Unit - 2
Transformer Design: Part 2
Q1) A 250 kVA, 6600/400 V, 3 phase core type transformer has total loss of 4800 W at full load. The transformer tank is 1.25 m in ht and 1m×0.5m in plan. Design a suitable scheme for tubes if average temp rise is to be limited to 35 oC. The diameter of tubes is 50 mm and are spaced 75 mm from each other. The average ht of tubes is 1.05 m.
So heat dissipation due to radiation and convection is respectively 6 and 6.5. Assume that convection is improved by 85% to provision of tubes.
A1)
Area of plane tank, St = 2(1+0.5)×1.25 = 3.75 m2
Let tube area be x.St
Total dissipating surface = 3.75(1+x)
Specific loss dissipation =
From eqn of loss dissipated =
Or x = 2.73
Area of tube = 2.73×3.75 = 10.23 m2
Wall area of each tube =
= = 0.165 m2
Total no of tubes = 10.23/0.165 = 62
Q2)

A2)
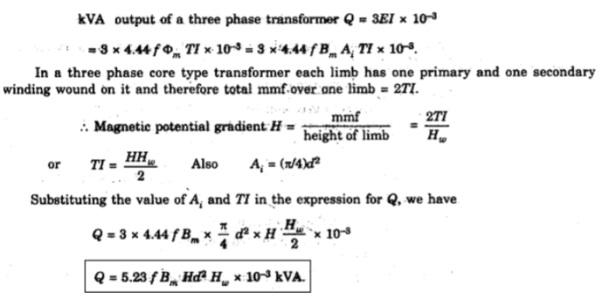
Q3)
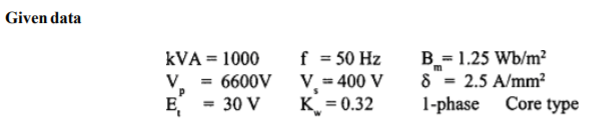
A3)
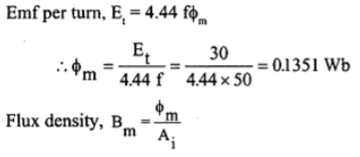
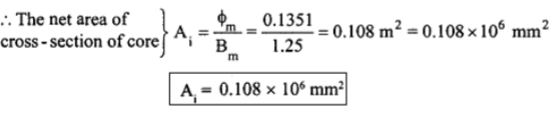
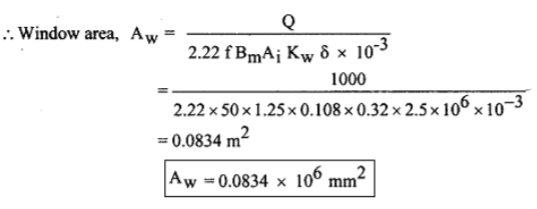
Q4)
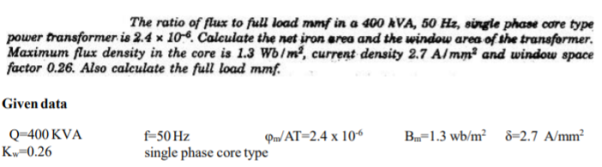
A4)
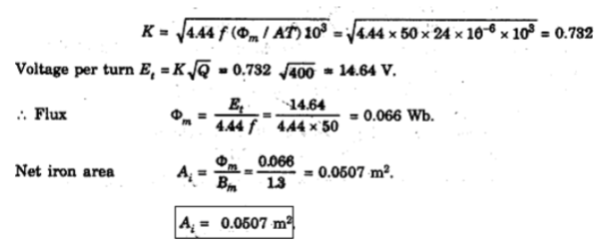
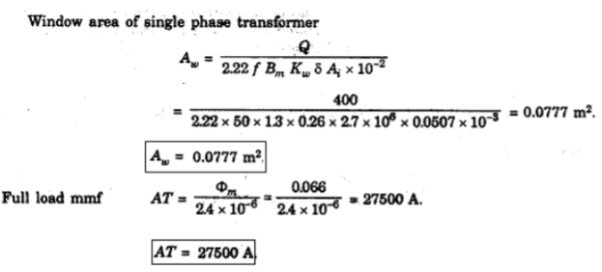
Q5)

