Unit 2
Corrosion and Metal finishing Corrosion
1.Explain the Electrochemical theory of corrosion?
Corrosion is the disintegration of a metal due to the chemical reactions between the metal and the surrounding environment. Both the types of metal and the environmental conditions, particularly gasses that come in contact with the metal, determine the form and rate of the corrosion.
Wet or Electrochemical theory of Corrosion: This corrosion occurs in metals that come in direct contact with a conducting liquid of two different metals are dissolved in a solution partly. There is formation of galvanic cell on the metal, as part of the metal acts as an anode and the rest is the cathode, the chemical in the solution along with the humidity acts as the electrolyte. Oxidation takes place in such conditions resulting in corrosion at the anode surface and reduction occurs at the cathode surface of the metal. In this case corrosion occurs at the anode but rust gets deposited on the cathode.
2. Explain two factors that affect the rate of corrosion?
The two factors that affect rate of corrosion are
- Ratio of Anodic and cathodic areas
The rate of corrosion is influenced by relative size of cathodic to anodic area. When a metal is taken into consideration, corrosion rate is very high if the anode area is small and the cathode area is large, as this ratio decreases the corrosion rate increases further. The reason, the electrons are liberated at the anode and are consumed by the cathode region, if the cathode region is large the electrons liberated are consumed rapidly consumed at the cathode, further this enhances the anodic reactions that further increases the overall rate of corrosion. When two dissimilar metals are in contact, Corrosion is more rapid and severe, if the anodic area is small and cathodic area is large (e.g., a small steel pipe fitted in a large copper tank), If during plating of tin on iron, some areas are not covered or some pin holes are left, there results a small anode and large cathode.
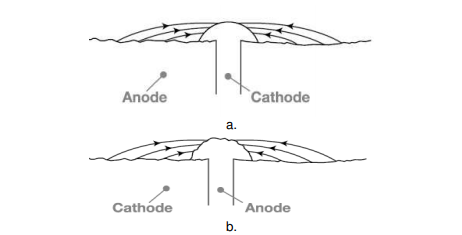
Figure. Effect of area ratios of bimetallic corrosion a. Large anode area, small cathode area showing relatively insignificant attack over a wide area of the sheet. b. Large cathode area, small anode area showing relatively pronounced attack of the rivet head.
- Nature of corrosion product
- The nature of the corrosion product like metal oxide may serve as a protective film, if the product is stable, insoluble and nonporous. The protective film can further prevent corrosion by acting as barrier between metal surface and corrosion medium. On the other hand, corrosion is enhanced if the product is unstable, porous, and soluble.
E.g., in oxidizing environments, metals that form protective layers are aluminium, chromium, titanium, etc., are highly passive and protect the metal surface from further corrosion. On the other hand, metals such as iron, zinc, magnesium etc., do not form any protective film and are highly susceptible for continuous corrosion, when exposed to oxidizing environments.
3. What are the two types of corrosion?
Differential Metal
When two different or dissimilar metals come in contact with each other and have different electrode potential values, when both these metals are exposed to a corrosive environment. The metal with lower electrode potential value forms the anode and undergoes oxidation and corrosion takes place, whereas the metal with higher electrode potential value forms the cathode and remains unaffected.
Pitting corrosion
Pitting corrosion, or pitting, is a localised corrosion, where small holes are formed on the metal surface, in this small area depassivation occurs that becomes anodic and the rest of the vast area becomes the cathode, oxidation occurs at the anode and reduction at the
Cathode, leading to a localised galvanic corrosion. The corrosion penetrates the mass of the metal, with a limited diffusion of ions.
4. Write Two ways to control corrosion?
Anodizing of Aluminium
Anodizing is an electrolytic surface treatment most commonly used with aluminium components. This treatment provides durable, hard, corrosion resistant and nonconductive finish on the outer surface of the anodized part. The oxide layer is porous in nature and makes the surface of the component easy to dye and paint. For this reason, it is often used as a pre-treatment for parts that will be dyed, coated or bonded
Anodizing is accomplished with the component or workpiece submerged in a tank filled with an electrolytic acid solution. A current (typically low, from 5-20V) is passed through the solution via a cathode submerged in the solution, with the workpiece serving as the anode. Oxygen is released by the current at the surface of the aluminium, building up a layer of aluminium oxide on the outside of the part.
Cathodic Protection
Cathodic protection in this process the main principle is to switch from the works by changing over undesirable anodic (active) sites on to a metal's surface to cathodic (passive) destinations in the presence of a restricting current. This restricting current provides free electrons and also supplies power to the nearby anodes,
Cathodic protection can, the presence of galvanic anodes. This process is also known as conciliatory form, this technique utilises metal anodes together with the electrolytic condition, to make themselves strong (erode) so as to secure the cathode. This technique proves to save the metals galvanic corrosion.
Though the metal that requires protection can differ, the conciliatory anodes are largely made up of magnesium, or zinc, metals that have the most negative electro-potential. The arrangement of galvanic setup gives a glimpse of the distinctive electro-potential - or integrity - of metals and amalgams.
In a conciliatory framework, the anode should be supplanted regularly as the metallic particles move from the anode to the cathode, which drives the anode to erode more rapidly. The second technique for cathodic security is alluded to as awed current protection.
This strategy, which is regularly used to ensure covered pipelines and ship bodies, requires an elective wellspring of direct electrical current to be provided to the electrolyte.
5.Write a Sacrificial Anode?
Sacrificial Anode
It is a method where an easily eroded material is deliberately placed in a tank or a pipe to be sacrificed for corrosion and the rest of the system remains free from corrosion.
