2 = Flow work of fluid as it exits the system (P = pressure, Ï… = specific volume)
P1Ï1 = Flow work of fluid as it enters the system
DEC.V./dt = Change in energy within the system per unit time
While this equation appears complicated, it is easily understood through a few definitions and simplifications. First, in many systems (especially steam generators) potential and kinetic energies are very minor compared to other energy changes and can be overlooked. Second, in a steady flow process such as in a steam generator, the system does not accumulate energy, so dEc.v./dt = 0.
Removing these terms leaves the internal energy of the fluid (u) plus its flow work (PÏ…) capabilities. Scientists have combined these two terms into the very useful property known as enthalpy (h). Enthalpy is a measure of the available energy of the fluid. Enthalpies have been calculated for a wide range of steam and saturated liquid conditions. These values may be found in the standard ASME steam tables, where saturated water at 0 C has been designated as having zero enthalpy. Using these simplifications and definitions, the energy equation for steady state operation in a turbine reduces to:
Q – WS = m(h2 – h1)
But this represents the ideal scenario and here is where the second law steps in. Among other things, the second law describes process direction. What that means is that a warm cup of coffee placed on a kitchen table does not become hotter while the room grows colder. Human beings grow old and so on. The second law has as a foundation the concept of the Carnot Cycle, which says the most efficient engine that can be constructed operates with a heat input (QH) at high temperature (TH) and a heat discharge (QL) at low temperature (TL), in which
QH/TH – QL/TL = 0
This equation represents a theoretically ideal engine. In every process known to humans, some energy losses occur. These may be due to friction, heat escaping from the system, flow disturbances or a variety of other factors. Scientists have defined a property known as entropy (s), which in its simplest terms is based on the ratio of heat transfer in a process to the temperature (Q/T). In every process, the overall entropy change of a system and its surroundings increases. So, in the real world, Equation 3 becomes
QH/TH – QL/TL < 0
While entropy may seem like a somewhat abstract term, it is of great benefit in determining process efficiency. Like enthalpy, entropy values are included in the steam tables.
Two important points should be noted about the Carnot cycle, and by logical inference all real-world processes. First, no process can be made to produce work without some extraction of heat from the process (QL) in Equation 3. QL in a conventional steam generator is heat removed in the condenser.
Second, the efficiency (η) of a Carnot engine is defined as
η = 1 – TL/TH
So, as input temperature goes up and/or exhaust temperature goes down, efficiency increases.
Q7) What is thrust and power?
A7)
- The cause of the turbine thrust bearing is to offer a fantastic axial vicinity for the turbine rotors relative to the cylinders. To obtain this, it ought to be capable of face up to the unbalanced thrusts because of blade response and steam stress performing on unbalanced regions. It ought to be loose from maintenance, besides at primary outages.
- Since it's far regularly occurring exercise to apply strong couplings among rotors, handiest one thrust bearing is needed in every whole shaft line. In operation, the pad faces are barely willing to the face of the thrust collar and the wedge-fashioned hollow space hence fashioned fills with oil. As thrust stress is applied, the wedge narrows and oil is pressured to the limited end.
- This guarantees that steel-to-steel touch among the pads and the thrust collar is prevented.
- The pads are fashioned and hooked up in order that every is capable of pivot independently. Since the feature of the thrust bearing is essential in controlling axial clearances among desk bound and rotating turbine components, unique precautions are taken to shield its integrity.
- Because of the near tolerances among the pads and the shaft collar, the oil deliver to the thrust bearing is in my view filtered. A part of the oil is fed directly to the thrust pad/shaft collar interface to hold the burden bearing oil film.
- The stability of the oil deliver is diverted round and in the back of the thrust pads to offer cooling; due to the fact that as an end result the thrust bearing runs flooded, the ensuing churning loss has additionally to be eliminated and consequently this part of the oil deliver is a good sized share of the whole.
- Thrust pad put on size is facilitated via way of means of the availability of oil stress nozzles among the white steel pads and hooked up at the thrust and surge facets of the shaft collar
- These nozzles are set at a distance barely extra from the shaft collar than the regular pad jogging clearance. A separately-filtered regular stress oil deliver is added to those nozzles and the release stress is constantly monitored.
- As pad put on takes place, the nozzle-to-collar hole is decreased and the growing nozzle discharge stress is regionally indicated and alarmed with inside the Control Room to provide indication of worn white steel thrust pads. Thrust pad temperatures are monitored via way of means of embedded thermocouples, with nearby and far flung indication and alarm facilities.
Now consider this situation from a bodily perspective. Calculations imply that the steam great on the turbine exhaust (at 1 Pisa condenser strain) is eighty two percentage. This manner 18 percentage of the steam has condensed to water. However, the closing steam takes up a selected quantity of 274.nine ft3/lbm.
The corresponding quantity of water with inside the condenser hot well is zero.016136 ft3/lbm. Thus, the condensation method reduces the fluid quantity extra than 17,000 times. The condensing steam generates the sturdy vacuum with inside the condenser, which really acts as a using pressure to drag steam via the turbine. Let’s take this idea a step in addition in Example 3.
Consider if waterside fouling or scaling (or extra air in-leakage) reasons the condenser strain of the preceding instance to growth from 1 Pisa to two Pisa.
Calculations display that the paintings output of the turbine drops from 582.four to 546.1 Btu/lbm. So, at a million lb. /hr. Steam flow, an upward thrust of one Pisawith inside the condenser backpressure equates to a lack of 36,300,000 Btu/hr or 10.6 MW of paintings. This is a number one cause why right cooling water chemical remedy and condenser overall performance tracking are critical.
Next we flip to the superheated/reheated. Although the mechanics of superheating are properly known, it's miles beneficial to talk about them in short earlier than discussing the reheated.
Consider the not unusual place drum boiler, wherein steam leaving the drum is saturated. If this steam had been to be straight away injected right into a turbine, little or no paintings could arise due to the fact the steam could straight away start condensing to water upon passage via the blades. That’s why all software steam turbines encompass super heaters.
The temperature to which steam is raised above saturation represents the diploma of superheat. A critical factor to recall is that it takes almost 1,000 Btu to transform a pound of water to a pound of steam.
As the examples with inside the preceding phase illustrated, the enthalpy of superheated steam at 1,000 tiers F is handiest round 1,500 Btu/lbm.
It ought to come as no marvel that efficiencies of fashionable software boilers are with inside the 30 percentage to 35 percentage range. Research into extra temperature- resistant superheated and reheated tube substances continues, in direct software of the equation,
η = 1 – TL/TH. That’s due to the fact water droplets will purpose extreme blade damage. The latter component is a critical foundation at the back of steam reheating and operation at excessive pressures.
Thermodynamics display that paintings and performance of a steam generator enhance with multiplied strain.
Q8) Explain dimensions and proportioning of the blades
A8)
Blade Design Procedure
Among the methodologies for wind turbine blade layout and evaluation, the BEM concept has been broadly used because of its brief calculation time and pleasant results.
This concept combines the blade factors with one-dimensional momentum concept, as certain in numerous literature.
This segment gives the BEM concept equations that have been used with inside the most desirable blade layout process on this study, which can be summarized in Figure.
In addition, it describes the general flow, consisting of the simple blade geometry layout, optimization manner for chord and twist perspective linearization, and aerodynamic overall performance evaluation process Initial Blade Geometry Design The preliminary blade geometry layout is acquired with the aid of using regarding the theoretical or best geometry and starts off evolved with the choice and location of airfoils alongside the span of the blade.
Initially, the width of all airfoils is about to the same, after which the right airfoil function is decided thru optimization. In this study, the choice of airfoils and their positioning are primarily based totally at the segment format of the NERL baseline blade.