A5)
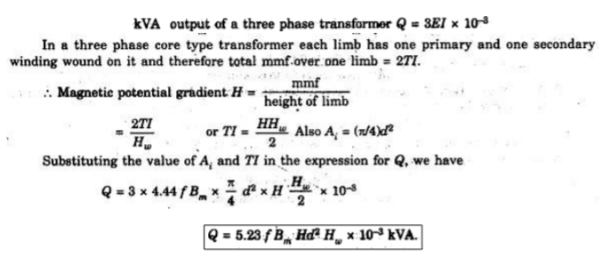
Q6)
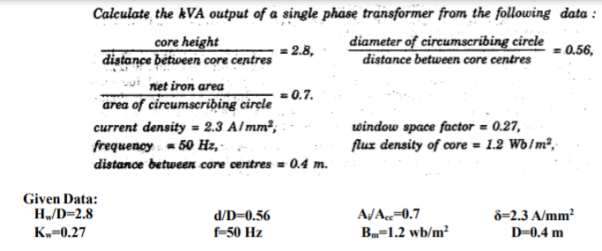
A6)
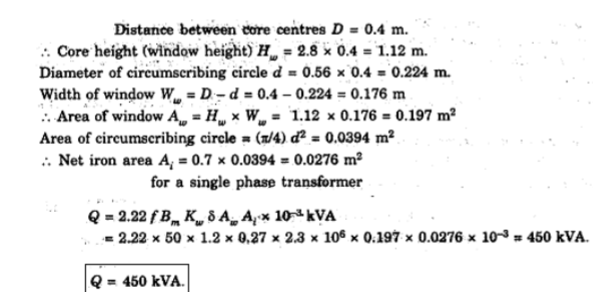
Q7)
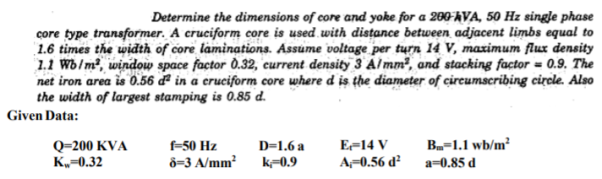
A7)
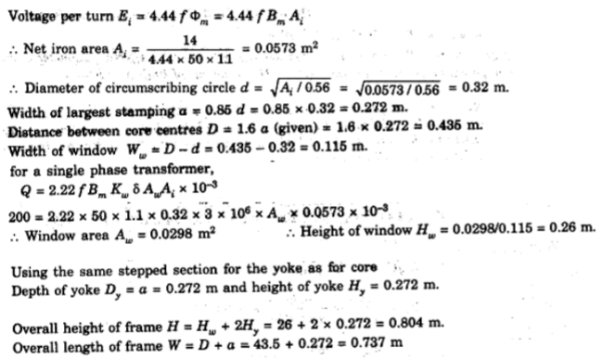
Q8)
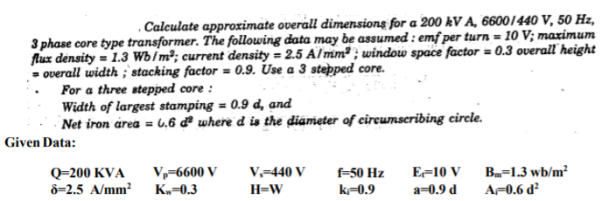
A8)
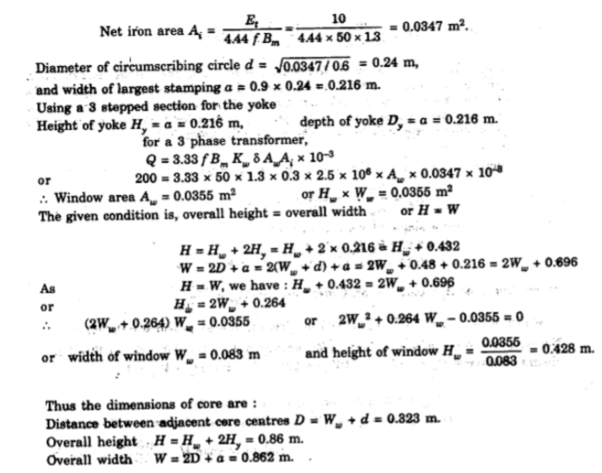
Q9)
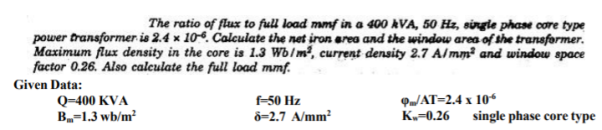
A9)
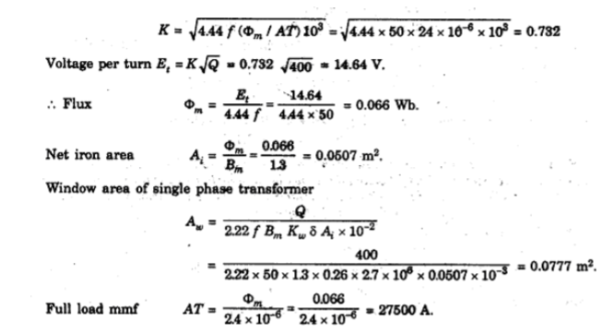
Q10)