A sacrificial anode is also known as a galvanic anode
The mechanism that occurs in this process is very similar to that of an electrochemical system. In this technique the metal that is protected is placed on the cathode side and then a more reactive metal or alloy (having a larger potential difference than the protected metal) is chosen and connected to the protected metal as an anode. The redox reaction will proceed spontaneously. As the reaction proceeds the sacrificial metal gets consumed as oxidation reaction occurs at the anode, simultaneously reduction reaction occurs on the cathode, thus preventing the metal from erosion. Thus, corrosion on the protected metal is successfully shifted to the anode, protecting the metal.
Sacrificial anodes are normally supplied with either lead wires or cast-m straps to facilitate their connection to the structure being protected. The lead wires may be attached to the structure by welding or mechanical conn
The materials used for sacrificial anodes are either relatively pure active metals, such as zinc or magnesium, or are magnesium or aluminium alloys that have been specifically developed for use as sacrificial anodes.
Advantages of using sacrificial anodes:
- Can be used where there is no power
- Lower initial cost
- Less supervision required
- Comparatively simple installation and additional anodes can easily be added if the initial installation proves to be inadequate
Sacrificial anodes are used to protect:
- Hulls of ships
- Water heaters
- Pipelines
- Distribution systems
- Above-ground tanks
- Underground tanks
- Refineries
The anodes in sacrificial anode cathodic protection systems must be periodically inspected and replaced when consumed.
6. Define metal finishing?
In the manufacturing process this forms the final step, this process provides environmental protection. This is also used to reduce the roughness of the surface beyond the capabilities of machining operations for parts that must mate or seal. The other processes also include metal cleaning, deburring, descaling etc, numerous types of metal finishing process are used for a range of purposes. Some of the general advantages of metal finishing treatments include:
- To Increase durability
- To Improve decorative appeal
- Enhanced electrical conductivity
- Higher electrical resistance
- Higher chemical resistance
- Higher tarnish resistance
7. Explain principles that govern electroplating?
Polarization: During electrolysis, the potential of the electrode changes due to Polarization, where the anode potential becomes nobler than that of cathode. Polarization has the property of decreasing the output voltage of batteries based on the conditions and thereby increases the voltage that is required for electrolysis cells.
This process is also known as kinetic deviation from the equilibrium because of an electric current passing through a galvanic cell. Polarization may occur at the cathode (cathodic polarization) or at the anode (anodic polarization). Cathodic polarization is more common
Decomposition Potential
A decomposition potential, in electrochemistry, is the difference in the electrode potential between an electrolytic cell's cathode and anode in order for electrolysis to occur. It is the minimum voltage produced from an electrolytic cell and is used in the electrolysis process.
Overvoltage
Overpotential is the potential difference (voltage) between a half-reaction's thermodynamically determined reduction potential and the potential at which the redox event is experimentally observed. The term is directly related to a cell's voltage efficiency.
8. Differentiate between Decorative and hard Chromium?
The undercoating of Nickel is deposited by Nickel electroplating in one or two layers. Nickel helps in levelling the substrate surface and also provides corrosion resistance, in addition Nickel also helps in surface preparing for chromium plugging.
Decorative chromium is deposited directly on bright underlying nickel.
The decorative chromium thickness lies in the range of 0.01-0.03 μinch (0.25-0.75 μm).
In decorative chromium numerous micro cracks and micropores are covered by under coating of Nickel, these microdefects play an important role in providing cathodic protection for the undercoating of nickel. Since the micro-cracks or micro-pores are uniformly spread over the chromium surface, corrosion reaction is not localized and therefore it proceeds slowly.
Hard chromium (chrome): It’s a relatively thick coating that is deposited on the metallic substrate mostly steel, in order to impart few specific properties to the surface.
The main component of all the chromium plating solution is chromium trioxide (CrO3) also known as chromic acid. The second component is a catalyst, which is either sulfate (SO42-) or fluoride.
Trivalent chromium (Cr3+), is the by-product of the electroplating process. Ions of trivalent chromium continuously reoxidize to the hexavalent state at the anode. Normal level of the trivalent chromium is about 1-2% of the chromic acid concentration. Higher contents of trivalent chromium may cause reduction of throwing power and plating rate, pitting and treeing of the deposit. If the trivalent chromium is too high (more than 2%) reoxidation operation should be carried out at high anode area/cathode area ratio (30) at cathode current density 20 A/ft² (2 A/dm²).
9. Explain the Electroless platting of Nickel?
Electroless plating of Nickel
This is the most effective and simplest way of applying a nickel plate over steel, copper, iron, brass, zincated aluminium and copper alloys.
The Nickel is applied by heating the Nickel bath to 195°F and then dipping the part to be plated in the bath for 15-60minutes, this process does not require DC power, and the process time is carried till the desired thickness is observed. In nickel coating an autocatalytic reaction occurs that applies the nickel coating.
The tricky part about electroless plating is that you must keep at least 80% of the nickel in the plating solution at all times. Letting the amount of nickel get below 80% will cause the bath to crash, rendering it useless.
10.Differentiate between electroless platting and electrplatting?
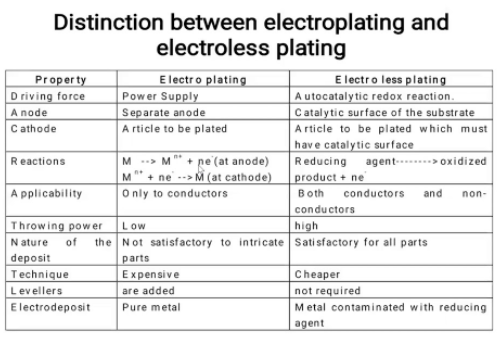
Unit 2
Corrosion and Metal finishing Corrosion
1.Explain the Electrochemical theory of corrosion?