After sections are divided alongside the span of the blade and airfoils are selected, the perspective of attack (AoA, α) of every airfoil is decided from the corresponding airfoil data. In addition, the nearby TSR (λr) is calculated in keeping with the rotor radial function (r) and best influx perspective (ϕr) of the wind for every segment (see Figure 2), as follows:
ϕr = tan−1 (2 / 3λr)
Equation (1) assumes a = 1/3 and a’ = 0 in Equation (7), i.e., the Betz limit and no wake rotation. Once the ideal inflow angle has been calculated, the chord length (cr) and twist angle (θr) of each blade section can be calculated as follows:

θr = φr – αr
Where N is the number of blades and cL is the lift coefficient to the AoA of the airfoil at section r.
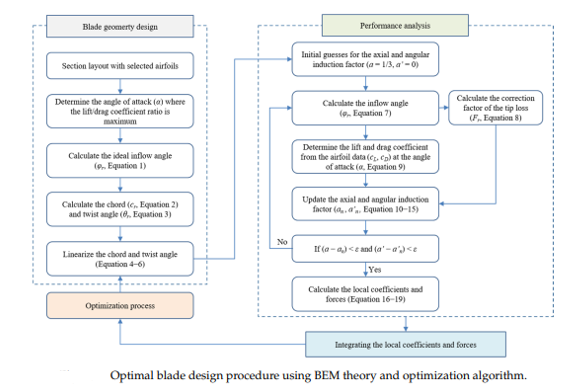
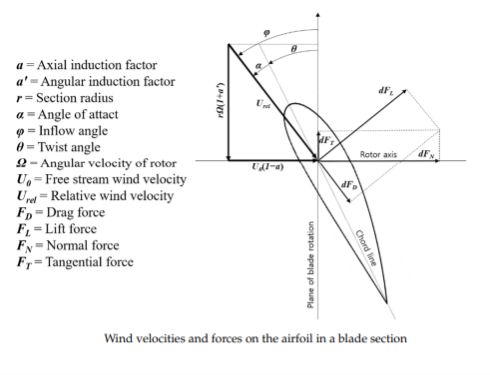
The turbine blading have to be cautiously designed with an appropriate aerodynamic form to well flip the flowing steam and generate rotational electricity efficiently.
The blades additionally must be robust sufficient to resist excessive centrifugal stresses and have to be sized to keep away from risky vibrations. Various varieties of blading preparations were proposed, however all are designed to take benefit of the precept that after a given mass of steam all of sudden adjustments its pace, a pressure is then exerted with the aid of using the mass in direct share to the charge of alternate of pace. Two varieties of blading were advanced to an excessive diploma of perfection: impulse blading and response blading.
The precept of impulse blading is illustrated with inside the schematic diagram of Figure for a primary level.
A collection of desk bound nozzles lets in the steam to extend to a decrease stress at the same time as its pace and kinetic electricity growth. The steam is then directed to the transferring passages or buckets wherein the kinetic electricity is extracted.
This additionally means that the cross-sectional location every day to the float stays constant, giving upward push to the everyday form of a symmetrical impulse blade—namely, thick on the center and sharp on the ends. Figure 1 additionally consists of the speed diagrams for any such level. Velocities are vectors which might be brought with the aid of using the parallelogram law.
The relative pace of the fluid as regards to the blade at inlet (or go out) brought vector ally to the (tangential) pace of the blade have to provide absolutely the pace as visible with the aid of using the desk bound passages.
That the kinetic electricity on the nozzle go out (proportional to the rectangular of the nozzle-leaving pace) is lots large than that on the blade go out is plain from the figure. In a really perfect impulse level, this modification of kinetic electricity is absolutely transformed into beneficial work.
For minimal go out kinetic electricity in a symmetrical impulse blade, the rotor pace need to be approximately one-1/2 of the coming into steam pace. In an idealized response level, approximately one-1/2 of the enthalpy drop in line with level is effected with inside the stator passage and the alternative 1/2 of with inside the rotor passage.
This means that the stress drop is likewise nearly identical in each the desk bound and the rotary passages, which generally tend to seem like replicate pix of every other.
If the float pace is subsonic (beneath the speed of sound with inside the fluid), an increasing passage float will growth its pace because the stress drops at the same time as the cross-sectional location decreases simultaneously, as a result main to the curved nozzle form proven in Figure 2.
Since there may be no stress drop in an idealized impulse level, stress forces at the rotor play no function on this sort of arrangement. By contrast, in a response level, the impact of the converting stress exerts an internet pressure with inside the tangential direction (as a result turning the wheel) and additionally with inside the axial direction.
The latter has a tendency to push the rotor into the ends of the casing, requiring a thrust bearing to take in the axial load. In big generators the axial load may be decreased with the aid of using admitting the steam float with inside the center and increasing in each axial directions.
Q9) Explain steam turbine efficiencies & Condition for maximum efficiencies
A9)
The performance of any turbine or engine may be described as its cap potential to transform the enter power into beneficial output power that is expressed with inside the shape of the subsequent equation.
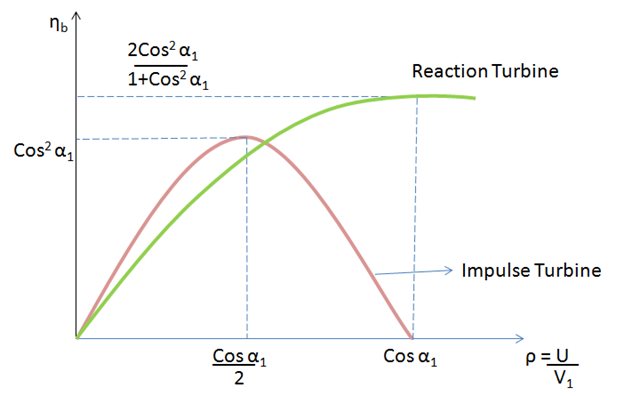
Figure: Blade efficiency of impulse and reaction steam turbine
Efficiency (ɳ) = Output / Input
A perfect turbine with 100% efficiency is the only which converts all its enter power into output paintings without dissipating power with inside the shape of warmth or some other shape. But with inside the actual world, it isn't always viable to construct a turbine with 100% efficiency due to friction with inside the components of generators, warmness loss, and different such losses.
In the case of steam generators following elements makes a decision the general performance f the turbine.
Velocity of enter steam (which in flip relies upon at the temperature and strain of steam) Angle of guiding vanes
The following figure is showing the graph of blade efficiency for both types of steam turbines. This figure is indicating that reaction turbine is more efficient than impulse turbine.
Q10) What is radius of rotor?
A10)
Radius of rotor
The electric producing performance of fashionable steam turbine electricity flora varies from an excessive of 37% HHV4 for large, electric powered application flora designed for the best realistic annual potential element, to below 10% HHV for small, easy flora which make strength as a byproduct of turning in steam to methods or district heating There are sorts of steam generators; impulse turbine and response turbine.
Both sorts of steam generators have exceptional performance because of their exceptional running standards however the performance of each sorts of steam generators is expressed through the subsequent equation.
Efficiency (ɳ) = Work done / Input Kinetic
Energy Here enter kinetic power absolutely relies upon at the absolute speed of the steam on the inlet of steam turbine however paintings achieved relies upon on plenty of things along with drop in warmness content material of steam in the turbine, the perspective of manual vanes specifically on the inlet of generators, blade angles, relative speed of steam with inside the turbine, etc.
It within reason hard to calculate paintings achieved through turbine due to these kind of elements and in a few instances it isn't always viable to appropriately calculate positive elements like speed, temperature, or strain of steam. There are methods of calculating steam performance.
These techniques referred as blade performance (ɳb) and level performance (ɳs). Blade performance is calculated the use of the speed of the steam whilst level performance is calculated through measuring adjustments with inside the enthalpy of the steam.
Enthalpy is noted the warmth content material of the steam. In each instances the perspective of manual vanes on the inlet performs a crucial function that is represented through α1. The cosine of this perspective performs the crucial function in defining the performance of each impulse and response steam turbine.
The most performance of impulse steam turbine is carried out at 0 stages perspective of inlet blades due to the fact this perspective maintains the friction on the minimal through decreasing the floor place of the blade.
It is likewise viable to hyperlink numerous generators in collection to make use of most power from steam earlier than sending it lower back to the condenser. In this sort of association level performance calculation approach works best.