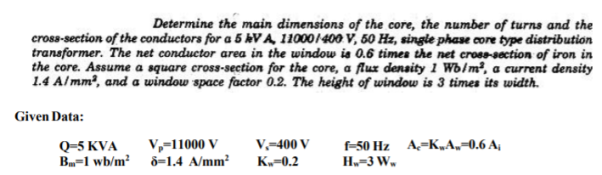
A10)
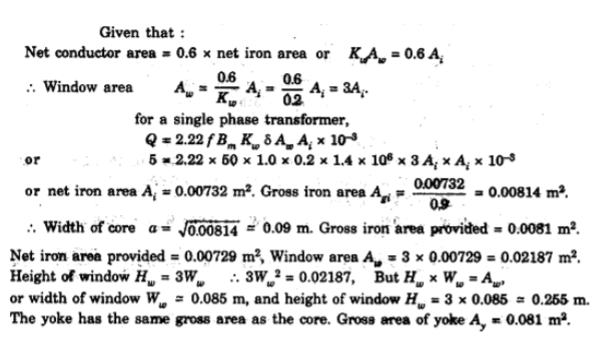
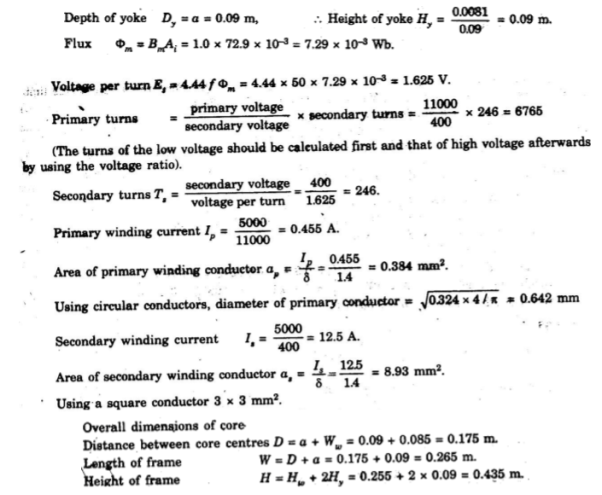
Q11)
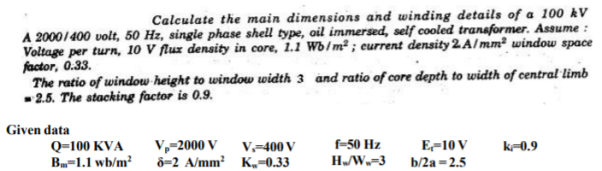
A11)
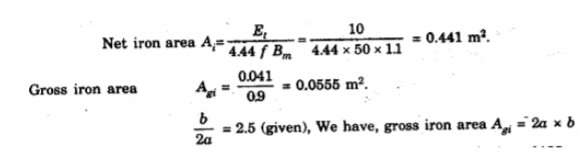
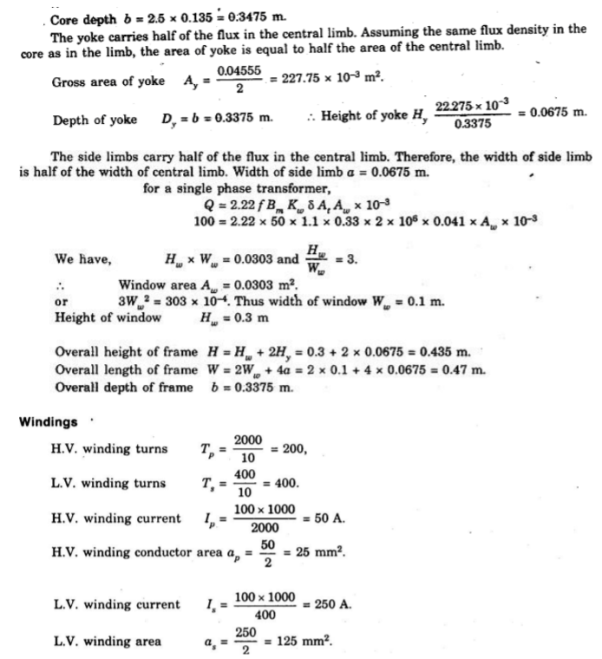
Q12)
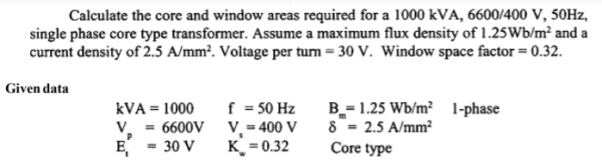
A12)
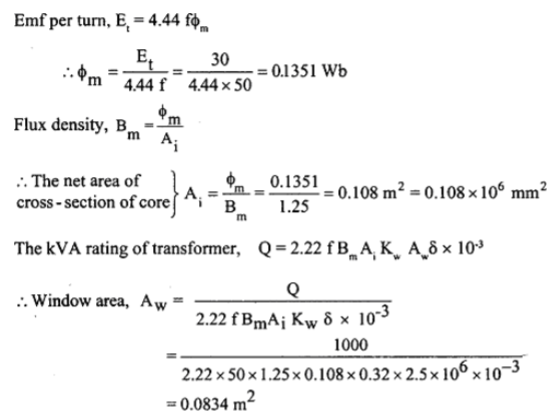
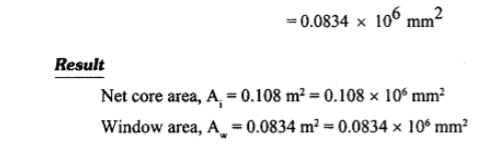
Q13)
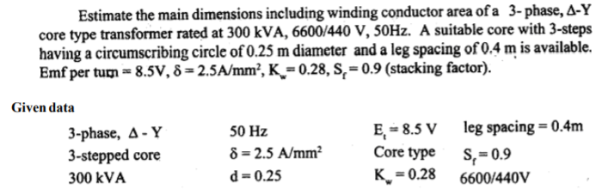
A13)