Corrosion is the disintegration of a metal due to the chemical reactions between the metal and the surrounding environment. Both the types of metal and the environmental conditions, particularly gasses that come in contact with the metal, determine the form and rate of the corrosion.
Wet or Electrochemical theory of Corrosion: This corrosion occurs in metals that come in direct contact with a conducting liquid of two different metals are dissolved in a solution partly. There is formation of galvanic cell on the metal, as part of the metal acts as an anode and the rest is the cathode, the chemical in the solution along with the humidity acts as the electrolyte. Oxidation takes place in such conditions resulting in corrosion at the anode surface and reduction occurs at the cathode surface of the metal. In this case corrosion occurs at the anode but rust gets deposited on the cathode.
2. Explain two factors that affect the rate of corrosion?
The two factors that affect rate of corrosion are
- Ratio of Anodic and cathodic areas
The rate of corrosion is influenced by relative size of cathodic to anodic area. When a metal is taken into consideration, corrosion rate is very high if the anode area is small and the cathode area is large, as this ratio decreases the corrosion rate increases further. The reason, the electrons are liberated at the anode and are consumed by the cathode region, if the cathode region is large the electrons liberated are consumed rapidly consumed at the cathode, further this enhances the anodic reactions that further increases the overall rate of corrosion. When two dissimilar metals are in contact, Corrosion is more rapid and severe, if the anodic area is small and cathodic area is large (e.g., a small steel pipe fitted in a large copper tank), If during plating of tin on iron, some areas are not covered or some pin holes are left, there results a small anode and large cathode.
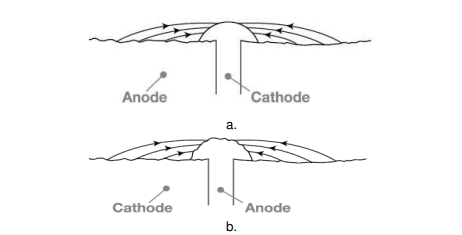
Figure. Effect of area ratios of bimetallic corrosion a. Large anode area, small cathode area showing relatively insignificant attack over a wide area of the sheet. b. Large cathode area, small anode area showing relatively pronounced attack of the rivet head.
- Nature of corrosion product
- The nature of the corrosion product like metal oxide may serve as a protective film, if the product is stable, insoluble and nonporous. The protective film can further prevent corrosion by acting as barrier between metal surface and corrosion medium. On the other hand, corrosion is enhanced if the product is unstable, porous, and soluble.
E.g., in oxidizing environments, metals that form protective layers are aluminium, chromium, titanium, etc., are highly passive and protect the metal surface from further corrosion. On the other hand, metals such as iron, zinc, magnesium etc., do not form any protective film and are highly susceptible for continuous corrosion, when exposed to oxidizing environments.
3. What are the two types of corrosion?
Differential Metal
When two different or dissimilar metals come in contact with each other and have different electrode potential values, when both these metals are exposed to a corrosive environment. The metal with lower electrode potential value forms the anode and undergoes oxidation and corrosion takes place, whereas the metal with higher electrode potential value forms the cathode and remains unaffected.
Pitting corrosion
Pitting corrosion, or pitting, is a localised corrosion, where small holes are formed on the metal surface, in this small area depassivation occurs that becomes anodic and the rest of the vast area becomes the cathode, oxidation occurs at the anode and reduction at the
Cathode, leading to a localised galvanic corrosion. The corrosion penetrates the mass of the metal, with a limited diffusion of ions.
4. Write Two ways to control corrosion?
Anodizing of Aluminium
Anodizing is an electrolytic surface treatment most commonly used with aluminium components. This treatment provides durable, hard, corrosion resistant and nonconductive finish on the outer surface of the anodized part. The oxide layer is porous in nature and makes the surface of the component easy to dye and paint. For this reason, it is often used as a pre-treatment for parts that will be dyed, coated or bonded
Anodizing is accomplished with the component or workpiece submerged in a tank filled with an electrolytic acid solution. A current (typically low, from 5-20V) is passed through the solution via a cathode submerged in the solution, with the workpiece serving as the anode. Oxygen is released by the current at the surface of the aluminium, building up a layer of aluminium oxide on the outside of the part.
Cathodic Protection
Cathodic protection in this process the main principle is to switch from the works by changing over undesirable anodic (active) sites on to a metal's surface to cathodic (passive) destinations in the presence of a restricting current. This restricting current provides free electrons and also supplies power to the nearby anodes,
Cathodic protection can, the presence of galvanic anodes. This process is also known as conciliatory form, this technique utilises metal anodes together with the electrolytic condition, to make themselves strong (erode) so as to secure the cathode. This technique proves to save the metals galvanic corrosion.
Though the metal that requires protection can differ, the conciliatory anodes are largely made up of magnesium, or zinc, metals that have the most negative electro-potential. The arrangement of galvanic setup gives a glimpse of the distinctive electro-potential - or integrity - of metals and amalgams.
In a conciliatory framework, the anode should be supplanted regularly as the metallic particles move from the anode to the cathode, which drives the anode to erode more rapidly. The second technique for cathodic security is alluded to as awed current protection.
This strategy, which is regularly used to ensure covered pipelines and ship bodies, requires an elective wellspring of direct electrical current to be provided to the electrolyte.
5.Write a Sacrificial Anode?
Sacrificial Anode
It is a method where an easily eroded material is deliberately placed in a tank or a pipe to be sacrificed for corrosion and the rest of the system remains free from corrosion.