A crucial factor to notice right here is that each one this dialogue did now no longer encompass the power loss in heating water and condensing steam.
Commercial industries additionally calculate efficiencies of those operations to discover the general performance of the complete setup.
Q11) Write a shot note on effective electrical efficiency
A11)
This performance is calculated through the formula
(Steam turbine electric powered electricity output) / (Total gasoline into boiler – (steam to procedure/boiler performance))
It is equal to 3,412 Btu/kWh/Net
Heat Rate and Net Heat Rate = (overall gasoline enter to the boiler – the gasoline that could require to generate the steam to procedure assuming the equal boiler performance/steam turbine electric powered output (kW)
Heat or electricity ratio is likewise a crucial element on this dialogue and it may be calculated through the formula
Power/Heat Ratio = CHP electric electricity output (Btu)/ beneficial warmness output (Btu)
Following desk 1 is displaying the listing of various overall performance traits f diverse industrial steam generators. This desk is for conventional steam/boiler CHP device with the capacities of 500kW, 3MW, and 15MW.
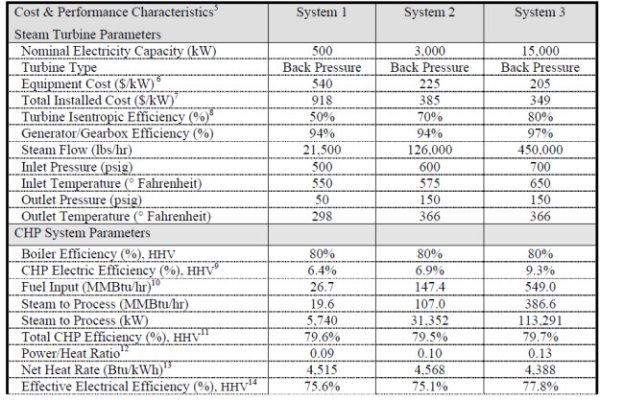
Q12) Explain reheat and regenerative cycles in detail.
A12)
Reheat and regenerative cycles
The reheat cycle will increase the turbine paintings and therefore the internet paintings of the cycle.
This is performed now no longer via way of means of converting the compressor paintings or the turbine inlet temperature however rather via way of means of dividing the turbine enlargement into or extra components with regular strain heating earlier than every enlargement.
This cycle modification, as proven in Fig. 1.8, is called reheating. By reasoning just like that utilized in reference to intercooling, it is able to be visible that the thermal performance of an easy cycle is diminished via way of means of the addition of reheating, while the paintings output is increased.
However, an aggregate of regenerator and reheated can growth the thermal performance’s Thermal sun electricity flora are just like the traditional ones with the exception that a discipline of concentrating sun creditors replaces the traditional steam boiler. In hybrid flora, a traditional boiler is likewise present, running on traditional fuel, generally herbal gas, each time there's a need.
Therefore, the thermal evaluation of sun electricity flora is just like that of some other plant and the equal thermodynamic family members are applied. The evaluation is substantially facilitated via way of means of drafting the cycle on a T-s diagram. In those cases, the inefficiencies of pump and steam turbine have to be considered.
In this section, the equations of the primary Rankin electricity cycle are given and of the extra realistic cycles, the reheat and the regenerative Rankine cycles, are analyzed thru examples. To resolve the troubles of those cycles, steam tables are required. Alternatively, the curve suits proven in Appendix five may be used.
The troubles that comply with had been solved via way of means of the use of steam tables. The intercooled and reheat cycles can every encompass regeneration to get better a number of the exhaust warmth to enhance the thermal performance of those respective cycles, and certainly there may be good sized growth with inside the thermal performance of those cycles.
The optimization of the strain ratio break up for the compressors and generators in this example could be about equal, and could correspond to the most precise paintings case.
However, it's far the inclusion of regeneration right into a blended intercooled-reheat cycle that offers the biggest development in thermal performance, and a schematic illustration of this sort of cycle
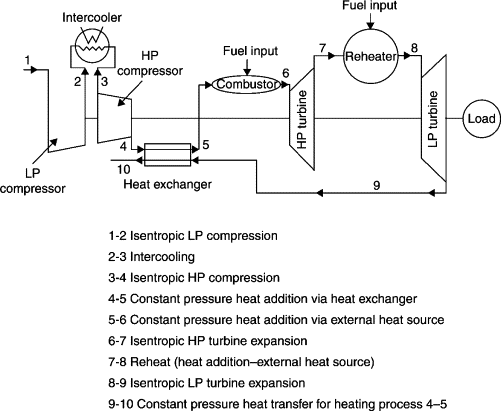
The steam energy cycle is a powerful manner to convert warmness power into mechanical power continuously.
According to the second one regulation of thermodynamics, the Carnot cycle has the best thermal performance of all cycles in a selected temperature range.
However, it is tough to comprehend the Carnot cycle whilst saturated steam is used as operating fluid.
Besides, the top restriction temperature of the saturated steam, Carnot cycle can simplest be under its vital temperature, and the lower restriction temperature can simplest be better than the ambient temperature, so the temperature distinction among them is small.
Even if the Carnot cycle with saturated steam is realized, its thermal performance isn't very high.
Therefore, the Rankine cycle has emerge as a basic cycle extensively utilized in current thermal energy flowers.
Furthermore, with the development of technology and technology, primarily based totally at the Rankine cycle, there are reheat cycle, regenerative cycle and so on.
At present, the real cycles of steam energy flowers are very complex, however they're all stepped forward primarily based totally at the number one cycle.
To preserve the energy unchanged, it is essential to growth the steam intake, therefore increasing the steam intake charge of the cycle.
With the non-stop development of parameters and energy of steam turbine generator devices in thermal energy flowers, increasingly devices undertake regenerative and steam reheat on the identical time.
As proven with inside the desk above, this improves the cycle thermal performance, exhaust dryness, and decreases the effect on steam intake charge. By evaluating the above calculation effects, we will see the need of enhancing the steam energy cycle greater intuitively.
Especially for our college students in better vocational colleges, we will higher recognize the development of financial indicators, because of the development of the steam energy cycle.
Of course, with the adoption of the reheat cycle and regenerative cycle, a sequence of thermal system want to be introduced to make the entire machine greater complex, and the funding value of system additionally desires to growth.
This desires to be measured comprehensively and brought as an entire. Besides, the calculation effects additionally confirm that the thermal performance of the cycle is normally less than 50% spite the fact that reheating and regenerative strategies are used.
Unit - 5
Energy losses in steam turbines
Q1) Write a short note on energy losses in steam turbines
A1)
Admission losses
In exercise the go with the drift of steam thru nozzle isn't isentropic, however followed with losses which lower the kinetic power of steam popping out of the nozzle.
- The lower in kinetic power is because of the subsequent reasons
- Viscous forces among steam debris
- Heat loss from steam earlier than coming into the nozzle
- Boundary layer improvement with inside the nozzle
- Turbulence with inside the nozzle
The friction with inside the nozzle which reduces to be had enthalpy drop and for this reason real pace leaving the nozzle is much less than that received with is-entropic expansion
Leakage losses
Steam leaves the boiler and reaches the condenser after passing thru the principle valve, regulating valves, nozzles, clearance areas among nozzles and shifting blades, diaphragm and rotating shaft etc.
Further there's big strain distinction among inner of steam turbine and the ambient and additionally from one area to every other area throughout those devices.
- Therefore, steam leakage takes region thru Main valve and regulating valve
- Spaces among nozzles and shifting blades
- Spaces among diaphragm and shaft of turbine
- Space among shifting blade earrings and turbine casing leakage of steam thru those is a right away lack of power.
Friction losses
Frictional resistance is obtainable all through go with the drift of steam thru nozzles on shifting and desk bound blades.
In maximum of the generators the blade wheels rotate in a area complete of steam.
The viscous friction on the wheel floor reasons admission losses as steam passes from nozzle to wheel.