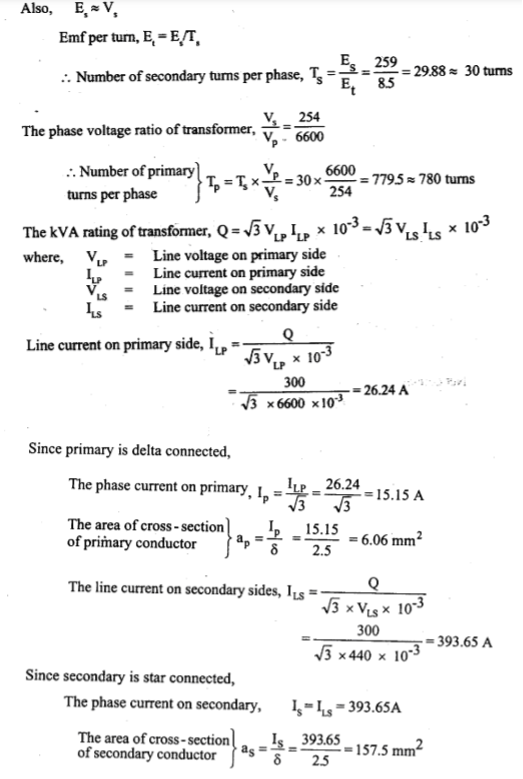
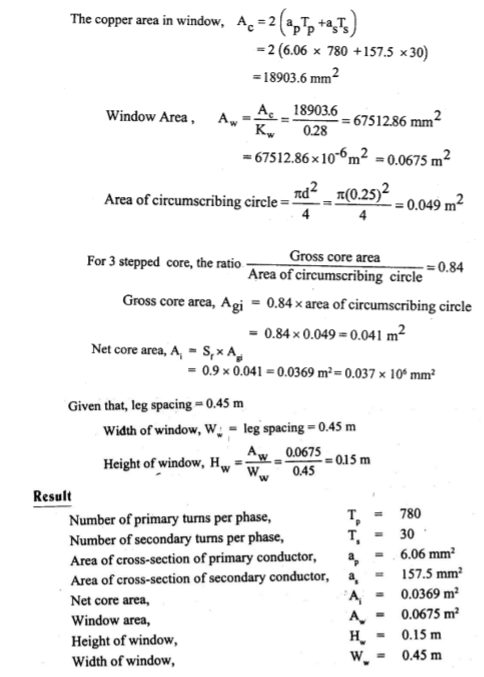
Q14)