A sacrificial anode is also known as a galvanic anode
The mechanism that occurs in this process is very similar to that of an electrochemical system. In this technique the metal that is protected is placed on the cathode side and then a more reactive metal or alloy (having a larger potential difference than the protected metal) is chosen and connected to the protected metal as an anode. The redox reaction will proceed spontaneously. As the reaction proceeds the sacrificial metal gets consumed as oxidation reaction occurs at the anode, simultaneously reduction reaction occurs on the cathode, thus preventing the metal from erosion. Thus, corrosion on the protected metal is successfully shifted to the anode, protecting the metal.
Sacrificial anodes are normally supplied with either lead wires or cast-m straps to facilitate their connection to the structure being protected. The lead wires may be attached to the structure by welding or mechanical conn
The materials used for sacrificial anodes are either relatively pure active metals, such as zinc or magnesium, or are magnesium or aluminium alloys that have been specifically developed for use as sacrificial anodes.
Advantages of using sacrificial anodes:
- Can be used where there is no power
- Lower initial cost
- Less supervision required
- Comparatively simple installation and additional anodes can easily be added if the initial installation proves to be inadequate
Sacrificial anodes are used to protect:
- Hulls of ships
- Water heaters
- Pipelines
- Distribution systems
- Above-ground tanks
- Underground tanks
- Refineries
The anodes in sacrificial anode cathodic protection systems must be periodically inspected and replaced when consumed.
6. Define metal finishing?
In the manufacturing process this forms the final step, this process provides environmental protection. This is also used to reduce the roughness of the surface beyond the capabilities of machining operations for parts that must mate or seal. The other processes also include metal cleaning, deburring, descaling etc, numerous types of metal finishing process are used for a range of purposes. Some of the general advantages of metal finishing treatments include:
- To Increase durability
- To Improve decorative appeal
- Enhanced electrical conductivity
- Higher electrical resistance
- Higher chemical resistance
- Higher tarnish resistance
7. Explain principles that govern electroplating?
Polarization: During electrolysis, the potential of the electrode changes due to Polarization, where the anode potential becomes nobler than that of cathode. Polarization has the property of decreasing the output voltage of batteries based on the conditions and thereby increases the voltage that is required for electrolysis cells.
This process is also known as kinetic deviation from the equilibrium because of an electric current passing through a galvanic cell. Polarization may occur at the cathode (cathodic polarization) or at the anode (anodic polarization). Cathodic polarization is more common
Decomposition Potential
A decomposition potential, in electrochemistry, is the difference in the electrode potential between an electrolytic cell's cathode and anode in order for electrolysis to occur. It is the minimum voltage produced from an electrolytic cell and is used in the electrolysis process.
Overvoltage
Overpotential is the potential difference (voltage) between a half-reaction's thermodynamically determined reduction potential and the potential at which the redox event is experimentally observed. The term is directly related to a cell's voltage efficiency.
8. Differentiate between Decorative and hard Chromium?
The undercoating of Nickel is deposited by Nickel electroplating in one or two layers. Nickel helps in levelling the substrate surface and also provides corrosion resistance, in addition Nickel also helps in surface preparing for chromium plugging.
Decorative chromium is deposited directly on bright underlying nickel.
The decorative chromium thickness lies in the range of 0.01-0.03 μinch (0.25-0.75 μm).
In decorative chromium numerous micro cracks and micropores are covered by under coating of Nickel, these microdefects play an important role in providing cathodic protection for the undercoating of nickel. Since the micro-cracks or micro-pores are uniformly spread over the chromium surface, corrosion reaction is not localized and therefore it proceeds slowly.
Hard chromium (chrome): It’s a relatively thick coating that is deposited on the metallic substrate mostly steel, in order to impart few specific properties to the surface.
The main component of all the chromium plating solution is chromium trioxide (CrO3) also known as chromic acid. The second component is a catalyst, which is either sulfate (SO42-) or fluoride.
Trivalent chromium (Cr3+), is the by-product of the electroplating process. Ions of trivalent chromium continuously reoxidize to the hexavalent state at the anode. Normal level of the trivalent chromium is about 1-2% of the chromic acid concentration. Higher contents of trivalent chromium may cause reduction of throwing power and plating rate, pitting and treeing of the deposit. If the trivalent chromium is too high (more than 2%) reoxidation operation should be carried out at high anode area/cathode area ratio (30) at cathode current density 20 A/ft² (2 A/dm²).
9. Explain the Electroless platting of Nickel?
Electroless plating of Nickel
This is the most effective and simplest way of applying a nickel plate over steel, copper, iron, brass, zincated aluminium and copper alloys.
The Nickel is applied by heating the Nickel bath to 195°F and then dipping the part to be plated in the bath for 15-60minutes, this process does not require DC power, and the process time is carried till the desired thickness is observed. In nickel coating an autocatalytic reaction occurs that applies the nickel coating.
The tricky part about electroless plating is that you must keep at least 80% of the nickel in the plating solution at all times. Letting the amount of nickel get below 80% will cause the bath to crash, rendering it useless.
10.Differentiate between electroless platting and electrplatting?
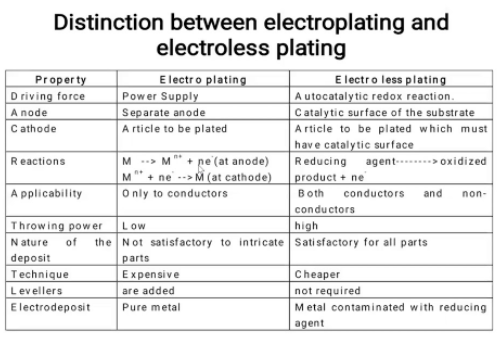
Unit 2
Corrosion and Metal finishing Corrosion
1.Explain the Electrochemical theory of corrosion?