The floor of curved shifting blades and desk bound blades gives resistance, which will increase with boom in roughness of blade floor and relative pace among steam and rotating blade.
The power loss additionally takes region while the steam jets turns alongside the curvature of the blade floor.
The turning losses rely on the perspective of turning.
Exhaust loss
The power content material of steam isn't completely applied with inside the turbine. Despite of being at very low strain the exhaust popping out of the turbine and coming into the condenser consists of a number of kinetic power and beneficial enthalpy, that's direct power loss.
Radiation and convection losses
The steam turbine operates at an incredibly excessive temperature; consequently a number of the warmth power of steam is radiated and convicted from the frame of the turbine to its surrounding.
These direct losses are minimized via way of means of right insulation. Losses because of moisture
The steam passing thru the remaining level of turbine has excessive pace and big moisture content material.
The liquid debris have lesser pace than that of vapor debris and for this reason the liquid debris impede the go with the drift of vapor debris with inside the remaining level of turbine and consequently, part of kinetic power of steam is lost. If the dryness fraction of steam falls beneath 0.88, the erosion and corrosion of blades also can take region.
Carry over losses
When steam passes from one level to every other thru the diaphragm, a few power losses takes region, that are called deliver over losses and consequently, the kinetic power of steam to be had at succeeding level of shifting blades for usage is much less than that of the go out at previous level.
This is because of formation of eddies in annular area among the nozzle and shifting blades.
Q2) Explain flow of steam through turbine blades
A2)
- Steam is first heated in a steam technology machine (for instance, in boilers or waste warmness restoration systems), in which it reaches an excessive temperature, round 400°C to 600°C.
- The first valve that the steam encounters because it travels from the steam technology machine to the steam turbine is the primary forestall valve (primary experience or shutdown valve), that's both completely opened and completely closed. This valve frequently does now no longer manage the steam go with the drift aside from to absolutely forestall it. Screen Shot 2016 07 29 at four 25 forty five Pm 1
- Control or throttling valves in unique preparations and configurations also are used to govern the steam inlet.
- Combined experience and throttle valves also are common. In many steam mills, as a minimum impartial experience valves need to be furnished for correct redundancy.
- These valves are right now beforehand of the steam turbine and are designed to resist the total temperature and stress of the steam. These valves are important because, if the mechanical load is misplaced, the steam turbine could swiftly over-velocity and damage itself.
- This is an occasional occurrence. An uncommon root-cause, including coupling failure, would possibly bring about this. Other injuries are possible, helping the want for 2 or 3 impartial forestall valves, which carry protection and reliability however upload price to the machine.
- Steam turbine drives are ready with throttling valves or nozzle governors to modulate steam go with the drift and obtain variable velocity operation. The steam turbine force is able to serving the equal feature as a variable velocity force electric powered motor driver.
- Steam mills can generally function throughout a vast velocity variety and do now no longer fail while overloaded.
- They additionally produce the excessive beginning torque required for regular torque masses including with fine displacement pumps or compressors.
- The steam hits the primary row of blades at pressures so excessive that it may produce torque with only a small floor area.
- The steam’s effect reasons the rotor to turn. As the steam turbine ranges progress, however, the steam loses stress and energy, therefore, requiring more and more massive floor areas.
- For this reason, the blades’ sizes boom with every level. When the steam leaves the turbine, its temperature has dropped, and it has misplaced nearly all its accelerated stress. Some of the stress drop additionally happens throughout the diaphragm, which is a part among the outer wall and internal web.
- The steam need to strike the blades at a selected perspective with the intention to maximize the beneficial paintings of the steam’s stress. This is in which nozzles come into play.
- Stationary jewelry of nozzles are located among the blade wheels to “turn” the steam on the best perspective for putting the blades. A thrust bearing is established at one cease of the primary shaft to hold its axial role and hold the transferring elements from colliding with the desk bound elements. The magazine bearing helps the primary shaft and restricts it from springing out of its casing at excessive speeds.
- An exhaust hood publications steam from the remaining level of the steam turbine, and its miles designed to reduce stress loss, which could lower the thermal performance of the steam turbine. After the steam leaves the exhaust section, it enters a condenser, in which its miles cooled to a liquid state. The technique of condensing the steam generally creates a vacuum, which then brings in greater steam from the steam turbine. The water is again to the steam technology machine, reheated and reused.
- The governor is a tool that controls the turbine’s velocity. Modern steam mills have a digital governor that makes use of sensors to display the rate with the aid of using inspecting the rotor teeth.
- To lay out a greater green steam turbine, a casing with right nozzles and vanes to restrict the steam and valves to govern the admission of steam to the nozzles need to be used.
- The thick-walled castings used for the stress-containing turbine sections are referred to as shells and are generally crafted from alloy metallic materials. Some designs encompass internal and outer shells, which serve to stability the stress drop and decrease the shell’s thickness for thermal stress, beginning and loading.
- Multistage designs are used to boom performance. The kind and range of turbine ranges and the form and length of the blades range. They are decided primarily based totally at the steam stress and temperature, the exhaust stress, and the rate.
- When the steam turbine’s rotor is desk bound, the steam flowing via the nozzle will hit the blades with complete force, exerting the finest quantity of torque. However, due to the fact that this happens at the same time as the rotor is at a standstill, the paintings achieved is 0. On the opposite hand, if the rate of the rotor is identical to that of the steam, the steam will don't have any pace element relative to the blades, and the blades will now no longer turn.
- Therefore, this example results in 0 torque and, as soon as again, 0 paintings. The most performance happens among those extremes. Proper optimization need to be achieved to attain perfect running situations and height performance.
- Because of the excessive pressures utilized in steam mills, the casing is pretty thick, and therefore steam mills show off massive thermal inertia. They need to be warmed up and cooled down slowly to reduce the differential growth among the rotating blades and the desk bound additives. Large steam mills might also additionally require about 5 to 9 hours to heat up.
- While smaller devices have greater fast begin-up instances, steam mills vary drastically from reciprocating engines, which begin up swiftly, and from fuelling mills, which could begin up in a mild quantity of time and cargo observe with affordable rapidity.
- Steam turbine packages generally function constantly for prolonged intervals of time, despite the fact that the steam fed to the unit and the mechanical electricity added might also additionally range all through such intervals of non-stop operation.
- Because maximum steam mills are decided on for packages with excessive-responsibility factors, the character in their software frequently looks after the want to have simplest sluggish temperature adjustments all through operation, and lengthy startup instances may be tolerated. Steam boilers further have lengthy startup instances.
Q3) What is reheat factor?
A3)
The Rankine Cycle geared up with a reheated may have at the least stages of steam turbine: high-strain turbine and low-strain turbine. High-strain steam turbine output steam, typically called bloodless reheat steam, has decrease strain and temperature of major steam, earlier than getting into the turbine.
Although the bloodless reheat strain drops significantly, it nevertheless has now no longer reached its saturation point. So, if this steam reheated, it'll go back to superheated steam. Therefore the bloodless reheat steam that exits the high-strain turbine, may be reheated again into the boiler. Modern boilers geared up with reheated pipes, particularly designed in order that the reheated steam soak up warmth similar to the principle steam.
The reheated steam, additionally referred to as warm warmth reheat steam, will attain the identical temperature as the principle steam vapor. To acquire this, the reheated pipes may be located now no longer some distance from the very last pipes of the superheated.
More specifically, allow us to confer with the subsequent supercritical boiler diagram. Seen in above boiler diagram, reheated pipes are divided into heating tiers.
First, the bloodless reheat steam passes thru the Low-Temperature Reheated pipes, which proven with the aid of using the name “LTRH” on the diagram. Furthermore, LTRH output steam flows to the pipes referred to as Final Reheated.
The steam produced with the aid of using the Final Reheated is then referred to as Hot Reheat steam. Hot Reheat steam then is going to the low-strain steam turbine, in order that the warmth power contained in its miles transformed into mechanical power of the turbine shaft rotation.