A14)
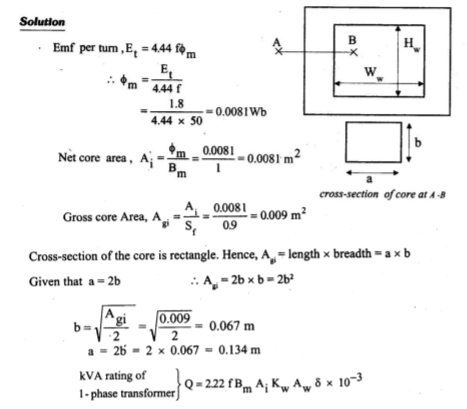
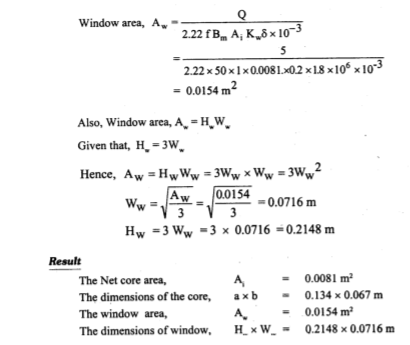
Q15)
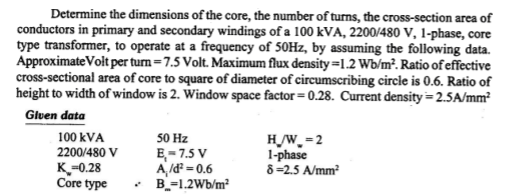
A15)
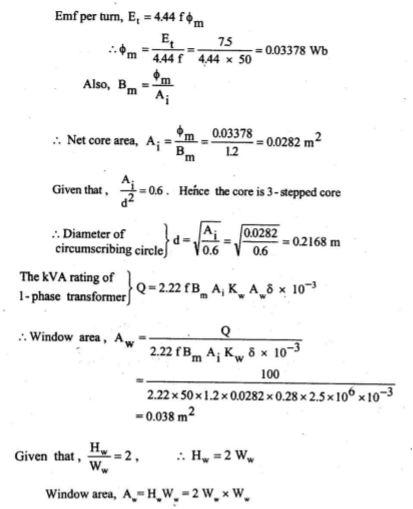
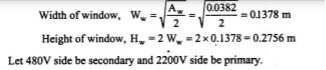
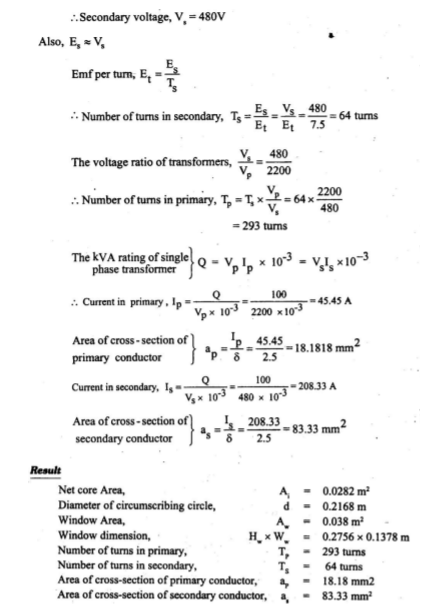
Q16)
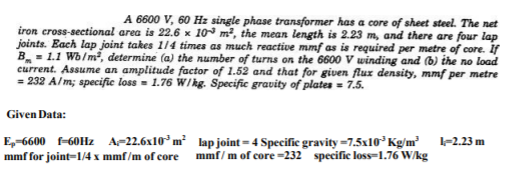
A16)
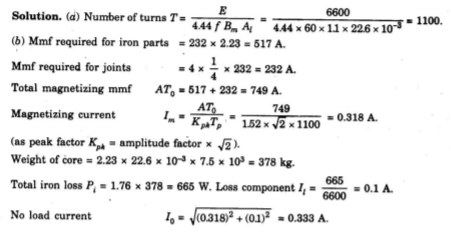
Q17)
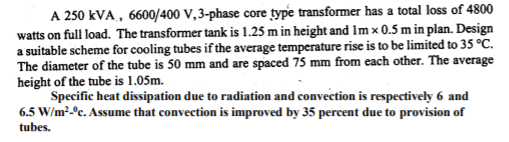
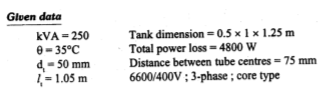
A17)
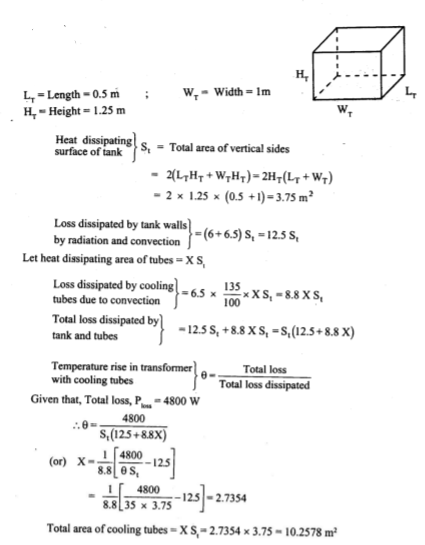
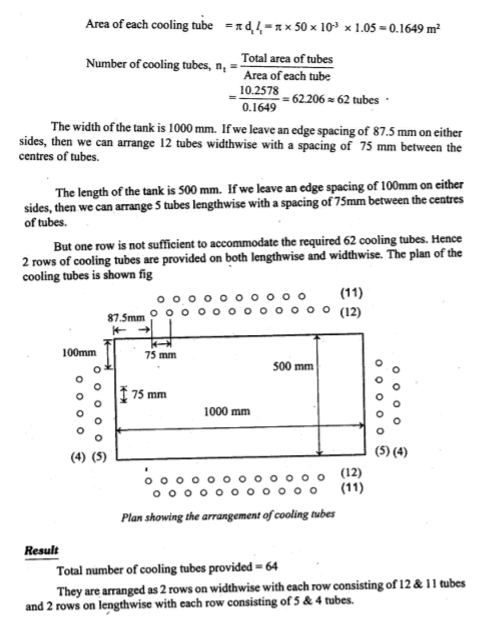
Q18)
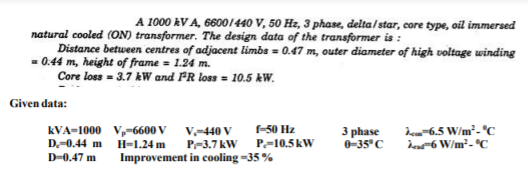
A18)
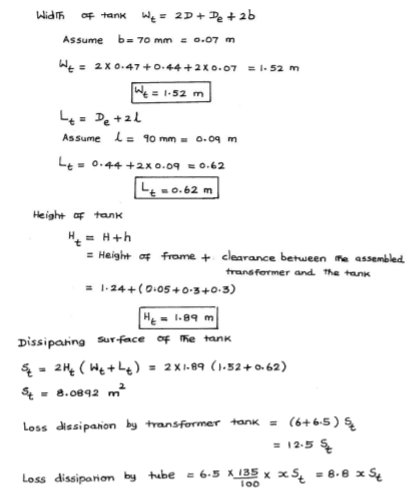
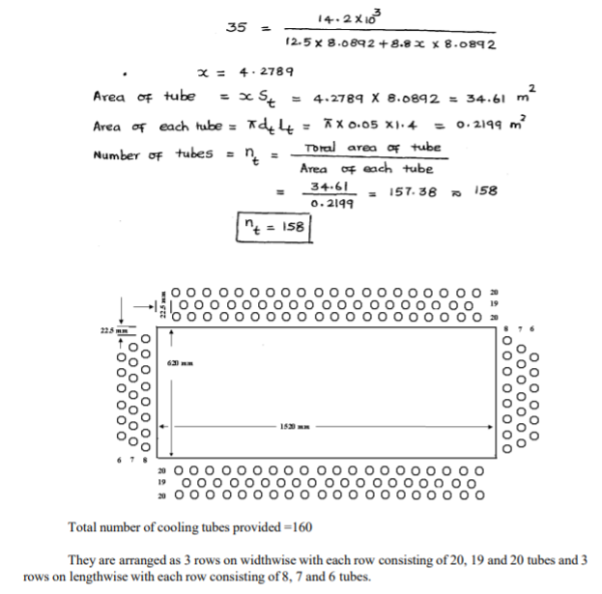
Q19) Derive the output equation of 3-phase transformer with usual notations?
A19)
main flux
Maximum flux density
=current density
=Gross core area
net core area
stacking factor *
Also known as laminate factor or space factor. It gives approximate no. Of how much core is effective when calculating flux.
.area of primary window
area of window
D=distance between core centers or distance between center of adjacent limbs
d=diagram of circumscribing circle
Window space factor