Corrosion is the disintegration of a metal due to the chemical reactions between the metal and the surrounding environment. Both the types of metal and the environmental conditions, particularly gasses that come in contact with the metal, determine the form and rate of the corrosion.
Wet or Electrochemical theory of Corrosion: This corrosion occurs in metals that come in direct contact with a conducting liquid of two different metals are dissolved in a solution partly. There is formation of galvanic cell on the metal, as part of the metal acts as an anode and the rest is the cathode, the chemical in the solution along with the humidity acts as the electrolyte. Oxidation takes place in such conditions resulting in corrosion at the anode surface and reduction occurs at the cathode surface of the metal. In this case corrosion occurs at the anode but rust gets deposited on the cathode.
2. Explain two factors that affect the rate of corrosion?
The two factors that affect rate of corrosion are
- Ratio of Anodic and cathodic areas
The rate of corrosion is influenced by relative size of cathodic to anodic area. When a metal is taken into consideration, corrosion rate is very high if the anode area is small and the cathode area is large, as this ratio decreases the corrosion rate increases further. The reason, the electrons are liberated at the anode and are consumed by the cathode region, if the cathode region is large the electrons liberated are consumed rapidly consumed at the cathode, further this enhances the anodic reactions that further increases the overall rate of corrosion. When two dissimilar metals are in contact, Corrosion is more rapid and severe, if the anodic area is small and cathodic area is large (e.g., a small steel pipe fitted in a large copper tank), If during plating of tin on iron, some areas are not covered or some pin holes are left, there results a small anode and large cathode.
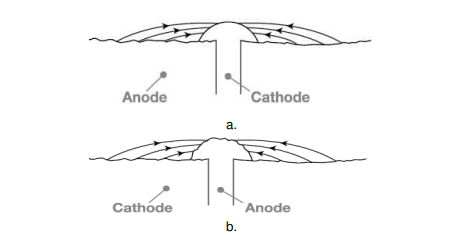
Figure. Effect of area ratios of bimetallic corrosion a. Large anode area, small cathode area showing relatively insignificant attack over a wide area of the sheet. b. Large cathode area, small anode area showing relatively pronounced attack of the rivet head.
- Nature of corrosion product
- The nature of the corrosion product like metal oxide may serve as a protective film, if the product is stable, insoluble and nonporous. The protective film can further prevent corrosion by acting as barrier between metal surface and corrosion medium. On the other hand, corrosion is enhanced if the product is unstable, porous, and soluble.
E.g., in oxidizing environments, metals that form protective layers are aluminium, chromium, titanium, etc., are highly passive and protect the metal surface from further corrosion. On the other hand, metals such as iron, zinc, magnesium etc., do not form any protective film and are highly susceptible for continuous corrosion, when exposed to oxidizing environments.
3. What are the two types of corrosion?
Differential Metal
When two different or dissimilar metals come in contact with each other and have different electrode potential values, when both these metals are exposed to a corrosive environment. The metal with lower electrode potential value forms the anode and undergoes oxidation and corrosion takes place, whereas the metal with higher electrode potential value forms the cathode and remains unaffected.
Pitting corrosion
Pitting corrosion, or pitting, is a localised corrosion, where small holes are formed on the metal surface, in this small area depassivation occurs that becomes anodic and the rest of the vast area becomes the cathode, oxidation occurs at the anode and reduction at the
Cathode, leading to a localised galvanic corrosion. The corrosion penetrates the mass of the metal, with a limited diffusion of ions.
4. Write Two ways to control corrosion?
Anodizing of Aluminium
Anodizing is an electrolytic surface treatment most commonly used with aluminium components. This treatment provides durable, hard, corrosion resistant and nonconductive finish on the outer surface of the anodized part. The oxide layer is porous in nature and makes the surface of the component easy to dye and paint. For this reason, it is often used as a pre-treatment for parts that will be dyed, coated or bonded
Anodizing is accomplished with the component or workpiece submerged in a tank filled with an electrolytic acid solution. A current (typically low, from 5-20V) is passed through the solution via a cathode submerged in the solution, with the workpiece serving as the anode. Oxygen is released by the current at the surface of the aluminium, building up a layer of aluminium oxide on the outside of the part.
Cathodic Protection
Cathodic protection in this process the main principle is to switch from the works by changing over undesirable anodic (active) sites on to a metal's surface to cathodic (passive) destinations in the presence of a restricting current. This restricting current provides free electrons and also supplies power to the nearby anodes,
Cathodic protection can, the presence of galvanic anodes. This process is also known as conciliatory form, this technique utilises metal anodes together with the electrolytic condition, to make themselves strong (erode) so as to secure the cathode. This technique proves to save the metals galvanic corrosion.
Though the metal that requires protection can differ, the conciliatory anodes are largely made up of magnesium, or zinc, metals that have the most negative electro-potential. The arrangement of galvanic setup gives a glimpse of the distinctive electro-potential - or integrity - of metals and amalgams.
In a conciliatory framework, the anode should be supplanted regularly as the metallic particles move from the anode to the cathode, which drives the anode to erode more rapidly. The second technique for cathodic security is alluded to as awed current protection.
This strategy, which is regularly used to ensure covered pipelines and ship bodies, requires an elective wellspring of direct electrical current to be provided to the electrolyte.
5.Write a Sacrificial Anode?
Sacrificial Anode
It is a method where an easily eroded material is deliberately placed in a tank or a pipe to be sacrificed for corrosion and the rest of the system remains free from corrosion.