Theoretically, the addition of 1 level reheated usage will boom the thermal performance of the Rankine cycle with the aid of using 3–4%, the addition of tiers of the reheated will increase the performance with the aid of using 1. 5–2%, the addition of the three-level reheated will increase performance with the aid of using 0.75–1%, and so on.
Commonly, present day boiler simplest makes use of one or level re-heater.
Reheat factor = Cumulative heat drop / isentropic heat drop (Overall)
Q4) What is velocity diagram?
A4)
The picture shows steam turbine velocity diagram.
The upper portion represents the inlet condition of steam and lower portion represents the outlet portion of steam.
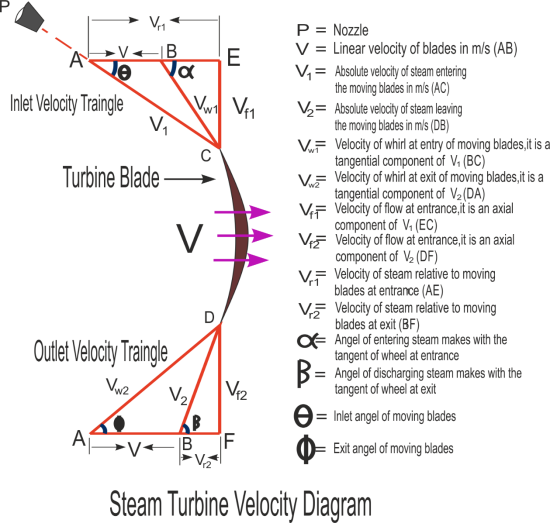
Let the steam jet is coming from nozzle P. After that it coming into a curved blade and leaving the nozzle at C. The jet glides over the internal floor and leaves the blade at D. Let us draw the steam turbine speed diagram.
Assume, it creates at a perspective a to the tangent of the wheel with a speed V1 that's absolutely the speed of steam.
This absolute speed V1 has components. One tangential thing Vw1 and any other axial thing Vf1.
Vf1 is the speed of go with the drift at entrance, so it's miles perpendicular to the path of blade's movement and it does now no longer any paintings, however that is the thing that's completely answerable for go with the drift of steam thru the turbine.
Now shifting blades begin to circulate at a tangential speed V with inside the horizontal path and the jet of steam is V1 speed create an perspective a to the a few horizontal path.
So each shifting blades and jet of steam are shifting with inside the equal path and steam input the shifting blades with a relative speed Vr which may be discovered through subtracting the V and V1 thing and count on it create a few perspective T1.
For clean flowing of steam whilst passing the shifting blades, the jet of steam input the shifting blade's tip and it additionally creates a few perspective of shifting blade T. T and T1 are equal.
When T1 and T could be equal the steam's go with the drift will easily strike the shifting blades. In real exercise T and Tthita1 is equal and that’s why we denote it T.
Similarly suffix 2 represents the opening speed of steam. Here steam leaving from shifting blades at a perspective β which makes with the tangent of the wheel with a speed V2 and its miles absolutely the speed of steam leaving of shifting blades. This speed V2 has components. One Vw2 that's tangential thing and any other is Vf2 that's axial thing.
Vw2 is the speed thing of whirl to go out and its miles the real thing for which steam leaving from the shifting blades. Vf2 is go with the drift thing and its miles answerable for speed of go with the drift of steam to go out.
The shifting blades are going for walks at horizontal path with a tangential speed V and V2 absolutely the speed of steam leaving of shifting blades create an perspective β with a relative speed Vr2 to shifting the blade to go out.
This Vr2 may be acquire through subtracting the V and V2 and it create a few perspective F1.
But for clean flowing of the steam at the same time as existing, it creates a perspective of shifting blades i.e.
Now F and F1 are equal. So, we denote it F. When F1 is same to F then steam go out easily and steadily.
Q5) Write a shot note on graphical and analytical methods
A5)
A steam turbine is a key unit in a steam strength plant from which we get strength.
A steam turbine is a faster system and a top mover wherein strength of stem is converted into kinetic strength and this kinetic strength is then converted into mechanical strength of rotation of shaft of turbine.
The cutting-edge steam turbine changed into invented in 1884 via way of means of Sir Charles Parsons, whose first model changed into related to a dynamo that generated 7.five kW (10 hp) of electricity.
The Parsons turbine additionally grew to become out to be smooth to scale up. Parsons had the pride of seeing his invention followed for all predominant global strength stations, and the scale of mills had extended from his first 7.5 kW installation to devices of 500MW capacity.
Steam mills are essential additives of technique plant application systems.
They provide possibilities for optimizing steam deliver reliability, in addition to site-extensive strength efficiency.
Steam mills are maximum not unusual place with inside the oil refining, ammonia and urea, methanol, ethylene, and pulp and paper industries, in which they may be normally sized to provide 10–60 MW of strength.
Good economics also are feasible at smaller sizes as little as 2 MW, which can be greater not unusual place with inside the meals and beverage industries, in addition to in small to medium-sized flora with inside the chemical technique industries (CPI).
Achieving favorable steam turbine economics relies upon on selecting the proper sort of turbine (e.g., backpressure vs. Condensing) with inside the proper size, in addition to integrating it successfully with the warmth exchanger network (HEN) according with the ideal placement precept of pinch analysis.
This article critiques the thermodynamic relationships and equations that hyperlink steam float situations and strength output, which can be beneficial for estimating initial economics of recent mills and studying the overall performance of present devices.
Backpressure steam generators (BPSTs) produce low-stress (LP) exhaust steam that may be used for one or extra method heating duties (Figure 1a). The targets are to offer the method with steam of the amount and stress required with the aid of using the method, even as producing the most quantity of energy which will lessen the want for bought energy. Because BPSTs cogenerate electricity products (i.e., steam and energy) simultaneously, they have got a powerful warmness charge of 4,500–5,500 Btu/kWh, which represents an electricity performance to 3 instances higher than that of a condensing turbine, even after deliberating each boiler and turbine electricity losses.
(Heat charge is the quantity of gasoline this is transformed with the aid of using a warmness engine into beneficial energy — the decrease the number, the higher.
The minimal feasible warmness charge is 3,413 Btu/kWh, representing a hundred% conversion of gasoline electricity into energy.)
Pure BPSTs are used typically in commercial centers that perform continuously, wherein the intention is excessive thermodynamic performance and the electricity needs are notably stable.
They are normally sized for 3–60 MW. Condensing steam generators (CSTs) exhaust steam to a condenser at atmospheric stress or the bottom feasible stress at which it may be condensed with the to be had cooling software (Figure 1b).
In places with a prepared deliver of water, cooling is commonly done thru a closed loop that circulates thru an evaporative cooling tower.
In arid regions, along with the Middle East, North Africa, and the Southwestern U.S., air-cooled warmness exchangers are commonly extra realistic than moist cooling towers.
Power plant CSTs are normally sized in extra of a hundred MW and feature warmness fees of 11,000–16,000 Btu/kWh, relying on elements along with the stress and temperature of the inlet steam, the temperature of the cooling medium, and the turbine isentropic performance.
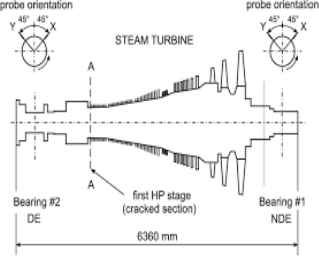
Extraction-condensing generators (ECTs) are hybrids, wherein a number of the exhaust steam is extracted at pressures excessive sufficient for method heating (cogeneration mode) and the relaxation is condensed with the aid of using a cooling software for energy technology (no cogeneration mode) (Figure 1c).
ECTs are much less not unusual place in industry, due to the fact they're extra highly-priced to shop for and hold and are extra tough to control.
They normally get hold of reasserts of inlet steam at unique pressures (e.g., excessive stress and medium stress) and exhaust at an unmarried decrease stress (e.g., ambient stress or vacuum). Figure 1d illustrates an easy case wherein an induction turbine could be appropriate.