F=frequency
emf [volts]
no. Of turns in primary and secondary winding respectively
=current in primary and secondary winding respectively
Terminal voltage of primary and secondary
Area of conductor of primary and secondary winding respectively
Mean length of flux in iron
Length of mean no. Of winding
Weight of active iron [kg]
Weight of copper[kg]
Weight of per
of iron [kg]
.
Loss in iron per kg[w]
Loss in cu per kg [w]
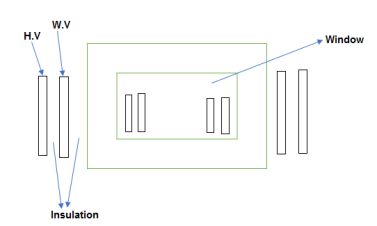
The voltage inducted in winding with T turn and excited by source having frequency ‘f’ Hz is given by considering core type. The voltage induced in with T turns is given by E=4.44f
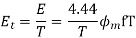
4f
Total CU area in window =
Primary turn *area of primary conductor +secondary turns *area of secondary conductor
------2
Taking e
So
Putting and
in eqn 2
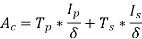
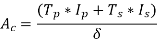
Now if we neglect magnetizing mmf
So,----------3
As we know that
Window space factor conductor area in window/Total area in window
---------------------4
Putting value of from eqn3 to eqn 4
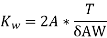
So,--------------5
Rating of 1in
VA is given by Q=VI*
KVA of both pri and sec is same so for
={as Vp is approximately equal to Ep}
=
=
We know