A sacrificial anode is also known as a galvanic anode
The mechanism that occurs in this process is very similar to that of an electrochemical system. In this technique the metal that is protected is placed on the cathode side and then a more reactive metal or alloy (having a larger potential difference than the protected metal) is chosen and connected to the protected metal as an anode. The redox reaction will proceed spontaneously. As the reaction proceeds the sacrificial metal gets consumed as oxidation reaction occurs at the anode, simultaneously reduction reaction occurs on the cathode, thus preventing the metal from erosion. Thus, corrosion on the protected metal is successfully shifted to the anode, protecting the metal.
Sacrificial anodes are normally supplied with either lead wires or cast-m straps to facilitate their connection to the structure being protected. The lead wires may be attached to the structure by welding or mechanical conn
The materials used for sacrificial anodes are either relatively pure active metals, such as zinc or magnesium, or are magnesium or aluminium alloys that have been specifically developed for use as sacrificial anodes.
Advantages of using sacrificial anodes:
- Can be used where there is no power
- Lower initial cost
- Less supervision required
- Comparatively simple installation and additional anodes can easily be added if the initial installation proves to be inadequate
Sacrificial anodes are used to protect:
- Hulls of ships
- Water heaters
- Pipelines
- Distribution systems
- Above-ground tanks
- Underground tanks
- Refineries
The anodes in sacrificial anode cathodic protection systems must be periodically inspected and replaced when consumed.
6. Define metal finishing?
In the manufacturing process this forms the final step, this process provides environmental protection. This is also used to reduce the roughness of the surface beyond the capabilities of machining operations for parts that must mate or seal. The other processes also include metal cleaning, deburring, descaling etc, numerous types of metal finishing process are used for a range of purposes. Some of the general advantages of metal finishing treatments include:
- To Increase durability
- To Improve decorative appeal
- Enhanced electrical conductivity
- Higher electrical resistance
- Higher chemical resistance
- Higher tarnish resistance
7. Explain principles that govern electroplating?
Polarization: During electrolysis, the potential of the electrode changes due to Polarization, where the anode potential becomes nobler than that of cathode. Polarization has the property of decreasing the output voltage of batteries based on the conditions and thereby increases the voltage that is required for electrolysis cells.
This process is also known as kinetic deviation from the equilibrium because of an electric current passing through a galvanic cell. Polarization may occur at the cathode (cathodic polarization) or at the anode (anodic polarization). Cathodic polarization is more common
Decomposition Potential
A decomposition potential, in electrochemistry, is the difference in the electrode potential between an electrolytic cell's cathode and anode in order for electrolysis to occur. It is the minimum voltage produced from an electrolytic cell and is used in the electrolysis process.
Overvoltage
Overpotential is the potential difference (voltage) between a half-reaction's thermodynamically determined reduction potential and the potential at which the redox event is experimentally observed. The term is directly related to a cell's voltage efficiency.
8. Differentiate between Decorative and hard Chromium?
The undercoating of Nickel is deposited by Nickel electroplating in one or two layers. Nickel helps in levelling the substrate surface and also provides corrosion resistance, in addition Nickel also helps in surface preparing for chromium plugging.
Decorative chromium is deposited directly on bright underlying nickel.
The decorative chromium thickness lies in the range of 0.01-0.03 μinch (0.25-0.75 μm).
In decorative chromium numerous micro cracks and micropores are covered by under coating of Nickel, these microdefects play an important role in providing cathodic protection for the undercoating of nickel. Since the micro-cracks or micro-pores are uniformly spread over the chromium surface, corrosion reaction is not localized and therefore it proceeds slowly.
Hard chromium (chrome): It’s a relatively thick coating that is deposited on the metallic substrate mostly steel, in order to impart few specific properties to the surface.
The main component of all the chromium plating solution is chromium trioxide (CrO3) also known as chromic acid. The second component is a catalyst, which is either sulfate (SO42-) or fluoride.
Trivalent chromium (Cr3+), is the by-product of the electroplating process. Ions of trivalent chromium continuously reoxidize to the hexavalent state at the anode. Normal level of the trivalent chromium is about 1-2% of the chromic acid concentration. Higher contents of trivalent chromium may cause reduction of throwing power and plating rate, pitting and treeing of the deposit. If the trivalent chromium is too high (more than 2%) reoxidation operation should be carried out at high anode area/cathode area ratio (30) at cathode current density 20 A/ft² (2 A/dm²).
9. Explain the Electroless platting of Nickel?
Electroless plating of Nickel
This is the most effective and simplest way of applying a nickel plate over steel, copper, iron, brass, zincated aluminium and copper alloys.
The Nickel is applied by heating the Nickel bath to 195°F and then dipping the part to be plated in the bath for 15-60minutes, this process does not require DC power, and the process time is carried till the desired thickness is observed. In nickel coating an autocatalytic reaction occurs that applies the nickel coating.
The tricky part about electroless plating is that you must keep at least 80% of the nickel in the plating solution at all times. Letting the amount of nickel get below 80% will cause the bath to crash, rendering it useless.
10.Differentiate between electroless platting and electrplatting?
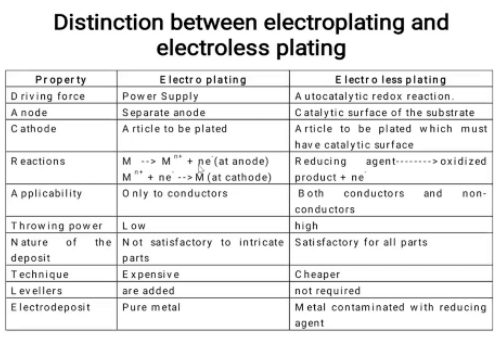
Unit 2
Corrosion and Metal finishing Corrosion
1.Explain the Electrochemical theory of corrosion?