The method is exothermic and generates extra LP steam than is wanted for method heating duties, however it desires excessive-stress (HP) steam for different higher-temperature duties.
With best steam stress levels, the desired quantity of HP steam is dispatched instantly to the tactics that want it, even as the excess exhaust from the turbine is condensed with the aid of using a cooling software for extra energy technology (no cogeneration mode).
Induction generators are even much less not unusual place than extraction generators, due to the fact they're extra highly-priced to shop for and hold and extra tough to control.
Q6) Write a short note on work done.
A6)
Work done
Everyone is aware of infant boomers with inside the electricity region have reached retirement age, that means many new hires could be thrust into technical positions in which essential records is valuable.
One such place is steam producing efficiency. It’s consequently profitable to cope with some basics of steam production.
For many people, even a few with technical backgrounds, the word “thermodynamics” evokes visions of complicated mathematics. Yet fantastically easy thermodynamic formulation give an explanation for a whole lot approximately the basics of steam generation.
Q – WS = m2[V22/2 + gz2 + u2 + P2Ï…2] – m1[V12/2 + gz1 + u1 + P1Ï…1] + dEC.V./dt
In this equation,
Q = Heat input per unit time
WS = Shaft work such as that done by a turbine per unit time
m2 = Mass flow out of the system per unit time
m1 = Mass flow into the system per unit time
(V22 – V12)/2 = Change in kinetic energy
Gz2 – gz1 = Change in potential energy
u2 = Internal energy of the exiting fluid
u1 = Internal energy of the entering fluid
P2Ï2 = Flow work of fluid as it exits the system (P = pressure, Ï… = specific volume)
P1Ï1 = Flow work of fluid as it enters the system
DEC.V./dt = Change in energy within the system per unit time
While this equation appears complicated, it is easily understood through a few definitions and simplifications. First, in many systems (especially steam generators) potential and kinetic energies are very minor compared to other energy changes and can be overlooked. Second, in a steady flow process such as in a steam generator, the system does not accumulate energy, so dEc.v./dt = 0.
Removing these terms leaves the internal energy of the fluid (u) plus its flow work (PÏ…) capabilities. Scientists have combined these two terms into the very useful property known as enthalpy (h). Enthalpy is a measure of the available energy of the fluid. Enthalpies have been calculated for a wide range of steam and saturated liquid conditions. These values may be found in the standard ASME steam tables, where saturated water at 0 C has been designated as having zero enthalpy. Using these simplifications and definitions, the energy equation for steady state operation in a turbine reduces to:
Q – WS = m(h2 – h1)
But this represents the ideal scenario and here is where the second law steps in. Among other things, the second law describes process direction. What that means is that a warm cup of coffee placed on a kitchen table does not become hotter while the room grows colder. Human beings grow old and so on. The second law has as a foundation the concept of the Carnot Cycle, which says the most efficient engine that can be constructed operates with a heat input (QH) at high temperature (TH) and a heat discharge (QL) at low temperature (TL), in which
QH/TH – QL/TL = 0
This equation represents a theoretically ideal engine. In every process known to humans, some energy losses occur. These may be due to friction, heat escaping from the system, flow disturbances or a variety of other factors. Scientists have defined a property known as entropy (s), which in its simplest terms is based on the ratio of heat transfer in a process to the temperature (Q/T). In every process, the overall entropy change of a system and its surroundings increases. So, in the real world, Equation 3 becomes
QH/TH – QL/TL < 0
While entropy may seem like a somewhat abstract term, it is of great benefit in determining process efficiency. Like enthalpy, entropy values are included in the steam tables.
Two important points should be noted about the Carnot cycle, and by logical inference all real-world processes. First, no process can be made to produce work without some extraction of heat from the process (QL) in Equation 3. QL in a conventional steam generator is heat removed in the condenser.
Second, the efficiency (η) of a Carnot engine is defined as
η = 1 – TL/TH
So, as input temperature goes up and/or exhaust temperature goes down, efficiency increases.
Q7) What is thrust and power?
A7)
- The cause of the turbine thrust bearing is to offer a fantastic axial vicinity for the turbine rotors relative to the cylinders. To obtain this, it ought to be capable of face up to the unbalanced thrusts because of blade response and steam stress performing on unbalanced regions. It ought to be loose from maintenance, besides at primary outages.
- Since it's far regularly occurring exercise to apply strong couplings among rotors, handiest one thrust bearing is needed in every whole shaft line. In operation, the pad faces are barely willing to the face of the thrust collar and the wedge-fashioned hollow space hence fashioned fills with oil. As thrust stress is applied, the wedge narrows and oil is pressured to the limited end.
- This guarantees that steel-to-steel touch among the pads and the thrust collar is prevented.
- The pads are fashioned and hooked up in order that every is capable of pivot independently. Since the feature of the thrust bearing is essential in controlling axial clearances among desk bound and rotating turbine components, unique precautions are taken to shield its integrity.
- Because of the near tolerances among the pads and the shaft collar, the oil deliver to the thrust bearing is in my view filtered. A part of the oil is fed directly to the thrust pad/shaft collar interface to hold the burden bearing oil film.
- The stability of the oil deliver is diverted round and in the back of the thrust pads to offer cooling; due to the fact that as an end result the thrust bearing runs flooded, the ensuing churning loss has additionally to be eliminated and consequently this part of the oil deliver is a good sized share of the whole.
- Thrust pad put on size is facilitated via way of means of the availability of oil stress nozzles among the white steel pads and hooked up at the thrust and surge facets of the shaft collar
- These nozzles are set at a distance barely extra from the shaft collar than the regular pad jogging clearance. A separately-filtered regular stress oil deliver is added to those nozzles and the release stress is constantly monitored.
- As pad put on takes place, the nozzle-to-collar hole is decreased and the growing nozzle discharge stress is regionally indicated and alarmed with inside the Control Room to provide indication of worn white steel thrust pads. Thrust pad temperatures are monitored via way of means of embedded thermocouples, with nearby and far flung indication and alarm facilities.
Now consider this situation from a bodily perspective. Calculations imply that the steam great on the turbine exhaust (at 1 Pisa condenser strain) is eighty two percentage. This manner 18 percentage of the steam has condensed to water. However, the closing steam takes up a selected quantity of 274.nine ft3/lbm.
The corresponding quantity of water with inside the condenser hot well is zero.016136 ft3/lbm. Thus, the condensation method reduces the fluid quantity extra than 17,000 times. The condensing steam generates the sturdy vacuum with inside the condenser, which really acts as a using pressure to drag steam via the turbine. Let’s take this idea a step in addition in Example 3.
Consider if waterside fouling or scaling (or extra air in-leakage) reasons the condenser strain of the preceding instance to growth from 1 Pisa to two Pisa.
Calculations display that the paintings output of the turbine drops from 582.four to 546.1 Btu/lbm. So, at a million lb. /hr. Steam flow, an upward thrust of one Pisawith inside the condenser backpressure equates to a lack of 36,300,000 Btu/hr or 10.6 MW of paintings. This is a number one cause why right cooling water chemical remedy and condenser overall performance tracking are critical.
Next we flip to the superheated/reheated. Although the mechanics of superheating are properly known, it's miles beneficial to talk about them in short earlier than discussing the reheated.
Consider the not unusual place drum boiler, wherein steam leaving the drum is saturated. If this steam had been to be straight away injected right into a turbine, little or no paintings could arise due to the fact the steam could straight away start condensing to water upon passage via the blades. That’s why all software steam turbines encompass super heaters.
The temperature to which steam is raised above saturation represents the diploma of superheat. A critical factor to recall is that it takes almost 1,000 Btu to transform a pound of water to a pound of steam.
As the examples with inside the preceding phase illustrated, the enthalpy of superheated steam at 1,000 tiers F is handiest round 1,500 Btu/lbm.
It ought to come as no marvel that efficiencies of fashionable software boilers are with inside the 30 percentage to 35 percentage range. Research into extra temperature- resistant superheated and reheated tube substances continues, in direct software of the equation,
η = 1 – TL/TH. That’s due to the fact water droplets will purpose extreme blade damage. The latter component is a critical foundation at the back of steam reheating and operation at excessive pressures.