Q=
Q=
Now, {Maximum flux density *net area of core}
SoQ=
Here winding bound over central limit so eqn for type is
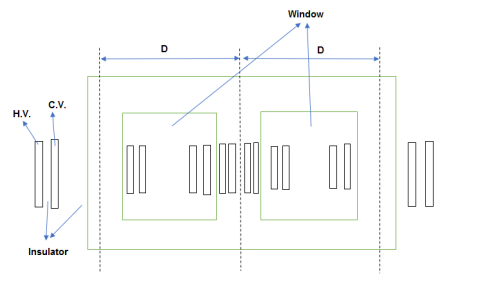
Note: In case of each 2 window consists of 2 primary and 2 sec windings
Total CU area in each window
=
=

Now
So

Now rating of 3 in KVA is given by
Q=
= {
={
=
=3*
=
Q=KVA
So both the equation of Q(holds good for core and shell type
O/P equation volt per turn
Consider O/P of 1
Q=…KVA

Q=
We know that
So Q=
The ratio of is constant for given type service and method of construct
Let{constant/controlling factor }
Q=
Q==
So,
Here roughly measures cross sectional of iron case AT gives cross sectional of winding so ratio of
will be constant for
As we know that voltage per turn

=



Putting value of r=
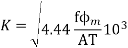
Ratio of depends on type service & method of construction so K also depend upon type service & method of construction.
For different type
Type K
Single phase shell type 1 to 1.2
Single phase core type 0.75to 0.85
3 shell type 1.3
3core type (distribution) 0.45
3core type (power) 0.6 to 0.7
Relation between core area & weight of iron &weight of w
KVA O/P of 1- is given by
Q=KVA----------------1
Now Weight of iron (G)&weight of copper (Gc) can be given as
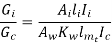
For a specific Lets assume ,
are constant=c1
So,
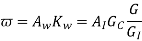
Where
Putting value of in equation -1
Q=2.22*
So Area of core (Ai) can be given as
{Mass how heavy it is }
So,------------------2
Where C=
----------------3
Let
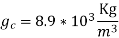
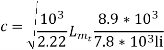
-------------4
Putting C in equation 2
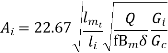
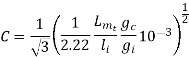
C=Typical ratio of
for diff are
1 core type =0.3-0.55
3 core type =0.17-0.5
1 shell type =1.2 to 2
For 3
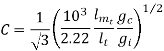

Typical value of ratio for different types of xmer is
1 core type =0.3 to 0.55
3core type =0.17 to 0.5
1core type=1.2 to 2
Calculate core and window area of 400kva,50hz .1core type xmer. The ratio of weight of iron to cu is4.length of mean turn of cu to mean flux path
Is 0.5 maximum flux density is 1.5 w6/A/
,density of cu is 8.9*
kg/
,window space factor is 0.12
Given kVA rating =400kva, f=50Hz

=0.5


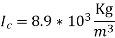
Space factor=0.12
The ratio of flux to full load mmf in 400 KVA,50Hz 1
Case type is 2.4*,Calculate net iron area &window area Maximum flux density in the core is
,current density 2.4
is 0.26.Also Calculate full load mmf
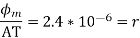
Q=400KVA
F=50Hz

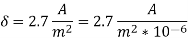

We know that from O/P eqn volt per turn

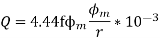
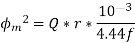
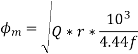
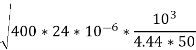
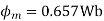
We know that

We know that

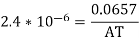
AT=27375
From
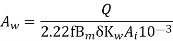
=

Q20) Explain design of core and elimination of overall dimensions?
A20)
DESIGN OF MAIN DIMENSIONS
Design of Core: Core is made up of several thin Lamination of 0.3-0.5mm thickness
Materials used for lamination is silicon steel which is alloy of iron & carbon
These Laminations are pile or stacked together to form core
Every Lamination is insulated by varnish or paper to reduce eddy current loss
Silicon steel used can be Hot rolled or cold rolled In recent times we use cold rolled as it has
1. High flux density
2. Reduction amount of core material used CRGO(Cold rolled grain oriented ) steel is used as core material in recent times widely
DIFFERENT TYPES OF LAMINATIONS
For 1Lamination for core type & shell type are given below
Core Lamination

Shell Lamination
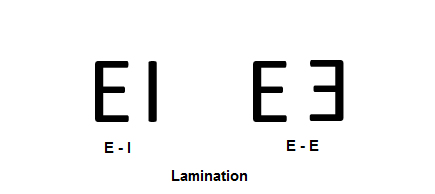
Stacking factor: The net cross sectional area is obtained from the dimensions of various packets & allowance is made for space lost between lamination this allowance is known as stacking factor value for sheet steel coating of insulation it becomes 0.96
Utilization Factor: The ratio of net cross sectional area to the area of the core circle is known as utilization factor. UF increase as number of core steps increases usually optimum number of steps is 6 for smaller and 15 for larger ,this result in reduction in winding
TYPES OF CORE
1 SQUARE CORE
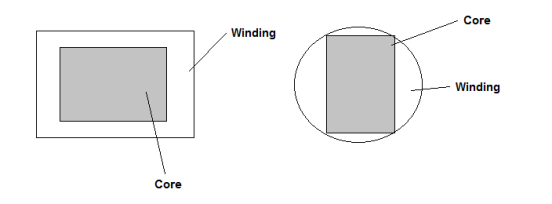
2 RECTANGULAR CORE
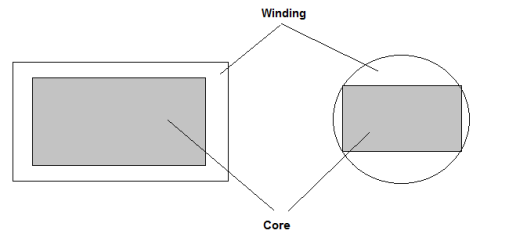
3 Circular core
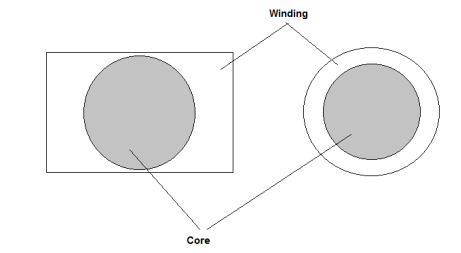
4 Stepped core
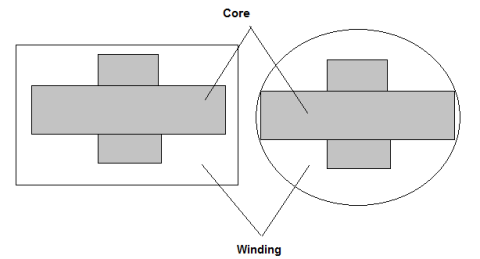
As circular core with circular or round conductor have uniform distribution of force and hence good mechanical strength. Hence circular core with circular conductor are more preferable than square and rectangular
Also winding put around the core have minimum length of mean turn hence reduced amount of conductor material thereby reducing the cost
A circular core however involves the unmanageably large number of Laminations of different sixes
The use of Laminations of different sizes is possible but is highly time consuming uneconomical
The corner of steps are so arranged that they lie on circle known as circumscribing circle circular coils are used because of their superior mechanical characteristic
Arrangement of core section in steps is called as stepped core or cruciform core .This involves Reduction in length of mean turn of winding
Reduction in cost of conductor material
Less loss but involves extra cost in shearing and assembly of lamination
Rectangular Core: For moderate & small voltage power & distribution for shell type
Square & Stepped Core: For High voltage power & distributed
If square core used then diameter of circumscribing circle hence size increase Hence small diameter of circumscribing circle reduces the size & cost
CORE TYPE: Rectangular core Square Core or Stepped core
SHELL TYPE: Rectangular core
Design of Square Core
1
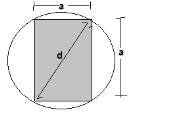
By applying Pythagoras theorem



