Question Bank of Module 05
Q- What are polymers?
A-
It is a long molecule formed by joining together of thousands of small molecular units by chemical bonds. Polymers are giant molecules also called macromolecules that are essential to our existence. They are important chemicals in our bodies in plants (starch, cellulose) and in our everyday lives (fibers, plastics, elastomers). Polymers are made by transforming small molecules into molecules with very large molecular weights. Although the chemical properties of polymers are similar to those of analogous small molecules, their physical properties are quite different. Every polymer has its own characteristics, but most polymers have the following general properties:
Polymers can be very resistant to chemicals.
Polymers can be both thermal and electrical insulators.
Generally, polymers are light in weight with varying degrees of strength.
Polymers can be processed in various ways to produce thin fibers or intricate parts.
Q- Explain different type of Polymerization.
Types of polymerization:
Polymers can be synthesized by the following polymerization processes:
- Addition polymerization or chain polymerization
- Condensation or step or step growth polymerization
III. Copolymerisation
Addition polymerization:
The addition polymerization is the process in which the liniking together of monomer molecules by a chain reaction is observed. Polymer synthesized by addition polymerization has the same empirical formula as that of monomer. No molecule is evolved during polymerisation and the polymer is an exact multiple of the original monomeric molecule.
Condensation polymerization:
An intermolecular reaction involving two different bifunctional reactants with affinity for each other and taking place through repeated condensation reaction is known as condensation polymerization.
Copolymerisation:
Addition polymerisation involving a mixture of two or more suitable or compatible monomers gives a copolymer and the process is known as copolymerization. A reaction in which a mixture of two or more monomers is allowed to undergo polymerisation is known as copolymerization. The polymer is known as copolymer.
E.g.: Copolymerisation of styrene and methyl methacrylate
Q- Explain molecular weight of Polymers.
Molecular weight is the average weight of the molecules that make up a polymer and gives an indication of the length of the polymer chains.
The polymerization process is subject to variation so there is no single chain length, there is actually a wide range of lengths, so when we discuss molecular weight, we really mean the average molecular weight of the material. This average is found by measuring samples of the material as it is produced.
Unless they have been purified, synthetic polymers have a distribution of molecular weights. Different methods of measuring the molecular weight yield different types of averages. Two of the most important are the number-average and the weight-average molecular weights. Suppose that you have a set of values {x1, x2, . . ., xn} for which you calculate an average value. If the probability of each value occurring are given by {P1, P2, . . ., Pn} then the average is given by the sum below:
∑i=0 ∞ Pixi
Q- a. To Find:
(a) The number-average molecular weight
(b) The degree of polymerization for the given polypropylene material b. Given:
Molecular Weight Range | xi | wi |
8,000–16,000 | 0.05 | 0.02 |
16,000–24,000 | 0.16 | 0.10 |
24,000–32,000 | 0.24 | 0.20 |
32,000–40,000 | 0.28 | 0.30 |
40,000–48,000 | 0.20 | 0.27 |
48,000–56,000 | 0.07 | 0.11 |
c. Assumptions:
The given data is accurate; the material (polypropylene) is pure.
Solution:
Number-average molecular weight:
Molecular Weight Range | Mean Mi | xi | xiMi |
8,000–16,000 | 12,000 | 0.05 | 600 |
16,000–24,000 | 20,000 | 0.16 | 3200 |
24,000–32,000 | 28,000 | 0.24 | 6720 |
32,000–40,000 | 36,000 | 0.28 | 10,080 |
40,000–48,000 | 44,000 | 0.20 | 8800 |
48,000–56,000 | 52,000 | 0.07 | 3640 |
Mn = xiMi
= 33,040 g/mol
Degree of polymerization:
For polypropylene, the repeat unit molecular weight,
m = 3(AC ) + 6(AH )
= (3)(12.01 g/mol) + (6)(1.008 g/mol)
= 42.08 g/mol
DP = Mn / m
= 33,040 /42.08 g/mol
= 785
Q- Explain Glass Transition Temperature.
Glass transition temperature is described as the temperature at which 30–50 carbon chains start to move. At the glass transition temperature, the amorphous regions experience transition from rigid state to more flexible state making the temperature at the border of the solid state to rubbery state. It is also said that at this temperature the free volume (gap between the molecular chains) increases by 2.5 time. Glass transition temperature is represented by Tg and is a property of the amorphous materials or the amorphous portion of a semicrystalline materials. When the ambient temperature is below Tg, the molecular chains of amorphous materials are frozen in place and behave like solid glass. Plastic materials with flexible backbone show lower Tg, whereas plastic materials whose molecular structure is stiff, rigid, and inflexible show a higher Tg. Glass transition temperature helps determine various flexible and rigid applications for a material.
Polymers are hard and brittle like glass, due to the lack of mobility below Glassy state (Tg)
Polymers are soft and flexible like rubber due to some mobility above Glassy State (Tg)
The physical and polymer properties of the polymer also changes above the Glassy State (Tg)
Q- Explain different types of Visco Elasticity.