Thermodynamics display that paintings and performance of a steam generator enhance with multiplied strain.
Q8) Explain dimensions and proportioning of the blades
A8)
Blade Design Procedure
Among the methodologies for wind turbine blade layout and evaluation, the BEM concept has been broadly used because of its brief calculation time and pleasant results.
This concept combines the blade factors with one-dimensional momentum concept, as certain in numerous literature.
This segment gives the BEM concept equations that have been used with inside the most desirable blade layout process on this study, which can be summarized in Figure.
In addition, it describes the general flow, consisting of the simple blade geometry layout, optimization manner for chord and twist perspective linearization, and aerodynamic overall performance evaluation process Initial Blade Geometry Design The preliminary blade geometry layout is acquired with the aid of using regarding the theoretical or best geometry and starts off evolved with the choice and location of airfoils alongside the span of the blade.
Initially, the width of all airfoils is about to the same, after which the right airfoil function is decided thru optimization. In this study, the choice of airfoils and their positioning are primarily based totally at the segment format of the NERL baseline blade.
After sections are divided alongside the span of the blade and airfoils are selected, the perspective of attack (AoA, α) of every airfoil is decided from the corresponding airfoil data. In addition, the nearby TSR (λr) is calculated in keeping with the rotor radial function (r) and best influx perspective (ϕr) of the wind for every segment (see Figure 2), as follows:
ϕr = tan−1 (2 / 3λr)
Equation (1) assumes a = 1/3 and a’ = 0 in Equation (7), i.e., the Betz limit and no wake rotation. Once the ideal inflow angle has been calculated, the chord length (cr) and twist angle (θr) of each blade section can be calculated as follows:

θr = φr – αr
Where N is the number of blades and cL is the lift coefficient to the AoA of the airfoil at section r.
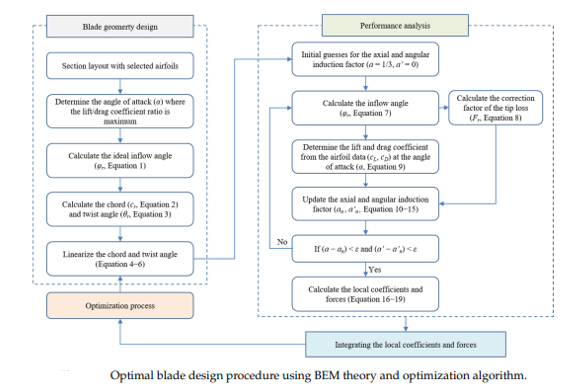
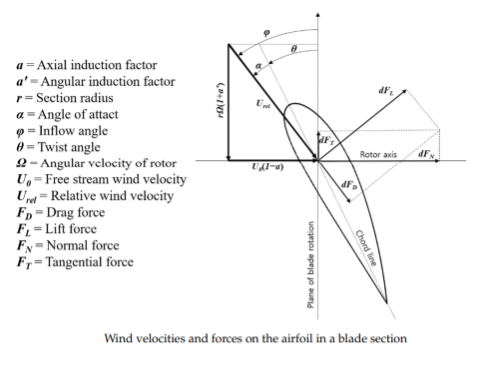
The turbine blading have to be cautiously designed with an appropriate aerodynamic form to well flip the flowing steam and generate rotational electricity efficiently.
The blades additionally must be robust sufficient to resist excessive centrifugal stresses and have to be sized to keep away from risky vibrations. Various varieties of blading preparations were proposed, however all are designed to take benefit of the precept that after a given mass of steam all of sudden adjustments its pace, a pressure is then exerted with the aid of using the mass in direct share to the charge of alternate of pace. Two varieties of blading were advanced to an excessive diploma of perfection: impulse blading and response blading.
The precept of impulse blading is illustrated with inside the schematic diagram of Figure for a primary level.
A collection of desk bound nozzles lets in the steam to extend to a decrease stress at the same time as its pace and kinetic electricity growth. The steam is then directed to the transferring passages or buckets wherein the kinetic electricity is extracted.
This additionally means that the cross-sectional location every day to the float stays constant, giving upward push to the everyday form of a symmetrical impulse blade—namely, thick on the center and sharp on the ends. Figure 1 additionally consists of the speed diagrams for any such level. Velocities are vectors which might be brought with the aid of using the parallelogram law.
The relative pace of the fluid as regards to the blade at inlet (or go out) brought vector ally to the (tangential) pace of the blade have to provide absolutely the pace as visible with the aid of using the desk bound passages.
That the kinetic electricity on the nozzle go out (proportional to the rectangular of the nozzle-leaving pace) is lots large than that on the blade go out is plain from the figure. In a really perfect impulse level, this modification of kinetic electricity is absolutely transformed into beneficial work.
For minimal go out kinetic electricity in a symmetrical impulse blade, the rotor pace need to be approximately one-1/2 of the coming into steam pace. In an idealized response level, approximately one-1/2 of the enthalpy drop in line with level is effected with inside the stator passage and the alternative 1/2 of with inside the rotor passage.
This means that the stress drop is likewise nearly identical in each the desk bound and the rotary passages, which generally tend to seem like replicate pix of every other.
If the float pace is subsonic (beneath the speed of sound with inside the fluid), an increasing passage float will growth its pace because the stress drops at the same time as the cross-sectional location decreases simultaneously, as a result main to the curved nozzle form proven in Figure 2.
Since there may be no stress drop in an idealized impulse level, stress forces at the rotor play no function on this sort of arrangement. By contrast, in a response level, the impact of the converting stress exerts an internet pressure with inside the tangential direction (as a result turning the wheel) and additionally with inside the axial direction.
The latter has a tendency to push the rotor into the ends of the casing, requiring a thrust bearing to take in the axial load. In big generators the axial load may be decreased with the aid of using admitting the steam float with inside the center and increasing in each axial directions.
Q9) Explain steam turbine efficiencies & Condition for maximum efficiencies
A9)
The performance of any turbine or engine may be described as its cap potential to transform the enter power into beneficial output power that is expressed with inside the shape of the subsequent equation.
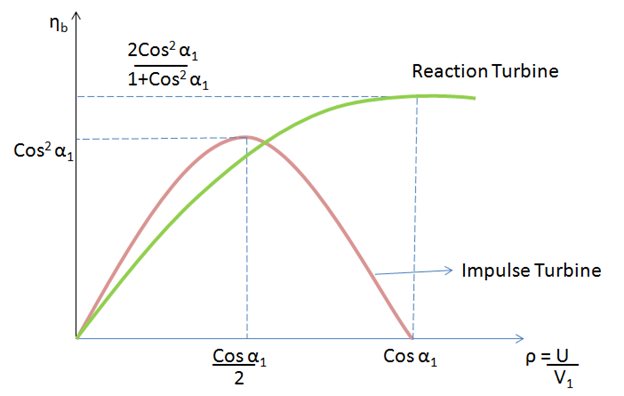
Figure: Blade efficiency of impulse and reaction steam turbine
Efficiency (ɳ) = Output / Input
A perfect turbine with 100% efficiency is the only which converts all its enter power into output paintings without dissipating power with inside the shape of warmth or some other shape. But with inside the actual world, it isn't always viable to construct a turbine with 100% efficiency due to friction with inside the components of generators, warmness loss, and different such losses.
In the case of steam generators following elements makes a decision the general performance f the turbine.
Velocity of enter steam (which in flip relies upon at the temperature and strain of steam) Angle of guiding vanes
The following figure is showing the graph of blade efficiency for both types of steam turbines. This figure is indicating that reaction turbine is more efficient than impulse turbine.
Q10) What is radius of rotor?
A10)
Radius of rotor
The electric producing performance of fashionable steam turbine electricity flora varies from an excessive of 37% HHV4 for large, electric powered application flora designed for the best realistic annual potential element, to below 10% HHV for small, easy flora which make strength as a byproduct of turning in steam to methods or district heating There are sorts of steam generators; impulse turbine and response turbine.