Corrosion is the disintegration of a metal due to the chemical reactions between the metal and the surrounding environment. Both the types of metal and the environmental conditions, particularly gasses that come in contact with the metal, determine the form and rate of the corrosion.
Wet or Electrochemical theory of Corrosion: This corrosion occurs in metals that come in direct contact with a conducting liquid of two different metals are dissolved in a solution partly. There is formation of galvanic cell on the metal, as part of the metal acts as an anode and the rest is the cathode, the chemical in the solution along with the humidity acts as the electrolyte. Oxidation takes place in such conditions resulting in corrosion at the anode surface and reduction occurs at the cathode surface of the metal. In this case corrosion occurs at the anode but rust gets deposited on the cathode.
2. Explain two factors that affect the rate of corrosion?
The two factors that affect rate of corrosion are
- Ratio of Anodic and cathodic areas
The rate of corrosion is influenced by relative size of cathodic to anodic area. When a metal is taken into consideration, corrosion rate is very high if the anode area is small and the cathode area is large, as this ratio decreases the corrosion rate increases further. The reason, the electrons are liberated at the anode and are consumed by the cathode region, if the cathode region is large the electrons liberated are consumed rapidly consumed at the cathode, further this enhances the anodic reactions that further increases the overall rate of corrosion. When two dissimilar metals are in contact, Corrosion is more rapid and severe, if the anodic area is small and cathodic area is large (e.g., a small steel pipe fitted in a large copper tank), If during plating of tin on iron, some areas are not covered or some pin holes are left, there results a small anode and large cathode.
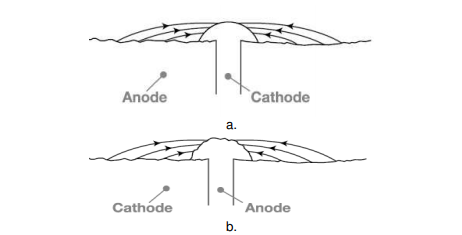
Figure. Effect of area ratios of bimetallic corrosion a. Large anode area, small cathode area showing relatively insignificant attack over a wide area of the sheet. b. Large cathode area, small anode area showing relatively pronounced attack of the rivet head.
- Nature of corrosion product
- The nature of the corrosion product like metal oxide may serve as a protective film, if the product is stable, insoluble and nonporous. The protective film can further prevent corrosion by acting as barrier between metal surface and corrosion medium. On the other hand, corrosion is enhanced if the product is unstable, porous, and soluble.
E.g., in oxidizing environments, metals that form protective layers are aluminium, chromium, titanium, etc., are highly passive and protect the metal surface from further corrosion. On the other hand, metals such as iron, zinc, magnesium etc., do not form any protective film and are highly susceptible for continuous corrosion, when exposed to oxidizing environments.
3. What are the two types of corrosion?
Differential Metal
When two different or dissimilar metals come in contact with each other and have different electrode potential values, when both these metals are exposed to a corrosive environment. The metal with lower electrode potential value forms the anode and undergoes oxidation and corrosion takes place, whereas the metal with higher electrode potential value forms the cathode and remains unaffected.
Pitting corrosion
Pitting corrosion, or pitting, is a localised corrosion, where small holes are formed on the metal surface, in this small area depassivation occurs that becomes anodic and the rest of the vast area becomes the cathode, oxidation occurs at the anode and reduction at the
Cathode, leading to a localised galvanic corrosion. The corrosion penetrates the mass of the metal, with a limited diffusion of ions.
4. Write Two ways to control corrosion?
Anodizing of Aluminium
Anodizing is an electrolytic surface treatment most commonly used with aluminium components. This treatment provides durable, hard, corrosion resistant and nonconductive finish on the outer surface of the anodized part. The oxide layer is porous in nature and makes the surface of the component easy to dye and paint. For this reason, it is often used as a pre-treatment for parts that will be dyed, coated or bonded
Anodizing is accomplished with the component or workpiece submerged in a tank filled with an electrolytic acid solution. A current (typically low, from 5-20V) is passed through the solution via a cathode submerged in the solution, with the workpiece serving as the anode. Oxygen is released by the current at the surface of the aluminium, building up a layer of aluminium oxide on the outside of the part.
Cathodic Protection
Cathodic protection in this process the main principle is to switch from the works by changing over undesirable anodic (active) sites on to a metal's surface to cathodic (passive) destinations in the presence of a restricting current. This restricting current provides free electrons and also supplies power to the nearby anodes,
Cathodic protection can, the presence of galvanic anodes. This process is also known as conciliatory form, this technique utilises metal anodes together with the electrolytic condition, to make themselves strong (erode) so as to secure the cathode. This technique proves to save the metals galvanic corrosion.
Though the metal that requires protection can differ, the conciliatory anodes are largely made up of magnesium, or zinc, metals that have the most negative electro-potential. The arrangement of galvanic setup gives a glimpse of the distinctive electro-potential - or integrity - of metals and amalgams.
In a conciliatory framework, the anode should be supplanted regularly as the metallic particles move from the anode to the cathode, which drives the anode to erode more rapidly. The second technique for cathodic security is alluded to as awed current protection.
This strategy, which is regularly used to ensure covered pipelines and ship bodies, requires an elective wellspring of direct electrical current to be provided to the electrolyte.
5.Write a Sacrificial Anode?
Sacrificial Anode
It is a method where an easily eroded material is deliberately placed in a tank or a pipe to be sacrificed for corrosion and the rest of the system remains free from corrosion.