Types of Visco Elasticity:
(i) Linear Visco Elasticity
(ii) Non-Linear Visco Elasticity
Linear Visco Elasticity:
Visco elastic materials are those for which the relationship between stress and strain depends on time. Linear visco elastic materials are those for which there is a linear relationship between stress and strain (at any given time). Linear visco elasticity is a theory describing the behavior of such ideal materials. Strain-time curves for various constant stresses are shown in the following figure for a linear visco elastic material. At any given time, say t1 , the strain is proportional to stress, so that the strain due to 3o at the t1 is three times the strain due to o same time.
Non-Linear Visco Elasticity:
Nonlinear visco elasticity is when the function is not separable. It usually happens when the deformations are large or if the material changes its properties under deformations.
An elastic material is a special case of a visco elastic material will fully recover to its original state on the removal of load.
Q-Explain Thermoplastic Polymer.
A thermoplastic is a resin that is solid at room temperature but becomes plastic and soft upon heating, flowing due to crystal melting or by virtue of crossing the glass transition temperature (Tg). Upon processing, usually via injection-molding or blow-molding-like processes, thermoplastics take the shape of the mould within which they are poured as melt, and cool to solidify into the desired shape. The significant aspect of thermoplastics is their reversibility, the ability to undergo reheating, melt again, and change shape. This allows for additional processing of the same material, even after being prepared as a solid. Processes such as extrusion, thermoforming, and injection molding rely on such resin behavior. Some common thermoplastic materials include polyethylene (PE), polycarbonate (PC), and polyvinyl chloride (PVC).
Q- Explain the properties of Thermoplastic and Thermosetting Polymer.
Properties:
Property | Thermoplastics Polymer | Thermosetting Polymer |
Molecular Structure | Linear polymer: weak molecular bonds in a straight-chain formation | Network polymers: high level of crosslinking with strong chemical molecular bonds |
Melting point | Melting point lower than the degradation temperature | Melting point higher than the degradation temperature |
Mechanical | Flexible and elastic. High resistance to impact (10x more than thermosets). Strength comes from crystallinity | Inelastic and brittle. Strong and rigid. Strength comes from crosslinking. |
Polymerization | Addition polymerisation: repolymerised during manufacture (before processing) | Polycondensation polymerisation: polymerised during processing |
Microstructure | Comprised of hard crystalline and elastic amorphous regions in its solid state | Comprised of thermosetting resin and reinforcing fibre in its solid state |
Size | Size is expressed by molecular weight | Size is expressed by crosslink density |
Solubility | Can dissolve in organic solvents | Do not dissolve in organic solvents |
Service temperature | Lower continuous use temperature (CUT) than thermosets | Higher CUT than thermoplastics |
Q- Explain the process of injection molding.
Steps involved in the Injection Molding:
The various stages of the injection molding process are carefully considered when analyzing part design, tool creation and efficient production of molded plastic products. There are a lot of factors and configurations which we won’t touch on here but the basic process is the same. Let’s start with the basics.
STEP 1: THE MOLD CLOSES
STEP 2: INJECTION
(The heated plastic is injected into the mold. As the melt enters the mold, the displaced air escapes through vents in the injection pins and along the parting line. Runner, gate and vent design are important to insure the mold is properly filled.)
STEP 3: COOLING
(Once the mold is filled the part is allowed to cool for the exact amount of time needed to harden the material. Cooling time is dependent on the type of resin used and the thickness of the part. Each mold is designed with internal cooling or heating lines where water is cycled through the mold to maintain a constant temperature)
STEP 4: PLASTICIZING THE RESIN
(While the part cools, the barrel screw retracts and draws new plastic resin into the barrel from the material hopper. The heater bands maintain the needed barrel temperature for the type of resin being used.)
STEP 5: EJECTION
(The mold opens and the ejector rod moves the ejector pins forward.
The part falls and is captured in a bin located below the mold.)
STEP 6: REMOVING THE RUNNER AND PACKAGING
Q- Explain the preparation and uses of PMMA.
Preparation:
This is an important thermoplastic resin. It is obtained by polymerization of methyl methacrylate which is an ester of methyl acrylic acid, CH2=C(CH3)COOH, in presence of acetyl peroxide or hydrogen peroxide. It is an acrylic polymer.
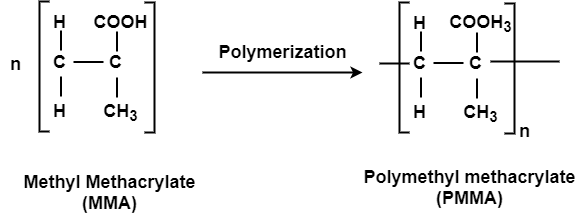
Properties:
(i) It is hard, fairly rigid material with a high softening point of about 130-14rfC.
(ii) It becomes rubber like at a temperature above 6oC.
(iii) It has outstanding shape-forming properties due to wide span of temperature from its rigid state to viscous.
(iv) It has high optical transparency.
(v) It has high resistance to sunlight and ability of transmission light accurately.
Uses:
They are used for making lenses, optical parts of instruments, air craft, light fixture, artificial eyes, wind screen, bone splints, decorative articles etc. PMMA is found in paint and used in window glasses.