Both sorts of steam generators have exceptional performance because of their exceptional running standards however the performance of each sorts of steam generators is expressed through the subsequent equation.
Efficiency (ɳ) = Work done / Input Kinetic
Energy Here enter kinetic power absolutely relies upon at the absolute speed of the steam on the inlet of steam turbine however paintings achieved relies upon on plenty of things along with drop in warmness content material of steam in the turbine, the perspective of manual vanes specifically on the inlet of generators, blade angles, relative speed of steam with inside the turbine, etc.
It within reason hard to calculate paintings achieved through turbine due to these kind of elements and in a few instances it isn't always viable to appropriately calculate positive elements like speed, temperature, or strain of steam. There are methods of calculating steam performance.
These techniques referred as blade performance (ɳb) and level performance (ɳs). Blade performance is calculated the use of the speed of the steam whilst level performance is calculated through measuring adjustments with inside the enthalpy of the steam.
Enthalpy is noted the warmth content material of the steam. In each instances the perspective of manual vanes on the inlet performs a crucial function that is represented through α1. The cosine of this perspective performs the crucial function in defining the performance of each impulse and response steam turbine.
The most performance of impulse steam turbine is carried out at 0 stages perspective of inlet blades due to the fact this perspective maintains the friction on the minimal through decreasing the floor place of the blade.
It is likewise viable to hyperlink numerous generators in collection to make use of most power from steam earlier than sending it lower back to the condenser. In this sort of association level performance calculation approach works best.
A crucial factor to notice right here is that each one this dialogue did now no longer encompass the power loss in heating water and condensing steam.
Commercial industries additionally calculate efficiencies of those operations to discover the general performance of the complete setup.
Q11) Write a shot note on effective electrical efficiency
A11)
This performance is calculated through the formula
(Steam turbine electric powered electricity output) / (Total gasoline into boiler – (steam to procedure/boiler performance))
It is equal to 3,412 Btu/kWh/Net
Heat Rate and Net Heat Rate = (overall gasoline enter to the boiler – the gasoline that could require to generate the steam to procedure assuming the equal boiler performance/steam turbine electric powered output (kW)
Heat or electricity ratio is likewise a crucial element on this dialogue and it may be calculated through the formula
Power/Heat Ratio = CHP electric electricity output (Btu)/ beneficial warmness output (Btu)
Following desk 1 is displaying the listing of various overall performance traits f diverse industrial steam generators. This desk is for conventional steam/boiler CHP device with the capacities of 500kW, 3MW, and 15MW.
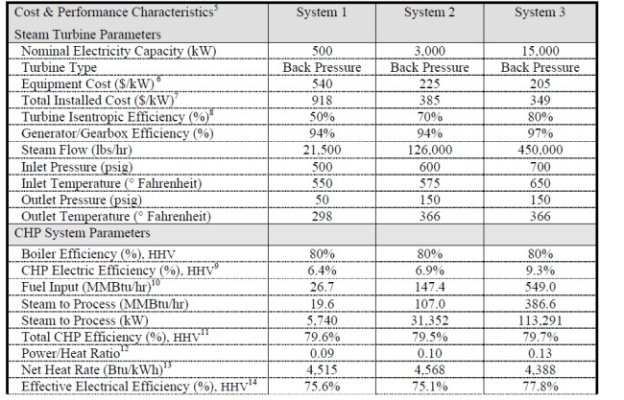
Q12) Explain reheat and regenerative cycles in detail.
A12)
Reheat and regenerative cycles
The reheat cycle will increase the turbine paintings and therefore the internet paintings of the cycle.
This is performed now no longer via way of means of converting the compressor paintings or the turbine inlet temperature however rather via way of means of dividing the turbine enlargement into or extra components with regular strain heating earlier than every enlargement.
This cycle modification, as proven in Fig. 1.8, is called reheating. By reasoning just like that utilized in reference to intercooling, it is able to be visible that the thermal performance of an easy cycle is diminished via way of means of the addition of reheating, while the paintings output is increased.
However, an aggregate of regenerator and reheated can growth the thermal performance’s Thermal sun electricity flora are just like the traditional ones with the exception that a discipline of concentrating sun creditors replaces the traditional steam boiler. In hybrid flora, a traditional boiler is likewise present, running on traditional fuel, generally herbal gas, each time there's a need.
Therefore, the thermal evaluation of sun electricity flora is just like that of some other plant and the equal thermodynamic family members are applied. The evaluation is substantially facilitated via way of means of drafting the cycle on a T-s diagram. In those cases, the inefficiencies of pump and steam turbine have to be considered.
In this section, the equations of the primary Rankin electricity cycle are given and of the extra realistic cycles, the reheat and the regenerative Rankine cycles, are analyzed thru examples. To resolve the troubles of those cycles, steam tables are required. Alternatively, the curve suits proven in Appendix five may be used.
The troubles that comply with had been solved via way of means of the use of steam tables. The intercooled and reheat cycles can every encompass regeneration to get better a number of the exhaust warmth to enhance the thermal performance of those respective cycles, and certainly there may be good sized growth with inside the thermal performance of those cycles.
The optimization of the strain ratio break up for the compressors and generators in this example could be about equal, and could correspond to the most precise paintings case.
However, it's far the inclusion of regeneration right into a blended intercooled-reheat cycle that offers the biggest development in thermal performance, and a schematic illustration of this sort of cycle
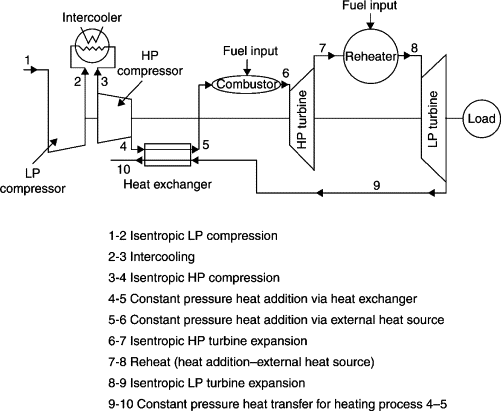
The steam energy cycle is a powerful manner to convert warmness power into mechanical power continuously.
According to the second one regulation of thermodynamics, the Carnot cycle has the best thermal performance of all cycles in a selected temperature range.
However, it is tough to comprehend the Carnot cycle whilst saturated steam is used as operating fluid.
Besides, the top restriction temperature of the saturated steam, Carnot cycle can simplest be under its vital temperature, and the lower restriction temperature can simplest be better than the ambient temperature, so the temperature distinction among them is small.
Even if the Carnot cycle with saturated steam is realized, its thermal performance isn't very high.
Therefore, the Rankine cycle has emerge as a basic cycle extensively utilized in current thermal energy flowers.
Furthermore, with the development of technology and technology, primarily based totally at the Rankine cycle, there are reheat cycle, regenerative cycle and so on.
At present, the real cycles of steam energy flowers are very complex, however they're all stepped forward primarily based totally at the number one cycle.
To preserve the energy unchanged, it is essential to growth the steam intake, therefore increasing the steam intake charge of the cycle.
With the non-stop development of parameters and energy of steam turbine generator devices in thermal energy flowers, increasingly devices undertake regenerative and steam reheat on the identical time.
As proven with inside the desk above, this improves the cycle thermal performance, exhaust dryness, and decreases the effect on steam intake charge. By evaluating the above calculation effects, we will see the need of enhancing the steam energy cycle greater intuitively.
Especially for our college students in better vocational colleges, we will higher recognize the development of financial indicators, because of the development of the steam energy cycle.
Of course, with the adoption of the reheat cycle and regenerative cycle, a sequence of thermal system want to be introduced to make the entire machine greater complex, and the funding value of system additionally desires to growth.
This desires to be measured comprehensively and brought as an entire. Besides, the calculation effects additionally confirm that the thermal performance of the cycle is normally less than 50% spite the fact that reheating and regenerative strategies are used.