Gross area of core

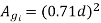

Net core area we know that

Practical value of stacking factor is 0.9



Area of circumscribing circle
=
Ratio
Hence finally
A=0.71d



U.F=0.58
2. DESIGN OF 2 STEPPED OR CRUCIFORM CORE
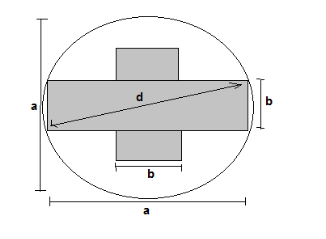
Gross core area
Let


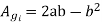
=
=

Differentiating the above expression w.r.t

=
For maximum area
=0




a=dCosθ
=dCos(31.71)
=0.85d
b=0.53d
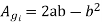

Net core area

We can say that by increasing number of steps area of circumscribing circle is more effectively utilized finally
A=0.85d
B=0.53d


Design of yoke:
The section of yoke can be taken as rectangular or stepped
Let,
Ay =area of yoke
Area of yoke =depth of yoke *height of yoke =Dy
Oy=width of largest core stamping=a[for cruciform or stepped core]
Ay=1.5 to 1.25 times ,[for using hot rolled steel]
.[for using CRGO]
Window space factor.

The window space factor [kw] depends upon the relative amounts of insulate &cu provided which in turn depends upon the voltage rating $ o/p of
The following empires formula may be used to estimate value of window space for factor [kw]
20 KVA rating :-
50-200 KVA rating =
1000 KVA rating :-
Where,
KV:-voltage of H.V winding in kilo-volt
Window space factor is larger for large o/p and smaller for small o/p
Window dimensions:
The leakage rectangle is affected by the distance between adjacent limbs.
D decreases ww is limited .so, have increases in cow value of leakage reactance.
Hw is decreases ww results in large of reactant.
The distance is small then width of winding is limited this muses will be ultimately lead to low value of leakage reactant.
Width of window has to increases in order to accommodate coil.
The height of window is small or limited then this share and wide calls used will ultimately give rise to large value of leakage reaction
Hence area of window [AW]
Aw =total conductor area/window space factor
If considering primary side


Area of window =Height of window *width of window
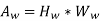
Also
The ratio of height to width of window is 2 to 4
Assuming suitable value for ratio window the height & width of window can be calculated
WIDTH OF WINDOW FOR OPTIMUM O/P
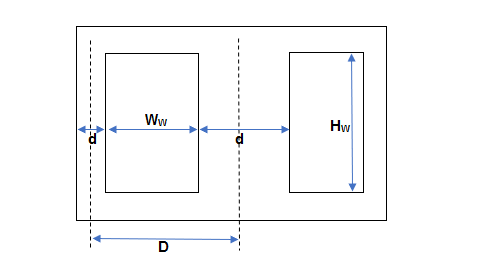
Let
D= distance between adjacent limbs
D=width of iron +width of bare conductor +width of insulation &clearance
Let m=space occupied by insulation & clearance etc.
Width occupied by CU or iron :D’=D-m
Width of bare conductor in window =D’-d
Let
S=O/P in VA in per unit height of window

Where voltage per turn
=turns per unit height
=mmf.per unit height
=
current density
A=area of each conductor
=Height of conductor *width of conductor
propor0tional to
*width of CU in window

S=
=
Where a= constant for maximum O/P for give
n value of D’,S is differentiated w.r.t.d
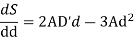
For maximum O/P

D=1.5d
D=D’+m value of m can be taken as 0.2d with normal design
D=1.7d
Width of window which gives max O/P is
Calculation of core area
Volt/turn is calculated using


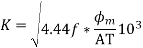
K value can be selected from table
Maximum flux calculated using

Calculating net core area & Gross core area
Net core area
Gross core area