A sacrificial anode is also known as a galvanic anode
The mechanism that occurs in this process is very similar to that of an electrochemical system. In this technique the metal that is protected is placed on the cathode side and then a more reactive metal or alloy (having a larger potential difference than the protected metal) is chosen and connected to the protected metal as an anode. The redox reaction will proceed spontaneously. As the reaction proceeds the sacrificial metal gets consumed as oxidation reaction occurs at the anode, simultaneously reduction reaction occurs on the cathode, thus preventing the metal from erosion. Thus, corrosion on the protected metal is successfully shifted to the anode, protecting the metal.
Sacrificial anodes are normally supplied with either lead wires or cast-m straps to facilitate their connection to the structure being protected. The lead wires may be attached to the structure by welding or mechanical conn
The materials used for sacrificial anodes are either relatively pure active metals, such as zinc or magnesium, or are magnesium or aluminium alloys that have been specifically developed for use as sacrificial anodes.
Advantages of using sacrificial anodes:
- Can be used where there is no power
- Lower initial cost
- Less supervision required
- Comparatively simple installation and additional anodes can easily be added if the initial installation proves to be inadequate
Sacrificial anodes are used to protect:
- Hulls of ships
- Water heaters
- Pipelines
- Distribution systems
- Above-ground tanks
- Underground tanks
- Refineries
The anodes in sacrificial anode cathodic protection systems must be periodically inspected and replaced when consumed.
6. Define metal finishing?
In the manufacturing process this forms the final step, this process provides environmental protection. This is also used to reduce the roughness of the surface beyond the capabilities of machining operations for parts that must mate or seal. The other processes also include metal cleaning, deburring, descaling etc, numerous types of metal finishing process are used for a range of purposes. Some of the general advantages of metal finishing treatments include:
- To Increase durability
- To Improve decorative appeal
- Enhanced electrical conductivity
- Higher electrical resistance
- Higher chemical resistance
- Higher tarnish resistance
7. Explain principles that govern electroplating?
Polarization: During electrolysis, the potential of the electrode changes due to Polarization, where the anode potential becomes nobler than that of cathode. Polarization has the property of decreasing the output voltage of batteries based on the conditions and thereby increases the voltage that is required for electrolysis cells.
This process is also known as kinetic deviation from the equilibrium because of an electric current passing through a galvanic cell. Polarization may occur at the cathode (cathodic polarization) or at the anode (anodic polarization). Cathodic polarization is more common
Decomposition Potential
A decomposition potential, in electrochemistry, is the difference in the electrode potential between an electrolytic cell's cathode and anode in order for electrolysis to occur. It is the minimum voltage produced from an electrolytic cell and is used in the electrolysis process.
Overvoltage
Overpotential is the potential difference (voltage) between a half-reaction's thermodynamically determined reduction potential and the potential at which the redox event is experimentally observed. The term is directly related to a cell's voltage efficiency.
8. Differentiate between Decorative and hard Chromium?
The undercoating of Nickel is deposited by Nickel electroplating in one or two layers. Nickel helps in levelling the substrate surface and also provides corrosion resistance, in addition Nickel also helps in surface preparing for chromium plugging.
Decorative chromium is deposited directly on bright underlying nickel.
The decorative chromium thickness lies in the range of 0.01-0.03 μinch (0.25-0.75 μm).
In decorative chromium numerous micro cracks and micropores are covered by under coating of Nickel, these microdefects play an important role in providing cathodic protection for the undercoating of nickel. Since the micro-cracks or micro-pores are uniformly spread over the chromium surface, corrosion reaction is not localized and therefore it proceeds slowly.
Hard chromium (chrome): It’s a relatively thick coating that is deposited on the metallic substrate mostly steel, in order to impart few specific properties to the surface.
The main component of all the chromium plating solution is chromium trioxide (CrO3) also known as chromic acid. The second component is a catalyst, which is either sulfate (SO42-) or fluoride.
Trivalent chromium (Cr3+), is the by-product of the electroplating process. Ions of trivalent chromium continuously reoxidize to the hexavalent state at the anode. Normal level of the trivalent chromium is about 1-2% of the chromic acid concentration. Higher contents of trivalent chromium may cause reduction of throwing power and plating rate, pitting and treeing of the deposit. If the trivalent chromium is too high (more than 2%) reoxidation operation should be carried out at high anode area/cathode area ratio (30) at cathode current density 20 A/ft² (2 A/dm²).
9. Explain the Electroless platting of Nickel?
Electroless plating of Nickel
This is the most effective and simplest way of applying a nickel plate over steel, copper, iron, brass, zincated aluminium and copper alloys.
The Nickel is applied by heating the Nickel bath to 195°F and then dipping the part to be plated in the bath for 15-60minutes, this process does not require DC power, and the process time is carried till the desired thickness is observed. In nickel coating an autocatalytic reaction occurs that applies the nickel coating.
The tricky part about electroless plating is that you must keep at least 80% of the nickel in the plating solution at all times. Letting the amount of nickel get below 80% will cause the bath to crash, rendering it useless.
10.Differentiate between electroless platting and electrplatting?
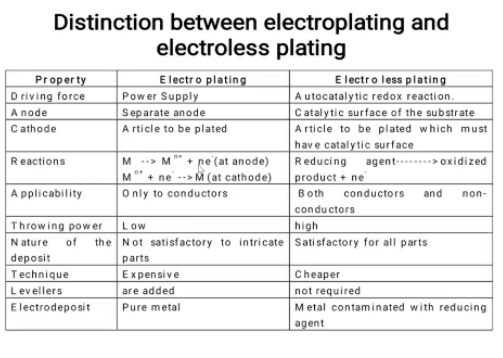